Table of Contents
- Comprehensive Flowmeter Selection Considerations
- What are the key factors to consider when choosing a flowmeter?
- Major Flowmeter Technologies Overview
- Differential Pressure Flowmeter Technology
- Electromagnetic Flowmeter Technology
- How does electromagnetic flowmeter technology work and where is it best used?
- Coriolis Mass Flowmeter Technology
- What is the principle behind Coriolis mass flowmeter technology, and when is it most suitable?
- Vortex Flowmeter Technology
- Swirl Flowmeter Technology
- Ultrasonic Flowmeter Technology
- Variable Area (VA) Flowmeter Technology
- What are the benefits and limitations of variable area flowmeter technology?
- How do I choose the right flowmeter for liquid, gas, or steam applications?
- What are the considerations for selecting the right flowmeter for gas applications?
Comprehensive Flowmeter Selection Considerations
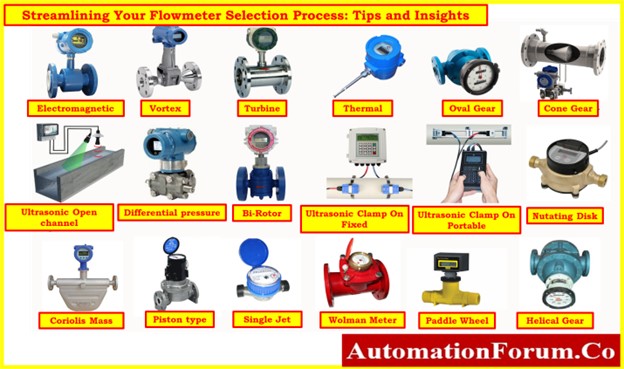
Choosing the right flowmeter necessitates a thorough examination of multiple critical factors:
What are the key factors to consider when choosing a flowmeter?
Media and Application
- Type of media (liquid, gas, steam)
- Media properties (viscosity, density, temperature)
- Purpose (process control, monitoring, billing, quality assurance, safety)
Specific Application Details
- Flowrate and pipe specifications (e.g., flanged, wafer style)
- Display and output requirements (rate, total flow, etc.)
- Device location (hazardous area, harsh environment)
- Additional features (enhanced diagnostics, conductivity, gas bubble detection)
Accuracy Assessment
- System accuracy
- Repeatability
- Response time
- Upstream and downstream straight piping length requirements
- Permanent pressure loss considerations
Total Cost Evaluation
- Long-term ownership costs (including maintenance)
- Energy consumption (for some flowmeter types)
- Balance initial cost against lifecycle expenses
Major Flowmeter Technologies Overview
- There are six main flowmeter technologies in the field of flow measurement that serve a wide range of applications.
- Choosing the best flowmeter requires first gaining a thorough understanding of each technology’s workings as well as its distinctive advantages and drawbacks.
- The following are the six most common flowmeter technologies:
- Differential Pressure flow measurement
- Electromagnetic flow measurement
- Coriolis mass flow measurement
- Vortex and Swirl flow measurement
- Ultrasonic flow measurement
- Variable Area flow measurement
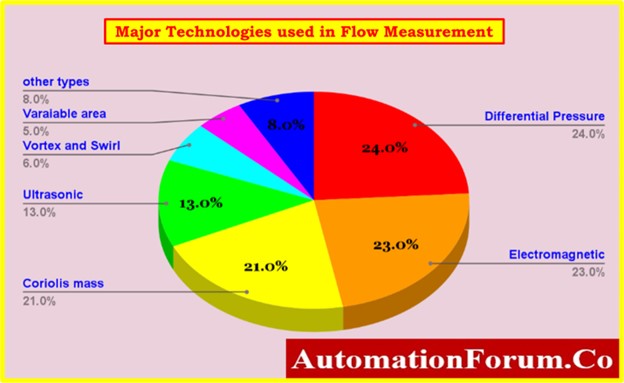
- It’s important to keep in mind that some flowmeter technologies, like thermal mass, positive displacement, and turbine methods, are included in the “Other” category and are not discussed in this article.
