- What is Advanced Process Control system?
- Advanced Process Control Benefits
- What are the components of advanced process control?
- Process Models
- Real-Time Data Acquisition
- Data Historian
- Control Algorithms
- Optimization and Control Engine
- Human-Machine Interface (HMI)
- Performance Monitoring and Reporting
- Integration and Communication Interfaces
- How does Advanced Process Control integrate with DCS?
What is Advanced Process Control system?
- Advanced process control (APC) is the name given to a group of techniques that are used to raise the effectiveness and performance of industrial processes.
- Real-time process variable optimization is the goal of APC, which will improve output, quality, security, and energy efficiency.
- The total amount of hardware and software required for the control loops can be managed by combining them to create a system.
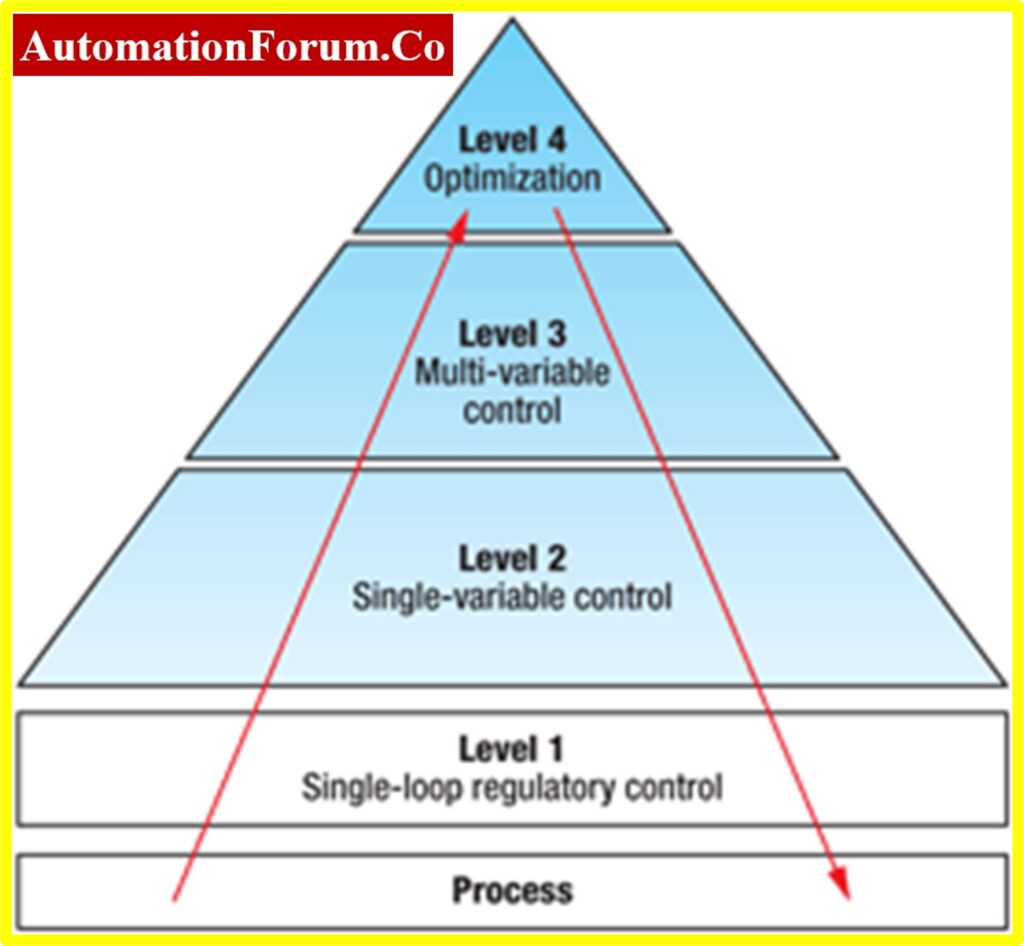
- In other words, sophisticated process control combines a variety of technologies and control methodologies.
