What is a hydraulic valve and what is its purpose
Hydraulic valves control the direction and flow rate of the valve. Hydraulic control valves can be divided into three types they are directional control valves, flow control valves, pressure control valves, and non-return valves. Hydraulic system uses many valves to control the flow of fluids, hydraulic valves regulates flow by cutting off, diverting, providing an overflow relief, and preventing reverse flow. Hydraulic valves are used in hydraulic power packs to direct the fluid to and from the cylinder. Hydraulic valves can be used to control the direction and amount of fluid power in a circuit. So these valves would do it by controlling the pressure and the flow rate in various sections of the circuit. System pressure can be controlled by hydraulic valves. The burden of pump pressure or temperature of the oil before the oil flow to the hydraulic circuit is reduced by using the hydraulic valve.
How hydraulic valves are constructed
Mostly all valves have the same structure a valve body, valve spool, and components of driven valve spool movements. Hydraulic valves are available in four types of construction and they are
- Threaded port type
- Sub-plate mounting type
- Cartridge type
Threaded port type
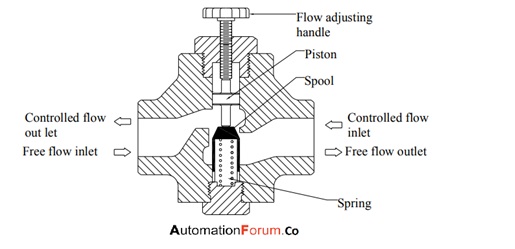
These valves have threaded ports as the name says, and it is connected by piping. The piping would require space. This design can be considered as an old one so it has many disadvantages like they are prone to leakage and needs more time to fix
Sub-plate mounting type
This valve is an industrial valve, it is the same as the threaded type and the only difference can be seen in the mounting. These valves have oil ports and they can be seen in the valve’s flat surface. These oil ports are bolted to manifold at this flat surface. The oil ports would match between the holes in the manifold and oil leakage is prevented by using O-ring at each oil ports.
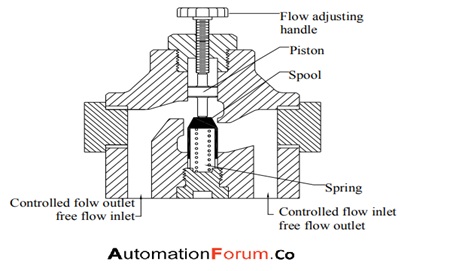
Cartridge type
This type of construction differs from the above types, their principle and concept are different. Cartridge type valves have better flow and response when compared to the other types. Cartridge valves are economical too.
What are the major requirements of hydraulic control valves
Required performance for hydraulic valves
Nominal pressure – it is the maximum working pressure allowed by long term reliable work of hydraulic control valve and this is limited by the valve intensity. Certain factors also influence the maximum permissible working pressure and they are reversing reliability of the reversing valve, and pressure regulation of the pressure valve. The nominal diameter is another factor, better flow capacity is achieved by good diameter so maximum flow could be achieved. Valves that have the same diameter would have different nominal flow because of their functions
The hydraulic valves must meet certain performance requirements and they are high sensitivity, reliability, and it must not have high noise or high vibration during the operation. Sealing should be better if the valve port is closed and if the valve port is open then the direction valve must have better core stability. High precision is needed while the operation and it must not be influenced by outside interference. These valves must be in small size and should be able to install properly.
What is a hydraulic proportional valve
The proportional valve can do the positioning of the spool in many ways. Due to this feature of the proportional valve infinite adjustable flow volume will be achieved by using this valve. This type of valves can be seen in hydraulic circuits that need more than one speed of actuators. These valves are capable to do the flow control of the fluid and speed of actuator and also control over the direction of the fluid flow. These valves are used in the hydraulic section where flow or pressure is needed to be varied. The proportional valves are operated by using DC power.
Why valves are used in hydraulic systems
In a hydraulic system, valves perform certain roles they are, control valves capable to control the operation of actuators. These valves would also regulate the pressure by controlling the oil flow. Some valves have multiple functions and are very useful an example of this would be hydraulic proportional valves.
