- Types of Split-Range Control System
- What is Complementary Split-Range Control ?
- Example Process: Temperature Control in Heat Exchanger Application
- Control Valves Operation in Complementary Split-Range Control
- Function of Complementary Split-Range Control
- Why Complementary Split-Range Control?
- Process Advantages of Complementary Split-Range Control
- What is Exclusive Split-Range Control ?
- Exclusive Split-Range Control for pH Adjustment Example
- Working Principle of Exclusive Split-Range Control in pH Neutralization
- Control Valves Operation in Exclusive Split-Range Control and Process Flow
- Example Process: Wastewater pH Neutralization
- Process Function in Exclusive Split-Range Control
- Benefits of Exclusive Split-Range Control in pH Adjustment
- What is Progressive Split-Range Control ?
- Progressive Split-Range Control for Gas Flow in a Combustion System
- Working Principle of Progressive Split-Range Control for Gas Flow in a Combustion System
- Control Valve Operation Progressive Split-Range Control
- Example Process: Combustion System Pressure Control
- Why Progressive Split-Range Control ?
- Key Benefits of Progressive Split-Range Control in Combustion Systems
- Comparison of Split-Range Control Types
- FAQ on Split Range Control Systems
- What is a split range control system?
- What does “split by range” mean?
- What is the difference between ratio control and split range control?
- How does cascade control differ from split range control?
In process industries, split-range control is a useful method where a single controller regulates several control valves. Control flexibility and efficiency can be improved by addressing particular process requirements by dividing the controller’s output range among several valves.
Types of Split-Range Control System
Split-range control is a crucial method in industrial automation that allows several control valves to be efficiently operated by a single controller.
Complementary split-range control
For accurate mixing or thermal balance, complementary split-range control makes sure that two streams are adjusted proportionately.
Exclusive split-range control
Exclusive split-range control allows independent streams to be controlled sequentially by avoiding overlap.
Progressive split-range control
Capacity is increased by progressive split-range control, which combines scalability and accuracy.
Complementary, Exclusive, and Progressive Split-Range Control will be discussed in the next part along with actual examples, thorough explanations, and practical applications of each type.
What is Complementary Split-Range Control ?
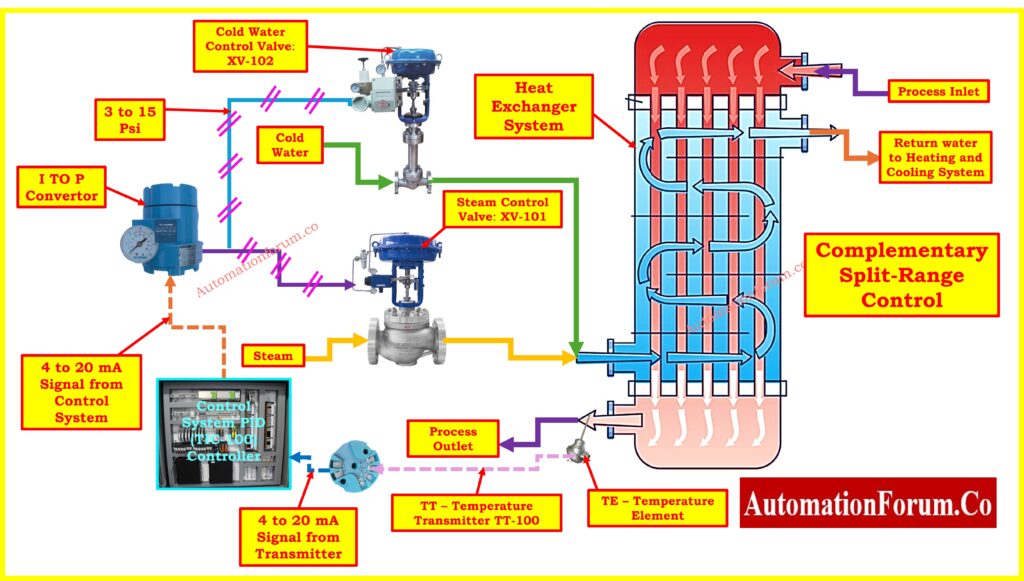
Complementary split-range control is a versatile method that ensures seamless and proportional regulation of two opposing media. The operation depends on complementary actions of two valves. one valve progressively opens as the other closes and achieving precise control of a key process parameter, such as temperature, pressure, or flow rate.
