- What is Compressor Surge?
- How Does Surge in a Compressor Occur?
- Operation of Anti-Surge Control System
- Key Components in Anti-Surge Control System
- Anti-Surge Control System Working
- Why Anti-Surge Control is Important?
- Causes of Anti-Surge Control Operation
- Interlock Situations for Anti-Surge Control Operation
- What are the requirements of anti-surge valve?
- How to select anti surge control valve?
- What are the characteristics of a surge?
- What are the consequences of surge?
- Why does the compressor have surge?
- What is the difference between an anti-surge control valve and general control valve?
- How to install anti-surge valve?
- How does an anti surge valve work
The anti-surge valve is a surge relief valve which is a kind of valve that can be used to do the surge control. Anti-surge valve can be considered as a dedicated control system which is capable to act as a surge controlled with great response time. The major function of the anti-surge valve is to open very fast when required and this requirement would be to control the surge, so the valve would open very fast and it will recirculate the gas from discharge to the suction and by that there will be only less flow through the compressor when it is running. The anti surge valve will be capable to remove the surge from the compressor, the surge could occur in the compressor very fast so the anti-surge valve must operate very quickly to handle this. So when the anti surge valve acts against the surge it not only has to remove the surge, it also should reverse the process.
What is Compressor Surge?
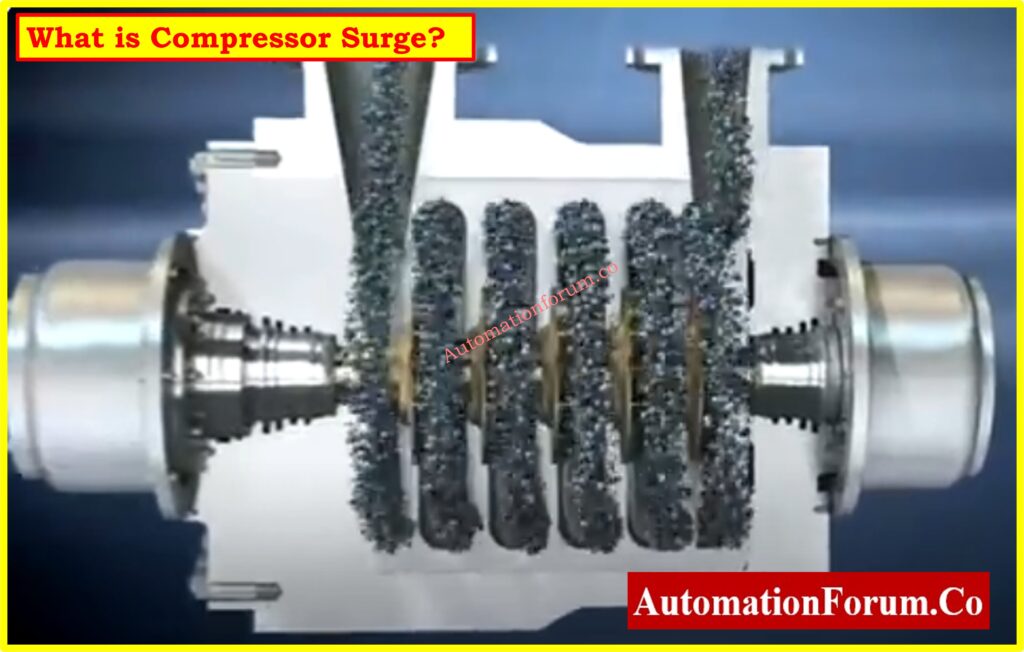
Compressor surge is a condition where the flow of air or gas through a compressor intermittently reverses, leading to instability in the compressor’s operation. In simple terms, it’s like the compressor “choking” or struggling when the flow is too low or too high compared to its design limits.
How Does Surge in a Compressor Occur?
Surge occurs when the compressor is operating outside its designed flow range. This typically happens in the following scenarios:
- If the flow of air or gas through the compressor decreases significantly, the compressor may reach a point where it cannot maintain stable operation. When the flow is reduced below a critical level, the pressure inside the compressor can rise, leading to a situation where the gas may start to flow backward. This condition is referred to as surge.
- If the pressure in the system (like a receiver tank) exceeds the pressure the compressor can maintain, the compressor might experience backflow, leading to surge.
- Other factors, such as sudden changes in load, throttling of the discharge, or malfunctioning components, can also cause surge.
When surge occurs, it can cause significant damage to the compressor and affect the overall performance of the system. Therefore, it’s important to ensure that compressors are operated within their designed flow and pressure ranges to avoid this issue.
