1.Define Instrumentation Engineering?
Instrumentation engineering is a branch of engineering that focuses on the principles and operation of measuring instruments used in the design and configuration of automated systems in the electrical, pneumatic, and other domains.
2. What is the job of an Instrumentation Engineer?
The required tasks vary greatly depending on the domain; instrumentation engineers typically work in industries with automated processes to improve productivity, reliability, safety, optimisation, and stability. Instrumentation engineers are typically in charge of connecting sensors to recorders, transmitters, displays, or control systems. They may be in charge of designing or specifying installation, wiring, and signal conditioning. They may be in charge of system calibration, testing, and maintenance.
3.What Is the meaning of PLC?
PLC is an abbreviation for Programmable Logic Controller. It is a small, special-purpose computer that performs logic operations to control various electromechanical systems. PLCs were initially designed to perform the functions of hard-wired relays in the automotive industry.
PLCs are widely used today to automate manufacturing processes, assembly lines, and various types of industrial machinery that require ease of programming, high levels of reliability, and advanced fault diagnosis. They are designed to be tough control systems that can operate reliably in harsh industrial environments.
4.How does a PLC work?
There are four fundamental steps involved in the operation of all PLCs, which run in a continuous loop. First, the PLC processor collects data from the connected input field devices via the input modules and processes it as pre-programmed data. Following that, the processor runs the logic of the stored PLC programme. The appropriate outputs are then triggered based on the results of the programme logic execution and the pre-programmed input parameters.
Finally, the processor maintains the housing by running memory routines and internal diagnostics continuously to ensure that the memory and other hardware/software components are not damaged. It also communicates constantly with the programming device to avoid programming errors. Following this step, the processor will resume scanning the inputs, and the previous steps will be repeated indefinitely.
5. Explain process control?
Process control is an engineering mechanism that uses operational variables such as temperature, pressure, chemical content, and algorithms to continuously monitor industrial processes. It then applies all of this data to adjust variables and, finally, achieve product output specifications and objectives. Such process control systems always aim to achieve the desired quantity of a process variable, indicating that the system is in control.
6. Why is a 4-20 mA signal preferred over a 0-20 mA signal?
In a 4-20mA signal, 4 represents the minimum value and 20 represents the maximum value within the signal. With 0-20 mA, it is impossible to distinguish between the minimum field value and connection breaks. In both cases, the output will be 0mA.
In a 4-20 mA internal circuit, connection breaks of minimal value can be easily distinguished. When the value is at its lowest, a transmitter can normally output 4 mA, while when the connection is broken, it can output 0 mA.
7.What is a transmitter?
A transmitter is an electronic device that is typically mounted in the field near a sensor. The sensor (also known as a transducer) measures a physical variable such as temperature or pressure and produces a very low-level electronic signal as a result. The transmitter’s basic function is to supply the correct electrical power to turn on (or excite) the sensor, then read the low-level sensor signal, amplify it to a higher level electrical signal, and send that signal a long distance to a control or read-out device.
8. What is a “Smart” Transmitter?
A microprocessor-based transmitter is another name for a “Smart” transmitter. It is the heart of an electronic device. Smart transmitters are used in remote areas to communicate as well as for calibration. A sensor signal transmitter is a type of smart transmitter that transmits a unified standard signal such as 0/4-20mA DC, 1-5V DC, or 0-10V DC. The output control signal is a standard 4-20mA signal. A good smart transmitter is noise-insensitive genetically.
9. What are the process variables?
Flow, Pressure, Level, Temperature, and Quality are process variables.
10. What are the primary flow measurement elements?
Flow is measured using an orifice plate, a venturi tube, a pitot tube, an annubars, a flow nozzle, a weir, and a flume.
11. What are the different types of Orifice Plates and what are their applications?
Concentric, Segmental, and Eccentric orifice plates are the three types.
12. Define concentric orifice?
The concentric orifice plate is ideal for liquid, gas, and steam service. The beta ratio of an orifice plate ranges from 0.15 to 0.75 for liquids and 0.20 to 0.70 for gases and steam. The best results are obtained when the value is between 0.4 and 06.
The beta ratio is the ratio of orifice bore to internal pipe diameters.
Friction resistance to flowing fluid is often reduced by using 450 bevelled edges.
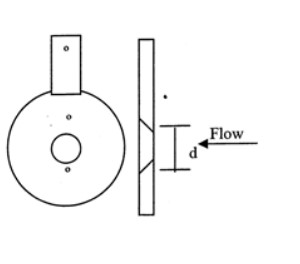
13. Explain eccentric orifice?
The eccentric orifice plate has an eccentric hole. Full for measuring solids, oil containing water, and wet steam. Eccentric plates can be fitted with either flange or vena contract taps, but the tap must be positioned at 1 800 or 900 to the eccentric opening. Eccentric orifices have the bore offset from the centre to reduce problems in solids-containing material services.
