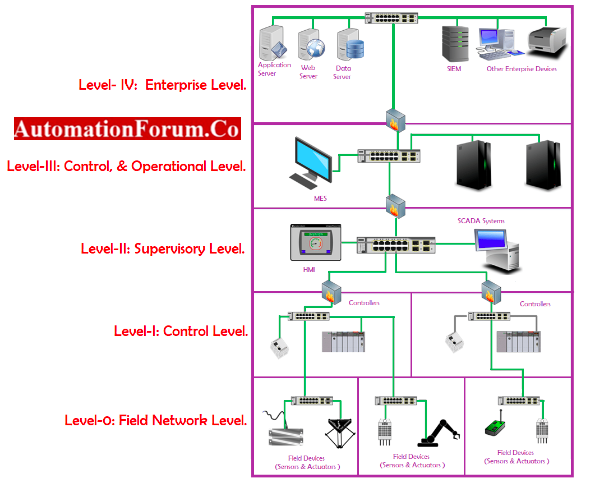
Describe Various Network Levels in Industrial Automation
Network Levels of Industrial Automation is classified into five levels
- Level IV – Business Planning, Logistics, and Enterprise-Level Operations
- Level III – Planning and Operations
- Level II – Supervisory Control
- Level I – Manipulation and Control
- Level 0 – Sensors and Signals
This Industrial Automation Network Levels are classified as
- Level A: Information Level
- Level B: Control Level
- Level C: Field Level
Level A: Information Level
- Level IV Business Planning, Logistics, and Enterprise-Level Operations.
Level B: Control Level
- Level III – Planning and Operations
- Level II – Supervisory Control
Level C: Field Level
- Level I – Manipulation and Control
- Level 0 – Sensors and Signals
These are described as
Level IV – Business Planning, Logistics, and Enterprise-Level Operations
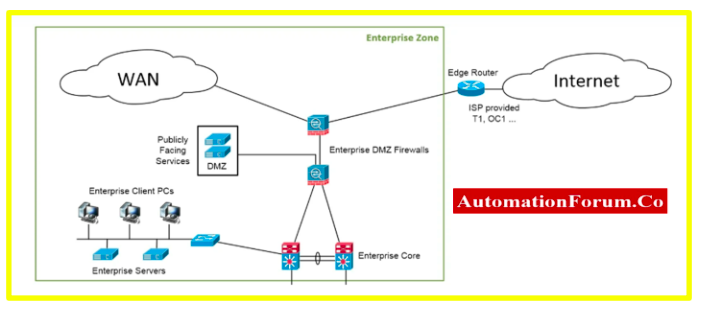
- This level comprises multiple departments such as HR, Finance, Logistics, production, purchase, sales, & inventory control.
- If the manufacturing process is not linked with the Manufacturing Execution System, the desired outputs are generated very slowly in the manual execution system.
- Employers need to wait for other department decisions to proceed to the next stage which leads to a decrease in production rate hence minimizing plant efficiency, so to avoid this Enterprise Resource Planning (ERP) system is used.
- This Enterprise Resource Planning is a kind of automation process that operates on computer technology to automate various processes related to the office in a comfortable way.
- Here the data flow is transparent and achieved automatically among departments to reduce time, increasing plant efficiency.
- The process travels from local control to enterprise process management via a supervisory system.
- This chain system makes the entire manufacturing process run smoothly through the automation cycle.
- Thus, it is essential to know and be familiar with each and every industrial automation strategy level present.
Level III – Planning and Operations
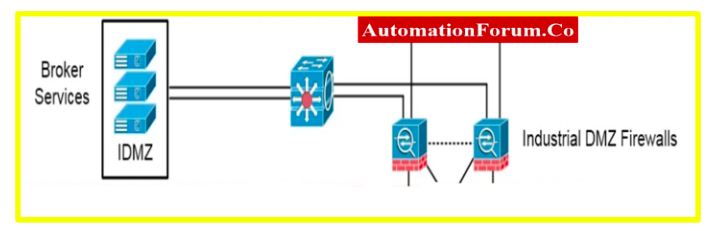
- This level is defined as a computer management system to monitor and control multiple SCADA systems.
