- What is maintenance?
- Maintenance Definition
- What are the different types of maintenance?
- What are the 4 Areas of Maintenance Management?
- What is a reactive maintenance?
- What is unplanned maintenance?
- What is an example of Reactive Maintenance?
- What are the Advantages of Reactive Maintenance?
- What are the disadvantages of reactive maintenance?
- What are the types of reactive maintenance?
- Emergency Maintenance:
- What are the objectives of emergency maintenance?
- What is a Run to Failure Maintenance Strategy?
- What is the planned maintenance system?
- What is meaning preventive maintenance?
- What is the main objective of preventive maintenance?
- What is preventive maintenance system examples?
- What is predictive maintenance with example?
- Understanding Predictive Maintenance
- Examples of Predictive Maintenance in Action:
- Benefits of Predictive Maintenance:
- What is reliability-centered maintenance?
- Reliability-Centered Maintenance (Proactive):
- What is statistical based predictive maintenance?
- What are condition-based maintenance approaches?
- Comparing Statistical-Based vs. Condition-Based Predictive Maintenance
- Maintenance Types Comparison: Planned vs. Unplanned Strategies
- Choosing the Right Maintenance Strategy: A Comprehensive Guide
- Key Benefits of Maintenance
- Maintenance vs. Repairs
- ISO Maintenance Standards for Enhanced Asset Management
- FAQs about Maintenance
What is maintenance?
- Maintenance, a fundamental concept in various sectors, plays a pivotal role in ensuring the smooth operation and longevity of devices, equipment, machinery, and building infrastructure across industrial, business, and residential installations.
- The technical meaning of maintenance contains all range of activities, including functional checks, servicing, repairs, and replacements. Over time, these processes have changed to include a variety of economical techniques for maintaining equipment functionality, whether proactive or reactive to failures.
Maintenance Definition
- Maintenance functions are broadly categorized into maintenance, repair, and overhaul (MRO), with standardized terminology gradually becoming the norm. The United States Department of Defense provides comprehensive definitions, encompassing activities such as tests, measurements, replacements, adjustments, and repairs.
- Beyond simple repairs, maintenance also involves keeping materials functional or in a state that is appropriate for use. In terms of military applications, it includes supply and repair operations to keep forces in a condition that allows them to complete their objective.
- The foundation of facility management is routine maintenance, which ensures that utilities, plants, buildings, and other facilities are always used to their full potential and efficiency.
- The concept of maintainability becomes essential when it comes to the stage of product or technological system utilization, which has an unbreakable connection to maintenance. The ability of an item to be maintained or restored to a state where it can carry out its necessary functions, using recommended processes and resources, under given conditions is known as Maintainability.
- Maintenance, in a wider sense, is the work that is done to keep machines in the same shape and condition as when they were first introduced. It is an active way to keep the machine in good shape throughout its entire life. Comprehending maintenance, with its multiple implications and uses, is crucial for industries trying to improve equipment reliability, reduce downtime, and ensure effective operations.
What are the different types of maintenance?
Different Types of Maintenance
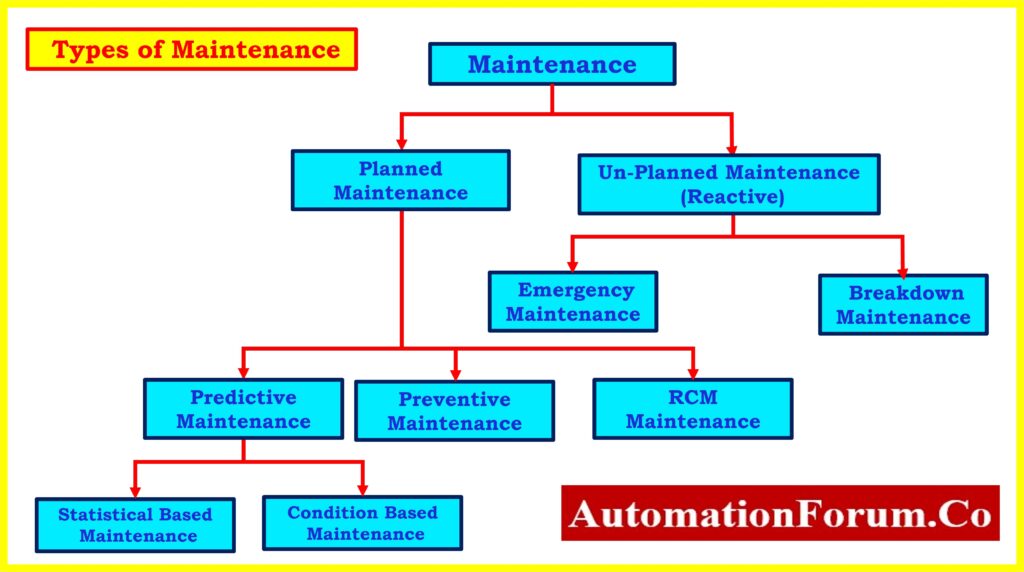
What are the 4 Areas of Maintenance Management?