Example Process: Temperature Control in Heat Exchanger Application
Process Overview
In a steam-to-water heat exchanger system, precise temperature control is achieved by regulating the flow of steam and cold water into the heat exchanger. The system uses two control valves: one for steam (XV-101) and one for cold water (XV-102). The steam valve is Air-To-Open (ATO), and the cold water valve is Air-To-Close (ATC).
Click here for Fail Open Vs Fail Close valves
Instrumentation Tags
- Controller: Temperature Controller (TIC-100) monitors and regulates the outlet water temperature.
- Temperature Transmitter: (TT-100) measures the water outlet temperature and provides feedback to the controller.
- Steam Control Valve: (XV-101) regulates the flow of heating steam; it is configured as Air-To-Open (ATO).
- Cold Water Control Valve: (XV-102) regulates the flow of cooling water; it is configured as Air-To-Close (ATC).
Control Valves Operation in Complementary Split-Range Control
Controller Output (%) | I/P Output (PSI) | Steam Valve (XV-101) Position | Cold Water Valve (XV-102) Position |
0 | 3 | Fully Closed | Fully Open |
25 | 6 | 25% Open | 75% Open |
50 | 9 | 50% Open | 50% Open |
75 | 12 | 75% Open | 25% Open |
100 | 15 | Fully Open | Fully Closed |
Function of Complementary Split-Range Control
At 0% Controller Output:
- Cold Water Flow (Cooling Only): The cold water valve (XV-102) is fully open, delivering maximum cooling water to the heat exchanger.
- Steam Flow (No Heating): The steam valve (XV-101) remains fully closed, ensuring no heat is added.
As the Controller Output Increases:
- The controller signals both valves to move proportionally.
- Steam Valve Opening: The steam valve begins to open, allowing heating steam to enter the exchanger.
- Cold Water Valve Closing: Simultaneously, the cold water valve starts to close, reducing cooling water flow.
At 100% Controller Output:
- Maximum Heating (Steam Only): The steam valve is fully open, delivering maximum heat to the exchanger.
- No Cooling: The cold water valve is fully closed, ensuring no cooling water is introduced
This setup ensures a balanced flow between heating and cooling media, maintaining precise temperature control.
Why Complementary Split-Range Control?
Process Advantages of Complementary Split-Range Control
- The precise control provided by complementary split-range control ensures a steady and constant process temperature since both valves react proportionately to the controller output.
- By decreasing energy waste and lowering the simultaneous usage of heating and cooling, it improves energy efficiency.
- By avoiding thermal shock or abrupt temperature changes in the heat exchanger, the method offers operational stability.
- It also provides the ability to support a broad variety of setpoints for different operational requirements.
What is Exclusive Split-Range Control ?
Exclusive split-range control means that only one valve is in use at once. An “either-or” flow path is produced when both valves are closed at the middle of the controller output.
