- Generally, the term maintenance in industries means increasing assets productivity & reducing failure to avoid accidental damage.
- Both these maintenance activities deliver better advantages in that these activities shrink the failure rate of machines and enhance the safety of expensive materials.
- Work orders for each maintenance sort are organized before the maintenance task to ensure both sorts of scheduled maintenance
- Usually, the maintenance is classified into Predictive Maintenance, & Preventive Maintenance.
What is Predictive Maintenance?
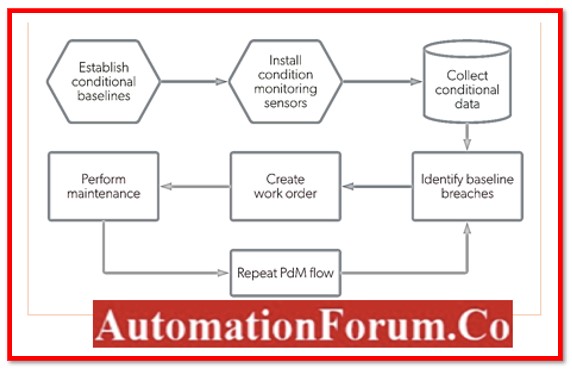
- Predictive Maintenance is organized on resource conditions.
- Predictive Maintenance minimizes the cost of labor and material required.
- The term predictive maintenance activity is quite similar or interrelated to preventive maintenance,
- Because some preset conditions are essential for this preventive maintenance
- In our human health comparison, this element is comparable to screenings or measures suggested for an individual who is in greater danger for a particular illness due to adopted or lifestyle habits.
- Technicians trigger a predictive maintenance protocol for a convenient schedule for repair to avoid future damage or accidents in case a part of the machine performs abnormal parameters.
- For this, a Computerized Maintenance Management System (CMMS) is advisable because this system delivers essential measurements and data that are required to adopt the smart resolution.
- This CMMS reduces unexpected maintenance tasks, reduces the cost required for maintenance, and builds a strong maintenance program for monitoring equipment and system to stay in running mode.
- However, establishing a predictive maintenance strategy involves a significant investment in terms of money, training, and resources. These costs tend to be acceptable to companies that effectively carry out a preventive upkeep program.
Advantages of Predictive Maintenance
- Proactive
- The actual problem is identified before they are addressed
- Shorter downtime
- Inventory efficiency is good
- Based on contemporary data, this report provides a wide range of alternatives for maintenance practices.
- Avoiding catastrophic breakdowns and spotting emerging issues with machines and systems.
- The automatic capability to track the mean-time-between-failures, (MTBF) is a side benefit of predictive maintenance.
- Eliminate unnecessary maintenance
- Reduce lost production caused by failures
- Reduce repair parts inventory
- Increase process ef?ciency
- Improve product quality
- Extend operating life of plant systems
- Increase production capacity
- Reduce overall maintenance costs
- Increase overall pro?ts
Disadvantages of Predictive Maintenance
- More complex
- Not as scheduled as preventive maintenance
- Requires advanced technology to share data with a centralized system
- Needs additional training
What is Preventive Maintenance?
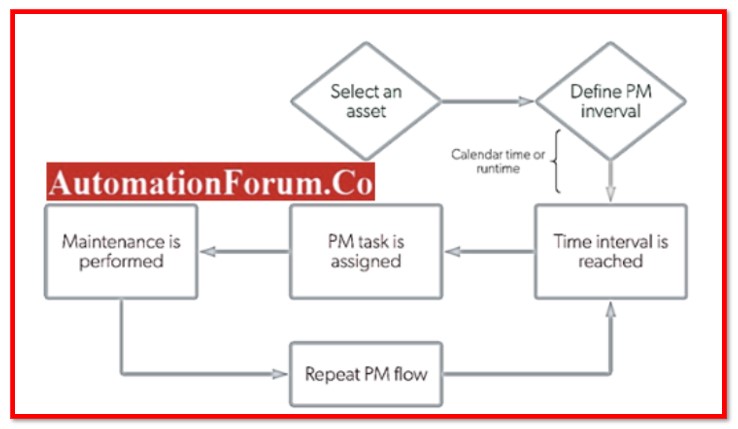
- Preventive maintenance is organized on a regular basis.
- Preventative maintenance is simpler to execute.
- Preventive maintenance is collated for a physical check-up annually.
- Technicians execute this maintenance task to avoid future breakdowns or emergency maintenance issues even in smooth-running conditions.
- Preventive maintenance is a physical checkup to prevent equipment failures and extend resource span like we consult a doctor to prevent illness or lengthen our life.
- Additionally, preventive maintenance balances the expanse cost, & return costs of resources.
- Maintenance managers having better experience should make a smart resolution for the preventive maintenance of machines
Advantages of Preventive Maintenance
- Proactive
- Limits unplanned downtime
- Increases equipment lifespan
- Efficient for experienced staff.
- Enhance capital equipment productive life.
- Reduce critical equipment breakdowns.
- Allow better planning and scheduling of needed maintenance work.
- Minimize production losses due to equipment failures.
- Promote health and safety of maintenance personnel
Disadvantages of Preventive Maintenance
- Increases planned downtime
- Improved inventory management for replacement parts.
Predictive Maintenance Vs Preventive Maintenance
Predictive Maintenance | Preventative Maintenance |
Triggers on Time | Triggers on Condition |
This is conducted to predict the occurrence of failures | This is conducted to avoid assets from unexpected damages. |
This is performed as per the schedule | This is performed on a routine basis. |
Here it is not required to stop the main function of the resource, because diagnostics of machine can easily be performed even if the resource is executing its usual functions. | The resource’s downtime must be increased, which means required functions can be stopped. |
Maintenance is performed when potential flaws are detected. | Maintenance is performed even if potential flaws may not be detected. |
Complexity is more and is much more difficult than preventive maintenance. | Complexity is very less and is quite easier than predictive maintenance. |
Less expensive than preventive maintenance. | Highly more expensive than predictive maintenance. |
It avoids unpredictable expenses, hence no more investment. | It doesn’t avoid unpredicted expenses, hence needs investment. |
Requires less time for simple periodic inspection and maintenance. | Requires more time for simple periodic inspection and maintenance |
Cost Savings in Predictive Maintenance 25% to 30% | Cost Savings in Preventive Maintenance is about 12% to 18% |
Predictive maintenance is typically carried out to foresee potential breakdowns so that they can be avoided. | Preventive maintenance is often carried out to guard against sudden asset breakdown. |
Only when probable problems are found in this does maintenance take place. | Even if probable faults are not detected in this, maintenance is carried out. |