- What is a PLC control system and how does it operate?
- Advantages of PLC control system
- Disadvantages of PLC control system
- Applications of PLC control system
- What is DCS and how does it operate?
- What are the major functional requirements of DCS?
- Advantages of DCS
- Disadvantages of DCS
- Applications of DCS
- What is a SCADA control system and how does it operate?
- What are the major functions of SCADA?
- Advantages of SCADA control system
- Disadvantages of SCADA control system
- Applications of SCADA control system?
- Comparison between SCADA and DCS (SCADA VS DCS)
- Comparison between PLC and DCS (PLC vs DCS)
- How SCADA control system is different from PLC and DCS?
- Comparison table between PLC, DCS, and SCADA?
- When should we use PLC, DCS, and SCADA?
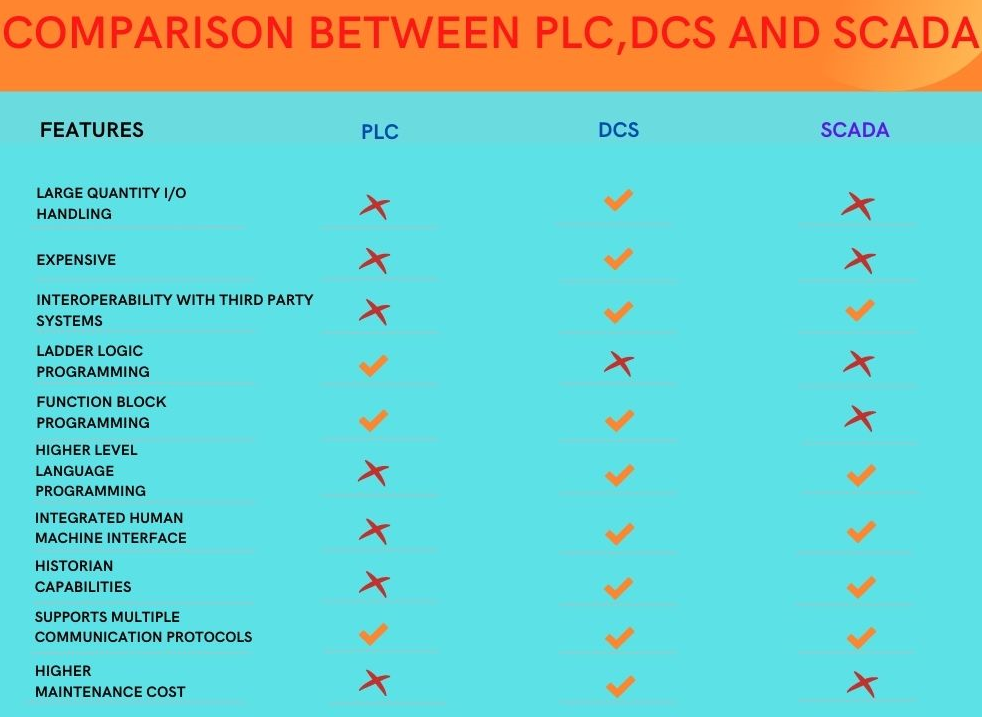
What is a PLC control system and how does it operate?
The Programmable logic controller is a digitally operated device that has a programmable memory for storing the instructions and also to do, the specified functions. A PLC would do logic, arithmetic, timing, counting, and sequencing functions to control various machines in an industrial process. We can use a PLC to do the automation of an industrial process like controlling the industrial machinery on a factory assembly line. We can improve the accuracy and speed of an operation by using PLC. So the PLC would take inputs from devices such as limit switches, proximity sensors, pressure sensors, etc.