Operation of Anti-Surge Control System
This below diagram illustrates the control system for a gas compressor, specifically focusing on anti-surge protection for a centrifugal or axial compressor. Let me explain the key elements and their functionality based on the schematic:
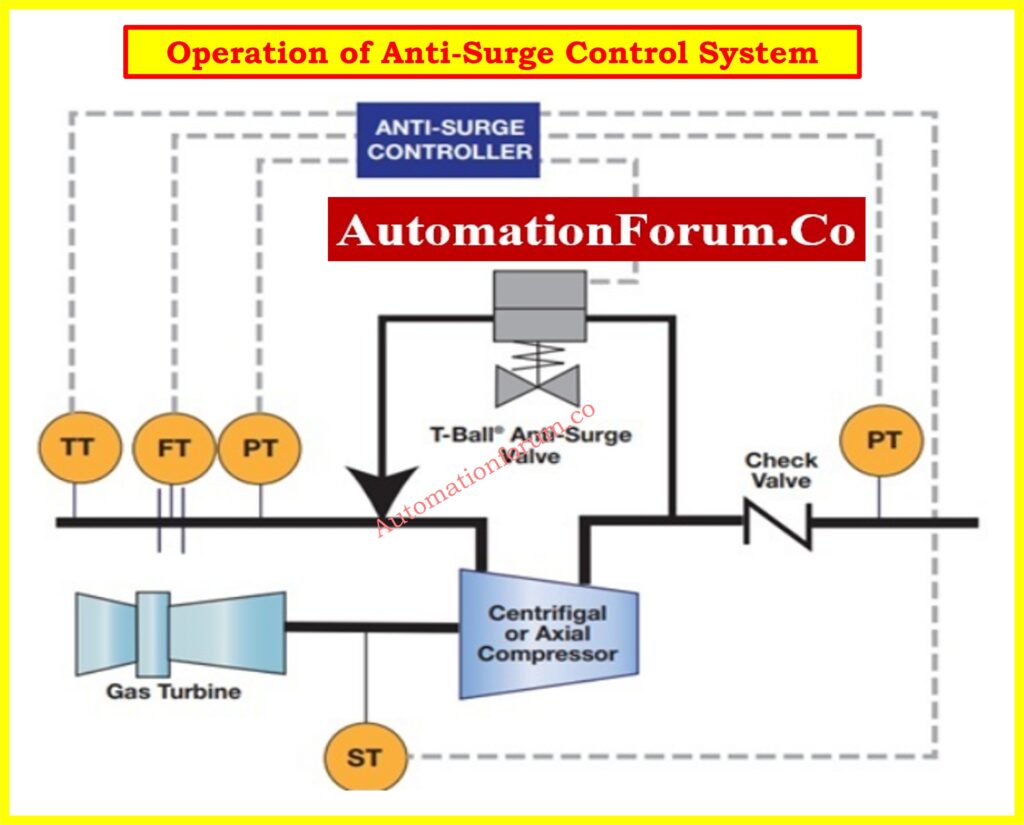
Key Components in Anti-Surge Control System
Gas Turbine:
The prime mover that drives the compressor, delivering mechanical energy to compress the gas.
Centrifugal or Axial Compressor:
Compresses the gas to the desired pressure. However, during low-flow conditions, it is prone to surge, which can damage the compressor.
Anti-Surge Controller:
The brain of the system that monitors key parameters (flow, pressure, and temperature) to detect surge conditions and control the anti-surge valve.
T-Ball Anti-Surge Valve:
A fast-acting valve designed to recycle gas from the discharge side back to the suction side when surge conditions are detected. This protects the compressor by stabilizing its operation.
Check Valve:
Located on the discharge line to prevent backflow into the compressor, ensuring unidirectional flow.
Sensors / Transmitters :
TT (Temperature Transmitter): Monitors gas temperature.
FT (Flow Transmitter): Measures gas flow rate.
PT (Pressure Transmitter): Monitors the suction and discharge pressure.
ST (Speed Transmitter): Tracks the speed of the gas turbine.
Signal Lines (Dashed Lines):
Connect the sensors, anti-surge controller, and anti-surge valve for real-time monitoring and control.
Anti-Surge Control System Working
Normal Operation:
Under normal operating conditions, the compressor takes in gas, compresses it, and sends it through the discharge line.
The flow rate, pressure, and temperature are monitored continuously by the respective transmitters.
The anti-surge valve remains closed during normal operation to allow maximum efficiency.
Surge Detection:
The anti-surge controller uses input data from the flow, pressure, and temperature transmitters to calculate the compressor’s operating point on the surge control map.