Areas of Maintenance
Civil Maintenance:
- Building construction and maintenance, covering service facilities (water, gas, steam, heating, ventilating, A.C.).
- Specialized tasks like painting, plumbing, carpentry work, and fire-fighting equipment maintenance.
Mechanical Maintenance:
- Maintenance of machines, transport vehicles, material handling equipment, steam generators, boilers, compressors, and furnaces.
- Inclusion of lubrication practices as an integral part of mechanical maintenance.
Electrical Maintenance:
- Management of electrical equipment such as generators, transformers, switch gears, motors, telephone systems, and lighting.
- Inclusion of broader aspects like electrical installations, fans, meters, gauges, instruments, control panels, and battery charging.
Information System Maintenance:
- Definition and importance of maintaining components within a computer system.
- Discussion on the critical nature of information system maintenance in the digital age.
What is a reactive maintenance?
Reactive Maintenance (Unplanned Maintenance)
- Reactive maintenance is a maintenance strategy in which no preventive measures are done to keep equipment operating as intended by its design. It is sometimes referred to as the “Run it, till it breaks” or “Run to fail” mode.
- Under this model, equipment is only given attention and effort when it begins to show indications of failure, so that all maintenance seems to be unplanned.
What is unplanned maintenance?
What is an example of Reactive Maintenance?
Examples of Reactive Maintenance
- The replacement of a light bulb.
- Repairing a broken HVAC equipment rather than maintaining it.
- Repairing an HVAC unit once data from the unit shows that it is not performing effectively.
What are the Advantages of Reactive Maintenance?
Advantages of Reactive Maintenance
- Reactive maintenance is often perceived as a cost-effective option in the short term. By addressing issues only when they arise, there is a reduction in upfront maintenance expenses.
- As maintenance activities are initiated in response to equipment failures, fewer staff members may be required for ongoing monitoring and routine check-ups.
What are the disadvantages of reactive maintenance?
Dis-Advantages of Reactive Maintenance
- Increased Downtime Costs: Unexpected equipment failures result in financial losses and interruptions to business, which lower production levels.
- Higher Labor Costs, Especially with Overtime: Overtime is frequently needed for urgent repairs, leading to tight labor budgets and may have an adverse effect on employee wellbeing.
- Elevated Repair or Replacement Expenses: Equipment replacement or repair expenses can increase due to more extensive damage caused by delayed responses to problems.
- Potential Secondary Damage: Reactive techniques may increase overall repair costs by unintentionally damaging other machinery or processes.
- Inefficient Staff Resource Utilization: Reactive strategies frequently result in the less-than-ideal utilization of staff resources since workers are assigned in a reactive rather than a proactive manner, which lowers overall productivity.
Root Causes in Reactive Maintenance
Neglected Basic Conditions:
- Ignored routine inspections and basic maintenance can lead to reactive breakdowns by allowing minor problems to get worse.
Inadequate Skills:
- One factor that may cause breakdowns is a maintenance crew member’s lack of experience. Reactive conditions can result in more significant damage if faults are not immediately addressed.
Non-Adherence to Operating Standards:
- Equipment stress and failure can arise from deviating from specified operating standards. Reactive reactions are frequently the result of procedures not being followed precisely as instructed.
Unchecked Deterioration:
- Failure to monitor and address gradual deterioration is a common cause of breakdowns in reactive maintenance. Regular inspections are crucial to prevent unchecked wear and tear.
Inherent Design Weakness:
- Breakdowns can be traced back to inherent design weaknesses in equipment. Reactive approaches may highlight issues that could have been addressed during the design phase to enhance durability and reliability.
What are the types of reactive maintenance?
After unexpected equipment failures, reactive maintenance is performed. The terms “emergency maintenance” and “breakdown maintenance” sometimes overlap, and various organizations may classify them differently. However, let’s examine these two main types:
Emergency Maintenance:
What are the objectives of emergency maintenance?