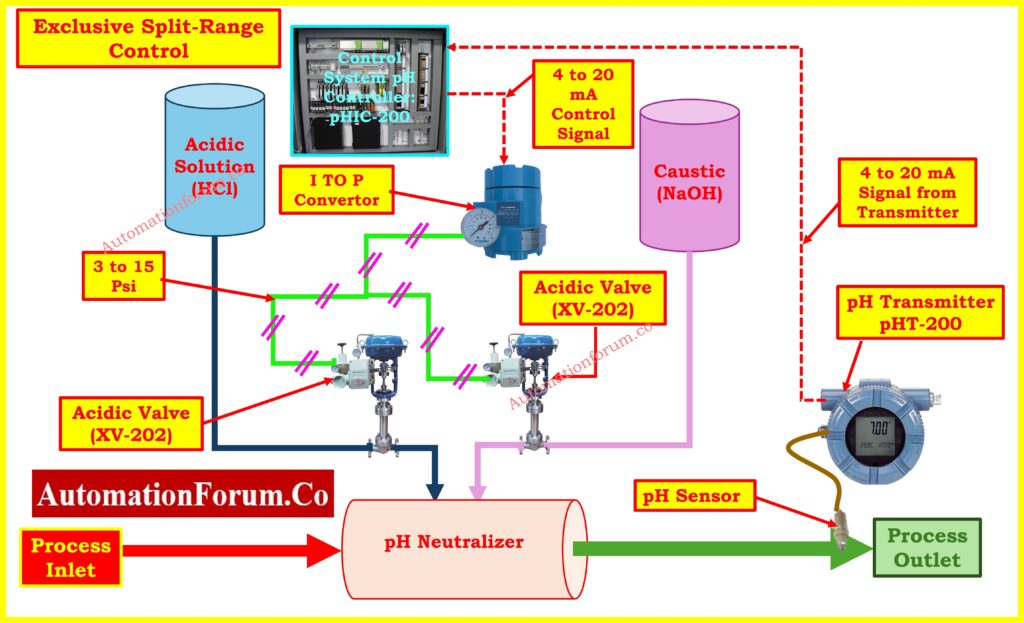
Exclusive Split-Range Control for pH Adjustment Example
The pH of an effluent stream (such as wastewater) is the process output in this case. The intention is to keep the pH between 6.5 and 7.5, which is a neutral zone. Following two compounds are utilized to accomplish this:
Caustic (NaOH): For neutralizing acidic effluent (pH < 6.5)
Acidic Solution (HCl): For neutralizing alkaline effluent (pH > 7.5)
Working Principle of Exclusive Split-Range Control in pH Neutralization
Exclusive Split-Range Control Action (FIC-200)
The pH sensor is responsible for determining the pH of the effluent and then transmitting the results to the controller. The controller adjusts its output (0–100%) based on the deviation(error) from the setpoint.
The output signal determines which valve operates:
- Caustic Valve (XV-201): Active at low controller outputs (0–50%) for NaOH dosing.
- Acidic Valve (XV-202): Active at high controller outputs (50–100%) for HCl dosing.
Control Valves Operation in Exclusive Split-Range Control and Process Flow
Controller Output (%) | I/P Output (PSI) | Caustic Valve (XV-201) | Acidic Valve (XV-202) | Result |
0 | 3 | Fully Open | Fully Closed | Maximum NaOH flow; pH rises. |
25 | 6 | Partially Open | Fully Closed | Moderate NaOH flow; pH rises. |
50 | 9 | Fully Closed | Fully Closed | Neutral; no flow. |
75 | 12 | Fully Closed | Partially Open | Moderate HCl flow; pH drops. |
100 | 15 | Fully Closed | Fully Open | Maximum HCl flow; pH drops. |
Click here for Split Range Calculator – Control system
Example Process: Wastewater pH Neutralization
Influent Characteristics:
- Influent pH may fluctuate due to upstream industrial processes (e.g., acidic from dyeing, alkaline from cleaning).
- pH range: 5.5–9.0 (outside acceptable discharge limits).
Effluent Treatment Aim
- Maintain pH in the range of 6.5–7.5 before discharge to meet environmental regulations.
Instrumentation Tags
- pH Controller: pHIC-200
- pH Sensor: pHT-200
- NaOH Valve: XV-201
- HCl Valve: XV-202
Process Function in Exclusive Split-Range Control
Low pH (Acidic Effluent):
- The controller output falls within 0–50%, activating the caustic valve (XV-201).
- Dosing with NaOH brings the pH up to the neutral range.
High pH (Alkaline Effluent):
- The acidic valve (XV-202) is activated when the controller output increases by 50–100%.
- Dosing with HCl brings the pH down to the neutral range..
Neutral pH (Setpoint):
- When pH is within the intended range, both valves stay closed at 50% controller output, preventing dosing.
Benefits of Exclusive Split-Range Control in pH Adjustment
- Ensures that just the necessary chemical (acid or caustic) is utilized based on pH variations, reducing chemical waste.
- Prevents overlapping NaOH and HCl processes, hence avoiding counterproductive chemical reactions.
- Allows for a smooth transition between acid and caustic dosage without requiring operator intervention.
- Reduces the likelihood of excessive pH corrections, which could impact downstream processes or the environment.
What is Progressive Split-Range Control ?
Progressive split-range control increases flow control capacity by employing two valves with staggered operating ranges. The smaller valve opens first, then the bigger valve, ensuring precision at low flows and scalability at huge flows.
