- Method:1 Wiring Diagram for Pressure transmitter Calibration in Workbench using HART
- Components Involved in Wiring
- Method:2 Wiring Diagram for Pressure transmitter Calibration in Workbench Using HART
- Method:3 Wiring Diagram for Pressure transmitter Calibration in Workbench using HART
- Importance of the 250-Ohm Resistor In HART Communication
- How the HART Communicator Works?
- What is the Hart Protocol for Pressure Transmitter?
- Why need a 250 ohm resistor in HART Protocol?
- What is the difference between 4-20mA and 4-20mA HART?
The following wiring configurations for HART-based bench calibration of pressure transmitters show different ways of connecting a HART communicator with a 250-ohm resistor. Every arrangement maintains the integrity of the analog current loop while guaranteeing precise signal measurement and efficient digital transmission.
Method:1 Wiring Diagram for Pressure transmitter Calibration in Workbench using HART
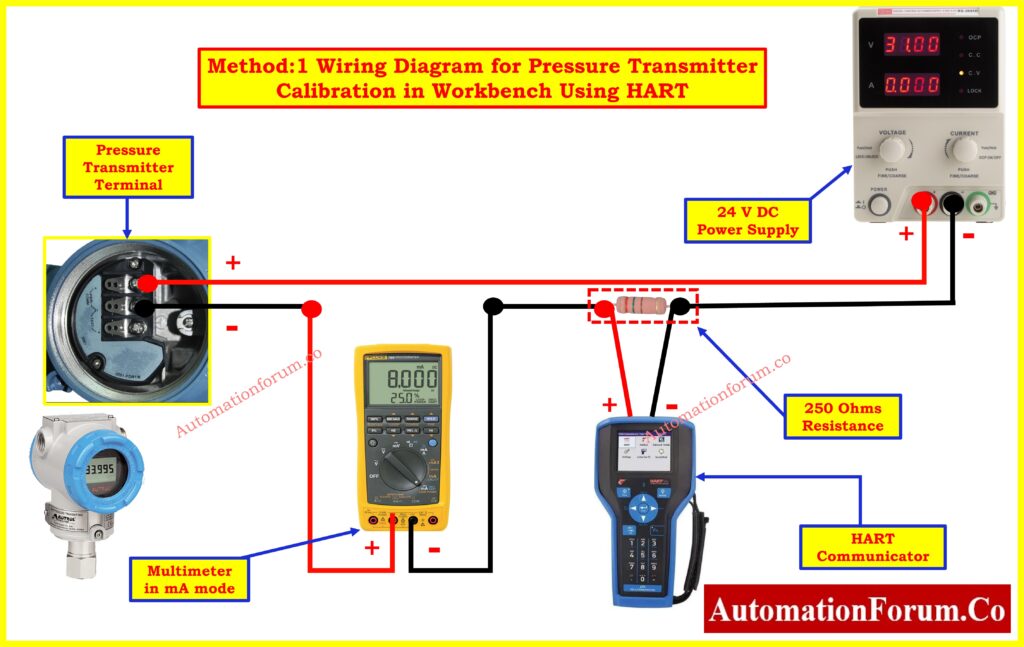
This wiring diagram illustrates the setup for calibrating a pressure transmitter using a HART communicator in a workbench environment. The step-by-step explanation of the wiring setup is below:
Components Involved in Wiring
- Pressure Transmitter is the device being calibrated, shown with its terminal connections exposed.
- 24V DC Power Supply Provides power to the transmitter and the circuit.
- 250 Ohms Resistance is Connected in series with the transmitter. This is necessary for HART communication, as it creates a voltage drop for the HART signal.
- HART Communicatoris a handheld device used to communicate with and configure HART-enabled instruments.
- Multimeter should be set to mA mode to measure the current output of the transmitter.
- Wiring in the image shows positive (+) and negative (-) connections for wiring.
Wiring Procedure:
- The positive terminal of the power supply connects to the positive terminal of the transmitter.
- The negative terminal of the transmitter connects to one end of the 250-ohm resistor.
- The other end of the resistor connects to the negative terminal of the power supply.
- The multimeter is connected in series to measure the current.
- The HART communicator is connected across the 250-ohm resistor.
Note: The 250-ohm resistor is crucial as it provides the necessary impedance for HART communication while allowing the current loop to function normally.
Safety Precautions:
- Double-check all connections before applying power to prevent any short circuits or damage to the equipment.
- Ensure the multimeter is correctly set to measure current in mA to avoid errors or equipment damage.