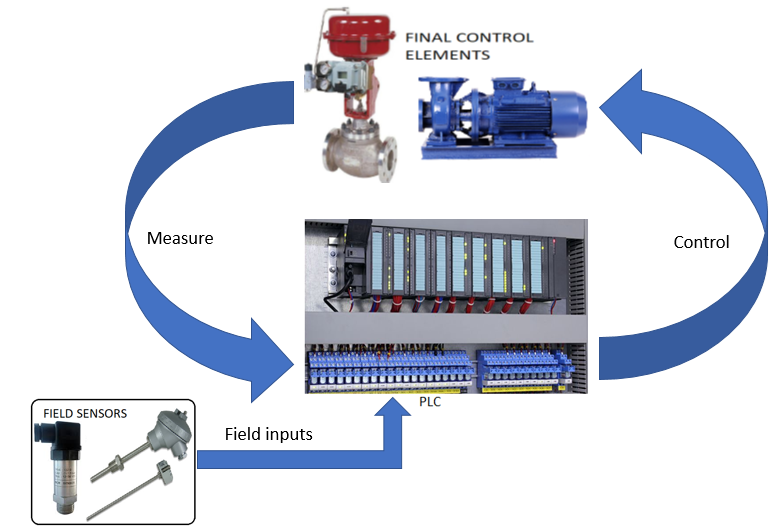
The conversion of the logic signal in the PLC and also the high-level signals in the field would be done by the I/O modules and it would also do the signal isolation. The PLC system activities would be carried out with the processor intelligence. The programming devices which are used to enter the desired program would mostly be a PC. Based on the entered program the PLC would do the operation and also it would control the process equipment. The PLC would check the input devices and then it would execute the program, after that it would energize or de-energize the output devices which are connected to it.
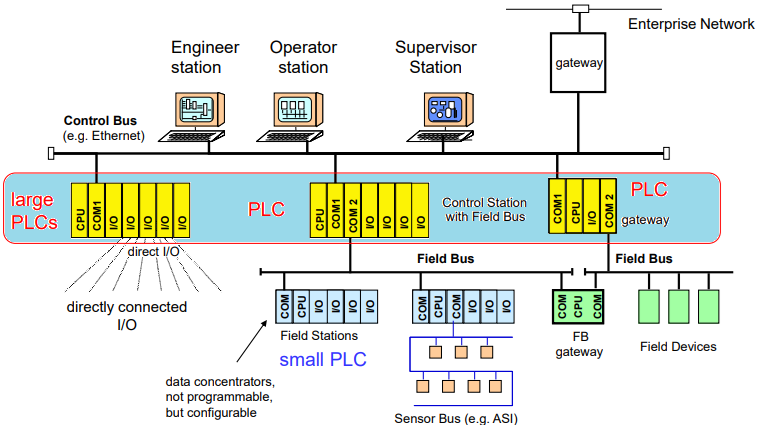
Advantages of PLC control system
- Reliability
- Flexibility in programming and reprogramming
- High operational speed
- Quick response time
- Easy troubleshooting
- Low cost
Disadvantages of PLC control system
- Limited design
- Fixed circuit design
Applications of PLC control system
- Food processing
- Material handling
- Machine tools
- Conveyor system
- Robot manufacturing and control
What is DCS and how does it operate?
In a DCS system, the total process would be divided into a certain number of subsystems. Each of these subsystems would be controlled by its own controller. So we can describe a DCS as a large process that is controlled by a certain number of controllers and each of these controllers would control its own subsystem. This system would divide the plant into different areas and assign separate controllers to each area of the plant. This whole system would be connected to become a single control system with the help of communication buses. This whole system would be connected to a communication network to do the communication and monitoring. The total controllers in the DCS system would be connected by the network to do the communication.
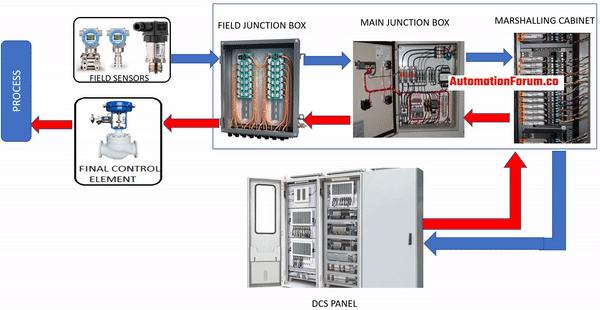
The DCS would collect data from the field device and these data would be checked and then it would utilize this data to control the specified process. So, based on the data which is received from the field device and also from the data which is gathered from another part of the plant would be utilized to control the process. The field device would transmit the process, signal to the field junction box from there it would reach the marshaling cabinet through the main junction box. This signal will be transmitted to the DCS panel by the marshaling cabinet. Then according to the received signal, the proper control signal will be transmitted by the DCS panel to the final control element.
What are the major functional requirements of DCS?
- Control
- Data acquisition
- Alarming
- Logging and report generation
- Historical data storage
- System diagnosis and security
Advantages of DCS
- Separate controllers are used to control, different processes and due to this failure of one control station won’t affect the whole plant
- Redundancy
- Access a large amount of current information from data highway
- Past process condition trends can be monitored
- Less overloading of the system
- Reliability
- Good speed
- Process information can be visualized by the user in different formats
Disadvantages of DCS
- Expensive
- Needs regular maintenance
- More prone to cyber security threats if not protected properly
- Needs regular upgrade of the system when technology evolves like windows OS going obsolete, DCS OEM support for particular version is not available etc.
