- Understanding Pressure Control Valves
- Why are Pressure Control Valves Used?
- Functions of Pressure Control Valves
- Types of Pressure Control Valves and their Operation
- Adjusting and Installing Pressure Control Valves
- Rupture Discs: Enhancing Pressure Control
- Applications of Pressure Control Valves
- Conclusion
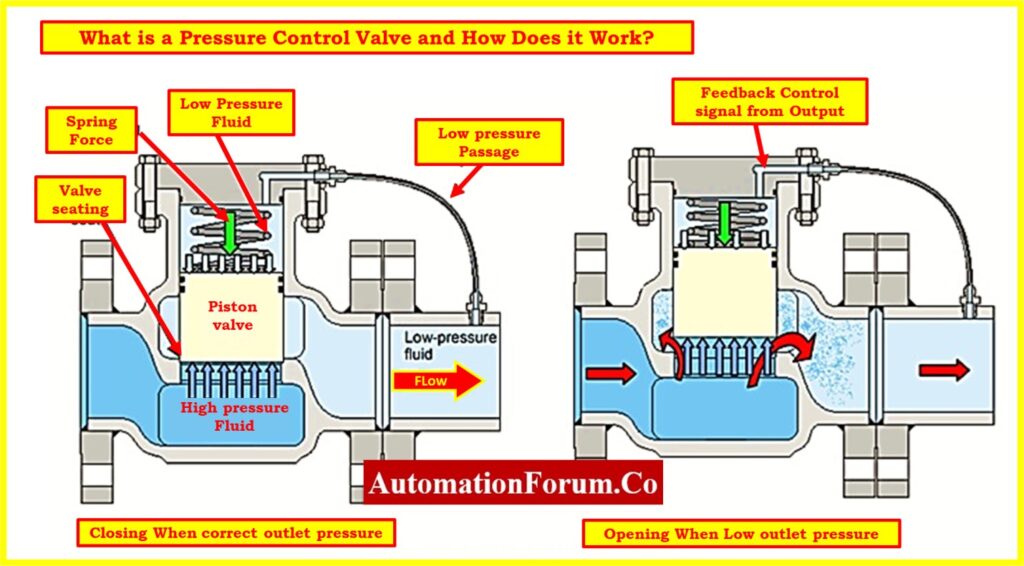
In this comprehensive evaluation, we’ll look into the complexities of pressure control valves, their operating principles, types, applications, and the critical components of adjustment and installation.
Understanding Pressure Control Valves
Definition and Purpose
- An essential component of hydraulic and fluid systems, a pressure control valve guards against system damage brought on by high pressure. It does this by means of control and pressure release systems.
- In the end, it protects industrial processes from overpressure situations that can result in system failure, ensuring lifespan and effectiveness.
Working Principle
- The pressure within a valve is caused by a restriction in the flow of fluid. The pressure control valve operates to keep the pressure within the permitted limits while fluid moves through the system. Excessive pressure can cause harm, downtime, and higher operating expenses if it is not controlled.
- Pressure control valves work by controlling the flow of fluid, setting a maximum pressure limit, and ensuring a safe, controlled environment.
Why are Pressure Control Valves Used?
Pressure control valves serve a multitude of critical functions in industrial applications:
Limiting Maximum Pressure
- The main purpose is to protect a system from potential damage by controlling the maximum pressure that is permitted in the system.
- A pressure control valve makes ensuring the ‘temperature’ of fluid systems stays within a safe range, just like a thermostat keeps your house at a comfortable temperature.
Backpressure Adjustment
- By allowing backpressure to be adjusted, these valves guarantee that fluid flow stays within intended bounds.
- Pressure control valves allow operators to modify the ‘volume’ of fluid flow. It’s like carefully adjusting the volume on your preferred playlist.
Signaling High Pressure
- As watchful sentinels, pressure control valves notify operators of any problems by providing signals when the predetermined pressure is achieved.
- Similar to a traffic signal going red, pressure control valves provide an alert when possible issues arise, indicating when to “stop” and take action.
Overpressure Protection
- They are critical in preventing equipment failure by protecting pumps and systems from overpressure conditions.
- Pressure control valves, like a circuit breaker, protect systems from hydraulic ‘overloads.’