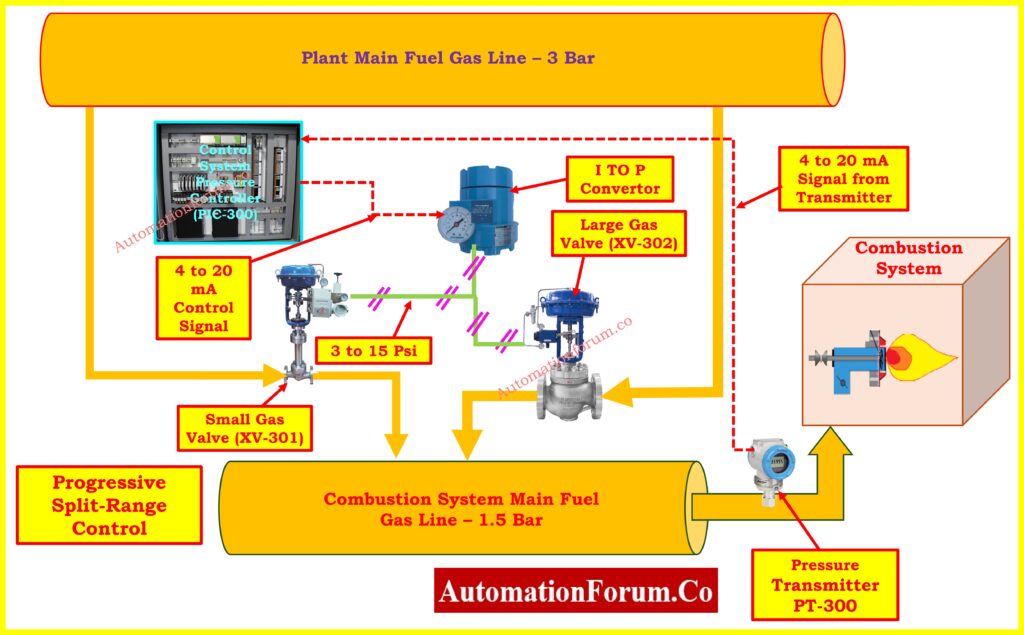
Progressive Split-Range Control for Gas Flow in a Combustion System
Process Parameter:
- Here, pressure in the gas supply line to the combustion chamber is the controllable process parameter.
- The controller maintains the appropriate gas pressure to provide safe and efficient combustion.
Working Principle of Progressive Split-Range Control for Gas Flow in a Combustion System
- Controller (PIC-300): Monitors the combustion chamber gas line pressure using a transmitter (PT-300).
- Small Valve (XV-301): Designed for fine control at low flow rates, providing accuracy when the demand is minimal.
- Large Valve (XV-302): Handles higher flow demands, operating in tandem with the small valve at increased pressures.
Control Valve Operation Progressive Split-Range Control
Controller Output (%) | I/P Output (PSI) | Small Gas Valve (XV-301) | Large Gas Valve (XV-302) | Result |
0 | 3 | Fully Closed | Fully Closed | No gas flow; system idle. |
25 | 6 | Half Open | Fully Closed | Precise, low gas flow. |
50 | 9 | Fully Open | Fully Closed | Moderate gas flow via XV-301. |
75 | 12 | Fully Open | Half Open | Increased gas flow. |
100 | 15 | Fully Open | Fully Open | Maximum gas flow. |
Example Process: Combustion System Pressure Control
Process Overview
- A combustion chamber (e.g., in a boiler or furnace) requires precise gas flow control to maintain the desired pressure for stable and efficient combustion.
- Gas demand fluctuates depending on the system’s operational load (e.g., startup vs. full load).
Operation Details
- At low demand (startup): The small valve (XV-301) opens first to provide precise flow control, ensuring smooth ignition and stable low-pressure conditions.
- At moderate demand: The small valve reaches full open, and the large valve (XV-302) begins to open, gradually increasing gas flow.
- At high demand (full load): Both valves are fully open, delivering the maximum flow needed to meet the combustion process’s pressure requirements.
- Pressure Controller: PIC-300
- Pressure Transmitter: PT-300
- Small Valve: XV-301
- Large Valve: XV-302
The pressure in the combustion system is directly tied to fuel supply and efficient burner operation.