Applications of DCS
• Power grid
• Oil and gas industry
• Chemical industry
• Water management systems
• Pharmaceutical manufacturing
What is a SCADA control system and how does it operate?
SCADA stands for supervisory control and data acquisition, as the name indicates the SCADA system supervises, acquires, and controls the data which is received from a distant data source from the control center. So the SCADA system supervises the communication between the remote station and the control center by means of two-way communication channels. So basically it can’t be called a whole control system, SCADA is software that is positioned on top of hardware to which it is integrated. A SCADA would allow the operator to monitor the equipment status and based on that the operator can control the process. The operator can view all the process parameters from a single central control room.
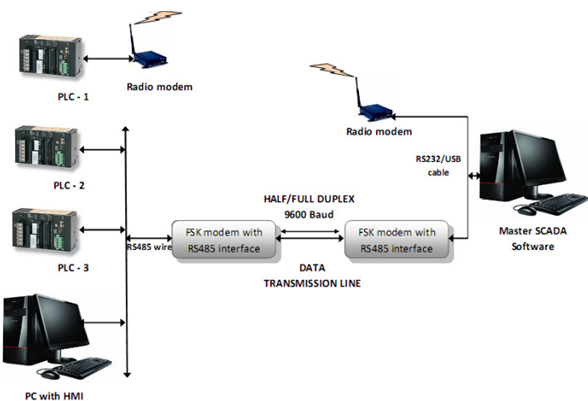
What are the major functions of SCADA?
Data Acquisition
It would show the status information and measurands data to the operator
Control
The operator can control the device according to the received data
Data processing
It would check the data quality and integrity
Tagging
Identification of specific subjects or devices so that they can be prevented from unauthorized operation
Alarms
The operator would be alerted by the alarm in case of unplanned operations or in case of undesirable operating conditions
Logging
All operator entries, alarms, selected entries would be logged
Trending
It would plot the measurement on the selected scale to give information on trends like one minute, one hour, etc.
Historical reporting
This would save and analyze the historical data and this can be useful to control the future process.
Advantages of SCADA control system
- Easy to maintain
- It would provide access to real-time data
- Implementation tools are advanced
- Reliable
- Continuous operation
- Maintenance of equipment can be improved
- Distant communication
- We can monitor the process remotely
Disadvantages of SCADA control system
- Implementation would need special skills
- It would only process data when the system is available
- Compatibility with PLCs needs to be verified
Applications of SCADA control system?
- Power generation, transmission, and distribution
- Water and sewage
- Building facilities and environment
- Manufacturing industries
- Mass transit
- Traffic signal
- Steel industry
- Chemical industry
Comparison between SCADA and DCS (SCADA VS DCS)
SCADA | DCS | |
Geographic span | Large- cross country | Small |
Data acquisition rates | Moderate seconds to a minute | Very fast milliseconds to seconds |
Data acquisition network | Slow with a moderate error rate | Fast with a low error rate |
Graphic user interface | Basic | Full-featured |
Alarming subsystem | Basic | Full-featured |
Control actions | Human initiated | Programmatically initiated |
Operation method | Data gathering oriented | Process-oriented |
Process controlling | SCADA would only collect details from the field and transmits them to the controller | DCS would control the process through H/W such as AI, AO, DI, & DO |
Comparison between PLC and DCS (PLC vs DCS)
PLC | DCS | |
Process type | Discrete operation handling input in binary. (*Advance PLCs can process analog signals as well) | DCS would control analog as well as digital signals |
Response time | Faster than DCS | DCS is comparatively slower than PLC |
Scalability | PLC can only handle a few I/Os, due to this PLC is used for small scale equipment | DCS is capable to handle several thousand I/O’s and due to this DCS can handle a large process(entire plant) |
Redundancy | Can have Redundant configuration | Can have Redundant configuration |
Programming | Ladder logic, STL, Functional block diagram, etc | In DCS functional block programming is used |
Hardware package | HMI and other software would be required to handle the networking and communication | DCS is composed of HMI and software which would be useful for communication and networking |
How SCADA control system is different from PLC and DCS?