Differential Pressure Flowmeter Technology
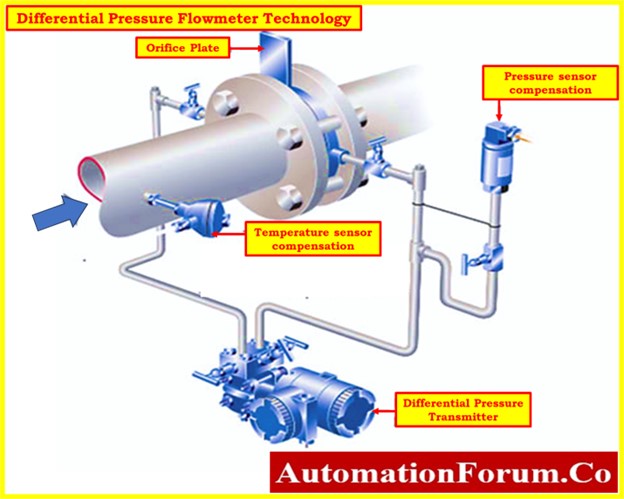
- Differential Pressure (DP) flowmeters are among the most widely utilized instruments for flow measurement.
- They typically consist of a flow element, sensors positioned both upstream and downstream of the flow element, and a differential-pressure transmitter.
- Various primary elements, such as orifice plates, venturis, wedges, pitot tubes, nozzles, or similar devices, can be employed.
- The design often includes a wedge-shaped flow element that creates a constriction within the pipe, resulting in a pressure drop from one side to the other.
- As the fluid flows from left to right, the higher pressure upstream of the constriction is compared to the lower downstream pressure, yielding the differential pressure.
- This difference is directly proportional to the fluid’s velocity, with higher flow velocities leading to larger differential pressure readings.
- The choice of primary element depends on specific application conditions.
- For instance, an orifice plate may not be ideal for flows with suspended solids causing turbulence and a substantial pressure drop.
- In such cases, a flow nozzle can minimize turbulence and reduce pressure loss.
What are the advantages and limitations of differential pressure flowmeters?
Advantages of Differential Pressure Flowmeters
- Suitable for measuring liquids, gasses, and steam.
- Ability to tolerate extreme process conditions.
- Transmitter replacement is feasible without process shutdown.
- Completely electronic with no moving parts.
- Approved for custody transfer applications.
- A well-established and understood method for flow measurement.
Limitations of Differential Pressure Flowmeters
- Limited rangeability due to the non-linear discharge coefficient.
- Inferior accuracy when compared to other flowmeter technologies.
- Accuracy may deteriorate with wear and clogging.
- Susceptibility to changes in fluid density, pressure, and viscosity.
- Maintenance can be intensive, particularly with orifice plate configurations.
Electromagnetic Flowmeter Technology

How does electromagnetic flowmeter technology work and where is it best used?
- Electromagnetic, or Mag Flow, technology relies on a magnetic coil, which can be integrated into a primary transmitter or connected to a secondary sensor assembly remotely.
- These coils are typically situated both at the top and bottom of the meter tube. Opposite these coils, a pair of electrodes is positioned outside a metal tube, which contains an inert liner, such as PTFE (Teflon™), elastomers, ceramics, or various plastic materials, chosen based on the specific application requirements.
- A current is applied to the coil package from the transmitter, generating a magnetic field across the metering pipe.
- As a conductive liquid flows through this magnetic field, it causes the charged particles within the solution to separate.
- This separation induces a voltage between the two electrodes, directly proportional to the flow velocity.
- Notably, Mag Flow meters feature open pipes with electrodes flush against the liner walls, eliminating flow obstructions.
- This technology’s simplicity and accuracy with conductive fluids have made it prevalent in various industries.
Advantages of Electromagnetic (Mag Flow) Flowmeters
- Capable of measuring electrical conductivity as low as 5 microsiemens.
- Typically requires minimal upstream (3-5D) and downstream (0-3D) straight piping.
- Independent of pressure, temperature, and viscosity variations.
- Suitable for use with fluids containing entrained solids.
