Table of Contents
- What is a Factory Acceptance Test (FAT)?
- FAT Procedure for PLC panel
- Define the scope and the requirements
- Prepare the Test Team
- Set up the testing environment
- Preparing Documentation
- Verification of Documentation
- Visual Examination
- General Arrangement (GA) Validation
- Inspection of the Fabrication and the Outdoor Environment
- Visual confirmation
- Sequence of Power-Up
- PLC Power-On
- Uploading software
- Check Run Mode
- Testing Digital IO
- Analog IO Testing
- Examine the alarm and fault handling
- Tests of communication
- Testing of loaded PLC Program
- Human-machine interface (HMI) testing
- Testing for Performance
- Conformity Report
- Corrective Measures (if required)
- Client endorsement
- Site Acceptance Test (SAT) and Installation
- This article will show you how to do a Factory Acceptance Test (FAT) of a PLC (Programmable Logic Controller) Panel by giving you general rules and a step-by-step guide.
- PLC systems are an important part of industrial automation, and they are usually kept in control panels.
- Some of the electrical parts in these panels are contactors, switches, terminal boards, fuses, circuit breakers, and bus bars.
What is a Factory Acceptance Test (FAT)?
- FAT stands for Factory Acceptance Test.
- Factory Acceptance Testing (FAT) makes sure that newly produced and packaged equipment serves the purpose for which it was designed. The FAT confirms that the equipment is operational and that all other requirements, including the customers’ purchase order specifications, have been met.
What is PLC FAT?
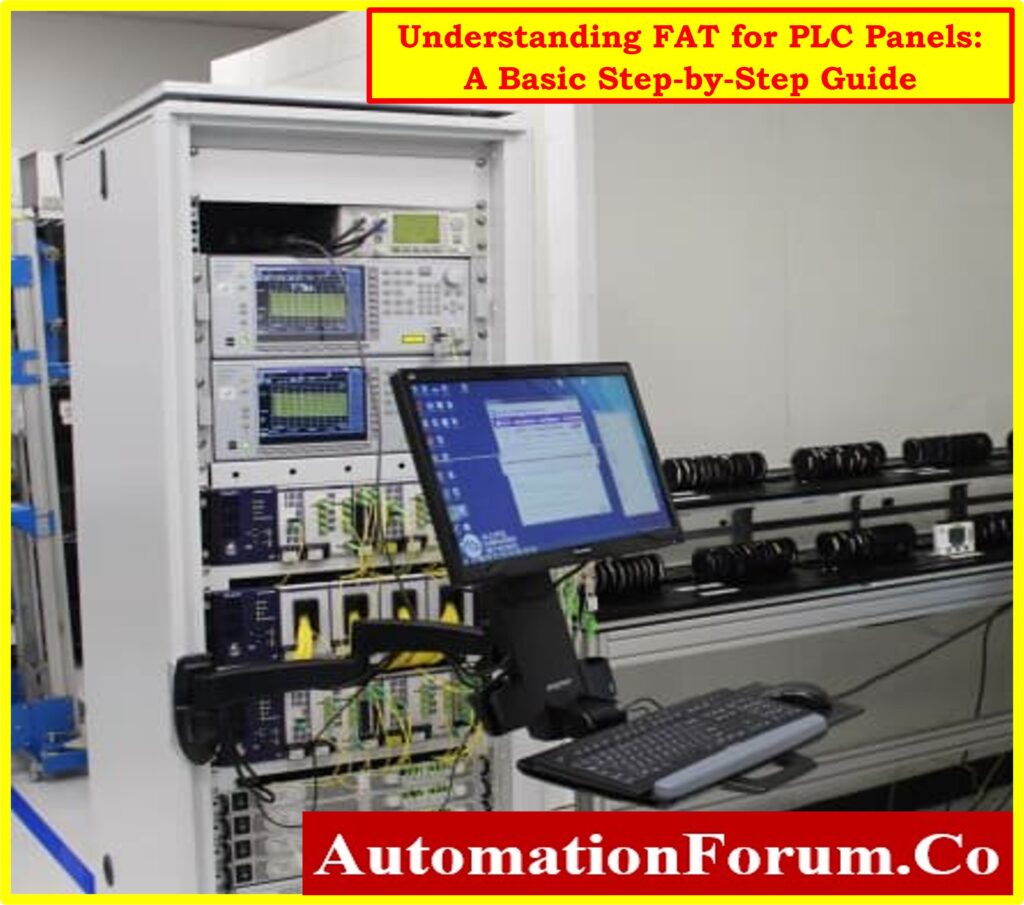
- A Factory Acceptance Test (FAT) is done on a PLC panel before it is sent to its end location and put to use.
- This important process makes sure that all of the parts are working right and that the system is working the way it was designed to.
- The FAT is done in front of the customer or their representatives, so they can be sure of the quality and performance of the system.
What is the FAT of the instrument panel?
According to the IEC 61511 standard, every instrument must pass a factory acceptance test (FAT) before being used in a final installation. In order to make sure that the machinery is built and operating in accordance with design standards, the FAT process entails testing it both during and after assembly.
FAT Procedure for PLC panel
Define the scope and the requirements
- Define the scope of the FAT clearly, including the exact requirements, functions, and performance criteria that the PLC panel must meet.
