A PLC can be described as an advanced computer and it is used in many industrial applications mostly it is used in the automation section. The PLC can handle multiple inputs and outputs, it has good temperature ranges, immune to electrical noise, and can handle vibrations or impact. A PLC can be considered as a real-time system because the output results must be produced in response to input conditions at a period of time.
- What are the components of a PLC?
- PLC communications
- What are the types of programming languages used in PLC?
- What are the different operating modes in PLC?
- Difference between Modular PLC & Compact PLC:
- What is Sinking and Sourcing?
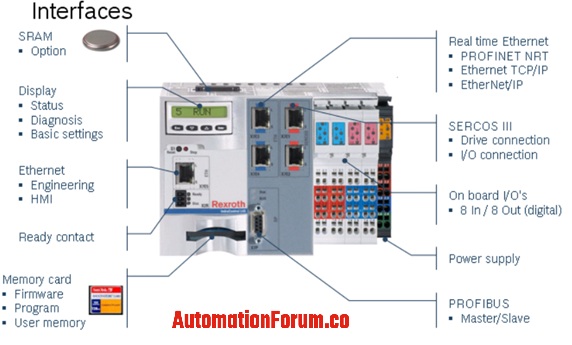
What are the items that is needed while working with a PLC?
- Programming terminal which would be a laptop or desktop PC
- PLC software
- Cables to connect with the PLC and the computer
- Documentation(PLC manual, software manual, drawings, printout of the program, and operation manual)
What are the characteristics of the PLC?
- The PLC is programmed according to the user’s requirement and due to this the user can write and change the program in the field without rewiring
- It has preprogrammed functions the PLC consist of logic, timing, counting, and memory functions and all these functions can be accessed by the user with the help of control-oriented programming languages
- It scans memory and input in a deterministic manner and because of this, the user can determine how a process will respond to the program.
How to select a PLC?
- It must be selected according to the number of logical inputs and outputs, the output ports must be capable to supply the required output voltage and current which is required to drive the output peripherals that is connected to it
- Memory – The memory required for an application will be related to the length of the program and the control system complexity. We must choose a memory that would have a little bit of space after entering the program
- Number of special I/O modules
- It must be selected according to the scan time, the scan time is the time taken by the controller to execute the program.
- Communications
- Software
- Compatibility to HMI
- While choosing a PLC we need to make sure that the existing products are compatible with the PLC
- We must also consider environmental factors like temperature, pressure, etc.
- Vibration must be considered while selecting a PLC, like if the PLC is going to be installed near vibrating equipment.
- It must be selected according to the programming, certain PLCs won’t support every instruction, so we must keep this in mind will choosing a PLC.
What is the need for the PLC?
- Highly distributed I/O’s
- The equipment can be located on the plant floor
- More than one cell or subsystem
- Discrete and analog control with a small amount of complex batch, blending, or multivariable analog control
How to do the troubleshooting and maintenance of a PLC?
The PLC has a resident diagnostic and overrides function and by this, the user can easily trace and correct the software and hardware problems. The control program can be watched in real-time when it executes to find the problem. The PLC troubleshooting consists of three processes and they are understanding how the application operates, finding the problem, and correcting the problem.
Troubleshooting
Before troubleshooting the PLC the personnel must know how the system works and how the different component in the system works. The problems can also arise due to the malfunction of the field device or because of the loose wiring in the field device and there could be programming errors in a control system that has never worked.
If the PLC runs properly then its power and RUN LED would be on and there won’t be any indication of the fault. If the fault LED is on then we can use the HHP or PC running PLC software to determine the reason for the fault.
If all the LEDs in the PLC are off then we must check if the PLC has proper power with the voltmeter. So if there is any kind of power problem we need to check all the wiring connections are ok and there are no broken wires. The power from the circuit breaker must be checked and after checking the PLC power we need to check the communication with the controller and it can be done with the help of HHP or PC running PLC software. If the communication is ok then the PLC is running properly, after that we need to check the field device, field power, and field wiring.
Mostly the PLC troubleshooting is done at the output’s by the technicians and this is because it is the fastest and easy procedure. Mostly we can know a problem in a PLC if there is an action that fails to occur. We can start the troubleshooting by checking the LED’s if there is power at the output terminal then the PLC is working, if the output LED is on and the devices are not on then we should test for power at the suspended output terminal, if there is no power at the PLC output terminal then the PLC has failed and it should be replaced.
Check the power at the non-functioning output device and if there is power at the output terminal then the device is faulty and this device must be fixed or replaced. In another case, there won’t be any power at the device, so there could be a blown fuse at the field wiring or a wiring fault between the PLC and the device. If there is no problem with the PLC and the device then we must check the program and verify the rungs that don’t have any outputs. So if this is the problem then we need to check which instructions need to be true in order to activate the outputs and we need to start tracing to determine which condition is not satisfied.
Preventive maintenance
The preventive maintenance in PLC can decrease the failure rate of the system components. The PLC preventive maintenance can be performed in the regular maintenance of the machine or the equipment. We must follow the safety procedure during the execution of the work. We must execute the safety procedure because we can avoid the work accident by doing the safety procedure.
Back-up PLC program
We can save a PLC program copy during the maintenance, so by doing that we are ensuring the backup. So this backup will be helpful if the PLC is faulty or to be replaced then we can download this backup program to the new PLC.
Check the LED indicators
We must look at the LED indicators if the power LED indicator is flickering or off, and if it is the same for the battery indicator then it means that there is a problem in the battery or in the power source.
Operating environment
We must check the operating environment, like the temperature, humidity, and other environmental factors. So that we can make sure that the PLC is operating in proper conditions. The PLC must not be placed to the equipment that creates heavy noise or generating heat
Check the operating voltage and program functionality
We must check the input voltage of the PLC so that we can determine if the voltage is in the proper range and we can also ensure that there are no power spikes. We can check the program functionality during the routine check so that we can make sure that the system which is being controlled is operating properly.
Check the components
We must look for overheated components, check the CPU and modules for distorted, warped, or discolored cases. The circuit card which is for the analog process control must be calibrated every six months and we also need to service the sensors monthly.
Check the venting and also check for the dust
We must make sure that the PLC components are free from dust. The I/O units and the CPU in the PLC are not designed to handle dust. We must make sure that the PLC and module cooling vents are not blocked by any debris or dust. If there is any filter that is installed in enclosures should be cleaned or replaced so that we can make sure that the air circulation is present in the enclosure.
Check the PLC connection
We must check all the communication cables, plugs, sockets, terminal strips, wiring, and modules are connected properly. If the PLC is located in a place where there is a lot of vibration then it could loosen the connections in the PLC. So we must do this check frequently if the PLC is not located in a vibration-free environment.
What are the advantages of PLC?
- Easily reprogrammable
- Flexibility
- Commissioning with simulation
- Large quantity of contacts
- Easy troubleshooting
- Speed
- Reliability
- Security
- Energy saving
What are the applications of PLC?
- Tire industry
- Bulk material handling system at ports
- Steel plants
- Wagon loaders
- Steel plants
- Blast furnace charging
- Pulp industry
- Printing industry
- Diary automation
- Power
- Chemical