- Securing a position as an Instrumentation Maintenance position in a refinery requires a thorough understanding of both theoretical concepts and practical applications.
- Refinery operations depend heavily on precise instrumentation and control systems to ensure safety, efficiency, and reliability.
- To help you prepare for your interview, we have compiled a list of 30 unique questions along with detailed answers.
- This guide aims to cover a broad range of topics, from basic principles to advanced problem-solving scenarios, providing you with a comprehensive resource for your preparation.
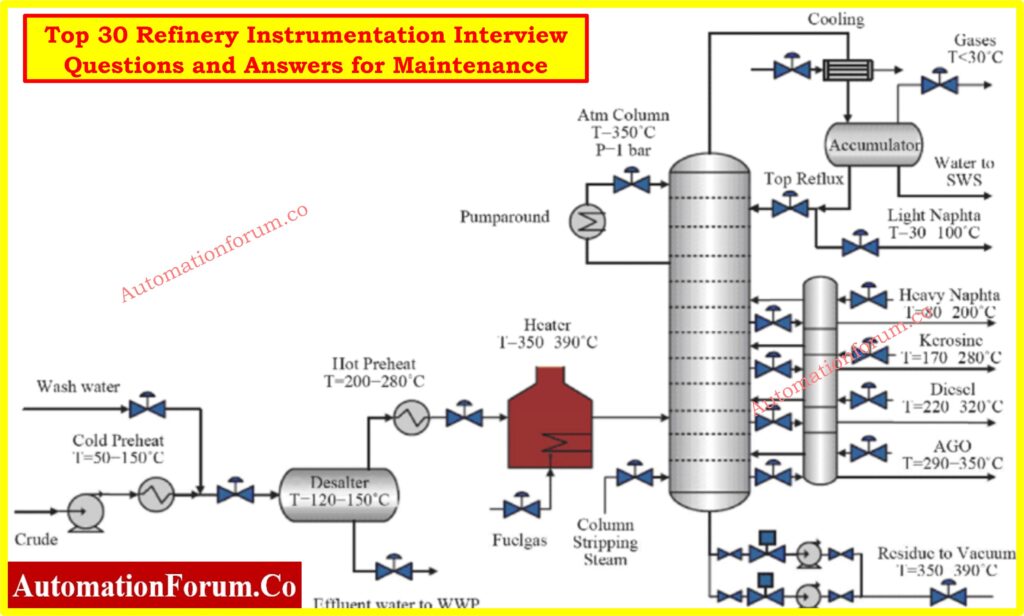
What are the different types of control strategies used in refinery process control?
Various control strategies used in refinery process control include:
- PID Control: Uses proportional, integral, and derivative actions to maintain process variables at desired setpoints. Commonly used for simple control loops.
- Feedforward Control: Anticipates process disturbances and adjusts control actions before they affect the process. Used for processes with measurable disturbances.
- Cascade Control: Employs a secondary control loop to enhance the performance of the primary loop. Useful in temperature and level control.
- Ratio Control: Maintains a specific ratio between two process variables. Used in blending and mixing applications.
- Model Predictive Control (MPC): Uses dynamic models of the process to predict future behavior and optimize control actions. Applied in multivariable and complex process control scenarios.
How do you implement and tune a PID controller in a complex refinery process?
Implementing and tuning a PID controller involves:
- Identifying Process Dynamics: Analyze the process response to changes in input.
- Selecting Tuning Methods: Choose methods like Ziegler-Nichols, Cohen-Coon, or software tools for initial parameter settings.
Click here for Excel based PID Loop Simulator
- Fine-Tuning: Adjust PID parameters (proportional, integral, derivative) through trial and error or using software tools to achieve a balance between responsiveness and stability.
Click here for PID controller tuning
Describe the principle and applications of different types of flow meters used in refineries.
Common flow meters include:
- Differential Pressure (Orifice, Venturi, Annubar): Measure flow based on pressure drop. Used for gas and liquid flow measurement.
- Positive Displacement type: Measure flow by capturing fluid in compartments. Suitable for high-viscosity fluids.
- Turbine type: Measure flow by the rotational speed of a turbine. Used for clean liquids and gases.
