A servo valve can vary the fluid flow according to the changes in the load motion. Servo valves can control high power by using small inputs and it could be electrical or mechanical. So basically a servo valve is a directional control valve, this valve can control the flow and also the direction of the flow. The servo valves are connected with a feedback sensing device and because of this, the servo valve can provide accurate control of the position, velocity, and also acceleration of the actuator. The servo valves are the control element in a servo system, a servo valve can provide the continuous variation of flow according to the input like a proportional valve. The proportional valve is almost similar to a servo valve, the major difference between these valves is the servo valves have better accuracy than a proportional valve, the servo valve is a closed-loop circuit while the proportional valve could be an open or closed-loop circuit.
- What is a proportional control valve?
- What is a rotary airlock valve?
- What is a choke valve and what are the functions of the choke valve?
- What is a vacuum breaker valve and what is the use of a vacuum breaker valve?
- What is a single-seated and double-seated valve and how are they different from each other?
- What are the problems in a control valve and how to do the troubleshooting and maintenance of a control valve?
How to select a servo valve?
- The oil volume between the valve and the actuator must be small
- It must be selected according to the response time
- We must consider the flow pressure gain
- If the oil volume is high then it would be good
- Installation position
- Temperature range
- Vibration
- Cavitation must be considered
- Fluid
- We must also consider the environmental conditions
What are the uses of a servo valve and where do we use it?
Servo valves are used to control the actuator, some actuators must move at a certain speed and it must create a proper force to do the work which they are designed for so by the proper signals and also by the help of feedback devices a servo valve can help the actuator to do all these functions properly. The servo valves are also used in hydraulic cylinders to do control their operation.
The servo valves are used as a control element in the servo system. In a servo system, a low-powered command signal will be compared with output and the error augmented by an auxiliary power source to give a high power drive to control that output. This device is really suitable for this purpose because of the high power density of the hydraulics. By using a servo valve we could get a continuous variation of the flow by varying the input signal. In a proper mechanical servo system, the valve is moved directly by a mechanism or linkage. But the electro-hydraulic servo valve works according to the electrical input and this valve is able to do the continuous control in order to use it for a closed-loop servo system.
What is a closed loop circuit and open loop circuit?
In an open-loop circuit, the controller would control the process according to the given input which is given from the controller to the valve. In a closed-loop circuit according to the requirement of speed, position, or pressure input signal is given and it is compared with the output value with the help of a sensor, and after that required adjustments are done. The servo valve has a closed-loop process in which the input signals and the output values are compared and the differences are removed and because of this high accuracy is achieved.
What are the types of servo valves and how do they work?
Mechanical servo valve
The mechanical servo valve is a mechanically operated valve and it can control the flow of hydraulic fluid to an actuator. This type of servo valve can be considered as a force amplifier and it can be used for position control. In this valve, a small input force will be provided and this force will shift the valve spool to the right by a specified amount. After that, the oil will flow through the port during this process the hydraulic cylinder will be retracted to the right. The feedback link action would shift the sliding sleeve to the right till it blocks the flow to the hydraulic cylinder. So the input motion would deliver a specified and controlled amount of output motion. In a closed-loop system, the output will be fed back to the input to improve the input. This type of servo valves are used for the hydraulic steering system of automobiles
Electrohydraulic servo valves
A hydraulic servo valve is a servo with either a flapper nozzle or jet pipe and they are used to position the servo. The servo valves are used when accurate positioning is required. The position control is achieved by a closed-loop control system as explained above. The closed-loop control system consists of a command sensor, feedback sensor, digital or analog controller, and the servo valve. We can use this valve to control the hydraulic actuators or hydraulic motors. The major components in a servo valve are a torque motor, flapper nozzle, jet pipe, and one or more spools.
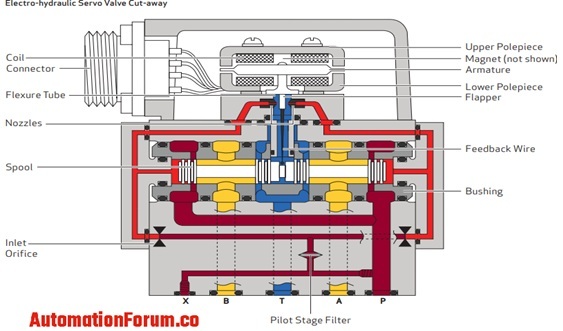
A low voltage is used to control the servo valve, the voltage will be sent to the amplifier and this amplifier would provide the power to change the position of the valve. The valve would give the proper amount of fluid power to the actuator for its movement. There would be a feedback transducer on the actuator and this would send an electrical signal to the amplifier in order to strengthen the voltage to the servo valve. In this way, the servo valve can vary the force, velocity, and position.
These valves are mostly used for applications that need variable and accurate flow. These valves operate by transforming a changing analog or digital input signal into a smooth set of movements in a hydraulic cylinder.
What are the types of servo valve control system?
Servo position control system
So in this type, the amplifier would receive an input command then this amplifier would send output to the valve and energizes the valve coil and thus it would actuate the valve that does the fluid flow to the actuator. If the fluid motor is being controlled then the position transducer would send a signal to the amplifier. The amplifier compares the position of the actuator to the valve of the command input. So if there is any difference between the two values an error signal is produced and according to this signal the input signal is changed and the actuator will be placed as per the amplifier’s input signal.
Servo force control system
We can consider the force or torque as the function of the load on the actuator, servo valve can control the force in a circuit. The pressure transducer can sense the force. The servo amplifier would check the feedback signal from the sensor and this amplifier controls the valve and the valve is shifted with the help of a velocity circuit to acquire the desired pressure.
Servo velocity control system
This type of control system is used with motors and also with cylinders. The amplifier would calculate the velocity so that an error signal can be sent. So if the error is zero in this circuit the spool will be shifted metering the flow to and from the actuator.
What are the advantages and disadvantages of servo valve?
Advantages
- These valves are capable to provide precise control of the pressure, velocity, and position
- These valves are able to govern a very large output power with a small input power
- High accuracy
- It can move large masses in a short time and this can be done against the varying forces and the servo valve would do this accurately
Disadvantages
- These valves are really expensive due to their high accuracy requirements
- The operation of these valves are expensive too because of the filtering of the fluid
What are the applications of servo valves?
- It is used in the hydraulic steering system in the automobiles
- Earthmoving vehicles
- Articulated arm devices
- Cargo handling cranes
- Lift truck
- Logging equipment
- Farm machinery steel mill controls
- Utility constructions
- Servicing vehicles