- Make sure you have all the necessary paperwork, such as project specifications, drawings, and functional design specifications.
Prepare the Test Team
- Put together a group of engineers and technicians who know the PLC system and how to program it.
- Give each team member an assignment and a set of responsibilities. This includes a test lead and technicians.
Set up the testing environment
- Set up a testing area with conditions that are as close as possible to the final installation location. This could involve simulating the process or system that the PLC panel is going to control.
- Make sure you have all the power sources, communication ports, and testing tools you need.
Let’s now get into the detailed steps for performing a proper FAT of a PLC panel:
Preparing Documentation
- Create the necessary paperwork first, including the IO list, electrical drawings, the panel’s GA, and a bill of materials (BOM).
- Send the customer a copy of these materials for review.
Verification of Documentation
- Make sure you have two copies of the approved documents in hard copy before the FAT one for your records and the other for the client to use as a reference during the inspection.
Visual Examination
- Allow the customer to visually inspect all components in accordance with the approved BOM when they arrive for the FAT. This process confirms that the panel has all of the materials that were promised.
General Arrangement (GA) Validation
- Inspect the GA of the PLC panel against the panel drawings (like System Cabinet and Marshalling Cabinet drawings) with the customer to ensure its correctness and conformity to requirements.
Inspection of the Fabrication and the Outdoor Environment
- Additionally, it is important for the customer to check the exterior aspects of the panel, such as the fabrication quality and the design of the gland holes.
Visual confirmation
- Before turning on any power, the FAT procedure requires first and foremost a visual inspection of all of the documentation and electrical panels.
Sequence of Power-Up
- After connecting the primary source of power to the panel, turn on the power.
- Check the terminal board with a multimeter to determine the voltage coming into the building. Check to see that the voltage between ground and neutral is not higher than 0.5 volts.
- Turn on the MCBs (Miniature Circuit Breakers) in the panel one at a time until they are all operational.
PLC Power-On
- When the MCBs are switched on, the panel’s components, including the PLC, receive their full power supply.
Uploading software
- Establish a connection between your laptop or desktop computer and the PLC, then download the most recent program backup.
Check Run Mode
- Put the PLC into run mode, and then check for any problems or mistakes that may have occurred. In the event that a Human-Machine Interface (HMI) or SCADA system is present, the final software for both should be downloaded and checked.
- Now it is time to inspect the inputs and outputs of the PLC. You should begin by looking at the digital inputs because of how the wiring is currently set up.
Testing Digital IO
- Start verifying that the inputs and outputs (IOs) of the PLC are functioning properly.
- Verify that the activation of the physical input results in the activation of the appropriate input address on the PLC. This can be done by checking the digital inputs.
- The matching PLC input address in the program must be turned on when the input is provided at the desired terminal point in the panel or elsewhere.
- Check the digital outputs and make sure that the physical PLC output comes on when the address that corresponds to it is turned on. If it is important, measure the voltage at the output.
Analog IO Testing
- Examine the analog inputs to ensure that they deliver the designated readings in accordance with the application. Use Simulator to test the analog input signals at AI terminals.
- Perform verification on analog outputs by checking to see if the actual counts or values produced by the PLC correspond to the values supplied.
- Conduct either a current or voltage test at the AO terminals that are currently connected.
Examine the alarm and fault handling
- Make sure the PLC panel handles alarms, errors, and fault circumstances properly.
- Check the PLC’s response to different problem scenarios to make sure it offers the right feedback and diagnostics.
Tests of communication
- Test the communication protocols and assure proper data interchange if the PLC panel connects with other devices or systems (such as SCADA, other PLCs, etc.).
- Check to see if security and data integrity controls are in place.
Testing of loaded PLC Program
- Test the newly build PLC program against supplied Control Narrative, Cause & Effect, RATS (Range, Alarm & Trip Sheet) and various other inputs and confirm its functionality is satisfactory.
Human-machine interface (HMI) testing
- Test the functionality of the human machine interface (HMI), including the display of relevant information, alerts, and operator interactions, if the PLC panel contains an HMI.
- Make sure the HMI is simple to use and intuitive.
Testing for Performance
- Examine the PLC panel’s performance under various load circumstances to make sure it satisfies the requirements for reaction time and processing speed.
Conformity Report
- Create a compliance report that provides a summary of the outcomes of all testing.
- Take note of any problems, defects, or checks that still need to be performed.
Corrective Measures (if required)
- Work with the manufacturer to identify and fix any problems or non-conformities found during the FAT.
- After taking appropriate action, retest the panel.
Client endorsement
- The PLC panel is prepared for delivery and the FAT is considered a success if the client accepts the testing procedure’ findings.
- One of the most important steps in ensuring the performance and quality of a PLC panel is to carry out a factory acceptance test.
- A system’s ability to function dependably in the environment it was designed for is ensured by carefully following these processes, which helps establish confidence among customers.
Site Acceptance Test (SAT) and Installation
- After the PLC panel has been installed at the location, a Site Acceptance Test (SAT) should be carried out to check that it functions appropriately in the environment for which it was designed.
Click here for Site Acceptance Test (SAT) Procedure for PLC Systems