What is a stepper motor?
A stepper motor is also called a step motor because it is a pulse-driven motor that would change the angular position of the motor in steps. The stepper motor would rotate at a specific angle of degree according to the electric pulse. Basically, it is a brushless synchronous electric motor and its full rotation is divided into a large number of steps. We can use a stepper motor if controlled movement is required. Stepper motors don’t have any brushes or contacts and they would convert the electrical pulse to mechanical motion. It can also rotate in the reverse direction positive pulses would rotate this in one direction and the negative pulses would allow it to rotate in the opposite direction.
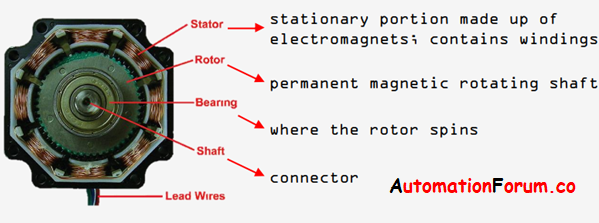
When should we use a stepper motor?
• It can be used if we need controlled movement
• Controlled rotation angle
• Controlled speed
• Controlled position and synchronism
How does a stepper motor work?
The stepper motor has a permanent magnet rotating shaft which is called a rotor and it also has electromagnets, this would be stationary. The electromagnet surrounds the motor and it is called a stator. The rotation speed of the motor would be depended upon the rate at which the electrical signals are applied and the rotational direction would be according to the pattern of the pulse which is applied to it.
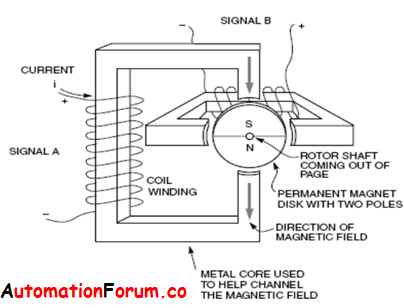
The above image shows the operation of the stepper motor, current would flow through the coil and thus creates a magnetic field. This magnetic field will be made perpendicular to the core by a metallic core. Based on the polarity there could be attraction or repulsion and it would drive the rotor. Current would be applied to the motor this current pulse would rotate the motor shaft. So if we control the pulse we can control the rotational speed. In this motor, if we energize the coil properly then we can rotate the motor according to the requirement.
What are the advantages of a stepper motor?
• It is compatible with digital systems
• There is no need for sensors to do the positioning and speed sensing
• It can be easily interfaced with other digital components
• We can achieve proper position and speed by this motor in an open-loop system
• There won’t be any problems related to instability and also no need for feedback transducers
• The design is simple for a stepper motor control system
• The stepper motor is capable to drive a wide range of frictional and inferential loads
• It doesn’t need any feedback
• It would act as a position transducer
• Less expensive
• Easy to use
• Stepper motor would stop in case of any malfunction or interference
• Low-speed torque is really good
• Repeatability
• These motors won’t be damaged by any mechanical overload
• Long-lasting
What are the disadvantages of stepper motor?
• It has low efficiency because it draws lot of power, this power is drawn regardless of the load
• If the speed increases, then the torque would decrease
• It would get heat up during its high performance
• Output power is really low compared to the size of the motor
• Accuracy would be low during the full load
What are the applications of stepper motor?
• Medical equipment
• Automotive devices
• Recording heads in computer disk drives
• Positioning of print heads
• Satellites
• CNC machines
• Robotic and control applications
• Used in military applications
• X-ray machines
• Ultrasound scanner
• Nuclear reactor
What is a servo motor?