- Wide diameter range, from 1/10″ to 96″.
- Features a straight-through tube with no moving parts.
- No pressure losses are incurred.
Limitations of Electromagnetic (Mag Flow) Flowmeters
- Limited to the measurement of conductive liquids.
- Measurement accuracy can be compromised when dealing with weakly conductive fluids, like demineralized water.
- The presence of deposits inside the measuring tube or on the electrodes may lead to measurement errors.
Coriolis Mass Flowmeter Technology
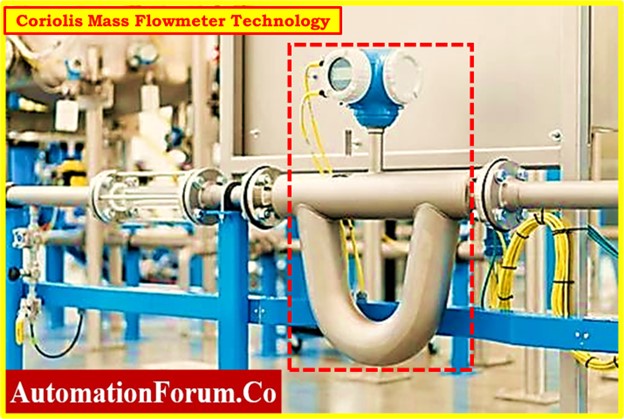
What is the principle behind Coriolis mass flowmeter technology, and when is it most suitable?
- The concept of Coriolis mass flow technology has a long history, but it has gained widespread adoption as a practical flow measurement tool in the past decade or so.
- Coriolis flow meters measure the direct mass of the medium using tubes within a sensor.
- An exciter imparts a “twisting” motion to the fluid, generating a uniform oscillation as the medium traverses the measuring tubes.
- The greater the flow velocity, the more pronounced the deflection of these oscillating tubes.
- Sensors positioned at the inlet and outlet of the element measure the time it takes for the oscillation, particularly in a one-to-one and a half-second time window.
- This time difference, known as the phase shift, is directly proportional to the mass flow rate, providing a precise measurement of the volume of liquid or gas in the pipe.
- Coriolis technology goes a step further by offering density measurement capabilities, which prove valuable for mass flow calculations.
- In addition to oscillation frequency, the sensors also capture amplitude data.
- A denser medium exhibits slower oscillations. While the cost of this technology is typically higher compared to other flow meters, it delivers data that others don’t, including temperature information.
- One major advantage of Coriolis flow meters is their insensitivity to changes in fluid density.
- They can accurately measure substantial pressure drops across the flowmeter at high flow rates and viscosities.
- They are especially suitable for applications where the physical properties of the fluid are unknown or subject to variability.
Advantages of Coriolis Mass Flowmeters
- Insensitivity to changes in fluid density, making them suitable for applications with variable or poorly known fluid properties.
- Applicable for measuring liquids, gasses, and steam.
- Exceptional accuracy.
- Direct mass measurement, including density and temperature.
- Suitable for sanitary applications.
- Approved for custody transfer of liquids and gasses.
- Highly reliable with low maintenance requirements.
- Unaffected by flow-profile disturbances.
- Easy installation, without the need for specific inlet or outlet sections.
- Excellent verification and diagnostic capabilities.
Limitations of Coriolis Mass Flowmeters:
- Higher cost, especially for larger sizes above 4″.
- Potentially higher pressure drops in older “U-shaped” tube designs and for high-viscosity fluids.
- Limited material options for wetted parts.
- Limited and potentially expensive for corrosive fluids.
- Limited range in terms of line size.