- Emergency maintenance is a reactive approach that is initiated in reaction to unplanned failures in equipment or systems. This method addresses immediate issues even though it is expensive—usually three to five times more than preventive maintenance.
- Prioritizing requests for corrective maintenance work becomes crucial in order to ensure appropriate scheduling and planning.
- The challenges that come with emergency maintenance include extended equipment outages, more impact on output, and higher risks to safety because of hurriedly performed corrective actions.
- To minimize the overall impact on operations, organizations must carefully prioritize work requests, postponing non-urgent jobs to enable enough time for proper planning and scheduling.
- In the overall structure of equipment management, proper planning and priority are essential components in reducing the drawbacks of emergency maintenance and converting it into a more managed and effective procedure.
What is a Run to Failure Maintenance Strategy?
Breakdown or Run-to-Failure Maintenance (RTF)
- The objective of a run-to-failure, or corrective maintenance, technique is to repair an item only after it has failed.Deliberate or unplanned, corrective maintenance is the response to malfunctions that may have been avoided with preventative maintenance.
- This method works under the assumption that the failure is acceptable, won’t significantly affect the environment or safety, and can’t be prevented economically or technically.
- This approach works especially well in situations where there are not many consequences from failure and no immediate need for immediate repairs, such as in general area lighting or smart process instrumentation without trip functionality.
- This strategy works well in scenarios where personnel and material costs are not crucial factors and equipment outages have little effect on output.
- When selecting Corrective Maintenance as a strategy, however, it is critical to ensure that the failure modes under consideration do not have the potential to escalate into Emergency Maintenance.
- Selecting a run-to-failure strategy for machinery that needs to be restored right away following failure would lead to a reactive maintenance setting. It is more costly, inefficient, and unsafe to operate in this reactive environment.
- Though a run-to-failure plan may be a good one, it’s important to make wise choices. Avoiding the traps of a reactive maintenance environment requires careful assessment of the possible outcomes and influence on overall operational efficiency.
What is the planned maintenance system?
Planned Maintenance
- The objective of planned maintenance is to minimize downtime and lower total maintenance costs while optimizing the performance of industrial machinery.
- The objective of planned maintenance is to maximize efficiency while requiring the least amount of maintenance possible. This method uses a methodical approach in which every worker participates to improve output quality, increase uptime, and lower maintenance costs by continuously optimizing equipment functioning.
- It includes putting predictive and preventative planned maintenance strategies into action, which improves the general dependability and efficiency of industrial machinery.
- The major goal is to create a proactive system that takes care of possible problems before they become more serious, guaranteeing smooth operations and economical maintenance procedures.
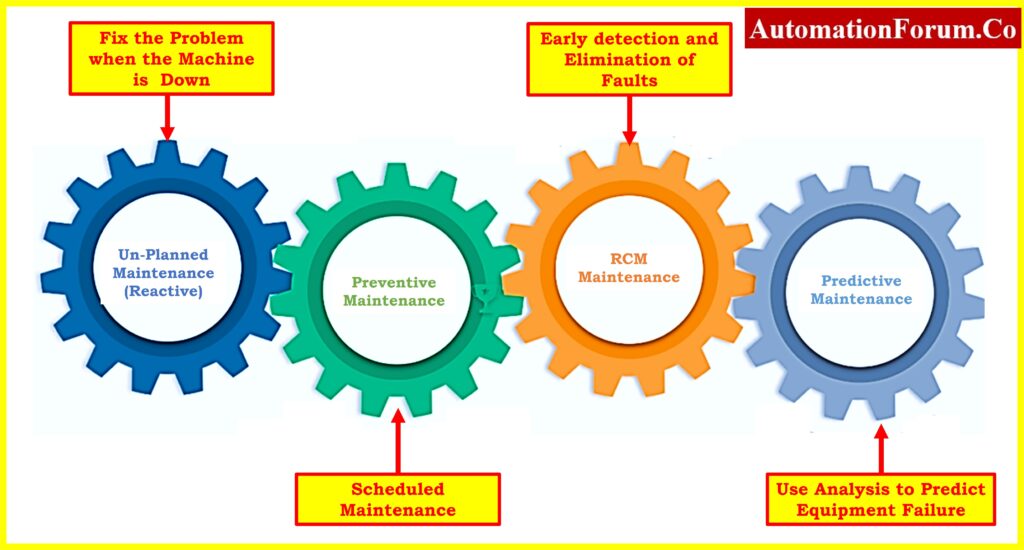
What is meaning preventive maintenance?