- This level enables process plant planning and operations.
- In case the processing unit consists of multiple processes, & control systems, it is essential to control the entire operation from start to end through Manufacturing Execution System (MES).
- An operator can schedule all plant activities to monitor and control the manufacturing process station.
- Manufacturing Execution System (MES) enables equipment, & data information from various vendors right from start to end for planning daily charts.
Level II – Supervisory Control
- This supervisory control enables the operator to monitor and control in a control room with more number of PLCs through networking and communication between all PLCs.
- Usually, this Supervisory Control integrates each and every plant controller into one single platform to supervise and control the whole process control easily.
- This level consists of a Supervisory Control & Data Acquisition system or SCADA to observe, & inspect the whole system for alarm visibility, report generation, run batches, & control the operator’s action.
- We must be familiar with various communication topologies used in PLC systems to integrate the whole network through SCADA, this SCADA runs only on desktop or Industrial PC.

Level I – Manipulation and Control
- This level is known as the controlling stage, in this level the controlling of all control systems within the process occurs.
- This level includes Programming Logic Controllers and Proportional, Integral & Derivative Controllers.
- The sensor signal from the lower layer or level 0 is collected to control an output device like the motor or final control element.
- To control this logic is required to be created in a controller to accept an input signal from the sensor input to control related output devices.
- This level transmits data or signals to a higher level through communication.
- The Programming Logic Controllers’ memory has a stored program to manipulate the inputs and outputs.
- Apart from Programming Logic Controllers, this Proportional, Integral & Derivative controller is also employed in this layer to minimize the financial requirement. Since this PID is a small controller for output modulation based on input & PID calculations.
- A PID controller consists of an in-built programmed device that cannot be changed by others but can be changed or modified by the manufacturer only.
- But Programming Logic Controllers provides the user to configure the logic as per process requirements.
Level 0 – Sensors and Signals
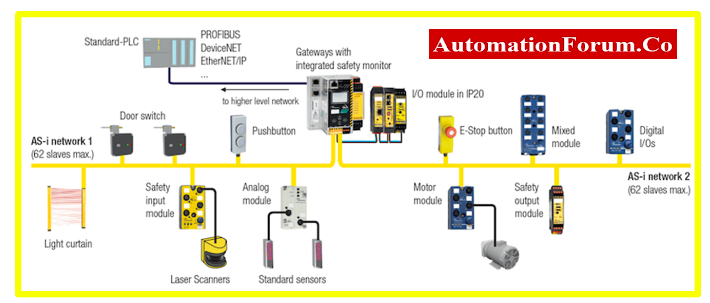
- This layer is also known as the field layer.
- It is the lowest, & the first layer in Industrial Automation.
- Usually, every working staff must have an idea of hardware input and hardware output controlling for higher or advanced levels of programming.
- It is also essential to have an idea of the sensor, & motor work, unless knowing these it is difficult to control at higher levels.
- The devices presented in this layer convey data with respect to the next level.
- The data may be analog, digital, or in communication form.
- This level includes field instruments such as sensors, transducers, actuators, instruments, motors, valves, actuators, switches, and other equipment.
- The primary purpose of industrial automation is to monitor and regulate all I/O’s for efficient process operation.
Frequently Asked Questions (FAQ)
What are the different types of industrial networks?
- Industrial network architectures consist of
- Sensor Networks,
- Control Networks,
- Safety Buses, &
- Field bus Networks.
What are the three main types of automation systems?
- Automation Systems are categorized into:
- Fixed automation.
- Programmable automation.
- Flexible automation.
What are Industrial Automation Networks?
- Industrial Communication networks in Industrial Automation include
- Ethernet,
- DeviceNet,
- Modbus,
- ControlNet
What are the four popular types of networks?
- Personal Area Network PAN
- Local Area Network LAN
- Metropolitan Area Network MAN
- Wide Area Network WAN
What are the top five sub-network classes?
- Class A: First Octet Value 0-126
- Class B: First Octet Value 128-191
- Class C: First Octet Value 192-233
- Class D: First Octet Value 224-239
- Class E: First Octet Value 240-255