Table of Contents
- Factor No.1: Module Failure
- Factor No.2: Power Supply Issues
- Factor No.3: Ground Integrity
- Factor No.4: Field Device Problems
- Factor No.5: Electrical Noise Interference
- Factor No.6: Network Communication Loss
- Factor No.7: Heat and Environmental Factors
- Factor No.8: Compatibility Issues
- Factor No.9: Memory Corruption
- Factor No.10: Cybersecurity Considerations for PLC Systems
- Factor No.11:Risk Management and Maintenance
- PLC Failure Causes and Mitigation Checklist
- In industrial environment, Programmable Logic Controllers (PLCs) play a crucial role in facilitating the operation of electronically controlled machinery.
- These PLCs translate user commands into actions that machines can understand and execute. Despite their significance, PLCs can encounter various issues leading to failure.
- Common causes of PLC failure include module failure, power outages, bad network connections, overheating, moisture, electromagnetic interference, among others.
- These issues can disrupt processes and even lead to system downtime, underscoring the importance of proactive maintenance and troubleshooting.
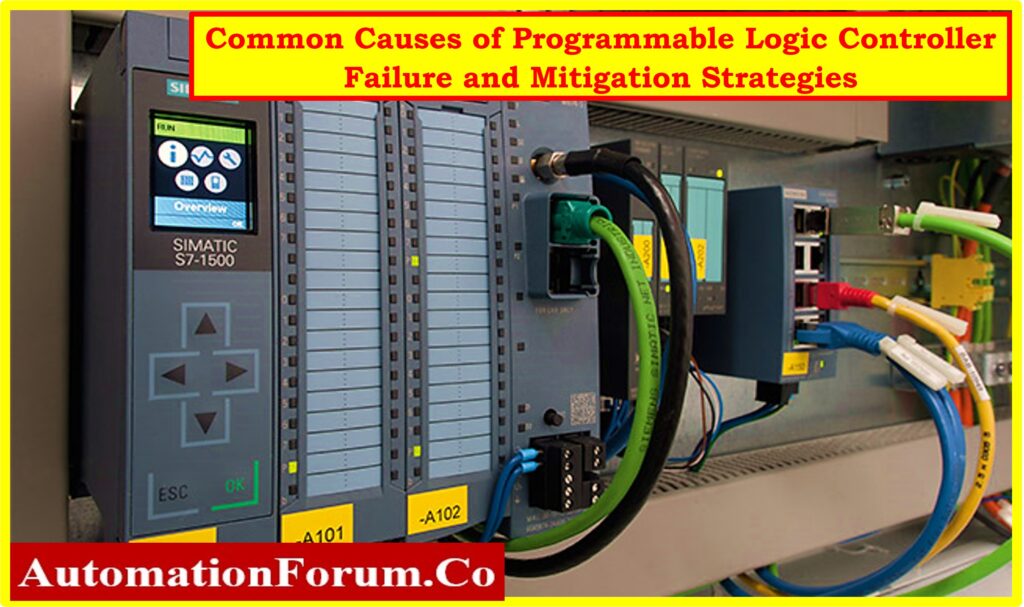
Factor No.1: Module Failure
- PLC modules, especially Input/Output (I/O) modules, are prone to failure due to various reasons such as manufacturing defects, wear and tear, or environmental factors.
- When a module fails, it can disrupt signal transmission between the PLC and connected devices, leading to operational issues or downtime.
- Engineers typically need to troubleshoot by inspecting the module, checking for loose connections, verifying proper power supply, and assessing for any configuration errors.
Factor No.2: Power Supply Issues
Voltage Fluctuations
- Variations in voltage levels can occur due to factors such as fluctuations in the grid, load changes, or electrical disturbances within the facility.
- These fluctuations can cause instability in the power supply to the PLC, leading to erratic behavior or failure.
- Voltage regulators or stabilizers can be employed to maintain a consistent voltage level and protect the PLC from damage caused by fluctuations.
Power Surges
- Power surges are sudden, brief spikes in voltage that can occur due to lightning strikes, switching operations, or faulty equipment.