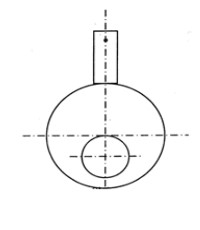
14. Define Segmental orifice?
The hole in the form segment of the segmental orifice place is used for colloidal and slurry flow measurement. The tap location should be 1800 from the centre of tangency for maximum accuracy. Segmental orifices are another type of plate that is useful for solids-containing materials.
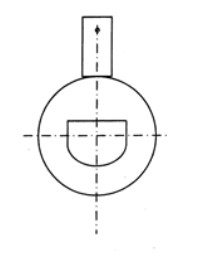
15. Edge of the Quadrant orifice?
It is widely used in Europe and is especially useful for pipe sizes less than 2 inches. For services with low Reynolds numbers ranging from 100,000 to 5,000, quadrant edge orifices produce a relatively constant coefficient of discharge.
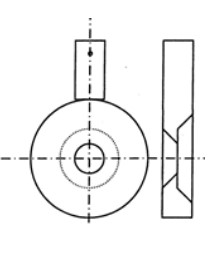
16. Difference between 2 wire, 3 wire and 4 wire transmitter?
- Power and signal are transmitted via a single common cable in a two wire transmitter.
- The data signal and power in a three-wire transmitter are always proportional to the common ground.
- Two wires are used for power supply and two separate ones for signals in a four wire transmitter.
17. What is an Actuator?
The part of a final control element in a closed-loop control system basically translates the control signal into an actionable element with the help of a control device.
18.What does an Orifice tab serve?
An orifice tab’s purpose is to indicate that the orifice plate remains in place, and the orifice diameter is usually marked on top of it. The material of an orifice plate is identified by a tag number. It also has a mark that represents the inlet of an orifice.
19. How to identify an Orifice in a Pipe Line?
An orifice tab is typically welded onto the orifice plate, which can be used to extend the line. This indicates the presence of an orifice plate.
20. How do you calibrate a DP Transmitter?
When calibrating a D.P. transmitter, the following steps must be taken.
- Set zero to transmitter.
- Static pressure test: Apply the same amount of pressure to both sides of the transmitter. Zero should not move. If it’s shifting, perform static alignment.
- Vacuum test: Apply equal vacuum pressure to both sides. The zero should not be moved.
21. How do I adjust a transmitter’s 20 psi air supply?
- Open the L.P. side of the vent to the atmosphere.
- Connect an instrument’s output to a standard test gauge. Set the zero.
- Apply the required pressure to the transmitter’s high pressure side and adjust the span.
- Re-adjust the zero if necessary.
22. What is Bernoulli’s Theorem and how does it apply?
The total energy of a liquid flowing from one point to another remains constant, according to Bernoulli’s theorem. It applies to non-compressible liquids.
23. How do you determine the high pressure side or inlet of an orifice plate in line?
The marking is always done on the HP side of an orifice tab, which indicates the HP side.
24. What do you mean by self-regulation?
For a sustained change in input, self-regulation means that the output moves from one steady state to another steady state. This means that as some input variable changes, the output variable rises until it reaches a steady state where inflow = outflow. Through this method, the process uses a specific value of the controlled variable for nominal load with no control operations.
25. Name the various test inputs.
Step, Ramp, Impulse, Sinusoidal, and Pulse inputs are all examples of step inputs.
26. Define interacting systems?
The load changes within the first process and affects the second process in an interacting system, and vice versa. An interacting system is formed when both are linked in a series. For example, two level tanks are linked in series.
27. What is a thermocouple?
It is a two-material junction that converts heat into electrical energy. A temperature difference can produce a voltage proportional to the heat when a pair of wires made of two completely different metals are joined at one end.
28. What are the benefits of using a thermocouple?
It has a tough build and can withstand temperatures ranging from -270 to -2700 degrees Celsius. This couple is inexpensive and easily replicated.
29. How does a thermocouple measure temperature?
A thermocouple is an electrical device made up of two electrical conductors that form electrical junctions at different temperatures. Due to a thermoelectric effect, it can generate temperature-dependent voltage, which can be interpreted to measure temperature.
30. What are the two features of first order process modelling?
The steeper the initial response of the system, the smaller the value of the time constant. A first order lag process self-regulates the ultimate value of the response = Kp or the process’s steady state gain for a unit step change in the input.
31. Define a controller’s function.
A controller is an instrument that is used to control a process variable in order to measure it. Its job is to continuously monitor the error signal and provide a corrective output to the final control element.
32. Define the term “process control.”
It is a design mechanism that specifies how much the manipulated variable should change in order to remain under control. It continuously monitors the operational variables of an industrial process.
