- Step 1. Understanding the Purpose of a PLC Datasheet
- Step 2. General Overview of the Allen-Bradley 1762-L24BWA
- Step 3. Power Supply and Electrical Ratings
- Step 4. Inputs and Input Circuit Characteristics
- Step 5. Outputs and Output Ratings
- Step 6. Memory and Data Handling
- Step 7. Communication Ports and Protocols
- Step 8. Expansion Capability
- Step 9. Physical Dimensions and Mounting
- Step 10. Environmental Ratings
- Step 11. Certifications and Compliance
- Step 12. Application Examples
- Step 13. Final Notes and Tips
- What are the data files in a PLC?
- What are PLC data inputs?
- What are PLC details?
- What is PLC memory?
- How many data types are there in a PLC?
- Test Your Knowledge on Understanding PLC Hardware Components
Reading a PLC datasheet may be scary at first, but it is an essential ability for any automation expert. Knowing how to get relevant data from the datasheet can help you guarantee correct device selection, effective control logic implementation, and safe system integration whether you are a PLC programmer, system designer, or installation technician. This post will guide you through reading and understanding the datasheet of the Allen-Bradley 1762-L24BWA, a MicroLogix 1200 family member.
Step 1. Understanding the Purpose of a PLC Datasheet
A PLC datasheet is an engineering document detailing the main features and characteristics of the controller. It offers knowledge of the physical traits, environmental tolerances, certifications, communication interfaces, memory, I/O capacity, and electrical needs.
Reading a datasheet is about understanding how the device will perform under real-world circumstances and making sure it fits your application needs, not only about locating numbers.
Step 2. General Overview of the Allen-Bradley 1762-L24BWA
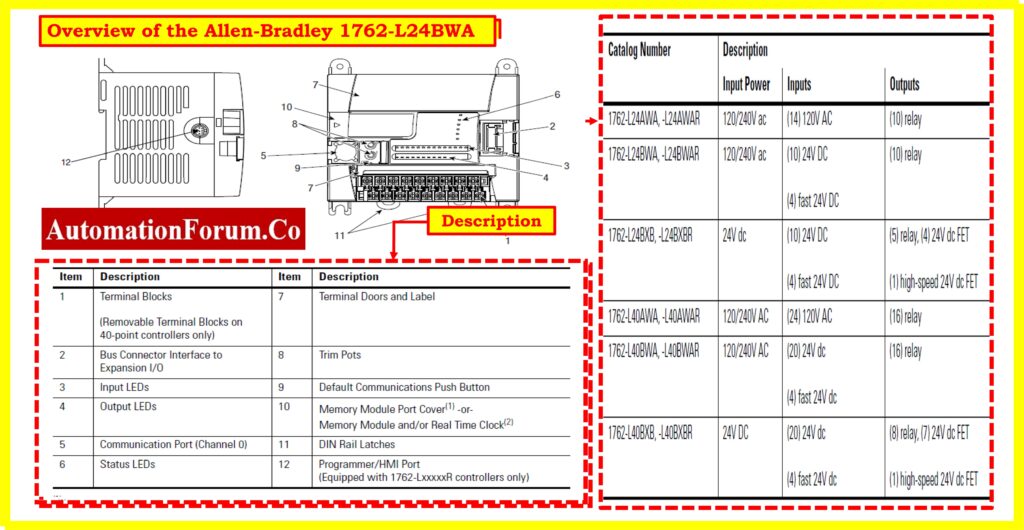
With built-in inputs and outputs, an integrated power supply, and communication ports, the 1762-L24BWA is a small, all-in-one PLC. Designed for mid-range control applications, it belongs to the MicroLogix 1200 series.
Key features include:
- ten relay outputs and fourteen digital inputs
- RS-232 port of communication
- Expansion capacity with 1762 I/O modules
- Input for AC power supply is 100–240V AC.
- Built-in 24V DC sensor supply output
Applications like machine control, conveyor systems, and small process automation tasks fit this controller well.
Step 3. Power Supply and Electrical Ratings

- Input Voltage Range: 100–240V AC, 47–63 Hz
- Inrush Current: 25 A @ 120V AC (8 ms), 40 A @ 240V AC (4 ms)
- Power Consumption: Approx. 70 VA
- Sensor Supply Output: 24V DC, 250 mA max (used for powering input devices only)
Click to Learn: How to Calculate and Minimize Voltage Drop in PLC Wiring?