- Advanced process control (APC) aims to improve the efficiency of control of production-related activities.
- Constantly controlling this procedure not only makes the production process simpler but also increases the reliability of the output results.
- By making changes to the production process, waste that results from repeated procedures can be eliminated.
- By eliminating this waste, the overall cost of the manufacturing process can be reduced even more.
- A programmable microcontroller, an advanced programme using ladder logic, multivariable control, multi-loop control, control optimization philosophies, programmed gain control, and advanced logic make up the advanced process control (APC) device.
Advanced Process Control Benefits
Implementing advanced process control (APC) offers several benefits to industrial processes:
- Improved Process Efficiency and Productivity
- Enhanced Product Quality and Consistency
- Increased Operational Stability and Reduced Process Upsets
- Optimal Resource Utilization and Cost Savings
- Enhanced Safety and Regulatory Compliance
- Extended Equipment Lifespan and Reduced Maintenance Costs
- Real-time Decision Support and Operational Effectiveness
- Process Flexibility and Adaptability to Changing Conditions
- Continuous Process Improvement and Performance Optimization
- Environmental Sustainability and Reduced Environmental Footprint
- Competitive Advantage in the Market
- Knowledge Capture and Retention for Training and Troubleshooting
- Scalability and Standardization across Processes and Plants
- Regulatory Reporting and Compliance Facilitation
- Enhanced Data Analysis and Process Insights.
What are the components of advanced process control?
- Advanced Control includes more than simply the usage of digital computers and the most recent software that runs on them. The adoption of sophisticated control algorithms is only one factor that contributes to the improvement of the fine regulation.
- Advanced control refers to the design of a system’s engineering infrastructure that combines components from other disciplines, including control engineering, signal processing, statistics, decision theories, engineering software, and even artificial intelligence strategies.
- Understanding the process, control issues, and the dynamics of the process, as well as connecting it to the most suitable method and technology for control, are key components of advanced control practice.
- A computer simulation model that incorporates process expertise and historical data, control and optimization algorithms, and current, real-time process information make up the Advance Process Control system.
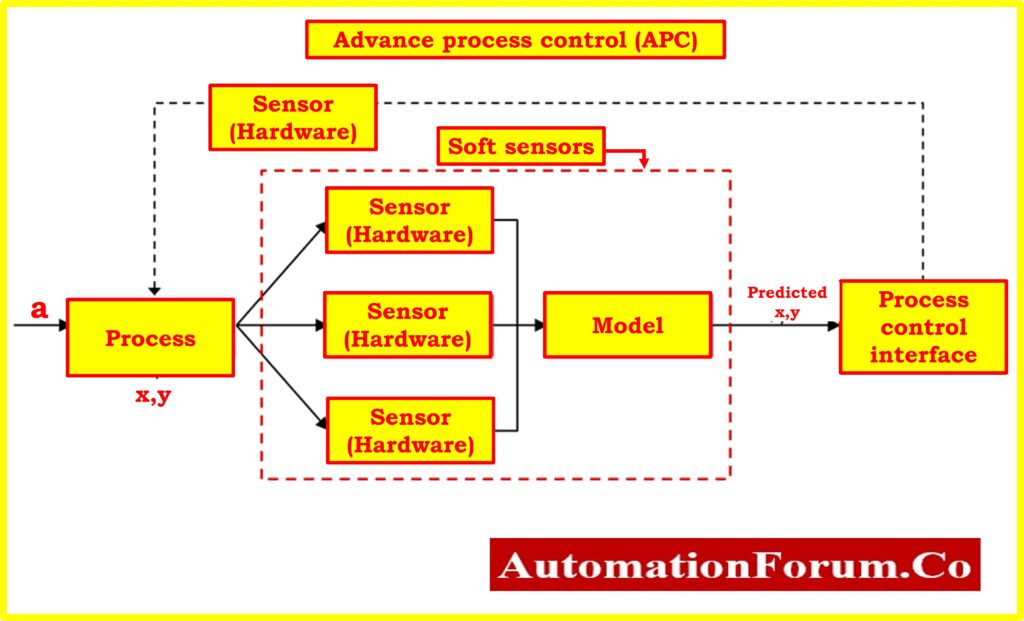
- APC enables multivariate control, adaptive tuning, predictive/process diagnostics, and relationships between manipulated and control variables.