33. Define mathematical modelling.
It is a collection of equations that describe the process. It is also the art of converting problems from one application area into tractable mathematical formulations with theoretical and numerical analysis that can provide insight, answers, and guidance for the originating application.
34. List two disadvantages of derivative action.
Derivative control is a rough prediction of future error based on the current slope of the error, and the time of error is measured with the Td. Some of its disadvantages include:
(i)The controller’s output is zero under constant error conditions.
(ii) It will increase the amount of noise in the error signal.
35. What steps are involved in creating the best controller?
To create a fool proof controller, the appropriate performance criteria must be defined (ISE, IAE, and ITATE). The value of these performance criteria must then be computed using a P, PI, or PID controller with the best settings for all adjusted parameters (Kp, Ti, and Td). Now choose the controller that provides the best value for the performance criteria listed above.
36. Why is electronic control preferable to pneumatic control?
Pneumatic vs. Electronic Controls: Electronic signals can travel long distances with no time lag. These electronic signals can be converted to work with digital controllers. Because intrinsic safety techniques eliminate electrical hazards, electronic devices can be designed to be almost maintenance-free. They are also less expensive to install and use less energy. Electronic controllers are preferred over pneumatic controllers due to their positive attributes and favourable properties.
37. What is the difference between SOE and alarms?
SOE stands for Sequence of Events. We can determine the trip’s location. We can also locate the first signal of the trip region.
An alarm is a process variable event such as low, high, high high and so on.
38. What is the difference between a level switch (LS) and a level transmitter (LT)?
A level switch is a digital input that provides only two signals: ON (1) or OFF (0).
When a level transmitter produces analogue output, the value of the output varies with time. In general, it ranges from 4 to 20mA.
39. Explain the difference between RS 485 and RS 232 communication protocols?
Because RS232 is a full duplex cable, both transmitting and receiving occur at the same time, resulting in increased noise and the inability to travel longer distances.
RS485 half-duplex cable means that either transmitting or receiving will occur at the same time, allowing us to travel a greater distance without interruption.
40. Why do we keep the gap voltage in the vibration probe?
The EDDY current is created when the vibration probe tip contacts the shaft area. Vibrations can be measured by increasing and decreasing the area of the shaft. As a result, it must be completed during the installation process.
41. Define flow meter?
Flow metres are devices that measure the rate of fluid flow. It can detect the linear, nonlinear, mass, and volumetric flow rates of gas and liquid.
42. How to Calibrate a Magnetic Flow meter?
We can perform dry calibration on a magnetic flow metre by disconnecting the flow tube/sensor connections from the metre and connecting the simulator to the transmitter.
After the connections are made, begin simulation by adjusting the simulator’s knobs and checking for errors. We can make adjustments if there is an error.
43. What is flow compensation?
The density of the steam or gas changes as pressure and temperature change in steam or gas flow measurement. If the density change is not compensated for, it can affect the accuracy of the measured flow rate. Temperature and pressure compensated flow control is a flow control that has been mathematically adjusted to include one or more additional variables.
44. Explain temperature compensation?
Temperature compensation is used to correct output characteristics that are influenced by the operating temperature as well as the temperature characteristics of electronic devices and electronic components in electronic circuits (temperature drift.)
45. What is an Ultrasonic flowmeter?
Ultrasonic flowmeters measure fluid velocity by passing a high-frequency sound wave through the fluid path. The ultrasonic method makes use of the change in propagation time of a moving fluid. Ultrasonic flowmeters are classified into two types: Doppler and transit time.
46. What are the options for measuring an object’s temperature without making contact?
Pyrometer measures the temperature of a surface without touching it. Every object that is greater than absolute zero (-273.15 ° C) emits radiation. This emission is heat radiation and is temperature dependent. The term infrared radiation is also used because the majority of the wavelengths of this radiation are in the infrared domain of the electromagnetic spectrum rather than visible red light.
47. How are DP transmitters linked to closed tanks?
In a closed tank, the bottom of the tank is attached to the transmitter’s high-pressure side. The tank’s top is attached to the transmitter’s low-pressure leg. The vessel’s pressure can be measured in this manner.
48. How does a D.P. transmitter work in an open tank?
The L.P. side of an open tank level measurement is vented to atmosphere. Whatever pressure acts is on the HP side, which is a level measure.
49. Explain purge level system?
This method is also known as the bubbler level measurement method. A pipe is installed vertically, with the open end at zero. The pipe’s other end is connected to a regulated air supply as well as a pressure gauge or a transmitter. To measure the level, the air supply is adjusted so that the pressure is slightly higher than the pressure caused by the liquid’s height. This is accomplished by gradually increasing the air pressure until bubbles can be seen leaving the open end of the pipe. The gauge then measures the amount of air pressure required to overcome the liquid’s pressure.
P=HXD delta
50. Use of purge level system?
On for corrosive liquids where the transmitter cannot be connected directly to the process, such as acids and some organic liquids.