The datasheet further lists isolation voltage ratings:
- Isolation Between Terminals and Internal Logic: 1500V AC RMS
- Dielectric Test of Withstand: Guarantees component protection and electrical safety
Note: These specifications help to make sure your field equipment don’t draw more current than allowed and help to choose fuses and surge protectors.
Must-Know Basics: Top 6 Important Rules for PLC Ladder Diagram Programming
Step 4. Inputs and Input Circuit Characteristics
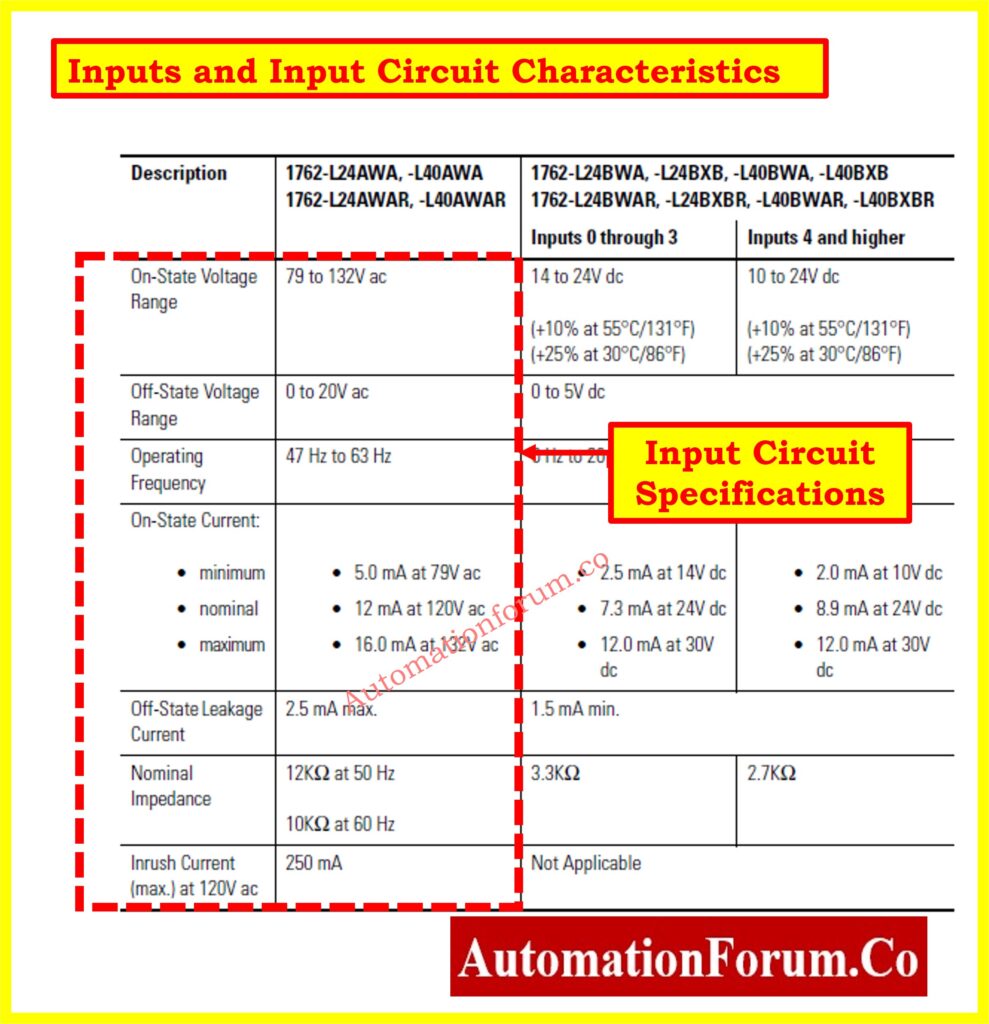
Fourteen digital inputs on the 1762-L24BWA can be set for either sourcing or sinking as desired.