Surge occurs when the flow rate drops below a critical threshold, leading to reverse flow and pressure fluctuations inside the compressor.
Anti-Surge Action:
If the operating point approaches the surge line (low flow and high pressure), the anti-surge controller sends a signal to the anti-surge valve.
The anti-surge valve quickly opens, allowing a portion of the compressed gas from the discharge side to recirculate back to the suction side.
Recirculation Process:
The recycled gas increases the flow through the compressor, moving its operating point away from the surge region.
Check Valve Role:
The check valve prevents backflow from the discharge side to the compressor during transient conditions or anti-surge operations.
System Stabilization:
Once the compressor stabilizes and the risk of surge is eliminated, the anti-surge valve closes gradually.
The system returns to normal operation, maintaining optimal flow and pressure.
Why Anti-Surge Control is Important?
- Surge can cause mechanical damage to the compressor blades and bearings due to vibrations and excessive pressure fluctuations.
- It reduces compressor efficiency and reliability.
- The anti-surge system ensures smooth and safe operation by dynamically adjusting to prevent surge conditions.
Causes of Anti-Surge Control Operation
The anti-surge control system is designed to protect the compressor from a surge event. A surge can occur due to the following causes:
Low Flow to the Compressor:
Cause: A drop in gas flow rate due to:
Blockages in the suction line.
Reduced demand downstream of the compressor.
Process upsets or system fluctuations.
Effect: Low flow causes a higher pressure ratio, bringing the compressor close to its surge line.
Rapid Changes in Operating Conditions:
Cause: Sudden changes in system demand, such as:
Quick valve closures downstream.
Emergency shutdowns or trips.
Load rejection by downstream equipment.
Effect: Flow to the compressor drops quickly, increasing the risk of surge.
Start-Up and Shutdown Conditions:
Cause: During start-up or shutdown, the flow may temporarily drop below the surge threshold.
Effect: Surge conditions can occur when the compressor is not operating at design conditions.
Fouling or Mechanical Issues:
Cause: Fouling, deposits, or mechanical damage in the compressor can reduce its performance and alter its surge characteristics.
Effect: The compressor may enter surge conditions more easily than expected.
Malfunction of the Compressor System:
Cause: Failures such as:
Sensor malfunctions (e.g., faulty flow, pressure, or temperature transmitters).
Control system errors or slow response of the anti-surge valve.
Blocked or stuck anti-surge valve.
Effect: Delayed or inaccurate control can lead to surge.
Backflow from Downstream:
Cause: A failure in the check valve could allow backflow into the compressor.
Effect: The reverse flow creates instability, leading to surge.
Power Loss or Speed Drops:
Cause: A sudden loss of power to the compressor driver (e.g., gas turbine or electric motor) or a drop in rotational speed.
Effect: Reduced speed decreases the flow rate, causing a higher likelihood of surge.
Interlock Situations for Anti-Surge Control Operation
Interlocks are safety mechanisms to ensure that the anti-surge control system activates when necessary. Typical interlock scenarios include:
1. Low Flow Interlock:
Trigger: The flow transmitter (FT) detects a flow rate below the safe operating limit.
Action: The anti-surge valve opens to increase flow and protect the compressor.
2. High Discharge Pressure Interlock:
Trigger: The pressure transmitter (PT) on the discharge line detects abnormally high pressure, which is a sign of a restriction or blocked downstream flow.
Action: The anti-surge valve opens to relieve pressure and maintain compressor stability.
3. Emergency Shutdown (ESD):
Trigger: In the event of an emergency shutdown, system demand drops rapidly, causing flow through the compressor to fall below the surge threshold.
Action: The anti-surge valve fully opens to prevent surge during the shutdown process.
4. Compressor Start-Up/Shutdown Interlock:
Trigger: During start-up or shutdown, the compressor passes through conditions that may approach the surge region.
Action: The anti-surge valve operates dynamically to maintain adequate flow through the compressor during these transient phases.
5. Speed Drop Interlock:
Trigger: The speed transmitter (ST) detects a drop in compressor speed below a critical level.
Action: The anti-surge valve opens to maintain flow and prevent surge as speed reduces.
6. Process Upset Interlock:
Trigger: Rapid pressure fluctuations or disturbances in the process (e.g., valve slamming downstream) detected by pressure or flow transmitters.
Action: The anti-surge valve opens momentarily to stabilize the compressor.
7. Anti-Surge Valve Malfunction Interlock:
Trigger: The system detects a fault in the anti-surge valve, such as:
Stuck valve position.
Actuator failure.
Slow response time.