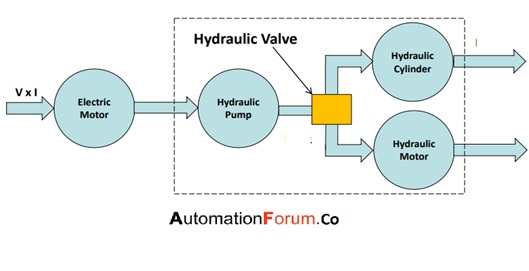
What is 4 way 3 position valve and what is a hydraulic valve spool
In a four-way three-port valve there are four ports and three positions and they are manually operated hydraulic control valve. In this valve there is a liver or it can also be called a spool which can be used for the flow direction so when the liver has moved a connection is established between two ports and the flow takes place. So by changing the liver or spools position we can establish the connection between ports and control the flow direction
What is an electro-hydraulic valve
The electro-hydraulic valve is a hydraulic servo valve and in this valve, the servo has a device that could be a flapper nozzle or a jet pipe and this device is used to position the servo. Electro-hydraulic or servo valves are used for accurate position control. These valves are used to control hydraulic motors. These valves are very costly so while selecting this valve make sure that you need accurate position control.
What is a hydraulic actuator and what is its use
The hydraulic actuator can convert the fluid pressure into motion, according to the signal received. Hydraulic actuators are required when a valve operation needs a large amount of force.
What are the types of hydraulic valves and how does it work
In a hydraulic system, valves are used to control the pressure, volume flow rate, and direction of flow. So based on these functions hydraulic valves are classified into pressure-volume or directional control valves.
Directional control valves
These valves are used to control the flow direction of hydraulic fluid to different lines in the circuit. These valves check the connection or disconnection of pathways with relative motion between the valve core and valve body to meet the requirements of the system. There are certain types of directional control valves they are one-way valves and reversing valves. In the one way valve as the name indicates it allows flow in one direction but not reverse flow. The reversing valves change the flow direction and they cut off or connects oil channels by the relative motion of valve core in the valve body
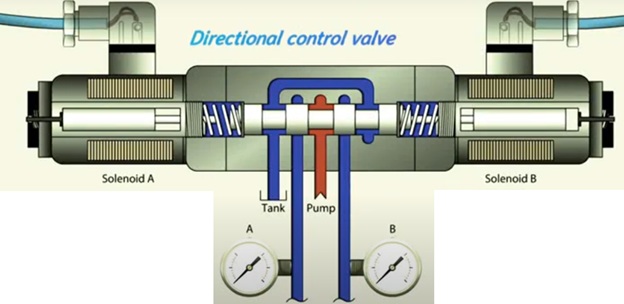
Pressure control valves
Pressure control valves control the pressure in different segments in the circuit. The pressure is created because of some flow restriction, if this not checked then it would create many problems in hydraulic components. There are many types of pressure control valves they are pressure relief valve, pressure reducing valve, pressure sequencing valve, pressure unloading valve, and counterbalance valve.
Flow control valve
Flow control valves are used if we want to control the amount of fluid flowing past the valves. These valves are used to regulate the speed of hydraulic cylinders and motors by controlling the flow rate to the actuator. The needle valve is an example of a flow control valve. In this valve, the flow is controlled by changing the flow area of the port. The orifice can be used for flow control it is a device in the shape of a disk with a hole so the fluid will flow through the hole. This can be used as a flow meter by measuring the pressure drop across the orifice.
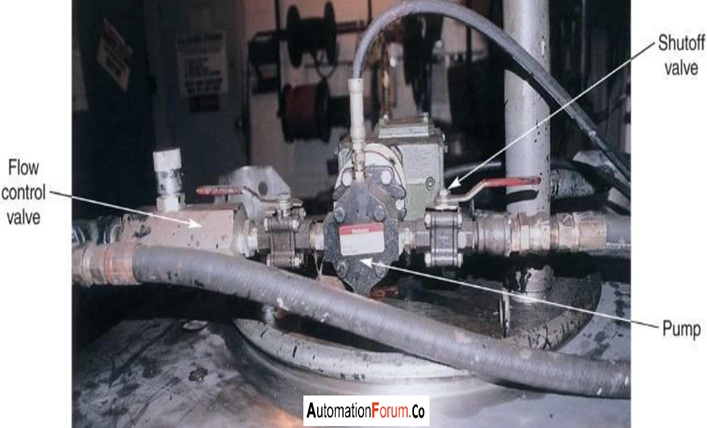
To get more info about the control valve check the following link