- Nominal Input Voltage: 24V DC
- Input Signal Delay (Debounce Filter): Adjustable from 0.8 ms to 10 ms
- Input Leakage Current: ~1.5 mA @ 30V DC
- Input Thresholds:
- On-state: ? 10V DC
- Off-state: ? 5V DC
A subset of these inputs allows for high-speed counting (HSC), permitting input of encoder pulses or comparable rapidly changing signals.
Note: You, as an installer, must understand voltage compatibility. HSC inputs are essential for motion or speed-based logic for programmers.
Read This First: Understanding PLC Redundancy: Cold, Warm & Hot Redundancy
Step 5. Outputs and Output Ratings
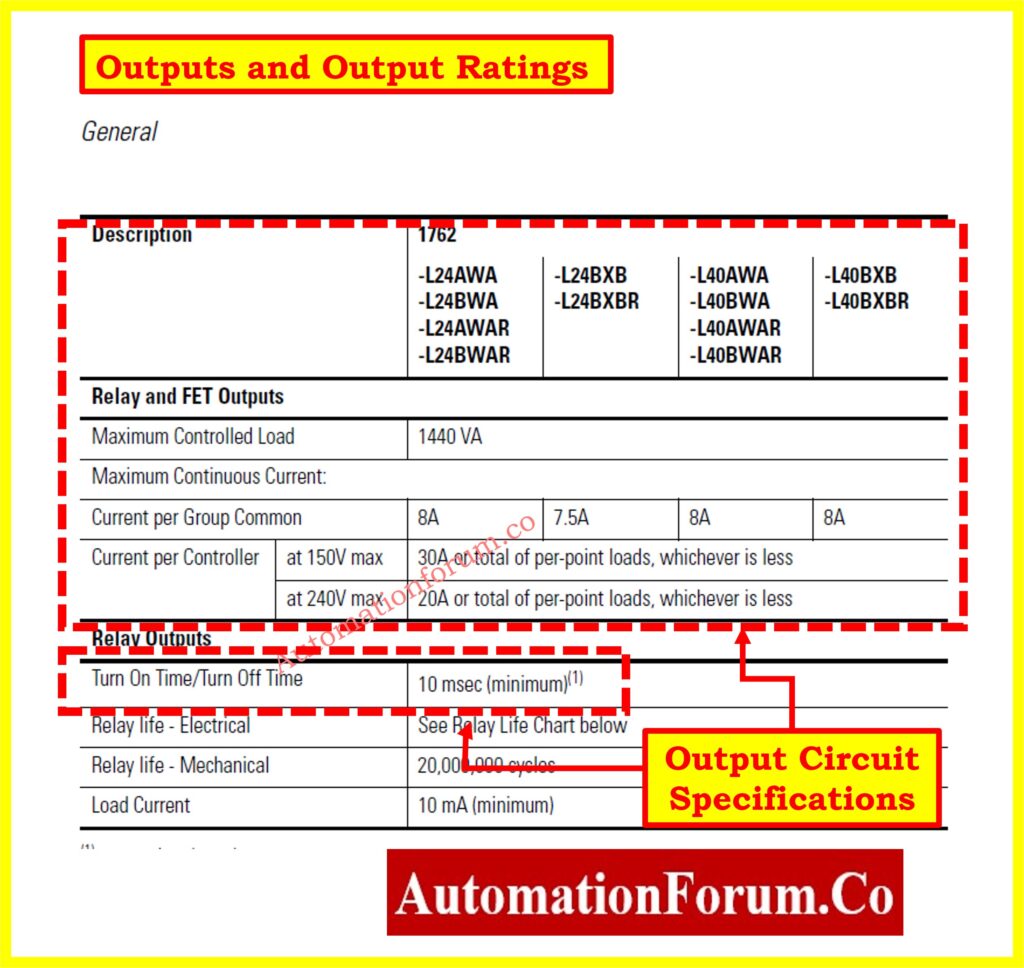
Suitable for both AC and DC load switching, there are 10 relay outputs. Because relay outputs are mechanical, the type of load affects how long they can switch.
- Operating Voltage Range: 5–125V DC or 5–265V AC
- Max Continuous Current per Point: 2.0 A
- Max Current per Output Group: 7.5 A
- Total Max Output Current: 20 A
- Isolation Between Relay Contacts and Logic: 1500V AC
Relay contact life depends on by:
- Load type (resistive vs inductive)
- Switching frequency
- Load current
Note: Relay outputs can wear out more quickly in high-speed or inductive applications. If required, use solid-state output modules or external relays.