Preventive Maintenance
The definition of preventive maintenance is actions carried out according to a time- or machine-run schedule that identify, stop, or mitigate a system’s or component’s degradation in order to maintain or increase its useful life by limiting degradation to an acceptable level.
What is the main objective of preventive maintenance?
The Essence of Preventive Maintenance:
- Preventive maintenance is the foundation of scheduled maintenance, focusing early component identification, replacement, and repair to prevent failures.
- This strategy significantly decreases the possibility of large repairs and improves the productivity and reliability of industrial machinery by taking proactive measures to fix minor problems.
- Planned maintenance aims for optimal equipment efficiency with a minimal impact on operations.
Techniques for Preventive Maintenance:
- Periodic Reviews: Regular assessments of equipment performance and condition.
- Routine Lubrication: Ensuring proper lubrication to reduce friction and wear.
- Calibrations: Adjusting equipment to maintain accuracy and optimal functionality.
- Inspections: Visual and data-driven inspections to identify potential issues.
Automation with CMMS Software:
- Preventive maintenance tasks are made easier with the incorporation of a Computerized Maintenance Management System (CMMS) software.
- By planning and monitoring maintenance tasks, this automated technique increases productivity and ensures that procedures and inspections are carried out on time.
Costs of Preventative Maintenance
- Preventive Maintenance involves higher labor costs for scheduled equipment inspections. However, these expenses are justified by the prevention of major repairs and the reduction in energy consumption from machines operating at peak efficiency.
- Outsourcing preventive maintenance services offers a cost-effective solution, providing specialized expertise without extensive in-house resources.
- Despite the initial labor expenses, the long-term benefits, such as avoiding major repairs and energy savings, make Preventive Maintenance a financially sound strategy. Outsourcing further optimizes costs, ensuring a balanced approach to maintenance practices and budget considerations.
Example of Preventive Maintenance in Action:
Example: Conveyor Belt Maintenance
In a manufacturing setting, conveyor belt systems play a critical role in the efficient movement of materials throughout the production process. To ensure uninterrupted operation and prevent unexpected breakdowns, a proactive preventive maintenance approach is employed.
What is preventive maintenance system examples?
Preventive Maintenance Activities:
- Regular Inspections: Scheduled inspections of conveyor belts are conducted at predetermined intervals.
- Belt Tension Checks: Ensuring the proper tension of the conveyor belt to prevent slippage or excessive wear.
- Cleaning and Lubrication: Removal of debris and application of appropriate lubricants to reduce friction and wear.
- Replacement of Worn Components: Timely replacement of worn-out or damaged components such as rollers, bearings and splices.
Benefits of Preventive Maintenance
- Cost Savings: Prevents major repairs, saving on extensive repair or replacement costs.
- Operational Continuity: Minimizes downtime by preventing unexpected breakdowns.
- Extended Lifecycle: Increases the lifespan of equipment, reducing the need for frequent replacements.
- Optimized Performance: Ensures efficient operation and peak performance of equipment.
- Energy Cost Savings: Well-maintained equipment operates more efficiently, lowering energy costs.
- Safety and Compliance: Mitigates safety risks, ensures compliance with regulations, and avoids legal issues.
- Enhanced Reliability: Reduces downtime, ensuring consistent production schedules.
- Asset Management: Optimizes inventory and ensures availability of spare parts for timely repairs.
- Improved Output Quality: Maintains consistent and high-quality output to meet customer expectations.
- Positive Reputation: Enhances the company’s reputation for reliability and professionalism in the industry’
What is predictive maintenance with example?
Understanding Predictive Maintenance
- Utilizing measurements to identify early indicators of system degradation, predictive maintenance changes traditional methods of care and makes it possible to remove or manage causing stressors before major deterioration takes place.
- Predictive maintenance is a data-driven, advanced technique that improves overall operating efficiency. In contrast with time-based preventive maintenance, predictive maintenance is based on the machine’s actual state.
Predictive Maintenance – Definition:
Measuring the beginning of system degradation and the present and future functional capability of components are essential elements of predictive maintenance. It deviates from preventive maintenance in that it uses real-time data instead of predetermined schedules.
Data-Driven Approach:
- Predictive maintenance makes use of data from the equipment to map out possible machine breakdowns and identify maintenance needs in a timely manner.
Examples of Predictive Maintenance in Action:
- Temperature Alarms: As seen in data center server rooms, these alerts sound when machine temperatures depart from safe ranges, preventing hazardous overheating.
- Monitoring Engine Misfires: Engine sensors keep a watch out for misfires, sending out alerts for prompt maintenance and ensuring maximum engine performance.
