An encoder is a device that can convert the mechanical motion into an electrical signal, so basically, the encoder is a motion sensor device. We can use encoders to measure the length, position, speed, or angular position. So the encoder is an angular position sensor, the electrical signal which resembles the motion will be given to a control device and this signal can be used to control an event. There are many types of encoders to do this type of motion sensing and they could be, magnetic, resistive, and optical. The encoders would produce either incremental or absolute signal. In order to do the proper measurement, we must select the proper model for our application, the selection of the proper encoder can be done by knowing the role of encoders in the motion control system.
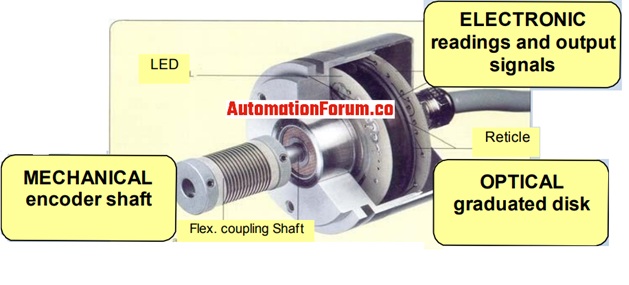
What is the need for an encoder and where do we use an encoder?
The encoder is capable to give information about the position, speed, and direction of a moving part. The encoder would send a feedback signal and it can be used to determine the position, count, speed, etc. We can use the encoder for almost all types of motion applications. There are many types of encoders and they can be used for a variety of applications.
They act like feedback transducers for speed control in motors, such as sensors for measuring, and position. It can also be used for speed and range control applications.
What are the types of encoder and how do they work?
There are two types of encoder they are linear and rotary encoder, the linear encoder would respond to motion along a path, while the rotary encoder would respond to rotary motion. The linear and rotary encoders are again divided into two types and they are absolute and incremental encoder.
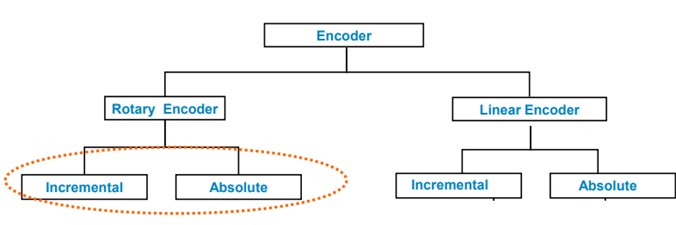
Rotary encoder
The rotary encoder is capable to convert the angular position of the shaft motion to a digital signal. In a rotary encoder, the shaft of the encoder will be coupled to the shaft of the spinning system to be monitored. The revolution of the shaft is then converted into an electrical signal and it is done with the help of a photoelectric and processing system and this electrical signal is then transferred to the PLC or counters.
Absolute encoder
This type of encoder can provide the specific location, the absolute encoders can be single-turn or multi-turn. The single-turn encoders are suitable for short travel applications while the multi-turn encoders are suitable for long position applications. The components of an absolute encoder are almost the same as in the incremental encoder. The absolute encoders are composed of a Light source which would be LED, a photo-detector, and a disk. The absolute encoders are also called shaft angle encoders they are used to detect the angular position.
The disc or plate that has opaque or transparent segments passes between a light source and this could be an LED and the light beam would be interrupted by the detector. The generated electronic signal will be then transferred into a controller where position and velocity are calculated according to the received signal.
What are the advantages of absolute encoders?
- The memory is non-volatile so in case of power failure the true position won’t be lost
- It is really flexible for programming
- Each position is unique
- Safety is improved, the position is automatically verified during the power-up
- It has good immunity to electrical noise
Incremental encoder
The incremental encoder is mostly used to determine the rotary or linear position. The incremental encoder has sensors in order to do the angular measurement, and the sensors would use the mechanical or magnetic index for this purpose. A transparent disk is used by the incremental encoder and it would have opaque sections which is equally spaced to know the movement. The LED would pass the light through a glass disk and it would be detected by a photodetector, because of this the encoder would generate pulses which are equally spaced pulses.
What are the advantages of incremental encoder?
- It would provide details about the relative position and won’t give the absolute position
- It must do a homing function for a fixed reference position
- If there is any interruption in the r supply then the pulse count could be lost
Linear encoder
This encoder would convert the linear position into an electrical output signal. The major parts of a linear encoder is a tape scale, light source, and a photoreceptor. The light source, photoreceptor are mostly housed together, the linear encoder can detect the movement from the changes in position with time. The working function of an optical and magnetic linear encoder is the same.
The linear encoder system uses a magnetic sensor and a magnetic scale in order to produce the analog output channel A and B so when the magnetic sensor passes along the magnetic scale, the sensor would detect a change in the magnetic field and outputs a signal. This output signal will be proportional to the measuring speed and the displacement of the sensor. The major advantage of the linear encoder is that it operates by a change in the magnetic field so it won’t be affected by the interference of light, oil, debris, etc
Magnetic encoder
The magnetic sensor has a rotor and a sensor, the rotor would move with the shaft and it would have north and south poles around its circumference the sensor would detect the small shifts in the position from north to south and south to north. The change in a magnetic field will be detected by hall-effect and magnetoresistive sensors. The hall-effect sensor work by detecting a change in voltage by magnetic deflection of electrons, while the magnetoresistive sensors detect a change in resistance caused by a magnetic field.
How to install an encoder
The encoder installation is very important, after selecting the motor we must know how to install it. The encoder installation is mostly done according to its mounting and base option, different mounting option has variable functionalities.
What is a single and multi-turn encoders?
The single-turn encoder solves a single revolution or turns from the axis. This type of encoders can provide positional data and it will be repeated cyclically after a complete revolution. The number of increments per revolution is measured by using a single coded disk. The multi-turn encoder would provide the positional data through multiple or continuous turns until reaching the maximum of revolution.
How to select an encoder?
- Size
- Output configuration
- Input power
- Resolution available
- Output type
- Frequency response
- We must also consider the available accessories such as couplings, mountings,
- Operating temperature
What are the advantages of encoders?
- Accurate and reliable
- Low cost
- High resolution and also has integrated electronics
- Small size
What are the disadvantages of encoders?
- The magnetic encoders are affected by magnetic or radio interference
- Optical encoders are affected by light source interference
- It is susceptible to dirt
- There will be dust and oil contaminates
What are the applications of encoders?
- Robotics
- Drilling machines
- Gate control
- Conveyors
- Medical equipment
- Assembly machines
- Lathes
- Automation