- What are the major functional units of SCADA?
- What are the major functions of SCADA to control an industrial process?
- How SCADA simulator does the process simulation?
- SCADA Simulator
- What are the major requirements of a SCADA system simulator?
- Why do we need SCADA and how can it provide security for the industrial processes?
- What are the advantages of the SCADA simulator?
A SCADA system is used for industrial process control, basically, it is a computer-controlled system that can monitor and transmit commands to improve the industrial process. So basically, a SCADA system would gather data and according to the collected data, it would provide command signals. The SCADA simulator is used to simulate the process principle and also, we can determine the process features and thus we could determine the outcome of the process. So the simulation would be done according to the collected data and this data could be received from the communication devices and from the data historian.
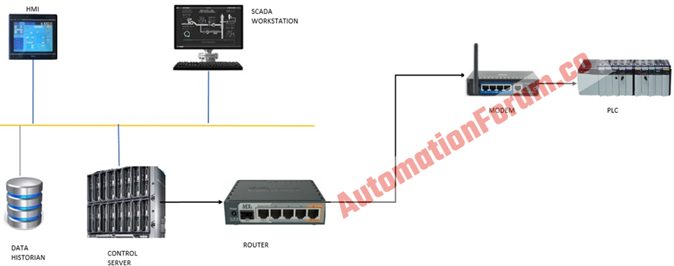
SCADA system architecture
What are the major functional units of SCADA?
- Data collection equipment
- Data transmission/telemetric equipment
- Remote terminal unit (RTU)
- Data loggers
- Data presentation equipment
What are the major functions of SCADA to control an industrial process?
- Data acquisition –Provides the process data
- Control – The operator can control the devices remotely
- Data processing – Quality and the integrity of the data will be checked
- Alarms – The operator will be alerted if there are any fault operating conditions
- Logging – All the operator entries will be logged
- Trending – This feature would give details about the measurements according to different time scales such as minute, hour.
- Historical reporting – in the historian the SCADA would save the historical data and this can be checked
How SCADA simulator does the process simulation?
With the help of a SCADA simulator, the operator would get hands-on experience dealing with the faults in an industrial process. So in order to do the simulation a certain environment similar to the plant process will be created. So with this simulator operator would get experience in artificial fault environments and this would give a better understanding of the plant process. So in order to make an environment similar to the process, the data which is used must be accurate. So in order to collect historical process data, the SCADA would provide a historical data reporting and we have discussed it earlier.
SCADA Simulator
1.SCADASim
SCADASim can create SCADA simulations it has a modular SCADA modeling tool and this would be useful for real-time communication to the external devices by using the communication protocols. We can simulate the SCADA system with a simulator and this would be useful for testing different attacks and also the security solutions. This simulator consists of certain modules which are capable to act as the SCADA components such as PLC, MTU, RTU, and also the protocols such as the MODBUS/TCP and DNP3. So because of this feature, we can integrate the external components into the simulation process.
SCADA simulation software download link
The major feature of this software is that it can integrate the hardware and also the prototype software modules. We can use this simulator to simulate the smart grid.
Communication protocols – MODBUS/TCP and DNP3
Major components of the simulation
Smart meter, Smart meter proxy, SSScheduler, MTU/HMI, HMI client proxy, and HMI client.
Operating system – MAC, Windows, and Linux
2. Wintr
This is an advanced SCADA simulator, which is developed by Fultek Industrial. By using this we can simulate the process and can determine if there is any fault or we can make required changes according to our needs. The major features of this simulator are that it has a redundant working style and this simulator consists of a lot of separators and has 46 different types of SQL queries as a reporting tool. This simulator has a lot of industrial symbols and has unlimited tables and each table would support 950 tags.
This simulator also has a print documentation function and also has a PLC communication error function. It can be connected to automation devices through S7 MPI, PPI, Profinet, and MODBUS RTU. In case of any emergency then it would send an email notification.
Operating system – Windows
Communication protocol – MODBUS TCP/IP, MODBUS RTU, OPC client, Fins Ethernet,
SCADA simulation software (Wintr) – Download link
What are the major requirements of a SCADA system simulator?
- Plug and play feature for creating simulation
The operators are using this simulator tool and they won’t have programming skills, so the simulator tool must be really simple without needing any programming skills for its operation.
- Connectivity to multiple hardware and software
There could be a lot of devices in a SCADA system to monitor the process, so the simulator must support multiple connections to the devices.
- Support different industrial standard protocol
A SCADA simulator should be flexible enough to support many protocols and also from different vendors. MODBUS/TCP and DNP3 etc are the standard industrial protocols.
Why do we need SCADA and how can it provide security for the industrial processes?
A SCADA system would monitor the process continuously and also it would give commands to do the required corrective actions.
System monitoring
We could get up to date information regarding the process condition
Contingency analysis
In case of any faulty condition in a process the operator should react very fast otherwise it would create a lot of problems. The contingency analysis of the SCADA system provides the action that must be done by the operator to prevent the faults before they could happen.
Corrective action analysis
This feature will be helpful for the operator in order to take the required actions, in case of any contingency, and thus there won’t be any interruption in the process.
What are the advantages of the SCADA simulator?
- The plant process can be visualized
- Graphical representation of the plant process
- We could determine the process results and can make changes according to our need
- We can determine the faults in a process before they could happen
- Less maintenance
- Process equipment can be protected