- Refrigeration Truck Sensors: To protect sensitive products, refrigeration trucks have internal temperature sensors that warn drivers when temperatures drop below permissible ranges.
Benefits of Predictive Maintenance:
- Enhanced Product Quality: By resolving any problems before they affect production, predictive maintenance improves the quality of the finished product.
- Decreased Catastrophic Failures: Prompt action reduces the possibility of catastrophic events, ensuring ongoing operational dependability.
- Enhanced Equipment Performance: Proactive maintenance based on real-time data is the key to achieving optimal equipment performance.
- Improved Customer Satisfaction: By ensuring dependable and constant delivery of goods or services, predictive maintenance helps to increase customer satisfaction.
Cost Considerations
While there may be higher setup costs for predictive infrastructure, the long-term benefits include:
- Cost Savings: Predictive maintenance saves money by preventing major repairs and reducing energy consumption.
- Labor Reduction: Automation integrated into the predictive process can lead to a reduction in maintenance labor.
Click here to know more about Difference between Predictive Maintenance and Preventive Maintenance
What is reliability-centered maintenance?
Reliability-Centered Maintenance (RCM)
- Determining the maintenance needs of physical assets within their operational environment is the primary objective of the whole procedure known as reliability-centered maintenance, or RCM.
- RCM recognizes variations in equipment design, operation, and susceptibility to various degradation reasons in comparison with traditional maintenance schedules. This strategy organizes maintenance programs by prioritizing and maximizing the use of limited human and financial resources.
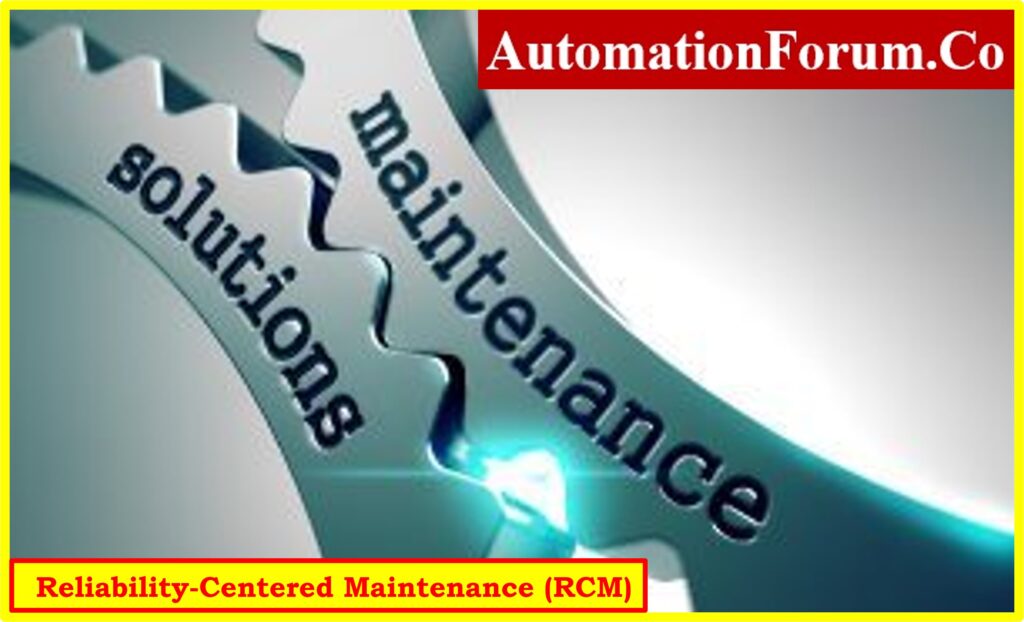
Reliability-Centered Maintenance (Proactive):
Basic Philosophy:
RCM (Proactive) utilizes predictive and preventive maintenance techniques, incorporating root cause failure analysis to detect and pinpoint precise problems. This approach employs advanced installation and repair techniques, including potential equipment redesign or modification to proactively avoid or eliminate issues.
Advantages:
- Efficiency: Can be the most efficient maintenance program.
- Cost Reduction: Lowers costs by eliminating unnecessary maintenance or overhauls.
- Minimized Overhauls: Reduces the frequency of overhauls.
- Prevents Sudden Failures: Lowers the probability of sudden equipment failures.
- Focus on Critical Components: Allows for the focused maintenance of critical components.
- Increased Reliability: Enhances component reliability.
- Root Cause Analysis: Incorporates root cause analysis for continuous improvement.
