The proximity sensor is a type of sensor that can detect an object that is near to it without any physical contact. This type of proximity sensor works on the principle of electrical induction, the inductive proximity sensors are used for an application that needs accurate non-contact detection of the metallic object so it is used in machinery and also in automation equipment. The inductive proximity sensor is used for the detection of metallic objects, so this device would create an electromagnetic field and detects the object. The inductance is a process in which the fluctuating current would have a magnetic component, this would create an electromagnetic force on the object which is conductive. These sensors are widely used for the detection and positioning of ferrous and non-ferrous metal objects. These sensors are widely available in both AC and DC powered models and it would need three electrical connections which would be ground, power, and output.
- What is a proximity sensor and what is it used for
- What is a proximity switch and what is it used for? How do proximity switches work
- What are sensors on a robot and why are sensors important to robots
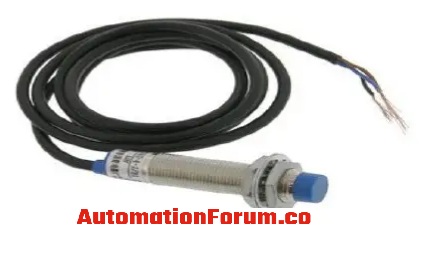
What is the difference between inductive and capacitive sensors?
The major difference between these sensors is the inductive proximity sensor would use a magnetic field to do the detection of the object while the capacitive sensor uses an electric field. The inductive sensor can only be used to detect the objects which are conductive while the capacitive sensors can detect the objects which are not conducive. The capacitive sensor can detect the dielectric and conductive objects.
How does an inductive proximity sensor work and what are its parts?
The inductive proximity sensor is composed of an oscillator, ferrite core with oil, a detector circuit, an output circuit, and a connector. So the oscillator circuit is the sensing part and the output circuit would have a switching device such as a transistor or a thyristor. The oscillator would generate a sine wave of fixed frequency, and the coil is driven by this signal. The coil that is connected with the ferrite core would produce an electromagnetic field. So if a metal object comes in place of these field lines then the field lines would get interrupted then the oscillator voltage will be reduced according to the size and also by the object distance from the coil. The oscillator voltage is reduced due to the eddy current that is induced in the metal field line, and the detector that is used in this sensor would know the reduction in voltage.
This type of proximity sensor can detect the object or it would generate the output signal when the conductive object comes in contact with its contacting area and they could detect the object from any direction. The inductive proximity sensors can detect objects such as iron, aluminum, copper, brass, etc. These sensors can detect the ferrous and non-ferrous metal objects and it is also capable to detect metal through a layer of non-conductive material. The inductive proximity sensors would operate better with ferromagnetic targets because they absorb more energy compared to non-ferromagnetic materials, so the operating distance for the sensor is more for ferromagnetic targets. Mostly the sensors operating range will be depended upon the shape and size of the actuator and it is dependent upon the nature of the material.
What are the advantages of inductive proximity sensor?
- It is very accurate
- It has a good switching rate
- This sensor is suitable for a bad environment
- Small in size
- Robust
- Economical
- Fast switching
- Reliable
What are the disadvantages of inductive proximity sensor?
- It can only detect metallic objects
- Limited operating range
What are the applications of inductive proximity sensor?
- It is used in automotive cruise control system
- It is used in access doors and panels of the machines
- Most of the helicopters have an inductive proximity sensor, to detect if there is any problem in the gearbox