- What is a PLC Rack?
- Definition of a PLC Rack
- Rack-Mounted or Modular PLCs: An Overview
- Block Diagram of Rack-Mounted PLC
- Types of PLC Racks in Modular PLCs
- Differences Between PLC Rack and Chassis
- Purpose of the Rack or Chassis in a PLC
- Comparison between Active and Passive Backplane PLC Racks
- Types of Rack Configurations in Modular PLCs
- Practical Example: Implementing a Modular PLC with an Active Backplane
- Applications and Benefits of Rack and Chassis in Industrial PLCs
- Key Takeaways on PLC Racks and Chassis
- Ready for Quiz on PLC hardware:
Programmable Logic Controllers (PLCs) are essential in industrial automation for managing complex processes and systems. They come in various types and configurations, most notably Fixed PLCs and Modular PLCs. Modular PLCs are commonly known as Rack-mounted PLCs, given their structure and functionality within the industrial environment.
This article provides an in-depth look at the rack and chassis of a PLC, explaining the types of racks, the differences between racks and chassis, and their purposes.
What is a PLC Rack?
- In modular PLC systems, racks and chassis are essential components. They serve as the core structure for mounting and connecting all necessary modules within the PLC, such as input, output, CPU, power supply, and communication modules.
- This setup allows for flexibility, easy configuration, and the ability to expand based on application needs.
Definition of a PLC Rack
- A PLC rack or chassis is a physical framework that organizes and holds modules together.
- It acts as a centralized assembly where each module is securely plugged in, ensuring connectivity and power supply across the system.
- The power supply unit, situated within the rack, provides regulated power to all modules through a backplane bus system, which is crucial for effective communication between modules.
Rack-Mounted or Modular PLCs: An Overview
- The Rack-mounted Programmable Logic Controller (PLC) or Modular PLC makes use of a rack framework to connect many modules, which enables efficient data interchange and coordination.
- Rack-based designs are useful for scalable industrial applications because they enable the addition or replacement of modules without affecting the entire system. This makes rack-based designs appropriate for use in industrial settings.

Block Diagram of Rack-Mounted PLC
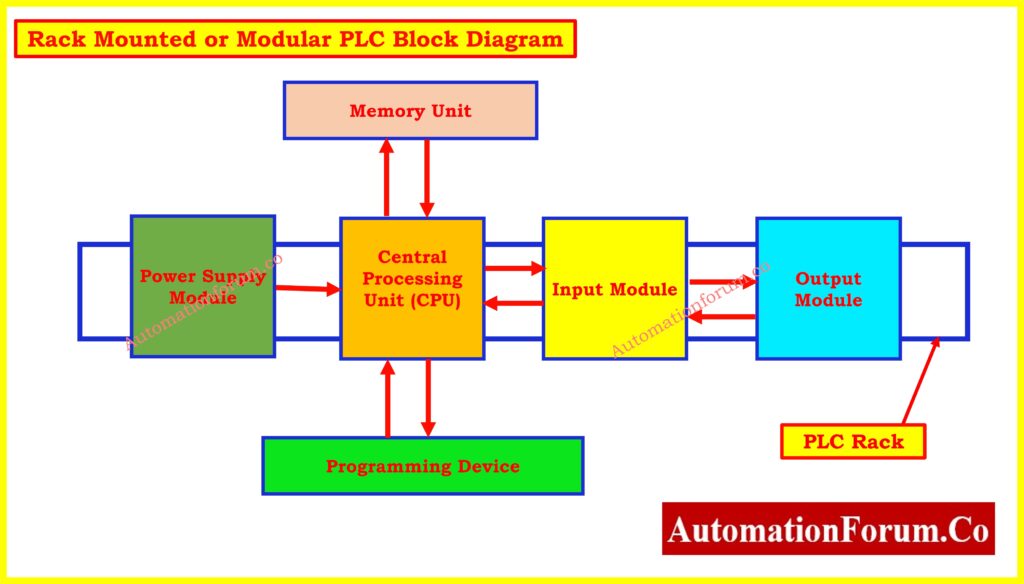
A typical rack-mounted PLC consists of:
- A power supply module
- A central processing unit (CPU)
- Input and output modules
- Communication modules
Modules are inserted into the designated slots on the backplane. The backplane serves as the primary circuit board, enabling communication and power distribution between modules.
Types of PLC Racks in Modular PLCs
Modular PLC racks utilize two main types of backplanes, each with specific roles in enabling module communication and power distribution. The types are Active Backplanes and Passive Backplanes.
Active Backplane
An Active Backplane consists of multiple slots and additional circuitry, enabling control over the communication between slots.
Active backplanes are commonly used in Siemens S7-400 PLCs, which support three types of racks:
- Central Rack (CR): Houses essential modules, such as the CPU, power supply, and base input/output.
