- What is an HMI?
- What are the benefits of HMI?
- What are the major functions of HMI?
- What is a high-performance HMI?
- What is the purpose of HMI?
- Various standards involved in developing HMI graphics
- How does an HMI work?
- What is ASM?
- Why ASM must be used to monitor an industrial plant?
- What are the standards mentioned in ASM for various components in HMI?
- How does an HMI with ASM standards solve abnormal conditions?
- What are the advantages of ASM standard HMI over normal HMI?
- What are the advantages of HMI?
- What are the major applications of HMI?
What is an HMI?
A human-machine interface (HMI) is a system that can be connected to the DCS or SCADA control system and the HMI would display the process data to the user. The HMI would display the processed data to a human operator and by the HMI system, the operator can monitor and transmit signals to the controllers to do the required operations. So we can describe the HMI as a user control station and mostly this would be in the form of monitors or touch screens with buttons attached to it. HMI would be a part of the DCS or SCADA control system so that it can display the process data which is controlled by this control system. HMI would be mostly connected to a system or a process. HMI has less memory when compared to the SCADA and DCS.
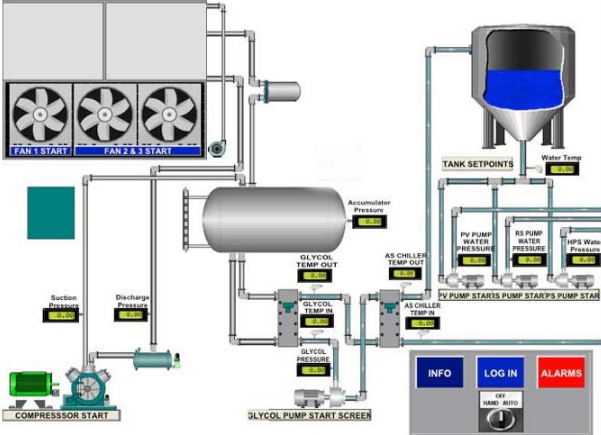
What are the benefits of HMI?
- Monitoring and controlling of industrial process
- User-friendly configuration and due to this, it can also be monitored by a new user
- Good connectivity features it can be connected to other software, devices, and system
- Powerful thin client technology
- Sophisticated alarm and trending
- True client/server architecture for ease of scalability
What are the major functions of HMI?
- Graphical representation of the process
- Alarms and events – Recording specified changes and operator actions
- History database, this is to keep the record of the process values
- Logging -keep logs on the operation of the automation system
- Reporting – generate incident reports
- It would be useful to monitor and supervise the control process
- It would represent the plant in real-time
- Statistical process control
What is a high-performance HMI?
- It can detect abnormal situations before the alarm occurs
- Good success rate in handling abnormal conditions
- It would quickly complete the abnormal situation tasks
What is the purpose of HMI?
HMI would act as the user interface in a process control system, HMI would provide a graphics-based visualization of industrial control and monitoring system. HMI would make sure that the human-machine interaction can be easily done. HMI would vary from control panels for power plants to the screen and input keys of a cell phone. The major part of an HMI is the interface between the user and the machine so that users can send required signals to the controller to control the machines. The major input device in an HMI would be the keyboard, toggles, switches, touchscreens, and mouse. It would display the progress of the process to the user.
Various standards involved in developing HMI graphics
The HMI graphics is an important way of representing the industrial process so they should be descriptive and it should not have colors with high contrast. In earlier days the HMI displays were really colorful and it would poorly depict the numerical data there won’t be any correlation between the graphics and the data. It would display less information with more pictures. Now we can see many changes in HMI and now there are high-performance HMI with better graphical features.
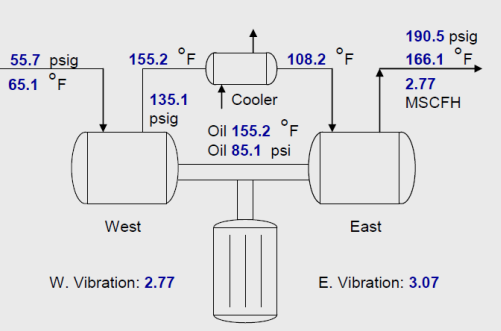
- Nonschematic depiction
- Limited usage of color
- Grey background is used to reduce the glare
- No animation except for alarm related
- Embedded trends with better parameters
- Analog representation with value relative to normal, abnormal, and alarm
- Hierarchical display of screens and sub-screens
- Low contrast depiction in 2D not in 3D
- Proper navigation
- Alarm colors would only be used for alarms
- Indicators would only appear in the event of an alarm
For things that are normal grey color is used like pipelines, vessels, etc. use low contrast for normal things but for abnormal conditions high contrast will be used. Warm colors such as red, orange, and yellow can be used to draw attention. Complex graphics and 3D objects would be very difficult to be used in a metal model. We shouldn’t choose display according to the trend, in case we choose a trend display that has eight variables then it would make confusion and also would take a long time to analyze.
How does an HMI work?
HMI would provide the interface in a process control system, HMI would be connected to the control system. So the operator can interact with another device with the help of HMI. So the HMI would be connected to the control system and due to this it can collect the process data and also it can create reports and can perform alarming functions, it would also display notifications. So based on these data’s alarms and notifications we can take proper measures to control an industrial process.