- Ultrasonic type: Use sound waves to measure flow. Suitable for large pipes and clean fluids.
- Coriolis type: Measure mass flow based on the Coriolis effect. Ideal for liquid hydrocarbons due to high accuracy and reliability.
How does a Distributed Control System (DCS) differ from a Programmable Logic Controller (PLC) in a refinery setting?
- DCS: Used for large-scale, continuous processes. Offers extensive data handling and integration capabilities, better for plant-wide control and advanced strategies.
- PLC: Suited for discrete control and smaller applications. Less scalable than DCS but excellent for high-speed, repetitive tasks.
Click here for PLC Learning
What are the advantages of using a Foundation Fieldbus over a traditional 4-20 mA analog signal?
Advantages of Foundation Fieldbus include:
- Greater Data Transmission: Digital communication allows for more information exchange.
- Device Interoperability: Supports multiple devices on a single pair of wires.
- Diagnostics: Provides detailed device diagnostics.
- Reduced Wiring Costs: Fewer cables are needed.
Explain the role of advanced analyzers like Gas Chromatographs (GC) in process control and optimization in refineries.
Gas Chromatographs (GC) analyze the composition of process streams, providing real-time data for:
- Process Optimization: Adjusting processes for efficiency.
- Quality Control: Ensuring product specifications.
- Process Safety: Monitoring hazardous substances.
What is the function of an Emergency Shutdown System (ESD) and how is it integrated with other control systems?
- Function: Safely shut down processes during hazardous conditions.
- Integration: Connected with DCS and SIS, receives inputs from sensors, and executes safety actions. Regular testing and maintenance ensure reliability.
How do you ensure accurate temperature measurements in high-temperature refinery processes?
- Sensor Selection: Use appropriate sensors like thermocouples or RTDs.
- Installation: Proper sensor placement and protection (e.g., thermowells).
- Calibration: Regular calibration, signal conditioning, and compensation for accurate readings.
Describe the principle and calibration procedure of a Coriolis mass flow meter.
- Principle: Measures mass flow by detecting the Coriolis force in a vibrating tube.
- Calibration: Compare output with known standard, adjust settings, and verify accuracy across the flow range.
Click here for Mass Flow Controller Calibration Procedure
What challenges do you face in integrating wireless instrumentation in a refinery, and how do you address them?
Challenges and solutions include:
- Signal Interference: Use robust protocols (e.g., ISA100, WirelessHART).
- Power Supply: Ensure reliable power sources.
- Security Concerns: Secure data transmission.
- Network Reliability: Proper network planning and redundancy.
What is a Safety Integrity Level (SIL) and how is it determined?
- SIL: Measure of safety system performance, indicated by the probability of failure on demand (PFD).
- Determination: Through risk assessment considering failure consequences, event frequency, and required risk reduction.
How do you implement redundancy in critical instrumentation systems?
Redundancy can be implemented by:
- Multiple Sensors: Dual or triple redundancy.
- Redundant Control Systems: DCS with hot standby.
- Redundant Power Supplies: Ensuring component failure does not compromise the system.
Explain the principle of operation of a radar level transmitter and its application in a refinery.
- Principle: Uses microwave radar signals to measure the distance to the surface of a liquid or solid.
- Application: Non-contact level measurement in storage tanks and process vessels, offering high accuracy and reliability.
What are the key considerations for selecting an appropriate valve actuator in a refinery application?
Considerations include:
- Type of Control: On/off or modulating.
- Power Source: Electric, pneumatic, hydraulic.
- Required Torque and Speed: Based on the application.
- Operating Environment: Conditions like temperature and pressure.
- Compatibility: With the control system.
Describe the principle and advantages of using a variable frequency drive (VFD) in process control.
- Principle: Controls motor speed by varying electrical supply frequency.
- Advantages: Energy savings, precise speed control, reduced mechanical stress, and improved process control.
How do you ensure accurate pH measurement in harsh process conditions?
- Sensor Selection: Use appropriate sensors (e.g., glass electrodes, solid-state sensors).
- Calibration and Maintenance: Regular calibration and maintenance.