- Universal Rack (UR): Expands functionality and can be used for various additional modules.
- Expansion Rack (ER): Allows further extension of the system’s capacity by adding more modules without replacing the main rack.
Passive Backplane
A Passive Backplane includes only slots for modules and lacks additional circuitry. This design relies on the modules themselves for communication. Passive backplanes are typically found in Siemens S7-300 PLCs and offer a more simplified and cost-effective option for smaller PLC setups.
Differences Between PLC Rack and Chassis
Considering their frequent interchangeability, rack and chassis have some minor differences. When setting up or growing a PLC system, it is crucial to understand these differences.
PLC Rack
- The rack in a PLC serves as a cabinet or frame to house all connected modules, providing a stable and organized layout for easy access and maintenance.
- Racks come in various sizes, such as 9-slot or 18-slot versions, and allow users to choose a configuration suitable for their system’s needs.
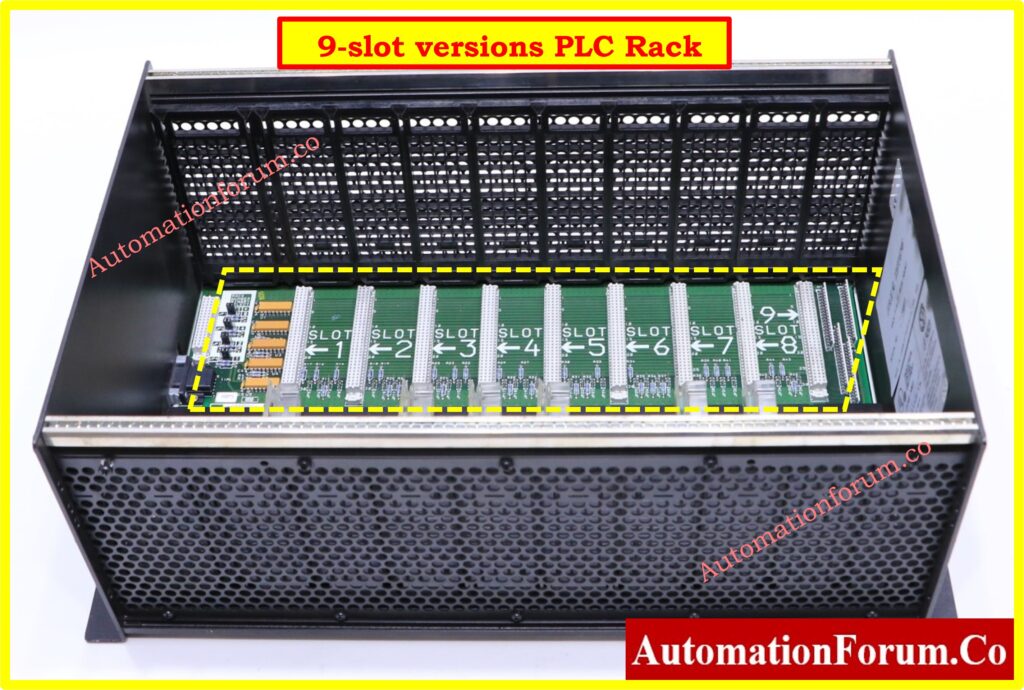
PLC Chassis
- The chassis in a PLC system is a piece of hardware with designated slots for inserting individual modules.
- It enables multiple chassis to be interconnected, allowing a PLC system to expand beyond the main rack.
- By using interconnecting cables, users can add additional chassis for further modules, increasing the overall capacity and flexibility of the system.
Purpose of the Rack or Chassis in a PLC
Racks and chassis serve multiple functions in modular PLC systems, enhancing both functionality and ease of maintenance.
Below are the key purposes:
- Power Distribution: Racks and chassis distribute regulated power from the power supply module to all connected modules through the backplane.
- Interconnectivity: They ensure inter-module communication, allowing data to flow seamlessly between input, output, and processing units.
- Flexibility for Expansion: Rack-mounted PLCs allow for easy modification or expansion, making it simple to add input or output modules as needed.
- Fault Isolation: In the event of a fault, individual modules can be quickly removed and replaced without impacting the entire system.
- Physical Support: Racks and chassis provide structural support, organizing modules within a compact, robust frame for secure mounting and reduced wear.
Comparison between Active and Passive Backplane PLC Racks
Feature | Active Backplane | Passive Backplane |
Structure | Includes additional circuitry | Contains only slots for modules |
Communication | Controls inter-slot communication | Depends on modules for communication |
Common PLC Use | Siemens S7-400 | Siemens S7-300 |
Rack Types | Central Rack, Universal Rack, Expansion Rack | Limited to basic rack configurations |
Suitability | Ideal for large, complex PLC systems needing high interactivity | Suitable for smaller, less complex PLC setups |
Types of Rack Configurations in Modular PLCs
As described earlier, different types of racks are used depending on the system’s complexity and requirements:
- Central Rack (CR): Hosts core components (CPU, power supply) and serves as the main hub for the PLC.
