What is pressure gauge?
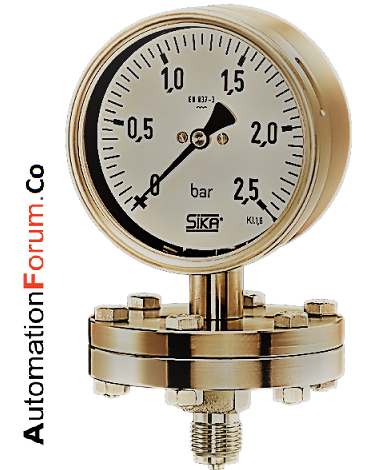
The pressure gauge is one of the widely used instrument to measure pressure. The widely used bourdon gauge measures and indicates pressure. The principle used in bourdon pressure gauge is that a flattened tube tends to straighten or retain its circular form in cross-section when pressure is applied.To measure pressure which is lower than the ambient pressure in atmosphere, a vacuum gauge is used, which is set as the zero point, in negative values . Almost all gauges measures pressure that is relative to atmospheric pressure as the zero point. This type of reading is referred to as gauge pressure. However, anything which is higher than total vacuum is technically a form of pressure.
What are the main parts of pressure gauge?
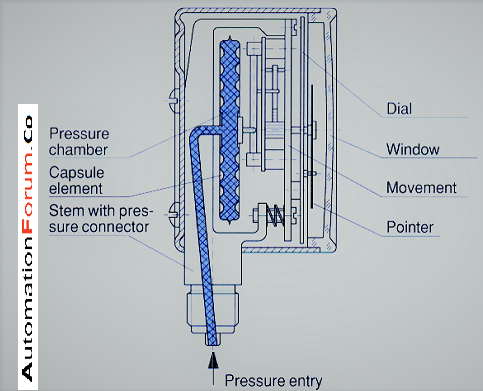
The main parts of pressure gauge are,
- Case: The case holds all moving parts of the pressure gauge in one place and protects the components from any damage. Depending on the demands of the application cases are made out of a variety of materials. For industrial applications, the cases have to be made rugged material, such as stainless steel, while for commercial applications may only require steel or aluminum cases.
- Hair spring: Hair spring is responsible for controlling the torque. It also eliminates any play into the linkages.
- Linkage: The linkage connects bourdon tube to the gear mechanism. The linkage transmits the movement of the bourdon tube to gear mechanism to activate the gears.
- Gear mechanism: Gear mechanism is the recipient of the movement from the linkage and bourdon tube and it is the part which controls the movement of the pointer.
- Dial face: The dial face contains the different pressure measurements and have gradations in pound force per square inch, kilogram force per square centimeter format, standard atmosphere.
- Pointer: The pointer is the visible part of the pressure gauge during measurement.
- Window: The window is made up of clear plastic or glass material and protection for pointer and dial face.
What are the types of pressure gauge or how pressure gauges are classified?
Pressure gauges are widely used in industrial application for measuring pressure. Pressure gauges are classified based on their sensing elements into:
Bourdon tube type pressure gauge:

These are most common type of pressure gauge used in industrial applications. As shown in the figure, the pressure input is given to a socket which is soldered to the tube at the base. The free end of the instrument is sealed by a tip. This tip is connected to a segmental lever through an adjustable length link. The lever length may also be adjustable. The tube walls will have a thickness between 0.01 and 0.05 inches. The basic element in the all the various forms is a tube of non circular cross section. The difference in pressure between inside and outside of the tube (high pressure inside) causes the tube to attempt to attain circular cross section. This result in distortion which leads to curvilinear translations of the free end in ‘C’ type and Spiral and Helical types and an angular rotation inthe twisted type and these motions are the output.
The expansion of Bourdon tube due to internal Pressure. Like all the elastic elements, a bourdon tube also has some hysteresis. By the right choice of material and its heat treatment, hysteresis may be kept within 0.1 and 0.5 percent of the maximum pressure cycle. When the fluid pressure enters the bourdon tube, it tries to be reformed. Due to this reformation, a free tip is available, this action causes the tip to travel in free space and the tube unwinds. A non-linear movement of the free tip occurs due to the simultaneous actions of bending and tension due to the internal pressure. This travel is suitably amplified for the measurement of the internal pressure. But the main requirement of the device is that when ever the same pressure is applied, the movement of the tip should not change in each time and on withdrawal of the pressure, the tip should return to the original position. The average linear motion of the tip when converted to a circular motion with the link-lever and pinion attachment, a one-to-one correspondence between them may not occur and distortion results. This is known as angularity which can be reduced by adjusting the length of the link. Other than C-type, bourdon gauges can also be constructed in the form of a helix or a spiral. The types are varied for specific uses and space accommodations, for better linearity and larger sensitivity.
