- Step 1: Safety Precautions
- Step 2: Work Permit and Lockout-Tagout (LOTO) Requirements
- Step 3: Bypassing the Flowmeter
- Step 4: Required Tools and Equipment
- Step 5: Required Drawings and Documents
- Step 6: Risk Assessment
- Step 7: Pre-Maintenance Inspection
- Step 8: Zero Point Check and Adjustment
- Step 9: Coriolis Mass Flowmeter Parameter Verification
- Step 10: Fault Indication Check
- Step 11: Sealing and Insulation Inspection
- Step 12: Coriolis Mass Flowmeter Cleaning and Fouling Removal
- Step 13: Periodic Calibration Verification of Coriolis Mass Flowmeter
- Step 14: Maintenance in Special Circumstances
- Step 15: Completion and Documentation
- Checklist for Inspection and Maintenance of Coriolis Mass Flowmeters – Download
- Coriolis Mass Flowmeters Maintenance Best Practices
- How to clean a Coriolis flow meter?
Coriolis mass flowmeters are used extensively because of their reliability and accuracy in determining fluid temperature, density, and mass flow rates. Regular inspection and maintenance are essential to guaranteeing their stable, long-term operation. The maintenance of Coriolis mass flowmeters in a process area is covered in detail in this document, with a focus on efficiency, safety, and best practices.
Step 1: Safety Precautions
- Ensure all personnel involved in the maintenance are trained and competent.
- Wear appropriate personal protective equipment (PPE)
- Verify the area is safe and free from hazards such as high-pressure fluids, corrosive gases, or electrical risks.
- Confirm the system is depressurized and isolated before commencing work.
- Use safety barriers and signage to restrict unauthorized access to the maintenance area.
- Follow process area-specific safety protocols and emergency response procedures.
Step 2: Work Permit and Lockout-Tagout (LOTO) Requirements
- Obtain the necessary work permits (e.g., hot work, confined space, electrical isolation permits) before starting.
- Adhere to the LOTO procedure to de-energize and isolate the flowmeter from the process line.
- Verify the zero-energy state by checking for residual pressure, flow, or electrical activity.
- Document all isolation points and ensure proper communication with operations and maintenance teams.
Step 3: Bypassing the Flowmeter
- Identify and operate the correct bypass valves to divert the flow around the flowmeter with help of process Engineers.
- Confirm that the bypass line is functioning correctly and that the main line is fully isolated from the flowmeter.
- Monitor the bypass operation using system flow indicators or feedback signals to ensure uninterrupted process flow.
- Communicate bypass activation and deactivation to all relevant process personnel.
Step 4: Required Tools and Equipment
- Standard maintenance tools (e.g., wrenches, screwdrivers, multimeters).
- Cleaning tools (e.g., brushes, non-corrosive cleaning agents).
- Sealing materials and replacement parts as per the manufacturer’s recommendations.
- Inspection aids such as flashlights, mirrors for hard-to-reach areas.
- Portable data logging devices( like HART communicators) for capturing diagnostic information.
Step 5: Required Drawings and Documents
- Flowmeter loop drawings and P&IDs (Piping and Instrumentation Diagrams).
- Isolation procedures and isolation valve lists.
- Bypass procedure.
- Manufacturer’s operation and maintenance manual.
- Risk assessment and Job Hazard Analysis (JHA).
- Maintenance records and flowmeter calibration history.
- Flowmeter datasheets, flowmeter manual and troubleshooting guides.
Step 6: Risk Assessment
- Identify hazards associated with the maintenance task (e.g., exposure to high-pressure process fluids, toxic gases).
- Implement control measures, such as additional isolation, ventilation, or the use of specialized PPE.
- Regularly review and update risk assessments based on site-specific conditions.
Step 7: Pre-Maintenance Inspection
- Examine the flowmeter’s exterior for physical damage, such as dents, cracks, or visible wear.
- Look for corrosion on the flowmeter’s body, particularly at joints, flanges, and fittings.
- Inspect the sensor wiring ports to ensure all seals are intact and there is no evidence of wear or damage.
- Verify that no dust, moisture, or corrosive materials have entered the wiring ports.
- Inspect the flowmeter mounting, pipeline vibrations, and transmitter functionality.
- Ensure electrical connections are secure and free from corrosion or damage.
- Evaluate display readings for consistency with process conditions.
- Examine the pipeline linked to the flowmeter for symptoms of severe vibration, which might reduce measurement accuracy.
- Ensure that the flowmeter is securely placed and properly aligned with the process piping.