Maintaining a stable pressure ensures consistent heat release, preventing:
- Under-pressure, which may lead to incomplete combustion or flame instability.
- Over-pressure, which could damage equipment or lead to unsafe operating conditions.
Why Progressive Split-Range Control ?
- Precise Low-Flow Control: The smaller valve provides accuracy during periods of low demand, such as startup or low-load operations.
- High-Flow Scalability: The larger valve complements the small valve when demand increases, avoiding the limitations of a single valve.
- Smooth Transition: The staggered operation of the valves ensures stable pressure control across the entire operating range.
Key Benefits of Progressive Split-Range Control in Combustion Systems
- The system adjusts gas flow precisely to match the combustion demand.
- Avoids over-supplying gas during low-demand conditions.
- Maintains stable pressure, preventing dangerous fluctuations.
Click here for Control Valves in Process Industries: A Collection of In-Depth Articles
Comparison of Split-Range Control Types
In industrial automation, Complementary, Exclusive, and Progressive split-range control types are crucial methods for process optimization. Depending on the process’s characteristics, control accuracy, and operational needs, each approach is appropriate for a particular application. A comparison table outlining the variations and uses of these control modes can be referred below.
Aspect | Complementary Split-Range Control | Exclusive Split-Range Control | Progressive Split-Range Control |
Primary Function | Balances two opposing media proportionally for precise control. | Operates one valve at a time, avoiding overlap, for sequential control. | Expands flow capacity by staggering valve operation for precision and scalability. |
Controller Output Range | Shared proportionally between two valves (e.g., 0–50% for one valve and 50–100% for the other). | Exclusive ranges for each valve (e.g., 0–50% for one valve and 50–100% for the other). | Staggered ranges for small and large valves, enabling finer control at low flows and scalability at higher flows. |
Valve Operation | One valve opens while the other closes in a complementary manner. | Only one valve is active at any time, with both closed at the midpoint. | Small valve operates first; the large valve engages later as demand increases. |
Typical Applications | Heat exchangers, mixing processes, or any system requiring balanced media control. | pH neutralization, chemical dosing, or any process requiring distinct sequential control. | Combustion systems, gas flow control, or applications needing precision at low flow and scalability at high flow. |
Advantages | Energy-efficient, prevents thermal shock, and offers smooth transitions. | Minimizes chemical waste, avoids counterproductive reactions, and ensures seamless transitions. | Provides precise control at low flows, accommodates high demands, and ensures smooth transitions across operating ranges. |
Disadvantages | Requires precise valve calibration; not suitable for mutually exclusive operations. | Limited flexibility if overlapping control is needed. | More complex setup; may involve higher initial costs due to additional valves and instrumentation. |
Example Scenario | Steam-to-water heat exchanger temperature control. | Wastewater pH adjustment using caustic and acidic solutions. | Combustion chamber gas flow and pressure control. |
Key Consideration | Ensure valves are configured with opposite fail-safe actions (e.g., ATO and ATC). | Avoid overlapping operations to prevent chemical wastage or process instability. | Proper sizing of small and large valves for optimal performance and scalability. |
FAQ on Split Range Control Systems
What is a split range control system?
A split range control system uses two or more control valves that operate over different portions of a controller’s output signal. At one end of the signal range, one valve is fully open while the other is fully closed, and vice versa at the opposite end. This setup allows seamless operation across the entire signal range by splitting control between the valves.
What does “split by range” mean?
The split-by-range concept divides the output signal from a PID controller into distinct segments. Each segment corresponds to a specific final control element (FCE). For example, part of the controller’s output might actuate one valve, while another portion governs a secondary valve, enabling coordinated control over different parts of the process.
What is the difference between ratio control and split range control?
Ratio control is primarily a feed-forward control strategy that ensures two variables maintain a fixed proportion. Split range control, by contrast, is a method of assigning different portions of the controller’s output signal to operate multiple control valves, providing precise manipulation of the process input.
How does cascade control differ from split range control?
Cascade control minimizes the impact of disturbances by linking two controllers, where one acts as the master and the other as the slave. In contrast, split range control manages multivariable processes by dividing the controller output among multiple control valves. Cascade control focuses on disturbance rejection, while split range control enables flexible valve operation across a signal range.