- Material Compatibility: Sensors should be compatible with chemicals and temperature.
What is a HAZOP study and how is it conducted in the context of instrumentation engineering?
- HAZOP (Hazard and Operability Study): Identifies and evaluates potential hazards.
- Conducting: Multidisciplinary team reviews process diagrams, identifies deviations, and analyzes consequences and safeguards.
Explain the concept of signal conditioning and its importance in instrumentation.
- Signal Conditioning: Manipulates sensor output for processing by control systems (amplification, filtering, isolation, conversion).
- Importance: Ensures accurate, reliable, and noise-free signal transmission.
What are the benefits and challenges of using fiber optic sensors in refinery applications?
- Benefits: High sensitivity, immunity to electromagnetic interference, operability in harsh environments.
- Challenges: Requires specialized equipment and expertise, higher initial costs.
Describe the working principle of an electro-pneumatic positioner and its role in valve control.
- Principle: Converts electrical control signal into a pneumatic signal to control valve actuator position.
- Role: Ensures precise valve positioning by comparing control signal with actual position and adjusting accordingly.
How do you perform a Functional Safety Assessment (FSA) for instrumentation systems?
- FSA: Evaluates design, installation, and operation of safety systems.
- Process: Reviewing documentation, inspecting equipment, testing safety functions, and verifying compliance with standards (e.g., IEC 61511).
What are the key differences between thermocouples and RTDs, and when would you use each?
- Thermocouples: Measure temperature based on the thermoelectric effect. Suitable for high temperatures.
- RTDs (Resistance Temperature Detectors): Measure temperature through resistance change of metal. Offer higher accuracy and stability at lower temperatures.
Explain the concept of Advanced Process Control (APC) and its benefits in a refinery.
- APC: Uses sophisticated algorithms and models to optimize process performance.
- Benefits: Improved product quality, increased throughput, reduced energy consumption, enhanced process stability and safety.
Click here to know more about Advanced Process Control (APC)
How do you handle drift in instrumentation sensors, and what techniques can mitigate it?
- Managing Drift: Regular calibration, using high-quality sensors, automatic recalibration systems, and software corrections based on historical data.
Describe the principle of a vibrating fork level switch and its application in refineries.
- Principle: Uses resonance frequency of a vibrating fork to detect liquid or solid presence. Frequency change triggers a switch.
- Application: Point level detection in tanks and vessels.
What are the considerations for implementing a remote monitoring system in a refinery?
Considerations include:
- Reliable Communication Methods: Wireless, fiber optic.
- Data Security: Ensuring secure data transmission.
- Sensor Coverage: Adequate coverage for accurate monitoring.
- Integration: With existing control systems.
- Real-Time Processing: Ensuring timely data processing and alarm management.
Explain the importance of hysteresis in control valves and how it affects process control.
- Hysteresis: Difference in valve position when approaching a setpoint from different directions.
- Effect: Can cause control inaccuracy and instability. Minimize through proper valve selection, maintenance, and using high-quality positioners.
Click here for What are the main causes of control valve hunting?
How do you perform diagnostics and maintenance on a digital valve controller (DVC)?
- Diagnostics: Use diagnostic software to check performance, identify issues like stiction or wear.
- Maintenance: Regular calibration, cleaning, and replacing worn components.
What are the advantages of using smart instruments in refinery automation?
Advantages include:
- Enhanced Diagnostics: More detailed and accurate diagnostics.
- Remote Configuration and Monitoring: Easier maintenance and troubleshooting.
- Improved Accuracy and Reliability: Better measurement performance.
- Reduced Maintenance Costs: Due to advanced features.
- Integration: Better integration with control systems for advanced process control.
Explain the principle and application of a magnetic flow meter in a refinery.
- Principle: Measures flow rate based on Faraday’s law of electromagnetic induction. Conductive fluid generates voltage proportional to flow velocity in a magnetic field.
- Application: Measuring flow of conductive liquids like water, slurries, and chemicals
Click here for Electromagnetic Flowmeter Troubleshooting: Identifying and Resolving Issues
Click here for More Instrumentation interview Questions and Answers