- To avoid misalignment or stress on the device, ensure that the support structures are strong and that the flowmeter is properly secured.
- Examine the installation environment for potential risks such as high humidity, corrosive gasses, or severe temperatures that could impair the flowmeter’s operation.
- Check that insulation or heat tracing systems, if installed, are working properly.
Refer the below link for the best practice in Coriolis Flow Meter Installation
Step 8: Zero Point Check and Adjustment
- Ensure that the flowmeter sensor pipeline is entirely filled with process fluid.
- Close the downstream valve to generate a no-flow condition in the flowmeter.
- For fluids that are susceptible to vaporization, apply enough back pressure to keep the liquid phase stable.
- Make zero-point adjustments according to the manufacturer’s instructions.
- To exactly adjust the zero point, use a calibrated instrument(HART communicator) or the built-in diagnostic tools.
- Record the corrected zero-point value for future reference.
- Compare the newly corrected zero-point value to the earlier recorded value.
- Calculate the zero drift that has occurred since the last correction and consider its impact on measurement accuracy.
- If severe zero drift is discovered, determine and correct the root cause. Common causes include: Installation stress causes damage to the flowmeter, Asymmetry in the measurement tube’s structure and the process fluid’s physical properties change.
- Repeat the zero-point adjustment procedure multiple times until the most accurate and stable zero-point value is obtained.
- Ensure constant circumstances during each change to avoid introducing errors.
- Keep a complete record of all zero-point adjustments, including the initial and adjusted values, Measurement errors are calculated as a result of zero drift and actions made to address any underlying issues that may be causing a lot of drift.
Step 9: Coriolis Mass Flowmeter Parameter Verification

- Check the working parameters, such as flow rate, density, and temperature, against the expected values. To find discrepancies, compare the data to their baseline or standard values.
- Verify the transmitter parameters, including calibration factors, range configurations, and communication protocols, to ensure they are in accordance with process requirements.
- If you see any inconsistencies, perform zero flow calibration. This includes recalibrating the meter under controlled settings in order to reduce offsets or errors.
- Document all findings properly, including parameter settings before and after calibration. Identify any substantial deviations or changes made to ensure traceability.
- If abnormal behavior persists after calibration, refer to the manufacturer’s documentation for additional guidance.
Click here to know more about Coriolis mass flowmeter basics
Step 10: Fault Indication Check
- Review the flowmeter’s fault indicators or alarm messages for any active alerts.
- Refer to the product manual to identify and address the root cause of any faults.
- Cross-check the fault codes with historical records to determine if the issue is recurring.
- Inspect wiring, connections, and environmental factors (e.g., humidity, dust) that may contribute to the fault.
- Take corrective actions such as replacing damaged components, recalibrating the meter, or addressing external conditions causing the fault.
- Reset alarms after successful troubleshooting to restore normal operation.
- Document the fault details, resolution steps, and any preventive measures implemented to avoid recurrence.
Step 11: Sealing and Insulation Inspection
- Inspect seals and gaskets for wear, cracks, or corrosion, especially in settings with corrosive gasses, excessive humidity, or dust.
- To prevent impurities from entering the system, ensure that all wire ports are correctly sealed.
- Examine the insulation and heat tracing systems on flowmeters that operate at high temperatures or measure crystallizable fluids.
- Ensure that the heat tracing devices offer uniform coverage and that the insulation is intact and properly attached.
- Replace or repair any broken insulation to avoid temperature changes that could compromise the flowmeter’s functioning.
- Document your results and ensure that any repairs or replacements are made with materials that are suitable with the process environment.
Step 12: Coriolis Mass Flowmeter Cleaning and Fouling Removal
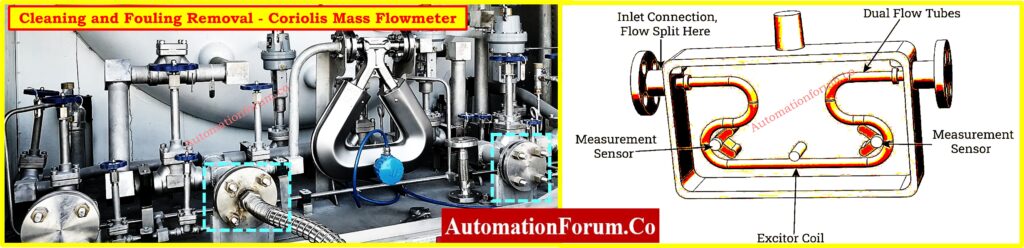
- If fouling is suspected (e.g., scaling or wax buildup), first remove the sensor from its installation point.
