This type of valve would allow the flow in one direction and it would restrict the flow in the opposite direction. These valves are normally closed valves, in order to do a reverse flow a check valve is used. These valves are mostly placed between a cylinder and the directional control valve. The counterbalance valve would act as a hydraulic resistance to the actuating cylinder. It is used in a hydraulic operated forklift, the valve would provide resistance to the flow from the actuating cylinder when the fork is lowered. It also supports the fork in the up position.
- What is an anti-surge valve and what are their functions?
- What is a sequence valve?
- What is a cartridge valve?
- What is a proportional control valve?
- What are the problems in a control valve and how to do the troubleshooting and maintenance of a control valve?
What are the uses of a counterbalance valve?
These valves are also used to prevent a load from accelerating uncontrollably. Mostly counter valves are used to prevent the weight from falling uncontrollably, these valves are used to maintain backpressure so that it can prevent a load from falling. A counterbalance valve would allow the downward movement of the load supported by a cylinder only when the system pump is operating. The force generated by the system pressure and the force created by the weight of the load is needed to move the load downward.
The counterbalance valve is normally a closed pressure valve and they are used with cylinders to a counterweight or a potentially overrunning load. In certain processes, there could be uncontrolled operation and this can be prevented by using a counterbalance valve. So basically a counterbalance valve is a hydraulic system pressure control valve that is used as a safety device to prevent the movement of a loaded actuator without the application of the additional pressure generated by the system power unit.
What are the major functions of a counterbalance valve?
- It would allow free upstream flow through the check valve for the load lifting
- It would lock the reverse downstream flow when the directional valve is not operated, or the pump is stopped
- It can reduce the pressure surges in the actuator
How does a counterbalance valve operates?
In certain actuators, it would have a run-away load and this load could fall if the directional control valve that controls the actuator shifts in order to lower the load. The counterbalance valve can prevent the free fall of the load. The working principle of a counterbalance is that the fluid will be trapped under pressure till the pilot pressure overcomes the preset value of the spring force. After that, the fluid will escape, thus letting the load move downwards under control. The counterbalance valve would stay close till a remote pilot pressure source acts on it. So only the lower spring source is required and this would lead the valve to be operated at lower pilot pressure and thus less power consumption. The pump life would be increased and the fluid temperature would decrease.
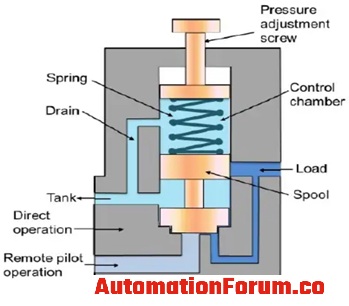
What is the need for a remote counterbalance valve?
The major disadvantage of a counterbalance valve is that it would reduce the available force. An example of this would be a press circuit in which this valve is used to counteract the weight. So the pressing force will be affected by the backpressure of the valve.
This disadvantage of the counterbalance valve can be removed by using a remote pilot operation. The remotely piloted counterbalance valve is also called a brake valve or over-center valve. There will be low pressure in the pilot section and this would open the valve and thus removing the back pressure from the cylinder. So when the piston tries to move away the pilot pressure is gone and the counterbalance section will switch back into the circuit. So during the beginning of the operation, the valve will be piloted open and thus the back pressure will be removed.
How to set and troubleshoot a counterbalance valve?
The counterbalance valve must always be pressure set before it is installed in a system after the installation it will be very difficult to set the pressure. In order to properly set a counterbalance valve, adjust its spring to the highest setting and then raise the load.
Contamination could cause the internal check valve or spool to stick open. The most common cause of the valve failure is because of seal failure of the cartridge
- Before removing the valve we must make sure that the machines and the loads are at rest and we must also make sure that the valve is not under pressure while it is being removed.
- Remove the cartridge from its cavity
- Check if there are any contaminants in the cartridge and remove the contaminants if found
- Replace any seal if it is damaged
- Immerse the cartridge in clean hydraulic fluid and reinstall it
- If this does not clear the operating problem then replace the cartridge with a new one
What are the applications of counterbalance valves?
- It is used in vertical presses
- Lift trucks
- Loaders
- It is also used in certain machine tools which need to position or hold the suspended loads.
- These valves are used in a hydraulic operated forklift
- It is used to retard the spinning motion of a weight that is attached to the motor’s shaft.
- It is used in cylinders to lock the fluid to prevent drifting