- Multivariable control problems or discrete control problems are frequently solved with APC. APC is made up of many process control instruments, including:
- Model Predictive Control (MPC)
- Statistical Process Control (SPC) techniques
- Fault detection and classification
- Sensor control
- Feedback Systems
Here are the key components of APC:
Process Models
APC utilizes mathematical models that represent the behavior of the process. These models capture the relationships between process variables, dynamics, and constraints. They serve as the foundation for predicting process behavior, optimizing control actions, and enabling real-time decision-making.
Real-Time Data Acquisition
APC relies on sensors and instrumentation to collect real-time data from the process. These sensors measure various process variables such as temperature, pressure, flow rates, and composition. The accurate and timely acquisition of data is crucial for effective APC implementation.
Data Historian
A data historian is a software component that stores and manages historical process data. It provides a repository for storing large volumes of process data collected over time. The data historian allows for the retrieval, analysis, and visualization of historical data, which is essential for APC model development, performance monitoring, and troubleshooting.
Control Algorithms
APC employs advanced control algorithms to manipulate process variables and achieve optimal performance. These algorithms can include model predictive control (MPC), adaptive control, fuzzy logic control, or neural network-based control. Control algorithms use real-time data, process models, and optimization techniques to calculate control actions and adjust setpoints.
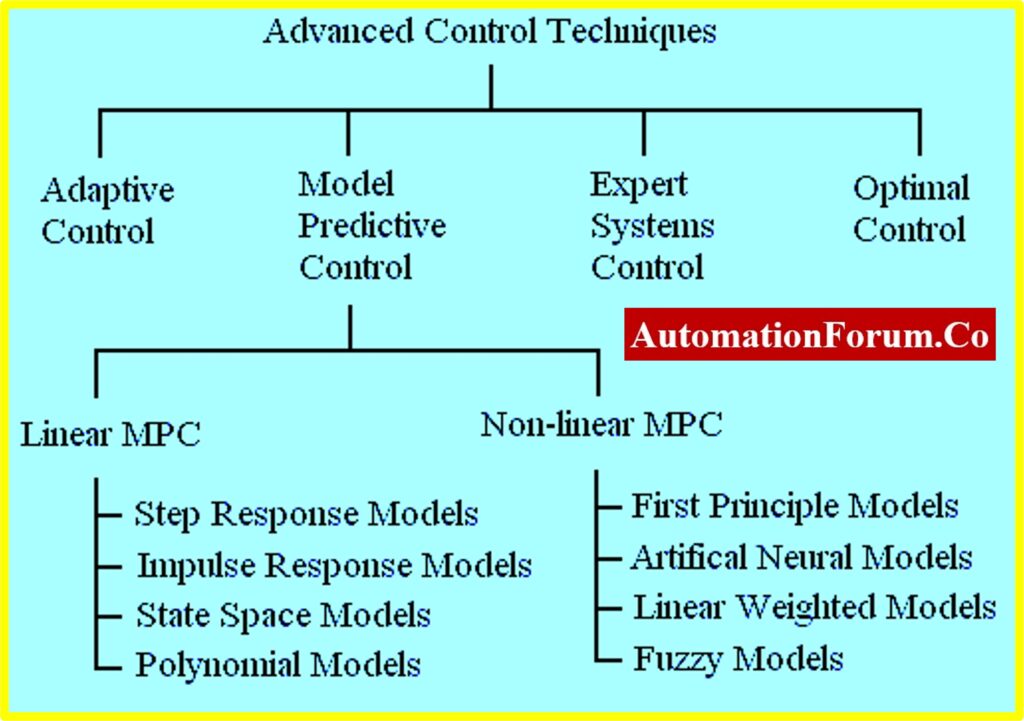
Optimization and Control Engine
The optimization and control engine is a core component of APC systems. It executes the control algorithms, performs real-time optimization calculations, and generates control strategies based on the process models, data, and objectives. The engine determines the optimal setpoints and control actions to achieve desired process outcomes.