Disadvantages:
- Startup Costs: May have significant startup costs, including training and equipment.
- Visibility of Savings: Potential savings might not be immediately evident to management.
Basic Steps: Initiating Reliability-Centered Maintenance
- Master Equipment List: Develop a list identifying all equipment in the facility.
- Prioritization: Prioritize components based on importance or criticality.
- Grouping: Assign components into logical groupings.
- Maintenance Activities: Determine maintenance activities using technical manuals, machinery history, root cause analysis, and engineering assessment.
- Assess Maintenance Staff: Consider the number of employees in maintenance.
- Operations Personnel Tasks: Identify tasks that may be performed by operations maintenance personnel.
- Failure Mode Analysis: Analyze equipment failure modes and their impacts.
- Mitigation Strategies: Identify effective maintenance tasks or mitigation strategies.
What is statistical based predictive maintenance?
Statistical-Based Predictive Maintenance
- Statistical-based predictive maintenance involves leveraging statistical models and data analysis to predict when equipment maintenance is needed. This method relies on historical data, patterns, and trends to forecast potential failures.
- By employing statistical algorithms, organizations can identify anomalies and deviations from expected equipment behavior.
- This approach is particularly effective for detecting gradual degradation or wear-and-tear that might not be apparent through routine inspections.
- Statistical models can analyze large datasets, making it a powerful tool for predicting maintenance needs based on the equipment’s statistical behavior over time.
What are condition-based maintenance approaches?
Condition-Based Predictive Maintenance:
- Condition-based predictive maintenance, on the other hand, relies on real-time data collected directly from the equipment during its operation.
- This approach involves using various sensors and monitoring devices to continuously assess the condition of the equipment.
- By measuring factors such as vibration, temperature, pressure, and other relevant parameters, organizations can gain insights into the actual operating condition of the equipment.
- This real-time data allows for more accurate and timely predictions of potential issues, enabling proactive maintenance before a failure occurs.
- Condition-based predictive maintenance is especially valuable for equipment with dynamic operating conditions, as it provides a more immediate and precise understanding of the equipment’s health.
Comparing Statistical-Based vs. Condition-Based Predictive Maintenance
Feature | Statistical-Based Predictive Maintenance | Condition-Based Predictive Maintenance |
---|---|---|
Data Utilization | Makes use of statistical models and historical data. | Depends on data that is obtained in real time directly from the equipment. |
Timing of Predictions | Estimates maintenance requirements by using historical trends and patterns. | Provides real-time information by forecasting maintenance requirements while the machinery is in use. |
Detection Focus | Effective for detecting gradual degradation and long-term trends. | Particularly valuable for immediate insights into dynamic operating conditions. |
Data Sources | Analyzes large datasets and historical records. | Utilizes sensors and monitoring devices to assess current equipment conditions. |
Maintenance Types Comparison: Planned vs. Unplanned Strategies
This extended table provides a more detailed overview, including task type, objective, and interval, for Planned Maintenance (with subtypes) and Unplanned (Reactive) Maintenance (with subtypes).
Feature | Planned Maintenance | Preventive Maintenance | Predictive Maintenance | RCM (Reliability-Centered Maintenance) | Unplanned (Reactive) Maintenance | Emergency Maintenance | Breakdown Maintenance |
---|---|---|---|---|---|---|---|
Task Type | Proactive and planned tasks based on schedules and insights. | Scheduled preventive tasks addressing known issues or wear-and-tear. | Predictive tasks based on real-time data and insights. | Varied tasks based on equipment importance, degradation, and risk. | Reactive tasks initiated by failure occurrences. | Immediate response tasks to critical failures. | Task initiated post-failure for repairs. |
Objective | Proactively ensure equipment reliability and prevent failures. | Prevent potential issues and extend equipment lifespan. | Predict and prevent failures based on data insights. | Optimize maintenance for equipment criticality and degradation mechanisms. | Reactively address immediate safety or operational concerns. | Urgently respond to safety-critical failures to mitigate risks. | Address failures to restore normal operations. |
Interval | Regularly scheduled intervals based on equipment needs and historical data. | Fixed intervals determined by manufacturer guidelines or past performance. | Dynamic intervals based on real-time equipment condition and predictive analysis. | Variable intervals based on equipment criticality, degradation, and risk. | No predefined interval, response is triggered by failure occurrences. | Immediate response triggered by safety-critical failure occurrences. | Immediate response post-failure for repairs. |