Diaphragm type pressure gauge:
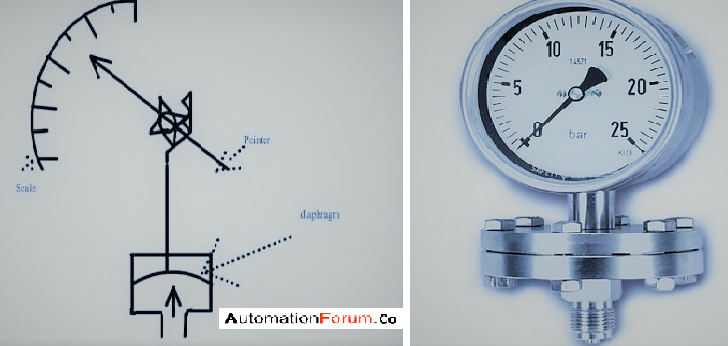
A diaphragm pressure gauge is a device, which uses a diaphragm with a known pressure to measure pressure in the fluid. The main application of this type of pressure gauge such as controlling the pressure of a canister gas, measurement of atmospheric pressure, recording the strength of vacuum in a vacuum pump. The diaphragm pressure gauge made up of a circular membrane made from a sheet metal which can be a flat or corrugated. The diaphragm is connected to the transmission mechanism. This will amplify small deviations of diaphragm and it will be transferred to the pointer. The process pressure is applied to the lower side of the diaphragm, the upper side is at the atmospheric pressure. The diaphragm is lifted upwards due to the differential pressure arising across the diaphragm and puts the pointer in motion. The deflection of the diaphragm is very small (+/- 1 mm) making it necessary to use a high-ratio multiplying movement to rotate the pointer down the full length of the scale. The actuation of such a high-ratio transmission mechanism is possible because diaphragm deflection is able to generate large force.
Bellow type pressure gauge:
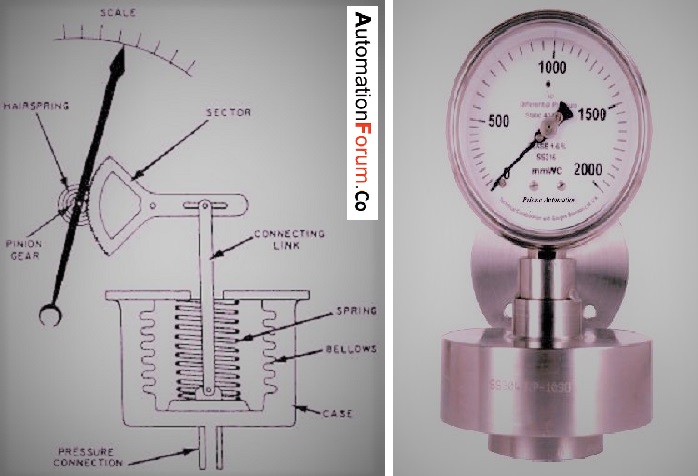
Bellows are thin walled metallic cylinders of which one end is sealed and the other end remains open. The open end is fixed and the closed end is free to move. The bellows will be compressed when pressure is applied to the closed end. The closed end will move upwards. The link, which is the rod in between the transmission mechanism and the closed end of the bellows, will go up and rotate the pointer.
The diameter of the bellows that determines the force which can be transmitted to the transmission mechanism. For the measurement of very low pressures, a larger diameter is to chosen in order to have enough surface area to which the measured pressure can act. A larger diameter also gives higher sensitivity and accuracy. Bellows can be fabricated from different materials and has its own specific stiffness which is proportional to Young’s modulus of the material and inversely proportional to the outside diameter and number of convolutions of the bellows. The bellows are sensitive to temperature changes, drift, hysteresis, vibrations, friction. To compensate this, bellows are generally used in a combination with calibrating spring. Also the measuring range can be determined by the choice of the spring. Strong spring makes it possible to measure large pressure. This is why most bellows gauges are spring-loaded. It also protects the bellows from being completely stretched beyond the elastic limit.