Pump Unloading
- Pressure control valves can unload a pump when necessary, providing flexibility in system operation.
- Think of it as a relief valve for a pump, allowing it to take a breather when the workload becomes too much, just like we all need a break.
Setting Entry Pressure
- These valves regulate the amount of oil that enters a hydraulic circuit, providing for precise control.
- It’s similar to adjusting the water pressure in a shower—pressure control valves guarantee that the fluid enters the circuit at just the proper level.
Functions of Pressure Control Valves
Pressure control valves boast diverse functions tailored to specific system needs:
Pressure Reduction
- Reducing valves decrease the pressure between two components of a process, ensuring that it runs properly.
- Similarly to how a dimmer switch controls the brightness of a room, lowering valves fine-tune the ‘brightness’ of pressure in a fluid system.
Load Holding
- These valves have the ability to hold loads in place, preventing uncontrolled movement.
- Consider a brake holding a car motionless on a slope—load holding valves keep equipment in place.
Sequential Control
- Pressure control valves enable controlled and sequential operations in applications that need a sequence of activities.
- Sequential control valves ensure that each stage in the industrial process is precise and well-timed, much like choreographing a dance routine.
System Pressure Limitation
- Pressure control valves limit the overall pressure within a system to prevent potential damage.
- Similar to a speed limiter on a vehicle, these valves ensure the system doesn’t ‘speed’ beyond its safe limits.
Sectional Pressure Control
- They optimize performance by controlling the pressure in certain portions of a hydraulic or fluid circuit.
- It’s similar to zoning your home’s heating system—sectional pressure control valves ensure each area receives the appropriate quantity of’heat.’
Sequence Motion
- Pressure control valves provide precise control and coordination for applications that require a specified sequence of operations.
- Sequence motion valves, like a conductor, ensure each component in a system plays its part in synchronization.
Actuator Sequence Control
- These valves aid in the sequencing of actuator movements in systems with several actuators for effective operation.
- Think of it as a traffic cop directing the flow of vehicles—an actuator sequence control valve ensures a smooth ‘traffic’ of movements.
Restrained Movement Control
- In situations where movement must be controlled and restricted, these valves provide the essential regulation.
- Similar to using a leash for a pet, restrained movement control valves ensure movements are controlled and within limits.
Reduced Pressure Control
- For applications requiring a reduction in pressure, these valves play a crucial role in achieving the desired level.
- Just like adjusting the pressure on a spray nozzle, reduced pressure control valves customize the ‘spray’ of fluid in a system.
Pump Unloading Control
- They contribute to the effective unloading of pumps, preventing unnecessary strain on the system.
- It’s similar to a car’s automatic clutch, allowing the pump to ‘disengage’ when the workload is light.
Types of Pressure Control Valves and their Operation
Pressure Reducing Valve (Pressure Regulators)
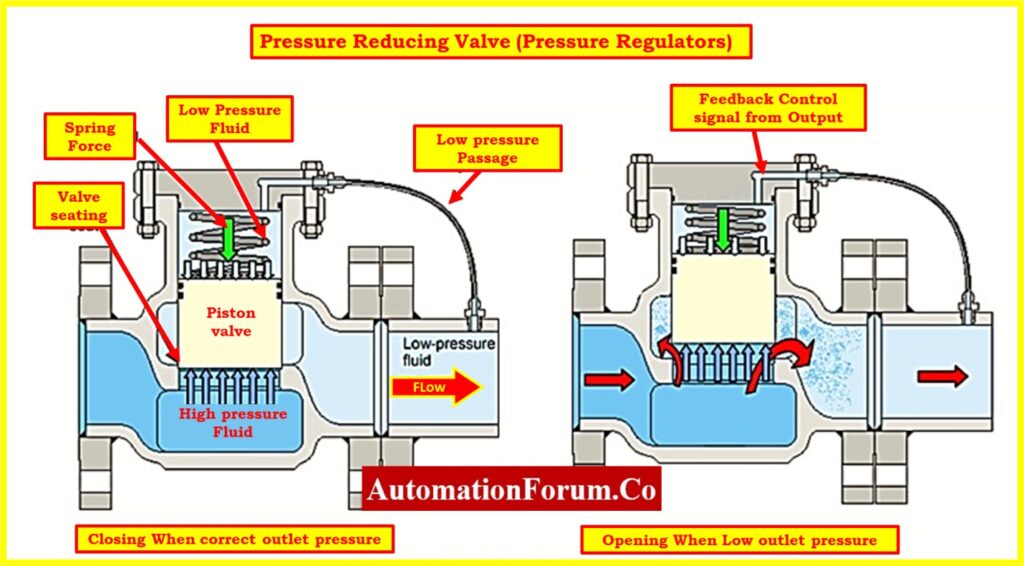
- The valve’s operation relies on maintaining a balance between the fluid pressures above and below a piston, along with the force exerted by a spring.