Must-Know Security Tips: How to Safeguard PLCs Against Cyber Attacks in Industrial Networks ?
Step 6. Memory and Data Handling
Full memory requirements are in the MicroLogix 1200 reference manual, which the datasheet itself directs users to; main elements include:
- User Memory: around 6 KB for data and ladder logic
- Data Files: Configurable data structures for bit arrays, integers, counters, and timers
- Memory preservation: Data preservation in the event of a power outage is ensured by an optional EEPROM backup system (1762-MM1).
- RTC Support: For timestamping and scheduling logic, Real-Time Clock module (1762-RTC) adds RTC support.
Note: Remember that enough RAM guarantees your software will fit. Data loss is prevented with EEPROM backup. RTC enables time-sensitive automation and scheduling.
Must Read for Installers: Sinking and Sourcing: Which Connection is Best for Your PLC?
Step 7. Communication Ports and Protocols
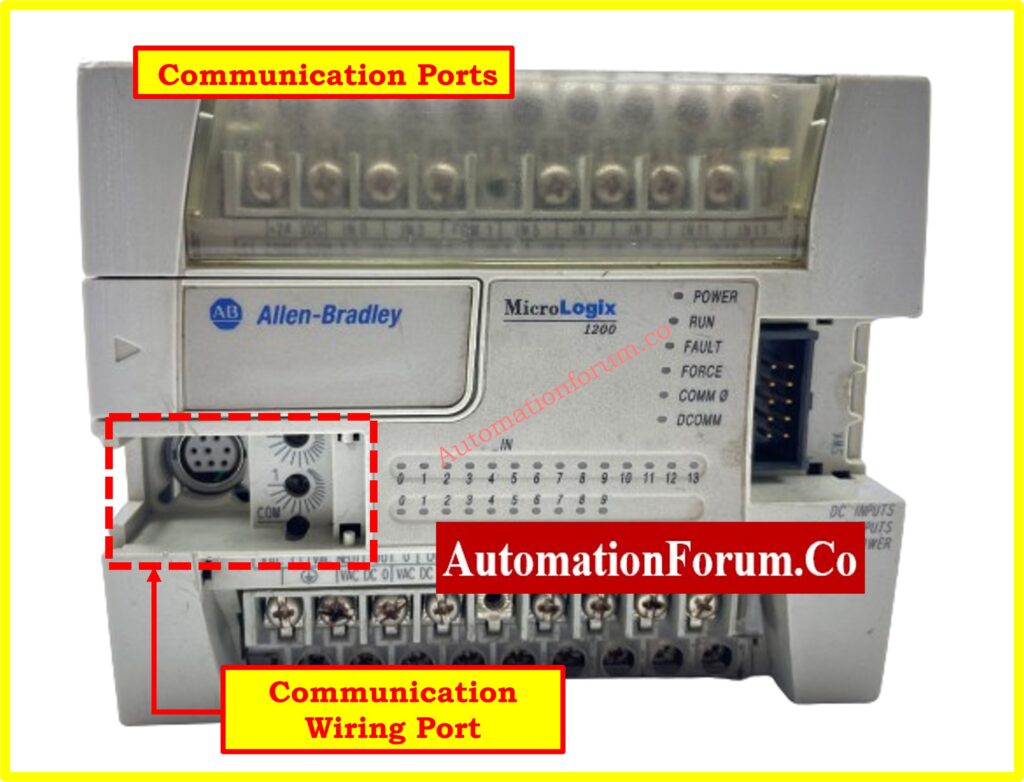
The 1762-L24BWA includes:
- Channel 0 – RS-232: DF1 full-duplex, ASCII, or Modbus RTU protocol
- Communication Baud Rates: Configurable (usually 1200–38400 bps)
Communication can be used for:
- Programming via RS-232 (using RSLinx and RSLogix 500)
- Linking to SCADA or HMI panels
- Device interface or data logging (using ASCII)
Note: Ethernet/IP is not built-in; it may be added via gateways or communication modules.