Action: Alerts operators and, if necessary, triggers emergency bypass systems or shutdown.
What are the requirements of anti-surge valve?
- The anti-surge valve must have good stroke speed
- The valve should be of a proper size so that it can control the surge and if it is oversized then it can’t do proper control
- The close to open time and the open to close time of the anti-surge valve must be very quick
- The proper air supply is needed to operate the anti-surge valve
- In order to decrease the lag time the turbine run should be reduced
- The fail position must be open
- More than one volume boosters must be needed for the quick response
- The anti-surge valve must be capable to handle high-pressure drop and also it must reduce noise and vibration
- It must provide tight shut-off so that it can avoid energy loss in the system
- The construction must be robust so that it can handle extreme service conditions
- It should have a stable response
- It must reduce overshooting at the time of valve adjustment steps
How to select anti surge control valve?
- The characteristics of the valve must be considered mostly linear type valves are used, but in certain cases, an equal percentage valve can be used
- Speed is an important factor of an anti-surge it should have a quick response time
- We must consider the capacity while selecting an anti-surge valve, the selected valve must be capable to allow or pass the highest output of the compressor
- Noise – In the case of the surge event there could be a high-pressure drop and flow rate and this could cause a high level of noise so according to this, we must select the valve.
What are the characteristics of a surge?
- It could cause the compressor to trip
- Noise will be created
- The temperature of the flowing liquid will be increased
- The compressor vibration will be high
- The flow reversal would be quick
What are the consequences of surge?
- Frequent surging can cause significant wear and tear on the compressor’s components, such as bearings and seals. This leads to increased maintenance needs and potentially costly repairs.
- Surge decreases the overall efficiency of the compressor and the entire system. The compressor may struggle to maintain the desired output, affecting operational performance.
- Continuous surge conditions can cause physical damage to the compressor, including blade erosion and structural damage. This can ultimately shorten the lifespan of the compressor.
- Surge can lead to operational issues like unstable flow, which can affect the downstream processes and result in poor system performance.
Why does the compressor have surge?
- Surge occurs when there is a mismatch between the compressor’s capacity and the system’s demand. If the demand decreases or fluctuates rapidly, the compressor may struggle to adjust quickly enough.
- Rapid changes in system pressure can lead to surge. For instance, if there is a sudden drop in system pressure, the compressor may not be able to adjust its output quickly enough to compensate.
- Inadequate or improperly tuned control settings can cause the compressor to operate outside its optimal range, leading to surge conditions.
- Mechanical issues, such as blockages in the intake or discharge lines, can disrupt the normal flow of air or gas, causing the compressor to surge.
What is the difference between an anti-surge control valve and general control valve?
- The primary difference is the response time. Anti-surge valves are designed for rapid opening and closing to handle the sudden changes in flow and pressure associated with surge conditions, whereas general control valves may not have the same quick response capability.
- Anti-surge valves are specifically designed to prevent or mitigate surge conditions by controlling the flow of gas or air back to the suction side, while general control valves regulate flow and pressure in a more conventional manner.
- Anti-surge valves often have features like a fail-open design, high-speed actuators, and enhanced durability to withstand harsh conditions, which may not be necessary in general control valves.
How to install anti-surge valve?
- The anti-surge valve should be kept at a minimum distance from the discharge line
- The straight pipe lengths upstream and down streams of the anti-surge valve must be provided as required so that we can reduce the noise and pipe vibrations
- These valves must be located in the higher part of the piping and because of this the upstream and downstream can easily drain into the suction.
- Ensure that the valve is properly aligned with the piping to avoid additional stress on the valve and to ensure smooth operation.
How does an anti surge valve work
- The anti-surge valve is typically a fail-open valve, meaning it remains open in the absence of a controlling signal. This design allows the valve to open and relieve surge conditions when necessary.
- The valve operates based on signals from the control system. A high signal (e.g., 20mA) will keep the valve closed, while a low signal (e.g., 4mA) will cause the valve to open. This allows the valve to quickly respond to surge conditions by diverting gas from the discharge back to the suction side.
- The valve should be sized appropriately to handle at least twice the maximum surge flow rate. An oversized valve may not operate effectively, while an undersized valve may not provide adequate surge control. The valve must be sized almost 2 times the maximum surge point flow rate and an oversized valve won’t operate properly.
- During compressor startup, the valve should initially be open to allow for proper operational adjustment. As the compressor reaches stable operation, the valve characteristics are adjusted to ensure it operates within the required range for effective surge control.
Explore essential aspects of air compressors, including seal systems, filters, preventive maintenance, and dryer types by referring the below links