Human-Machine Interface (HMI)
The HMI provides a graphical user interface for operators and engineers to interact with the APC system. It presents real-time process data, control strategies, alarms, and other relevant information. The HMI allows users to monitor process performance, override control actions if necessary, and make informed decisions based on the APC recommendations.
Performance Monitoring and Reporting
APC systems include tools for monitoring and evaluating the performance of the control strategies. Performance metrics and key performance indicators (KPIs) are calculated and displayed to assess the effectiveness of APC implementation. Performance reports and trends help identify areas for improvement and support continuous process optimization.
Integration and Communication Interfaces
Interfaces and protocols that enable the integration of APC systems with other control systems, plant-wide automation systems, or supervisory control and data acquisition (SCADA) systems. These interfaces allow for seamless communication and coordination between different control layers.
How does Advanced Process Control integrate with DCS?
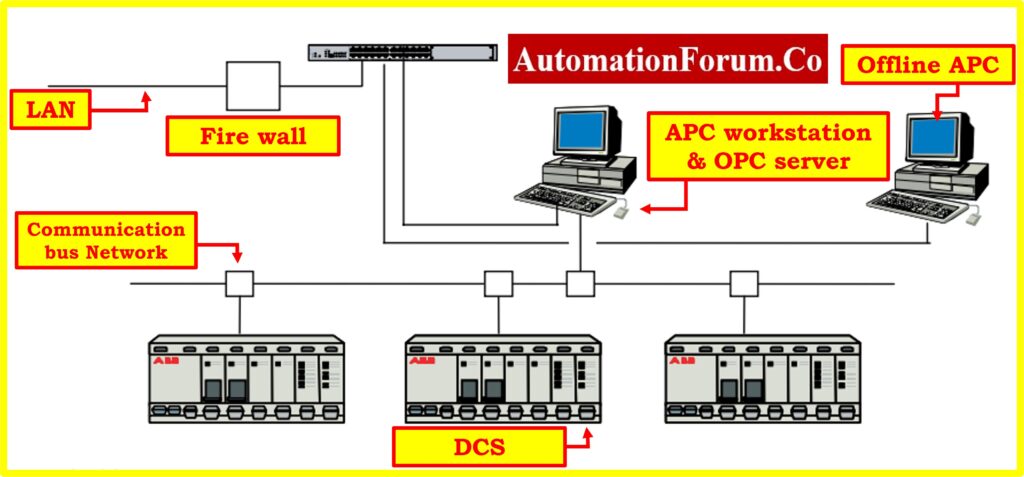
- The term “Advanced Process Control” (APC) refers to the application of a number of different methodologies and sets of equipment in order to enhance the control of a process or solve a particular issue that arises with a process.
- APC is multidisciplinary in nature. Through the use of engineering, signal processing, statistics, decision theory, and artificial intelligence (AI), it gathers knowledge.
- A DCS is typically coupled to an APC system. Moves are calculated and sent to regulatory controllers via the APC programme.
- An APC technology is typically connected to the distributed control system (DCS) that regulates the process in order to achieve the planned process control objectives. Advanced process control is utilized in a wide range of industries because of its innate propensity to handle issues that include several factors.
- A distributed control system (DCS) is typically used in process control to manage a production process.
- A distributed control system is one in which the system’s various parts, each with varying degrees of functionality, are dispersed throughout the entire process.
- Tools for advanced process control (APC) often connect to a distributed control system through the use of software interfaces or well-established communication protocols.
- To assist in isolating a problem or calculating the various variables that contributed to a problem, APC will track all information supplied to DCS regulatory controls during this communication exchange.
- The interfaces between DCS and APC systems in the past were special software interfaces.