- Surges can overwhelm the PLC’s internal circuitry, causing damage to components such as processors, memory modules, or input/output interfaces.
- Surge protection devices, such as transient voltage suppressors (TVS), surge protectors, or surge arresters, are installed to divert excess voltage away from the PLC and prevent damage during surge events.
Complete Outages
- Power outages, whether brief or prolonged, result in the loss of power to the PLC, causing it to shut down and interrupting industrial processes. To mitigate the impact of outages, industrial facilities often deploy uninterruptible power supply (UPS) systems.
- UPS systems provide temporary backup power to critical equipment like PLCs during outages, allowing them to continue operating or safely shut down processes to prevent damage or data loss.
Harmonics and Electrical Noise
- Harmonics and electrical noise, generated by non-linear loads or nearby electrical equipment, can distort the waveform of the power supply and interfere with the operation of the PLC.
- Filters, isolation transformers, or shielded cables are employed to minimize the effects of harmonics and noise on the PLC’s power supply, ensuring stable and reliable operation.
Factor No.3: Ground Integrity
- Programmable logic controllers (PLCs) are extremely important for both their safety and their performance, and it is absolutely essential to make sure that they are properly grounded.
The following are some significant uses of ground integrity:
Safety:
- Proper grounding helps to prevent electric shocks and potential hazards to personnel working with or near the PLC system.
- It ensures that any excess current is safely directed to the ground rather than flowing through unintended paths.
Protection against electrical noise:
- Grounding helps to minimize electromagnetic interference (EMI) and radio-frequency interference (RFI) that can disrupt the operation of the PLC system.
- It provides a reference point for electrical signals and helps to maintain signal integrity.
Equipment protection:
- Grounding can also protect the PLC system from damage due to transient voltage spikes or surges.
- By providing a low-resistance path to ground, it helps to dissipate excess voltage safely.
To maintain ground integrity, engineers should perform regular inspections of the ground wiring and connections. This includes:
- Checking for any signs of damage or corrosion in the ground wires.
- Ensuring that ground connections are securely tightened and free from loose connections.
- Using tools such as multimeters to measure resistance levels and ensure that ground connections have low impedance.
- Following manufacturer recommendations and industry standards for proper grounding techniques.
Factor No.4: Field Device Problems
- Field devices, such as sensors, actuators, motors, and other peripherals, play a crucial role in the operation of PLC systems within industrial environments.
- However, these external components are susceptible to various issues that can lead to PLC failure.
- Environmental factors, including moisture, temperature fluctuations, dust, and corrosive substances, pose significant risks to the functionality of field devices.
- Exposure to such elements can degrade the performance of sensors, impair the operation of actuators, or damage the components of motors, resulting in communication errors with the PLC.
- These errors can disrupt industrial processes and lead to unplanned downtime.
- To mitigate the risk of PLC failure attributable to field device problems, regular inspection and maintenance are imperative.
- Periodic checks allow for the detection of potential issues such as corrosion, wear and tear, or environmental damage.
- Maintenance tasks may include cleaning, calibration, lubrication, and the replacement of worn-out components.
- In cases where field devices are found to be faulty or beyond repair, timely replacement is essential to ensure the uninterrupted operation of industrial processes.
- Selecting replacement components that are compatible with the existing PLC system is crucial to avoid compatibility issues and minimize downtime during installation.
Factor No.5: Electrical Noise Interference
- Electrical noise, comprising electromagnetic interference (EMI) and radio frequency interference (RFI), poses a considerable threat to PLC performance in industrial environments.
- This interference can emanate from various sources, including large motors, lightning strikes, nearby antennas, and handheld transmitters. Such noise can disrupt the communication signals within the PLC system, leading to malfunctions, data corruption, or even system failures.
To mitigate the adverse effects of electrical noise on PLCs, several measures can be implemented:
Shielding and Filtering
- Shielding cables and equipment, as well as installing filters on power lines and signal cables, can help reduce the ingress of electromagnetic and radio frequency interference into the PLC system.