What is ASM?
ASM means Abnormal Situation Management, ASM standards were invented to do better alarm management, there are many cases where the operator would be overloaded due to the alarm floods in abnormal conditions. The ASM can detect the events before the alarming due to its situation awareness, so the operator would be updated according to the variations and he can take necessary actions to prevent any problematic events.
Why ASM must be used to monitor an industrial plant?
ASTM standard is created to handle the abnormal conditions, so during abnormal conditions, the operator would see many alarming events in a normal HMI. All these alarming events should be handled properly at a proper time otherwise it can create a lot of damage to the process plant. In order to avoid this problem, ASM standards are used. If an HMI is developed with ASM standards, then that HMI will have better monitoring features and it could detect a problematic event before the alarming and the operator would have time to solve all these problems before it can occur.
What are the standards mentioned in ASM for various components in HMI?
Design standard
- Bright intense colors would be used for alarms and these colors won’t be used for anything else
- Low intense colors would be used for real-time data
- Mostly the display background color would be grey because it would have less interference with other colors.
- There would be less foreground color and the colors which are used for alarms and real-time data won’t be used for other objects.
- There won’t be any gradient colors, dark grey or black colors would be used for process lines
- State depiction would be done by colors, text, or by using shapes
- The color which is utilized would be standardized, consistent and it would be added to the HMI
- The color which is used would have proper contrast too much contrast would lead to eye strain
- In order to display important factors shapes and colors are used together because certain colors could cause visual illusions when placed near to each other
Various levels of HMI display
- Level 1 display would provide an area-wide overview, it would show critical variables like major equipment status, abnormal situation, etc.
- Level 2 would display the processing unit wide controllers, values, etc.
- Level 3 display would show detailed operating information control loops, troubleshooting displays, etc.
- Level 4 display would provide auxiliary information like help screens, documentation, trends, etc.
How does an HMI with ASM standards solve abnormal conditions?
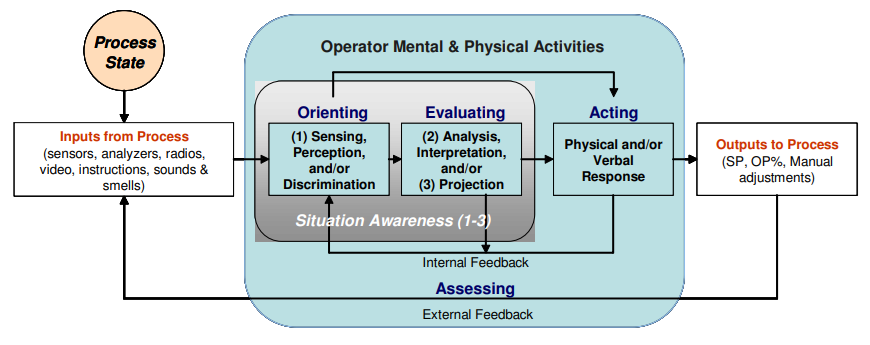
We can use the HMI with ASM standards to do the operation of complex industrial plants. The major concept of using an HMI with ASM standards is to prevent and respond to abnormal situations. If an industrial process is affected by an abnormal situation, then the control system must be able to handle the abnormal situation if not it can lead to many problems. So in order to handle the abnormal situations, HMI with ASM standards are used.
Abnormal situations would impact profitability in many ways
- Product quality
- Equipment damage
- Loss of life
- Personal injury
- Product thruput
- Maintenance costs would increase
So the ASM would use operator-friendly graphics which would be very easy to analyze. This standard would improve the usability and effectiveness of the human-machine interface. Grey background color would be used for the display and high contrast color won’t be used high contrast color would only be used to indicate the abnormal conditions. The ASM also has a predictive maintenance feature that would provide variations in the data and the operator can work on it before the abnormal situation arises.
ASM based HMI can provide
- Proactive monitoring
- Quick response
- We can detect the event before the first alarm
- Proper handling of abnormal conditions
- We can easily analyze the data
What are the advantages of ASM standard HMI over normal HMI?
- Better reliability and safety
- Proper alarm management
- There is no unplanned maintenance due to the predictive planning
- Hazards can be identified quickly
- Operating costs will be low because of the higher data quality and transparency
- Improved human-machine interaction
- Single integrated view of the multilevel hierarchy
- Mixed initiative approach
- It can detect events before the alarm
- Effective window management and layout
- Good navigation
- Visual coding scheme
- Interaction objects
- Better task view
- The operator would only take less time to solve a problem
- It can monitor the whole plant
- Problems can be easily determined and can take proper actions too
- User-friendly graphical features
What are the advantages of HMI?
- User-friendly display
- Real-time data would be displayed
- It can decrease the cost of product manufacturing
- Profit can be increased
- More interactive
What are the major applications of HMI?
- Machine monitoring
- SCADA
- Monitoring the control center
- Building automation and security
- Monitoring electrical substation
- Pipeline monitoring
- It is also used in transportation control system
- Telecommunication
- Statistical process control