Capsule type pressure gauge:
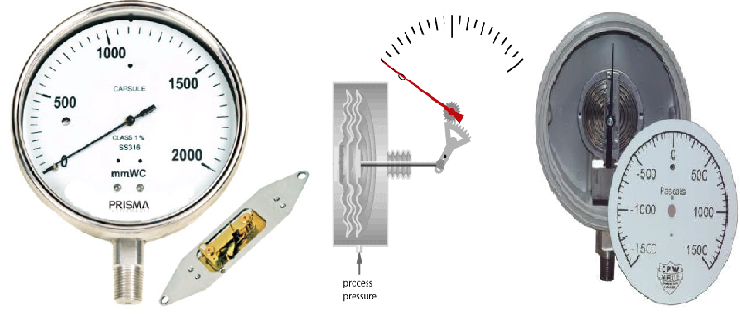
The capsule pressure gauge used to measure low pressure efficiently. It contains a bellow type element instead of a bourdon tube. The capsule pressure gauge can measure negative values up to 600 millibar with a high accuracy. The pressure gauge is made up of two corrugated thin diaphragms that are welded together. When the pressure changes, it causes the capsule to change shape on both sides of the measuring element. Then it is transferred through mechanical movement, causing the pointer to show the pressure measurement. Almost all capsule gauges are made out of stainless steel, making them suitable for use in corrosive environments and gaseous media.
What is a differential pressure gauge?
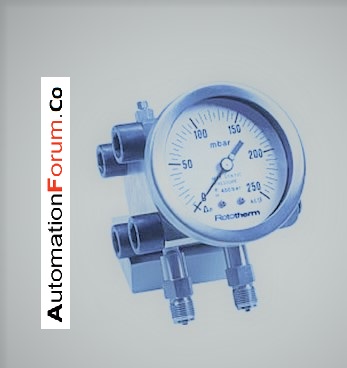
Differential pressure gauges use a U-tube to illustrate the difference in pressure between the two points. The instrument contains two entrance ports, which are connected to monitor the pressure capacities. This makes the instrument to display both pressure measurements and makes it more efficient than reading the pressure from two gauges and calculating the difference.
There are three types of differential pressure gauges,
- Piston type
- Dual Diaphragm type
- All-Welded type
The three differential pressure gauges are suitable for various applications and the choice depends on specific applications. Dual diaphragms type are best suited with low differential pressure atmosphere. The all welded pressure gauges are suitable for corrosive atmospheres. Piston type differential pressure is used to work in gaseous media.
How to calibrate pressure gauge?
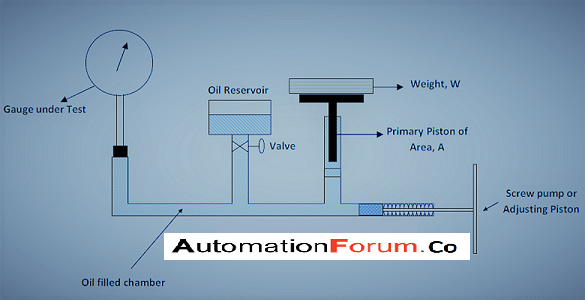
Materials required:
- Data sheet
- Dead weight pressure gauge tester
- Test gauge
- Dead weight
What is the procedure for calibrating pressure gauge?
The following steps are the procedure for calibrating pressure gauge using a dead weight pressure gauge tester. Dead weight pressure gauge is a testing instrument which helps to calibrate and test the pressure gauges.
- The oil tank is filled with sufficient oil.
- Then release the AIR RELEASE VALVE.
- The oil starts dripping continuously.
- Close the valve when it reaches 10-12 drops.
- Release the control valve and pump so that the oil will circulate through the tubes.
- Pump for certain time till all the tubes will be filled with oil so that any air bubble inside the tube will be removed .
- Then close the control valve, and pump the oil till the line on the plunger is visible and rotate the plunger gently.
- The pressure is built inside the chamber is proportional to the weight on the plunger and the Test Gauge fixed will start showing the pressure.
- Then add dead weight on the plunger and continue pumping till the line on the plunger is visible.
- The pressure inside the chamber gradually increases by 1 kg/cm². Now add another weight on the plunger and pump till the line on the plunger is clearly visible.
- The bourdon tube pressure gauge will read the pressure corresponding to the deadweight on the plunger.
- Note down the readings on the pressure gauge and with the corresponding readings to the dead weight.
- Plot the graph for actual pressure vs pressure gauge reading.
- Calculate the accuracy,linearity of the pressure gauge.
- Slowly release the control valve and remove the dead weight from plunger.
What are the applications of pressure gauge?
- Diaphragm pressure gauges are used for the measurement of steam pressure in kitchens.
- For high pressure cleaning and water jet cutting, bourdon tube pressure gauges are used.
- For the measurement of temperature in tanks on utility vehicles .
- For the inspection of air brake system in trucks.