- If the low-pressure fluid and spring force exceed the high-pressure supply, the piston closes the valve. Conversely, if the force from the reduced low-pressure fluid, combined with the spring force, is less than the high-pressure supply, the piston opens the valve.
- To ensure pressure control, the valve continually alternates between opening and closing. Adjusting the outlet pressure is achievable by using a stronger or weaker spring, or by employing an adjusting screw to modify the spring force.
- In some instances, multiple pistons and diaphragms are employed in reducing valves to enhance their performance.
Pressure Relief Valve
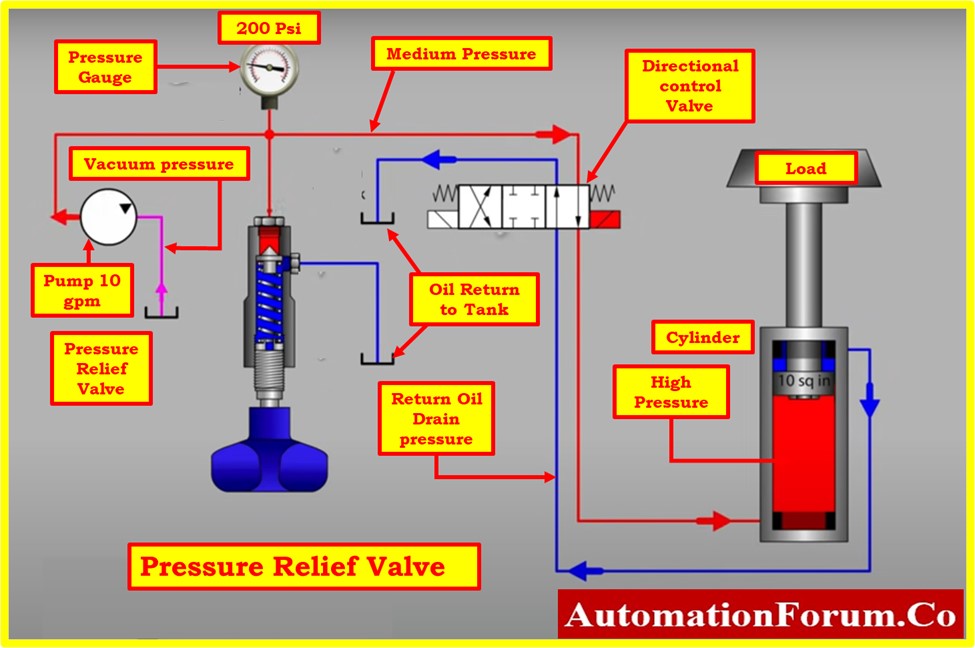
- Under normal conditions, pressure relief valves remain closed, only opening when the fluid pressure exceeds the setpoint. They keep systems safe by releasing excess pressure and then closing to return to normal levels.
- These valves are used so that the overpressure of the liquid can be relieved. The operation of the pressure relief valve under normal conditions, like when the system pressure is normal the pressure relief valve will stay close with the help of a spring.
- The valve would open when the pressure of the fluid pushes the spring. The force or pressure required to open the valve is setpoint pressure. The setpoint pressure is the maximum normal operating pressure of the liquid.
- When the fluid pressure is more than the setpoint pressure then the valve will open slowly and the pressure is brought back to its normal level. Spring force is changed with the help of adjustment screw in case of different set point pressure. Think of it as a safety valve on a kettle, releasing excess pressure to prevent a catastrophic ‘boil-over.’