- This ensures the fouling issue can be addressed safely without impacting the surrounding equipment.
- Use approved cleaning methods specific to the sensor type.
- Chemical Cleaning: Use solvents or cleaning agents to dissolve or loosen buildup.
- Mechanical Brushing: Physically remove deposits with care to avoid damaging the sensor.
- Take special care to protect delicate components, such as measuring tubes, during cleaning.
- Inspect the sensor for remaining debris or signs of damage.
- Carefully reinstall the cleaned sensor in its original position.
- Perform a zero-point check or calibration to ensure proper functionality and accurate measurements.
- Only bring the system back online after confirming the sensor’s functionality and accuracy.
Step 13: Periodic Calibration Verification of Coriolis Mass Flowmeter
Verify flow meters on a regular basis against a recognized standard or comparison meter. This ensures the correctness of the measurements.
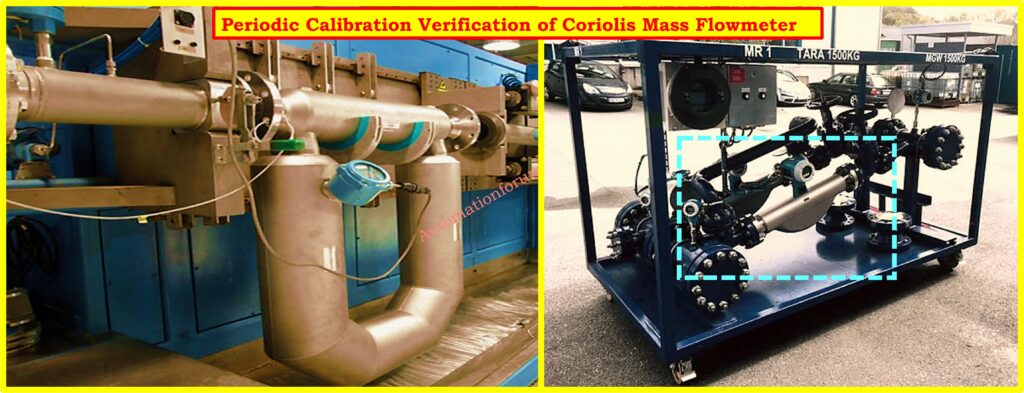
- Check the flowmeter on a regular basis to ensure it is working properly and meets industry standards.
- Annual verification of trade settlement applications is often necessary to ensure regulatory compliance.
- For other applications, verification can be scheduled twice annually, according to manufacturer recommendations, or based on operating needs.
- Maintain detailed documentation of the verification process, including the results, the date of verification, and any discrepancies identified.
- This documentation is critical for regulatory compliance and timely resolution of any issues.
- If differences or defects occur during the verification, modify the flowmeter’s calibration parameters accordingly.
- Calibration should be performed in accordance with the manufacturer’s specifications or using appropriate calibration equipment.
- Regular verification helps to preserve the accuracy of the flowmeter throughout time, reducing the risk of measurement error and ensuring the overall system’s efficiency and safety.
- It also contributes in satisfying industry standards, regulatory requirements, and ensuring operational reliability.
Step 14: Maintenance in Special Circumstances
- For intermittent flow measurement: Check for false metering caused by transient flows or overlooked readings.
- For heat-traced installations: Regularly inspect insulation and heat tracing systems to ensure proper functioning.
- For fouling-prone fluids: Increase inspection frequency and proactively clean the sensor as needed.
Step 15: Completion and Documentation
- Reassemble the flowmeter and reconnect it to the process line, ensuring all connections are secure.
- Gradually bring the flowmeter back online and verify its operation under normal process conditions.
- Record all maintenance activities, including findings, adjustments, and verification results, in the flowmeter’s logbook.
- Update the flowmeter’s maintenance file with detailed reports and calibration certificates.
- Close all bypass valves and return the system to its normal configuration.
- Communicate task completion to relevant stakeholders and obtain sign-off from the responsible authority.
Checklist for Inspection and Maintenance of Coriolis Mass Flowmeters – Download
Our Coriolis Mass Flowmeter checklist ensures accurate maintenance, safety compliance and reliable operation in industrial processes.