Focus on Equipment Importance | Prioritizes critical equipment based on its importance to processes. | Critical components are identified and scheduled for preventive tasks. | Prioritizes equipment based on predictive insights and criticality. | Recognizes varying importance of equipment and optimizes resources. | Reactively addresses failures as they occur, regardless of criticality. | Immediate attention to failures impacting safety or critical processes. | Reactive response to failures regardless of criticality. |
Resource Optimization | Prioritizes and optimizes both financial and personnel resources. | Efficiently allocates resources for scheduled preventive tasks. | Optimizes resources based on real-time insights and equipment importance. | Balances limited resources for optimal maintenance outcomes. | Reactive response might result in inefficiencies and increased costs. | Utilizes resources urgently to address safety-critical failures. | Resource allocation after the failure has occurred. |
Advantages | Improved efficiency, reduced costs, and enhanced equipment reliability. | Regular upkeep prevents major failures, reducing overall maintenance costs. | Timely maintenance based on real-time insights, enhancing reliability. | Efficient maintenance program, reducing unnecessary tasks. | Immediate response to critical failures, minimizing operational impact. | Urgent response to safety-critical failures, ensuring safety. | Addressing failures post-occurrence for continued operations. |
Disadvantages | Initial setup costs may be significant. Savings potential may not be immediately evident. | Regular scheduled tasks may lead to some unnecessary maintenance. | Requires investments in technology and training. Savings potential might not be immediately visible. | Initial setup costs might be high, and potential savings may not be immediately visible. | Reactive nature may result in higher costs, inefficiencies, and safety risks. | Reactive approach may lead to higher operational costs. |
Choosing the Right Maintenance Strategy: A Comprehensive Guide
Choosing the right maintenance strategy involves a careful evaluation of various factors and considerations. Here are some steps and considerations to guide you in selecting the most appropriate strategy:
Risk Assessment:
- Evaluate the potential risks associated with equipment failure.
- Consider the consequences in terms of safety, production loss, and financial impact.
Cost Analysis:
- Compare the cost of potential equipment failure with the cost of implementing different maintenance strategies.
Proactive vs. Reactive:
- If the cost of failure is greater than the cost of repairs, a reactive maintenance strategy may be suitable.
- If the cost of failure is higher, a proactive maintenance strategy may be more beneficial.
Impact on Production:
- Analyze the time it takes for maintenance to occur under different strategies.
- Consider the impact of maintenance on production schedules and overall efficiency.
Customer Impact:
- Assess whether customers will be impacted by equipment failures.
- Consider the potential damage to the business’s reputation and customer satisfaction.
Combination of Strategies:
- Recognize that different equipment or systems may require different maintenance approaches.
- Implement a combination of strategies based on the nature and criticality of assets.
Lifecycle Considerations:
- Consider the lifecycle stage of the equipment.
- Proactive maintenance may be beneficial for critical assets, while reactive maintenance could be economical for equipment near the end of its lifecycle.
Utilize Maintenance Management Software:
- Implement maintenance management software, such as CMMS (SAP), to automate tasks, streamline processes, and maintain an overview of maintenance activities.
- Utilize technology to carry out maintenance tasks more effectively and economically.
Legal and Compliance Risks:
- Consider legal and compliance risks associated with equipment failure.
- Proactive maintenance can help in meeting regulatory requirements and reducing legal risks.
Continuous Improvement:
- Regularly review and assess the effectiveness of the chosen maintenance strategy.
- Adopt a culture of constant improvement and modify your plans in response to changing equipment requirements and business needs.
Key Benefits of Maintenance
Maintenance is critical to helping businesses operate smoothly and cost-effectively. Companies can save money and avoid delays by maintaining their equipment, machinery, and facilities. However, the benefits of maintenance are contingent on how well it is planned and done. Let’s look at why maintenance is important and how it might benefit your organization.
- Extend the Life of Assets
Regular maintenance, such as inspections, cleaning, and servicing, helps expensive equipment last longer. This not only saves money by delaying replacements, but also ensures that operations function smoothly. - Boost Performance
Maintaining assets ensures optimal performance and consistent results. This increases efficiency and production, ultimately leading to a higher return on investment (ROI). - Prevent Unexpected Downtime
Breakdowns can halt operations, resulting in delays and financial losses. Proactive maintenance helps to avoid these delays and ensures that everything goes as planned. - Save Money in the Long Run
Industrial machinery and equipment represent considerable investments. Regular maintenance reduces the chance of costly repairs or replacements, allowing organizations to get the most out of their assets.