Pressure Safety Valve
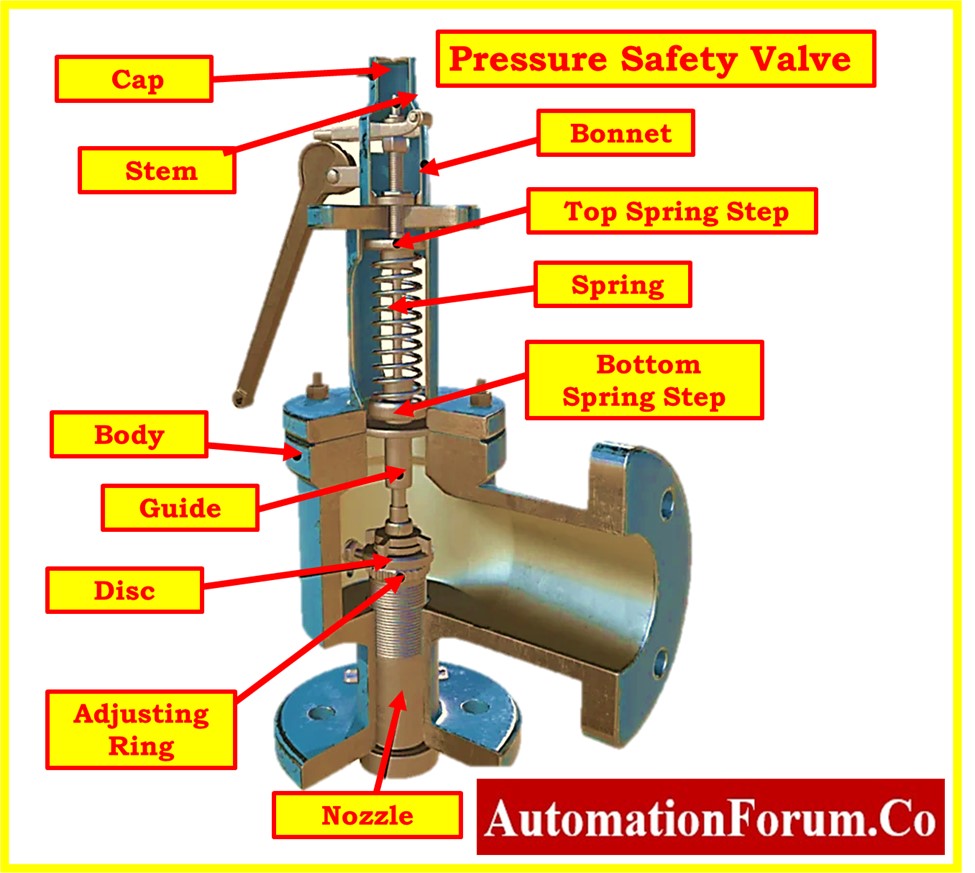
- These valves can relive the overpressure of gasses and vapors, in this valve the setpoint is greater than the maximum normal operating pressure of the process fluid, but it is less than the maximum safe operating pressure of the equipment.
- If the fluid pressure is more than the setpoint pressure then the valve opens fully. So this can decrease the overpressure very fast and after that, the valve will close.
- The pressure at which the valve closes after the reducing process is less than the setpoint pressure. The difference between the opening and closing pressure is called blow-down.
- Most of the pressure control valves have their outlet diameter bigger than the inlet so that pressure can be reduced.
Adjusting and Installing Pressure Control Valves
Adjustment Process
- The spring force that affects the opening and closing speed of a pressure control valve is adjusted. For adjustment, some valves make use of numerous pistons or diaphragms.
- The spring force can be adjusted by changing the spring or using an adjustable screw, giving the valve precise control over how it functions.
Installation Guidelines
Proper installation is crucial for the effective performance of pressure control valves:
- Check for Protective Elements: Before installing, make sure all protective plugs and wrapping are in place.
- Inspect Fittings: Before installing the valve, ensure that all fittings and plugs have been removed.
- Examine the Seals: Make that the seals that protect the valve setting are intact and in place.
- Verify the information: To avoid conflicts, compare the information on the nameplate and identification tags to the work order.