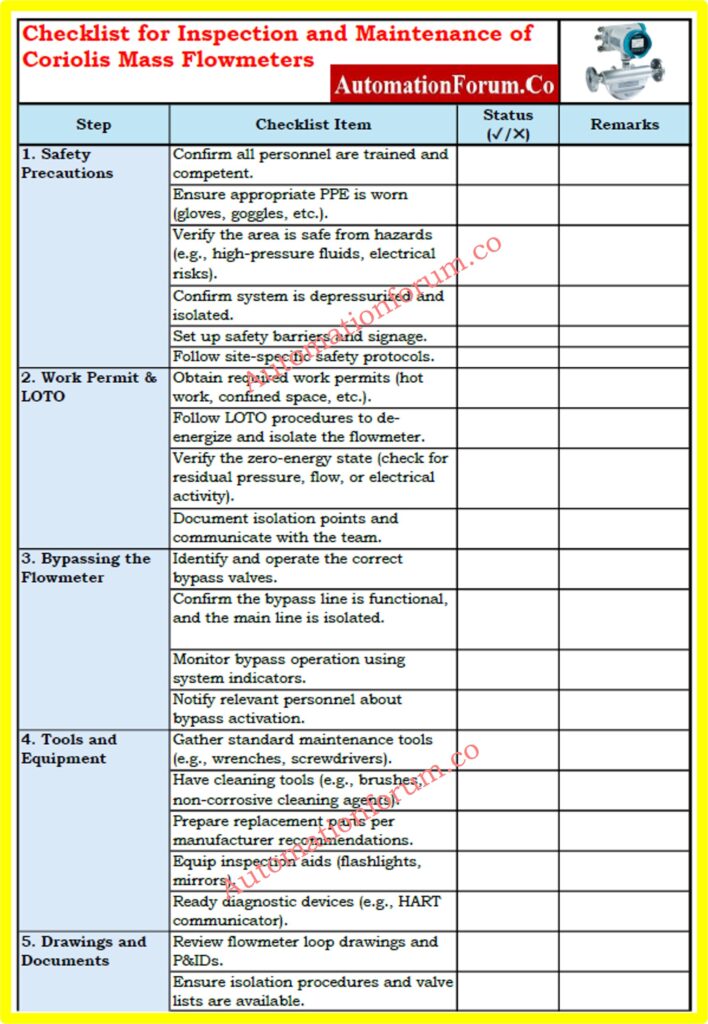
Refer the below link to download the Checklist for Inspection and Maintenance of Coriolis Mass Flowmeters in excel form.
Click here for 50+Collection of Essential Instrumentation and Automation Control System Checklists
Coriolis Mass Flowmeters Maintenance Best Practices
- Create a routine inspection schedule based on process criticality and operational conditions.
- Maintain a spare parts inventory that includes seals, gaskets, and common replacement components.
- Train maintenance professionals about flowmeter use, diagnostics, and troubleshooting.
- Review manufacturer updates or technical notes on a regular basis to identify opportunities for product enhancement.
- Use predictive maintenance techniques, such as vibration analysis or diagnostic monitoring, to detect potential problems early.
How to clean a Coriolis flow meter?
To remove high-viscosity oil attachments and fouling from the measuring tube of the Coriolis mass flowmeter, the following steam purging and cleaning approach is recommended:
- Combine the line sweeping steam from the petrochemical plant with an adequate volume of circulating water. This should be connected to the flowmeter via a steam line.
- Place the flowmeter flat on the ground, with the bottom slightly raised, to ensure that the flow tube is inclined. This will allow the wastewater to discharge itself.
- Ensure that the steam outlet pressure does not exceed 0.5MPa.
- The steam temperature should not go above 110°C.
- To prevent steam ingress, seal the flowmeter’s junction box properly.
- Direct the wastewater into the appropriate oil discharge channel.
- Start by cleansing the flange.
- Then, systematically purge the flowmeter’s two measurement tubes, beginning with the intake and ending with the outlet.
- The purging and cleaning operation should be completed only when there are no visible stains or foreign elements in the washing solutions.
- After linking the flowmeter to the transmitter and turning it on, verify the density indicator value. It should be about zero.
- If the indication value is high, it means that there is still foreign matter in the measurement tube and more cleaning is needed.
- If the physical and chemical qualities of the measuring tube attachments are known, it is recommended that the cleaning process be completed with a suitable solvent.
- After cleaning and testing the sensor’s performance, reinstall it and run a zero-point check. Before restarting operation, ensure that the flowmeter has been accurately calibrated.
- This procedure ensures that high-viscosity oils and fouling are effectively removed from the Coriolis mass flowmeter while retaining safety, accuracy, and functionality.
Click here for What is a Coriolis flowmeter and how does it work