- Shielding materials, such as metallic conduits or ferrite cores, can effectively contain and divert noise away from sensitive components.
Grounding
- Proper grounding of equipment and electrical systems is crucial for minimizing electrical noise.
- Ground loops, which occur when multiple grounding points create unintended paths for electrical currents, can exacerbate noise issues.
- Implementing a single-point grounding scheme and ensuring that all equipment shares a common ground reference can help mitigate ground-related noise problems.
Isolation
- Isolating PLCs and sensitive equipment from sources of electrical noise, such as large motors or high-voltage equipment, can prevent interference from affecting the PLC’s operation.
- Physical barriers, such as enclosures or distance separation, can be used to segregate noisy machinery from PLCs.
Equipment Placement
- Careful placement of PLCs and associated equipment can help minimize exposure to sources of electrical noise.
- Avoiding placement near high-voltage equipment, electrical panels, or sources of electromagnetic radiation can reduce the likelihood of interference.
Prohibiting Handheld Devices
- Restricting the use of handheld devices, such as mobile phones or two-way radios, in close proximity to PLCs can prevent electromagnetic interference caused by these devices.
Factor No.6: Network Communication Loss
- Network communication is vital for PLC control systems in industrial environments, facilitating interaction between peripherals and human-machine interfaces through Ethernet cables and etc.
- When communication breaks down, it disrupts programmed functions, leading to downtime and decreased productivity in industrial facilities.
- Identifying root causes through system diagnostics is crucial, with potential issues often traced back to problems with the central processing unit.
- Failure to establish connections, degradation of network infrastructure, and CPU malfunctions affecting data processing and transmission are common culprits.
- Regular inspections of connections and cables, as well as ensuring the integrity of the physical infrastructure at all network points, are essential for preventing communication failures.
- Thorough inspections during device integration, along with the installation of firmware updates and security patches, help maintain network reliability.
- It is crucial to prioritize safe and secure operations, implementing measures to safeguard against security vulnerabilities and ensure uninterrupted communication.
Factor No.7: Heat and Environmental Factors
- Excessive heat and environmental conditions pose significant risks to PLC systems, potentially causing performance degradation or failure.
- To address these risks, facilities must implement effective heat management and environmental control measures.
Heat Management
- Adhere to manufacturer-recommended temperature limits to prevent component overheating.
- Install HVAC or dedicated cooling mechanisms to regulate temperatures and prevent heat buildup.
- Employ heat sinks, fans, or thermal insulation to dissipate heat efficiently and maintain operational stability.
Environmental Factors
- Control humidity levels and employ dehumidifiers, moisture-resistant enclosures, or sealing to mitigate moisture-related damage.
- Regularly monitor temperature and humidity levels to identify potential risks and intervene proactively.
- Use waterproof seals, gaskets, and cable glands to protect internal components from dust, debris, and moisture ingress.
Factor No.8: Compatibility Issues
- Changes to system configurations or peripheral devices can lead to compatibility issues, potentially causing PLC failure.
- Thorough testing and validation of system changes are essential to ensure seamless integration and operation.
Factor No.9: Memory Corruption
- PLC memory can become corrupted due to external factors like frequency interference or power outages, which can interfere with system operation and make the code unreadable.
- Implementing redundant storage solutions and protecting PLCs from interference sources help mitigate the risk of memory corruption and data loss. These measures safeguard PLC systems, ensuring uninterrupted operation in industrial environments.
Factor No.10: Cybersecurity Considerations for PLC Systems
As industrial automation becomes increasingly interconnected through networks and the internet, the risk of cyber threats targeting PLCs has also risen.
Here are some key points to consider regarding PLC cybersecurity:
Vulnerability Management
- PLCs, like any other computing device, can be vulnerable to cyber attacks.
- Manufacturers regularly release patches and updates to address known vulnerabilities.
- Implementing a robust vulnerability management program ensures that PLC systems are regularly updated with the latest security patches.
Access Control
- Limiting access to PLC systems through strong authentication mechanisms such as passwords, biometrics, or multi-factor authentication helps prevent unauthorized access.