Rupture Discs: Enhancing Pressure Control
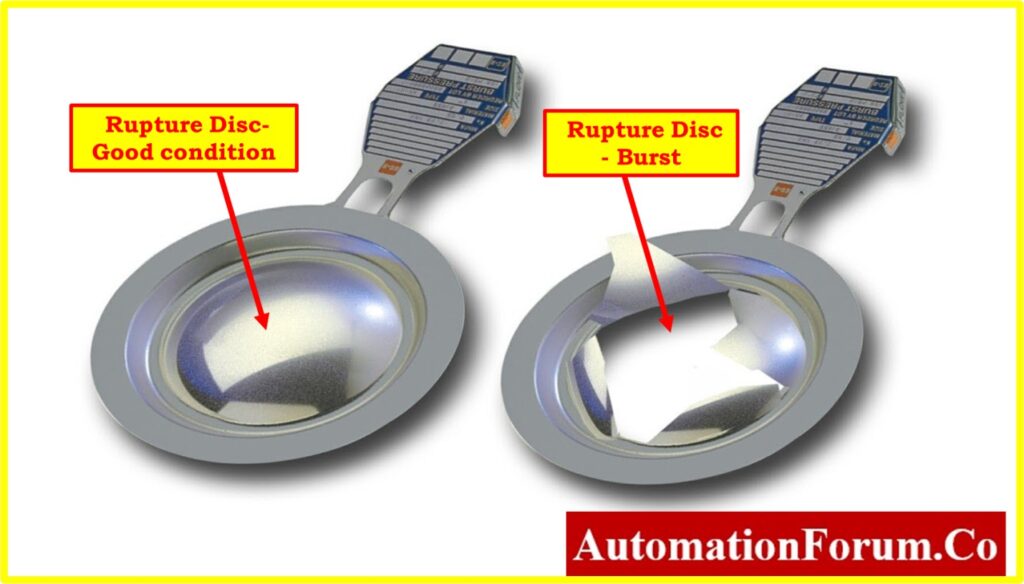
- Rupture discs, also known as bursting discs, play an important role in improving pressure control in specific industries by functioning in tandem with typical pressure control valves.
- In contrast to valves, rupture discs are static pressure safety devices with no moving elements that activate only when the pressure exceeds a predetermined threshold.
- When the system is subjected to extreme pressure, the rupture disc responds quickly by breaking open. This rupture, which is free of moving parts, provides for a rapid flow of fluid, quickly relieving the increased pressure.
- Rupture discs are especially useful in conditions with heavily contaminated fluids because they provide a reliable defense against probable valve malfunction caused by debris.
- The addition of rupture discs to pressure control valves creates a powerful combination for total pressure management. While control valves allow for real-time modifications, rupture discs act as an immediate fail-safe mechanism, allowing for a quick response to sudden pressure spikes. Their benefits include quick response, minimal moving parts for increased reliability, contaminant resistance, and controlled unidirectional fluid flow upon rupture.
- The collaboration of rupture discs and pressure control valves, in essence, creates a layered approach to pressure safety. This synergy not only reduces risks but also strengthens the resilience of industrial systems, which is especially important in demanding settings when immediate pressure relief is required.
Applications of Pressure Control Valves
Pressure control valves find applications across various industries:
- Nuclear Power Plants: Critical for controlling fluid flow and pressure in nuclear power systems.
- Hydraulic Power Plants: Essential components for maintaining optimal pressure levels in hydraulic systems.
- Oil Industry: Used in oil exploration, extraction, and refining processes for pressure regulation.
- Gas, Steam, and Water Systems: Integral for controlling pressure in these systems.
- Boiler Houses and Distribution Mains: Employed to ensure safe and efficient operation in boiler houses and distribution networks.
Conclusion
Pressure control valves act as industrial guardians, preserving the delicate balance between optimal pressure and potential damage. Their diverse functions, types, and applications make them integral across various industries. Understanding their principles, precise adjustment, and meticulous installation are crucial for optimal performance and industrial safety. Whether in nuclear power plants, hydraulic systems, or the oil industry, these valves play a crucial role in maintaining equilibrium.
Click this link to know more about the Control valves.
Click this link to know more about the Different types of valves.