Method:2 Wiring Diagram for Pressure transmitter Calibration in Workbench Using HART
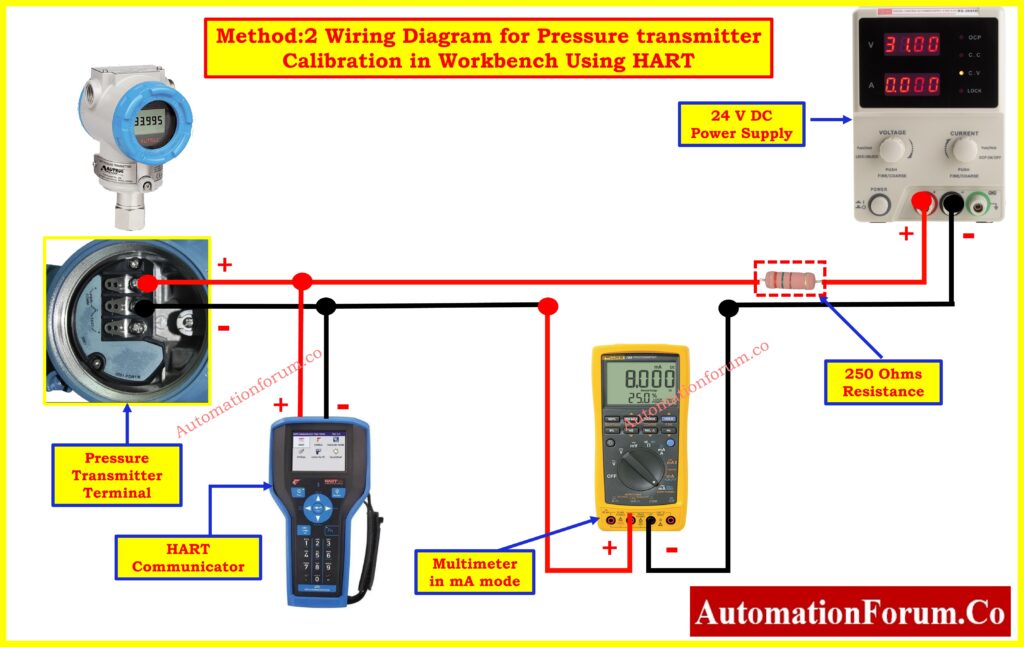
The above diagram shows an alternative method for calibrating a pressure transmitter using HART communication. The wiring connection setup is explained in the below procedure:
How do I connect my hart to my pressure transmitter?
Wiring Procedure:
- The positive terminal of the 24 V DC power supply is connected to one side of the 250-ohm resistor.
- The other side of the 250-ohm resistor is connected to the positive terminal of the pressure transmitter.
- This ensures that the resistor is in series with the transmitter on the positive side of the loop.
- The negative terminal of the pressure transmitter is connected to the positive terminal of the multimeter.
- The negative terminal of the multimeter is connected to the negative terminal of the 24 V DC power supply.
- This completes the 4 to 20 mA current loop in the circuit..
- The HART communicator is connected across the transmitter Hart loop in between terminals (positive and negative).
- The resistor is placed in series with the transmitter on the positive side. It is necessary for the HART communication to function properly, as it provides a path for the HART communicator to impose its digital communication signals on the current loop.
- This setup allows the HART communicator to send and receive digital signals over the 4-20mA analog current loop.
Method:3 Wiring Diagram for Pressure transmitter Calibration in Workbench using HART
In this method, the HART communicator is directly connected to the HART transmitter terminals. The below procedure will cover detailed explanation of the wiring connection setup:
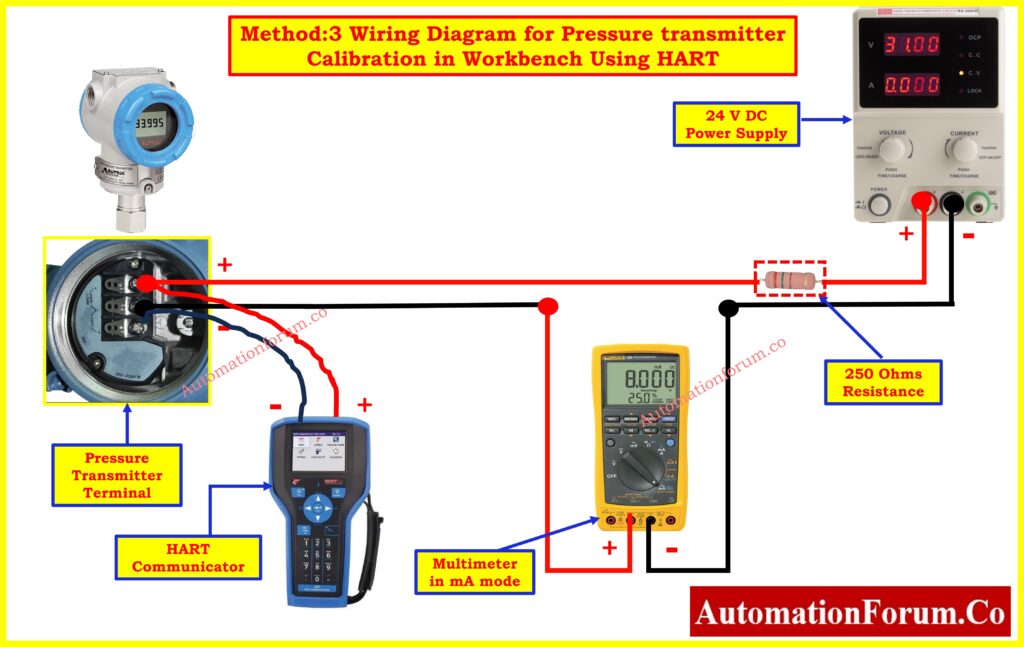
Wiring Procedure
- The positive terminal of the 24 V DC power supply is connected to one side of the 250-ohm resistor.