Maintenance vs. Repairs
While both maintenance and repairs aim to keep operations running smoothly, their approaches differ.
Aspect | Maintenance | Repairs |
Definition | Proactive actions taken to keep equipment in good working condition. | Reactive actions taken to fix equipment after a failure or breakdown. |
Goal | Prevent issues and extend the lifespan of assets. | Restore functionality after a problem occurs. |
Approach | Planned and scheduled activities. | Unplanned and urgent responses to failures. |
Frequency | Regular (daily, weekly, monthly, or as per a schedule). | Occasional, only when a breakdown happens. |
Cost | Low to moderate (preventive tasks are often inexpensive). | High (due to urgency, parts replacement, and potential downtime). |
Examples | Cleaning, lubrication, inspections, part replacements, and system monitoring. | Fixing a broken part, repairing a malfunction, or replacing damaged components. |
Impact on Operations | Minimizes disruptions by preventing failures. | Causes downtime until the issue is resolved. |
Resource Requirement | Requires dedicated personnel and a structured plan. | Requires skilled technicians and immediate availability of parts/tools. |
Risk of Downtime | Low (planned maintenance can be scheduled during non-peak hours). | High (unexpected breakdowns can halt operations). |
Long-Term Benefits | Extends equipment life, improves efficiency, and reduces overall costs. | Restores functionality but doesn’t prevent future issues. |
Examples in Practice | Weekly cleaning of machinery.- Monthly inspection of HVAC systems. | – Fixing a conveyor belt that has snapped.- Repairing a leaking pipe. |
Tools/Software Used | CMMS (Computerized Maintenance Management Systems) for scheduling and tracking. | Emergency repair tools and diagnostic equipment. |
Dependency | Relies on a proactive mindset and adherence to schedules. | Relies on quick response times and availability of repair resources. |
ISO Maintenance Standards for Enhanced Asset Management
The International Organization for Standardization (ISO) provides various maintenance standards that organizations can utilize to create best practices and ensure effective asset management.
Here are some important ISO standards for maintenance:
- ISO 55000 Series – Asset Management: Assists organizations of all sizes and industries in improving how they manage and maintain their assets.
- ISO 14224 – Collection of Reliability and Maintenance Data: Aims to standardize how industries such as petroleum collect data on equipment reliability and maintenance.
- ISO 9001 – Quality Management Systems: A general quality management standard that contains standards for effective maintenance processes that maintain the quality of products and services.
- ISO 18436 Series – Condition Monitoring of Machines: Provides guidelines for monitoring machine conditions, including principles, personnel qualifications, and training.
These standards help firms improve maintenance processes, improve asset performance, and meet industry standards for improved business outcomes.
Click here to know more about different Instrumentation maintenance procedure
FAQs about Maintenance
What is Maintenance?
Maintenance refers to the procedures used to keep equipment, machinery, or facilities in good operating order. It’s all about being proactive identifying and addressing possible concerns before they become huge problems.
What Does Maintenance Involve?
Inspecting, cleaning, repairing, and replacing parts are all examples of maintenance operations. These responsibilities ensure that systems and equipment are operating optimally and safely.
What Are the Types of Maintenance?
There are several types of maintenance, each serving a specific purpose:
- Preventive Maintenance: Regular checks to prevent issues.
- Corrective Maintenance: Fixing problems after they occur.
- Predictive Maintenance: Using data to predict and address potential failures.
- Condition-Based Maintenance: Monitoring equipment condition to determine when maintenance is needed.
How Do You Create a Maintenance Plan?
- To develop an effective maintenance plan:
- List all equipment and machinery.
- Prioritize them according to importance.
- Determine maintenance schedules for each group.
- For precise needs, refer to the manufacturer’s guidelines.
- Assign duties and verify that the plan is implemented consistently.
What’s the Difference Between PM and CM?
- PM (Preventive Maintenance): Scheduled tasks to prevent equipment failure.
- CM (Corrective Maintenance): Repairs done after a breakdown occurs.
What is PMO in Maintenance?
PMO (Planned Maintenance Optimization) is an approach for improving current maintenance procedures by studying previous failures and fine-tuning preventative maintenance routines.
What is PM in TPM?
PM (Planned Maintenance) is an aspect of Total Productive Maintenance (TPM) that focuses on scheduling and carrying out maintenance chores to enhance equipment efficiency and lifespan.
What is the maintenance concept?
The maintenance concept should include a concise summary of the system/equipment under development’s maintenance considerations, restrictions, and operational support plans as determined from the Concept of Operations (CONOPS).