A magnetic proximity sensor is a non-contact proximity sensor and it can be used to detect magnetic objects. This type of proximity sensor is also called reed contacts. This would use the magnetic field distortion for its operation, in case if a ferromagnetic material comes in the range of this sensor then the magnetic field would vary and a signal will be given to the sensor. The magnetic proximity sensor would use inductance, hall-effect principles, variable reluctance, or magneto resistive technology to detect the object. The operating range of the magnetic proximity sensor is good. The magnetic field can pass through many non-magnetic materials, so the switching process can also be done without the need for direct exposure to the target object. With the help of a magnetic conductor, the magnetic field can be transmitted over long distances, and due to this, the signal can be carried away from high-temperature areas. This type of sensor has no electrical noise effect and it can operate on AC or DC. This sensing distance of this device would vary due to certain factors such as temperature, sensing object, surrounding object,s and also the mounting distance from the sensor.
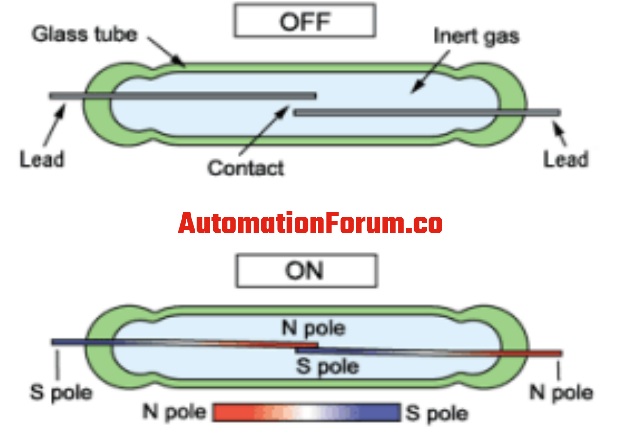
The magnetic proximity sensors’ body style could be rectangular, limit switch, barrel, slot, or ring. The barrel body type would be in a cylindrical shape and they could be threaded. The limit switch would be similar to the contact limit switch, in this the sensor is separated from the switching mechanism and it would give the detection signal. In the rectangular body type, it would have a block-shaped sensor. The slot type sensor is used to detect the presence of a vane when it passes through a sensing slot. The ring-shaped type is a donut-shaped sensor in which the object passes through the center of the ring.
- What is an optical proximity sensor?
- What is a capacitive proximity sensor?
- What is an inductive proximity sensor?
- What is an encoder and what are its types
- What are sensors on a robot and why are sensors important to robots
- Tachometer: Rotation measurement Techniques-Magnetic and Optical method
What are the types of magnetic position sensor?
- Reed switch
- Magnetostrictive sensor
- Magnetoresistive sensor
- Inductive magnetic proximity sensor
- Hall effect sensor
- LVDT
- RVDT
Reed switch
These sensors are actuated by the presence of a permanent magnet, and their operating principle is according to the use of the reed contact. The reed contact would have two low reluctance ferromagnetic leads which are enclosed in glass bulbs that contain inert gas. The reeds would get attracted in the presence of a magnetic field because of the magnetic induction and this process would make an electrical contact. In the reed switch, the contacts are open normally and it would close if a magnetic field is present. The size and type of the magnet that is needed would be according to the type of reed switch and how it is built. The magnet and switch distance is really important if the distance between the magnet and the switch is wide then a strong magnet is required to interact with the switch.
While installing a reed switch we must make sure that there are no interfacing magnetic fields near the sensor. So during this case, we must make sure that the proximity sensor must be shielded according to this.
Types of reed switch
There are two types of the reed switch and that is a dry reed switch and mercury wetted reed switch. In a dry reed switch, the ferromagnetic contact blades are sealed in a glass container with inert gas. While in the mercury wetted type the mercury is the contact material for an electrical circuit, mercury to mercury.
What are the advantages of reed switch
The contacts are not affected by dust, corrosion, and oxidization because of the glass bulb and the inerted-gas. The maintenance of this sensor is really less, this switch would provide many electrical and mechanical characteristics together with various output function. The operation of this device is really easy and it is reliable too. The operating distance of this switch is good.
Magnetostrictive sensor
This type of sensor is composed of coils, a magneto-elastic core, and a sensing shaft. In this sensor, the change in the position of the sensing shaft would produce stress in the sensitive core. The core materials permeability would vary with stress, and thus it would affect the inductance of the winding wound around the core, the inductance is the function of the shaft position.
Magneto-resistive sensor
If the material is said to have magnetoresistivity then it has the ability to change its resistivity under the influence of a magnetic field. So this type of position sensor would check the magnetoresistive effect of the material under the influence of a magnetic field. So in order to detect the position, we can place the sensor to an angular or linear moving object with its complementary sensor or magnet stationary. The magnetoresistive property would occur in a ferrous material and can be applied as a thin strip to become a resistive element.
Inductive magnetic proximity sensor
This type of sensor is similar to the inductive proximity sensor, the major difference is that it has a built-in oscillator, the oscillating coil is not of a half shell core design creating a magnetic field directed onwards, but a coil with a closed shell design, an example for this is a coil with a shielded ferrite core. By using a permanent magnet the core material of the oscillator core is saturated and this would cause a vibration in the oscillator current of the proximity sensor. A trigger state evaluates the change and converts it into a defined output signal. This type of proximity sensor would only react to the magnetic fields and not to any metallic objects.
Hall effect sensor
A hall effect sensor is a non-contact position detector and the major part of this device is a permanent magnet and a hall effect sensor IC. The hall effect is the process in which there would be an interaction between the moving electric carrier and an external magnetic field. The hall sensor output is dependent upon the magnetic field, this sensor can be used to do the proximity switching, positioning, and speed detection.
The hall sensor IC can detect the change in the magnetic field when a permanent magnet comes in close proximity to it and generates an electric signal. This signal is then amplified and rectified to control the output signal of the switch.
LVDT
By using LVDT we can do accurate and reliable linear distance measurement. The ferrous core will be connected to the moving part in the equipment in order to get the position details. Position of the electrical sensor whose output is proportional to the position of a movable magnetic core and it produces a linear electrical output and it will be similar to the position of the movable ferrous core.
What are the applications of a magnetic proximity sensor?
- This sensor is used in, door and window sensor in burglar alarm
- It is widely used in panel building industries
- It is used for reliable diagnostic applications
- They are used in hostile welding conditions
- These sensors are used to determine the position of points and mechanical locking of a switch machine to make sure the safe passage of trains
- Mobile phones