- The other side of the 250-ohm resistor is connected to the positive terminal of the pressure transmitter.
- The negative terminal of the pressure transmitter is connected to the positive terminal of the multimeter (need to be set in mA mode).
- The negative terminal of the multimeter is connected to the negative terminal of the 24 V DC power supply. This completes the 4 to 20 mA current loop in the circuit.
- The HART communicator is directly connected across the pressure transmitter’s positive and negative terminals.
- This setup allows the HART communicator to directly communicate with the transmitter for calibration and configuration.
- The power supply provides the necessary 24 V to the loop. The current flows from the power supply, through the 250-ohm resistor, into the transmitter, through the multimeter, and back to the power supply.
- The multimeter measures the current flowing through the loop, which should reflect the output of the pressure transmitter in relation to the applied pressure.
- By connecting the HART communicator directly to the transmitter terminals, it can communicate with the transmitter to perform tasks like calibration, configuration, and diagnostics.
- The direct connection allows the HART communicator to send and receive digital signals directly to and from the transmitter, without needing to interact with the rest of the loop.
All three wiring connection setups facilitate powering the transmitter, measuring its current output, and enabling communication via the HART protocol for configuration and diagnostics during calibration activities.
Refer the below link for the calibration procedure of Hart pressure transmitter
Importance of the 250-Ohm Resistor In HART Communication
Impedance Requirement
For the HART protocol to work, there should be a loop impedance of between 230/ohms and 1100/ohms. The 250-ohm resistor guarantees that this loop satisfies this condition and therefore opens a way to proper and effective HART communication.
Signal Separation
The resistor develops a voltage across it , wherein the HART digital signal is placed on top of the 4-20 mA analog current. This split is necessary particularly for the HART communicator to filter out the digital signal from the analog one.
Current to Voltage Conversion
The 250-ohm resistor then changes the received current signal (ranging from 4-20mA) into a voltage signal that the HART communicator can quantify.
Protection
It also helps to shield the power supply and other components in the loop from the ac component of the HART signal, and thus keeps the loop stable during the communication.
How the HART Communicator Works?
Digital Communication
The HART communicator encodes the digital signal with an existing 4 to 20 mA analog signal using Frequency Shift Keying (FSK). This leads to the digital communication without affecting the analog measurement.
Bidirectional Communication
It is possible for the communicator to effectively read various data from the transmitter as well as write data to it. This involves capturing of values, writing of values and performing diagnostics on the reader without interfering with the analog signal that is on progress.
Functions
It allows specifying the parameters of operation of the device, detecting malfunctions, and adjusting the transmitter. These are the functions of installation and maintenance of transmitter in the field.
Connections
In the above all connection setup, the HART communicator is connected across the 250-ohm resistor, allowing it to send and receive HART signals. This connection point is critical as it allows the communicator to access the superimposed digital signal.
Non-intrusive
It should be noted that in comparation to most of the other protocols, HART communication does not have any impact on the analog signal. This means that one can use digital communication while at the same time using analog measurement with out Interference.
What is the Hart Protocol for Pressure Transmitter?
Pressure transmitters use an analog 4–20 mA signal, which is overlaid with digital transmission using the HART (Highway Addressable Remote Transducer) protocol. Without interfering with the main analog signal, it enables sophisticated configuration, diagnostics, and data extraction, resulting in more data and better process instrumentation management.
Why need a 250 ohm resistor in HART Protocol?
The 250-ohm resistor provides the necessary impedance for the HART protocol to function correctly. It creates a voltage drop that allows the HART signal to superimpose on the 4-20 mA analog signal, facilitating digital communication.
The loop resistor value is defined by the HART specification as being between 230 and 600 ohms. A typical value is 250 ohms. The amount makes it simple to convert a current value to a voltage value that is needed in some control systems. Here, 4 mA is 1 Vdc when passing through a 250 ohm resistor, and 20 mA is 5 Vdc.
What is the difference between 4-20mA and 4-20mA HART?
A typical analog current loop used for process measurements is shown by the 4–20 mA signal. On the other hand, 4-20mA HART incorporates an additional digital communication layer on top of the analog stream.
This improves overall process management by enabling extra data, configuration, and diagnostics without interfering with the primary analog measurement.The 4–20 mA signal is overlaid with a frequency shift keyed (FSK) signal to form the typical HART transmission. 1200 bits per second (bps) is the transmission speed for the FSK bits.
Click here for knowing more about HART Protocol