- Universal Rack (UR): Used for various expansion modules; it can serve multiple functions.
- Expansion Rack (ER): Enables additional modules to be added, supporting scalability.
Practical Example: Implementing a Modular PLC with an Active Backplane
In an industrial environment requiring a robust, flexible, and expandable control system, the Siemens S7-400 PLC is often chosen due to its modular structure and use of an active backplane. This setup is well-suited for large and complex applications, such as manufacturing plants, power stations, or process automation systems.
Let look at how a rack and chassis configuration would be implemented, utilizing different rack types to create an efficient and scalable solution.
Central Rack (CR)
The Central Rack (CR) is the core of the Siemens S7-400 system. It houses critical components such as the CPU, power supply, and basic input/output (I/O) modules. In this setup:
- CPU Module: The CPU module is responsible for processing all data and executing control logic. It connects to other racks through the active backplane, allowing for seamless data exchange.
- Power Supply: A dedicated power module provides the required, regulated voltage across the rack, ensuring stable operation for all connected modules.
- Basic I/O Modules: These modules handle the essential input and output requirements, such as simple sensors or actuators, directly connected to field devices in the production area.
In this configuration, the Central Rack acts as the “brain” of the system, coordinating operations, managing communication, and powering modules across the entire setup. By using an active backplane, data is efficiently transferred between the CPU and I/O modules, ensuring real-time response to field data.
Universal Rack (UR)
The Universal Rack (UR) provides added flexibility and functionality by expanding the system’s capabilities. Typically installed adjacent to the Central Rack, the Universal Rack can support a range of additional modules, depending on the specific needs of the facility. Common uses include:
- Specialized I/O Modules: To handle more complex sensors or actuators, such as analog inputs/outputs, high-speed counters, or temperature modules.
- Communication Modules: Supporting fieldbus protocols (e.g., Profibus, Profinet, Modbus) to integrate with other PLCs, distributed control systems (DCS), or SCADA systems. These modules enable communication with other industrial devices, allowing the system to function as part of a larger automated network.
- Safety and Redundancy Modules: Used in critical applications that require high reliability and safety, such as emergency shutdown systems or fail-safe systems, these modules ensure system stability and safety even in fault conditions.
The Universal Rack greatly enhances the PLC’s adaptability to diverse applications, accommodating specialized modules and allowing integration with existing automation infrastructure. As the facility’s requirements change, the Universal Rack can be reconfigured to support new functionalities without altering the core system in the Central Rack.
Expansion Rack (ER)
The Expansion Rack (ER) serves as a platform for future growth, enabling the system to scale with the evolving needs of the industrial environment. It is often placed remotely or in another part of the facility to manage additional processes, reducing the need for long cabling to the main control area.
Key components and uses include:
- Additional I/O Capacity: The Expansion Rack can accommodate a wide range of input and output modules, allowing the PLC to interface with additional field devices and sensors as the production line or plant grows.
- Remote Processing Modules: These modules allow the Expansion Rack to act semi-independently, handling tasks and processes closer to the field, which is ideal for distributed control systems.
- Interconnecting Cables and Modules: The Expansion Rack is connected to the Central Rack via interconnecting cables and modules, ensuring that power and data are transmitted reliably across the entire PLC network.
Click here for Understanding Remote I/O in PLC Control Systems
Applications and Benefits of Rack and Chassis in Industrial PLCs
The rack and chassis setup in modular PLCs offers various benefits that make it an ideal choice in industrial environments:
- Increased System Flexibility: Easily add or swap modules, adapting to changing process requirements.
- Enhanced Reliability: Modular PLCs provide stable and organized mounting, reducing wear and enabling faster fault isolation.
- Scalability: Support for future expansion without needing extensive reconfiguration.
- Reduced Maintenance Time: Modules can be individually accessed, allowing for straightforward maintenance or replacement.
Key Takeaways on PLC Racks and Chassis
- Rack and chassis serve as the foundation for modular PLCs, providing the structure to mount, organize, and connect all modules.
- Active backplanes are ideal for complex systems with high communication needs, while passive backplanes suit simpler configurations.
- Modular PLCs allow for expansion, scalability, and flexibility, making them ideal for dynamic industrial environments where system requirements may change.
By understanding the structure and purpose of racks and chassis in PLC systems, engineers and technicians can make informed decisions about implementing and maintaining modular PLC setups that meet specific industrial demands.
Ready for Quiz on PLC hardware:
This below advanced PLC hardware components quiz is designed for professionals to test and enhance their knowledge of programmable logic controllers. Covering topics such as CPU functions, signal conversion, power supply roles, and more, this quiz provides a comprehensive review to ensure a solid understanding of essential PLC elements.
Click here for more PLC articles