- Additionally, role-based access control ensures that users have access only to the functionalities necessary for their roles.
Network Segmentation
- Segmenting industrial networks helps contain cyber attacks by isolating critical PLC systems from other parts of the network.
- This limits the impact of a breach and prevents lateral movement by attackers.
Intrusion Detection and Prevention Systems (IDPS)
- Deploying IDPS solutions helps detect and mitigate cyber threats in real-time.
- These systems monitor network traffic for suspicious behavior and can automatically block malicious activity.
Security Monitoring and Logging
- Logging and monitoring network and system activity provide visibility into potential security incidents.
- Analyzing logs for abnormal behavior helps detect and respond to security threats promptly.
Employee Training
- Educating employees about cybersecurity best practices, such as recognizing phishing emails, using secure passwords, and avoiding unauthorized software installations, helps mitigate the risk of human error leading to security breaches.
Incident Response Plan
- Developing and regularly testing an incident response plan ensures that organizations are prepared to respond effectively to cybersecurity incidents involving PLC systems.
- This includes procedures for containment, eradication, and recovery.
Encryption
- Encrypting sensitive data transmitted between PLCs and other devices over the network protects it from eavesdropping and interception by unauthorized parties.
Factor No.11:Risk Management and Maintenance
- To minimize the likelihood of PLC problems, area maintenance engineers must adhere to maintenance procedures and ensure proper environmental conditions.
- Neglecting maintenance can lead to costly system failures, particularly concerning issues like overheating and electrical noise interference.
- Employing backup power sources, conducting regular inspections of wiring, grounding, and network connections, and implementing measures to mitigate environmental risks are essential components of effective PLC risk management.
PLC Failure Causes and Mitigation Checklist
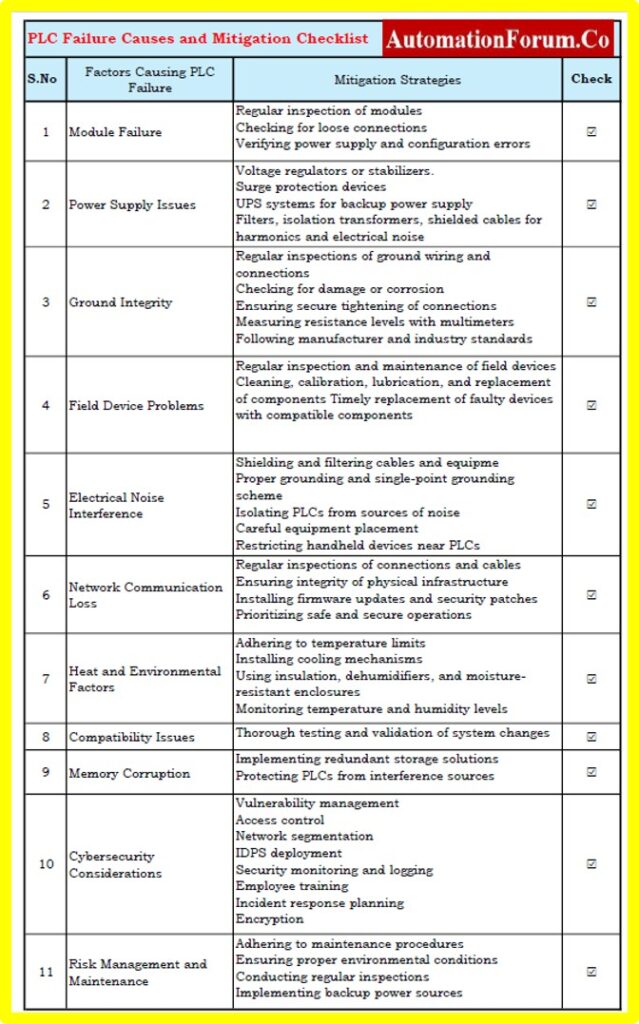
Here’s a simple Excel checklist in summarizing the factors causing PLC failure and corresponding mitigation strategies:
Click here for Getting Started with PLC Hardware and Software(PLC Basic to Troubleshooting)