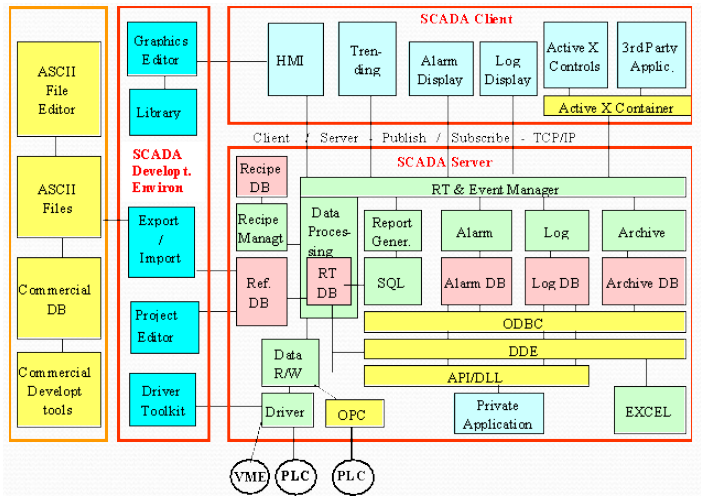
SCADA is a control system architecture that utilizes computers, networked data communications, and a graphical user interface to do high-level process management. PLC and DCS have hardware packages with them but SCADA doesn’t have this, SCADA won’t send some binary or analog signal to the field devices to control the process. SCADA would only control the process by using certain controllers like PLC, DCS, or PID. So these controllers would control the field element and the process would be supervised or controlled by the SCADA. The command signal to control the process would be given to SCADA these command signals will be transmitted to the PLC/DCS/PID controllers to control the process. So we can consider the SCADA as software that would communicate to the PLC and DCS.
Comparison table between PLC, DCS, and SCADA?
PLC | DCS | SCADA | |
Functions | Single process control | Entire plant control | Provides communication between equipment in a plant |
Speed | Faster than DCS & SCADA | Faster than SCADA | Slower than DCS |
Networking | Engineered networking as per requirements | All the components are tightly integrated into the network | All the components are tightly integrated into the network |
Communication | Doesn’t have a wide range of communication | Wide range of communication | Wide range of communication |
Margin for error | Only one device controls the process so there is a chance for error | There are many controllers so less margin for error | Less margin for error |
Pricing | Low cost | High initial cost | High initial cost |
Major brands | Allen Bradley, Texas Instruments, Omron, etc. | Honeywell, Yokogawa, Siemens, etc. | Allen Bradley, Siemens, MODICON etc. |
Monitoring range | Short distance (single process) | Entire plant | Long-distance monitoring |
System composition | Hardware | Hardware, Visualizing software, and historian | No hardware, Data collection, and monitoring |
Flexibility | Highly flexible | Due to the complex architecture, it is not flexible as PLC | Due to the complex architecture, it is not flexible as PLC |
Process changes | It can handle process changes | Due to the complexity, it won’t be able to handle the process change | Due to the complexity, it won’t be able to handle the process change |
Applications | Used for dedicated applications | Used for complex applications | Used in big industries (Remote monitoring) |
When should we use PLC, DCS, and SCADA?
If we need to control a single process then we can use PLC, it can also be used when the industrial plant has extensive interlocking. PLC has a faster scan time when compared to the DCS, so it can be used to do the safety interlocks. PLC is used to control the discrete manufacturing process. PLC’s have replaced relays and it has good processing power.
PLC – Controller
DCS – Controller + Network + Software + I/O Acquisition
SCADA–Data collection + System monitoring + Network + Software
We can use DCS when we need to control an entire plant and it can also be used where the process failure could cause a lot of damages like in a chemical plant. DCS would divide the plant into certain sections and a process can be controlled in case there is any controller failure. Due to the wide range of networking features of the DCS, it would easily determine the faults. In order to determine the plant production rate industrial networking has become really important and due to this PLCs have become a section of DCS. If you need controller redundancy then you can choose DCS, so in case there is any controller failure then there would be a redundancy to our controller. If it is a large system and also you need to get much previous data then you can choose DCS.
SCADA is software not a controller like the DCS and PLC, basically, it collects data and monitors the entire plant. SCADA is used for huge industries where data collection, data transmission, and remote plant monitoring are required. SCADA system is used in power generation and transmission units, Oil and gas it is also used in many chemical plants where frequent monitoring is required. SCADA transmits data and commands to the PLC and DCS to control a specified process. A PLC would be used to control the flow of water through a certain part of the industrial process, by using a SCADA HMI system the operator would be able to vary the setpoint for the flow.