Note: Modern integration, remote diagnostics, and data collecting all depend on communication.
Click and Understand: Understanding PLC Racks and Chassis: Types, Differences, and Purposes
Step 8. Expansion Capability

Unlike certain small PLCs, the 1762-L24BWA permits expansion using specific I/O modules:
- Module Compatibility: Up to six 1762-series extension modules
- Types available include specialized modules (RTC, high-speed counter), digital and analog I/O.
Bus Current Draw (Backplane):
- Modules can receive up to 450 mA from the base unit.
Note: Keep in mind power use and mounting space even if you may increase your system by including more I/O.
Step 9. Physical Dimensions and Mounting
Correct installation guarantees durability and serviceability.
- Mounting Options: DIN rail or panel mount
- Orientation: Horizontal (to maintain thermal limits)
- Dimensions:
- Width: 110 mm
- Height: 90 mm
- Depth: 87 mm
- Clearance Requirements: 50 mm above/below for airflow and wiring
Note: These measurements influence enclosure size. To avoid overheating, appropriate airflow is required.
Step 10. Environmental Ratings
The data from the environment reveals the precise location where the PLC can be positioned safely.
- Operating Temperature: 0°C to 55°C
- Storage Temperature: –40°C to +85°C
- Relative Humidity: 5–95% non-condensing
- Shock:
- Operating: 30G
- Non-operating: 50G
- IEC 60068-2-6 states that the vibration is 1.5 millimeters at a frequency of 10–55 hertz.
Note: Knowing this helps in choosing enclosures, particularly for industrial or outdoor settings.
Step 11. Certifications and Compliance
This PLC meets several international standards:
- UL Listed
- CSA Certified
- CE Marked
- Class I, Division 2, Groups A, B, C, and D T4 (compliant with rules governing hazardous locations)
- RCM, EAC (Eurasia)
Note: If your project is in oil & gas, food, pharma, or other regulated industries, certifications are a must.
Step 12. Application Examples
To bring it all together, let us investigate usual uses:
- Machine Control: Logic for actuators, sensors, and safety interlocks
- Material Handling: Control of conveyors and sorters
- Packaging Lines: Time-based logic with relay actuation
- Small Process Automation: Water treatment skids, dosing systems, HVAC
Step 13. Final Notes and Tips
- Not all datasheet values are directly valuable; learn to emphasize what matters for your position.
- For a complete picture, cross-reference datasheet data with installation instructions, user manuals, and wiring diagrams.
- Check the environmental and electricity parts first if you are unsure; these are the most installation-critical.
- Think about lifecycle planning: relay outputs degrade, memory fills up, communication requirements change.
Reading a PLC datasheet like that of the Allen-Bradley 1762-L24BWA is about knowing the capabilities and limits of the controller, not only a box-checking task. The capacity to read technical papers will be very vital as automation systems grow more sophisticated. Mastering this ability will enable you to create better, diagnose quicker, and carry out more dependable automation systems.
FAQ on PLC DataSheet
What are the data files in a PLC?
Data files in a PLC hold information on inputs, outputs, timers, counters, and other control components. By means of these files, the PLC may track and operate various systems and devices effectively by helping to organize and manage the data utilized during automation activities.
What are PLC data inputs?
Signals from sensors, switches, or instruments linked to machines make up PLC data inputs. These inputs let the PLC decide and act on the system by providing real-time data, such as turning on motors or opening valves.
What are PLC details?
A PLC (Programmable Logic Controller) is a robust computer used in industrial settings to manage machines and operations. It receives input signals, uses software to process them, and outputs signals to control things like lights, pumps, and motors.
What is PLC memory?
PLC memory holds system information, data, and programs. It has non-volatile memory (which retains data when the power is off), random-access memory (RAM), and ROM (which contains firmware). Power loss clears RAM; ROM and non-volatile memory preserve vital data.
How many data types are there in a PLC?
PLCs support a wide range of standard data types, including characters, strings, booleans (true/false), floating-point numbers, and integers (8 to 64 bits). These kinds enable the PLC manage several sorts of data for several automation activities and computations.
Test Your Knowledge on Understanding PLC Hardware Components
Refer the below link to test your knowledge on Understanding PLC Hardware Components