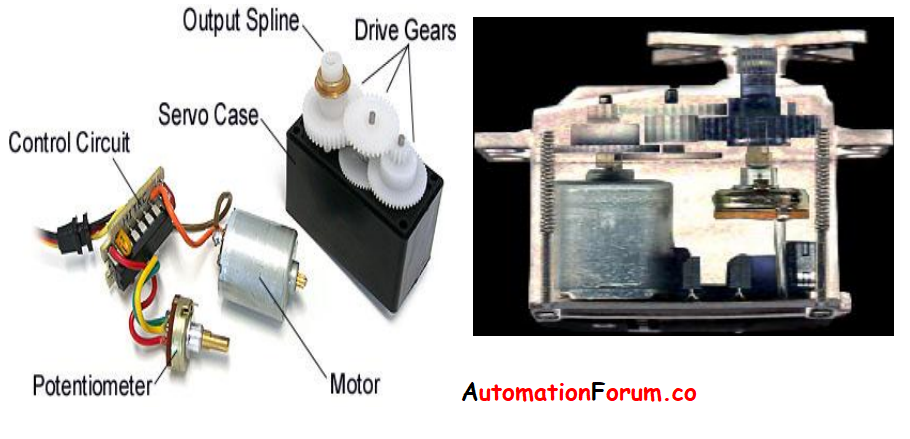
A servo is a small device that has an output shaft. This shaft can be positioned at a specified angle by transmitting a coded signal. So based on the signal the servo would keep its position. If there is any change in the signal then the position of the shaft would change too.
We can describe the servo motors as modified DC motors. Servo motors are constructed by adding some gear reduction, a position sensor, an electric circuit to control the operation of the motor, and a potentiometer to a DC motor.
Servo motors are not used as an industrial motor to do the energy conversion, it is mostly used to do the accurate control of the position. These motors are used when precise speed and position should be attained at high torque. These motors are capable to operate at low speeds and they can be used to control the machines. These motors are mostly used in motion control applications.
How does a servo motor work?
Mostly these motors operate according to the feedback in case of any error. It would receive feedback and it would operate to a certain limit based on this command. The operating principle of the servo motor is the pulse width modulation, due to this the pulses would control their angle of rotation.
As we discussed earlier there is a circuit, potentiometer, and another component in this motor. So these components would be really useful to rotate the servo motor according to our requirements. The servo controller would transmit a voltage signal for positioning, torque, or speed. The potentiometer is capable to sense the mechanical position of the shaft and it couples with the shaft through gears. The potentiometer would convert the shaft position to an electrical signal and this signal would be compared with the input signal. So command input would be given according to the shaft position. If the input is different from the feedback signal then an error signal would be generated. So based on the error signal input signal would be applied to the motor.
Difference between a stepper motor and a servo motor?
Characteristics | Stepper motor | Servo motor |
Pricing | Stepper motor is a lot cheaper than the servo motor | Servo motor is costlier |
Torque and speed | These motors are not suitable for high torque applications | It can operate at high speed and in high torque |
Repeatability | Compared to servo motors it is not that good for repeatable short movement | Servo motors can provide good repeatable movements |
Positioning | It can do positioning at low torque applications | Good positioning features |
Controlling | Open loop applications | Closed loop applications |
Closed loop applications | Good reliability because of less control parts | Less reliable due to the Control parts |
Size | It is only available in few different sizes | It is available in different size and it can handle huge machines |
Starting procedure | Its operation is simple as plug and play | Tuning is required to do the operation properly |
Low speed | Stepper motors are really good at low speed applications | Not as good as stepper motors |
Overload handling | It can handle overload better than servo motors | It won’t work properly in case of any mechanical overload |
Efficiency | Low efficiency | Good efficiency |
Noise | It would create more noise than the servo motor | Creates very less noise |
Heating | It would easily heat up due to large amount of current | Less heating issues |
Simplicity | Very simple construction | Due to the control system and components its really complex |
What are the advantages of servo motor?
• It would provide high output power
• The accuracy and resolution of the servo motor are determined by the encoder
• It would provide high efficiency
• Good torque to inertia ratio, it can accelerate the loads quickly
• These motors have two to three times continuous power for short periods
• It has 5 to 10 times rated torque for short periods
• These motors would stay cool because the current which is drawn would be proportional to the load
• These motors can maintain usable high-speed torque
• These motors would operate quietly
• It would provide a resonance-free and vibration-free operation
What are the applications of servo motors?
• It is used in computers and also for machine control
• Radar
• Robotics
• Aircraft control system
• Electromechanical actuators
• Remote positioning devices