Vortex and Swirl Flowmeter Technology
Vortex Flowmeter Technology
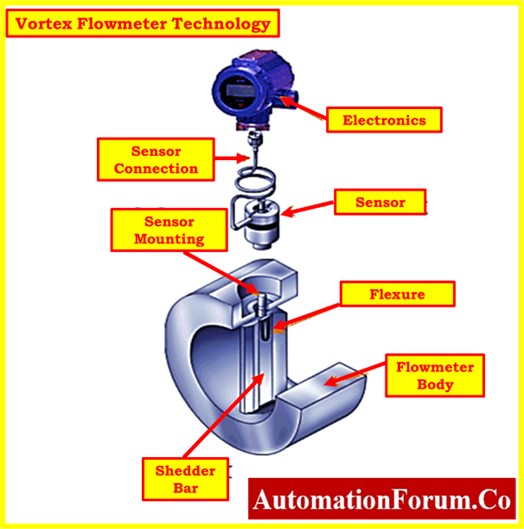
- Flowmeters employing this vortex principle feature an obstruction known as a “bluff body” inside a pipe, typically situated in the middle.
- The presence of this bluff body disrupts the flow of the medium, inducing repeated vortices on each side of the obstruction.
- A mechanical sensing element measures the frequency of the oscillations between these vortices, which correlates directly with the flow velocity.
- The key advantages of this technology include its versatility to work with all types of media and the absence of moving parts within the meter.
- By incorporating pressure and temperature measurements, it becomes possible to calculate mass flow.
- However, one notable drawback is its performance at low flow rates, which is less optimal.
Advantages of Vortex Flowmeters
- Suitable for measuring liquids, gasses, and steam across wide measurement ranges (e.g., 30:1 for gas/steam and 20:1 for liquids).
- Available in a range of diameters from ½” to 16″.
- Mass flow measurement is attainable by integrating pressure and temperature data.
- Offers good accuracy (e.g., ±0.75% for liquids and ±1.0% for gas/steam).
- Incurs low pressure loss, typically around 0.44 psi.
Limitations of Vortex Flowmeters
- Accuracy can be reduced by pulsating flow.
- Requires extended inlet and outlet runs for optimal performance.
- Not well-suited for highly viscous fluids.
- Inferior accuracy compared to other technologies at the lower end of the measurement range.
- Not ideal for applications involving dirty or abrasive fluids.
Swirl Flowmeter Technology
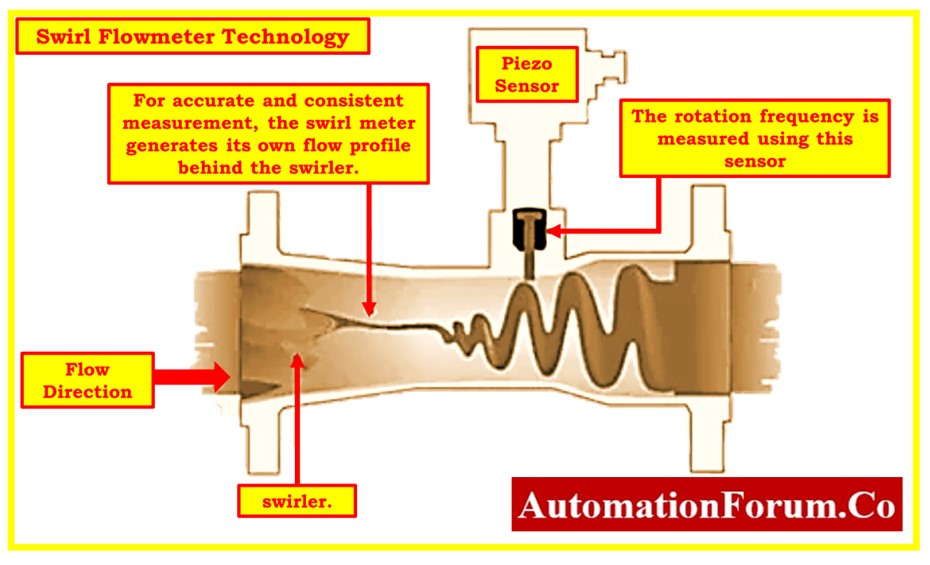
- Swirl technology is akin to vortex flowmeters but with some distinctions. It measures pressure variations caused by an obstruction.
- A stationary turbine rotor at the inlet generates a small, thread-like rotating flow, which expands as it moves toward the outlet.
- Sensors at the outlet calculate the flow rate based on the rotation speed.
Advantages of Swirl Flowmeters
- Minimal requirements for upstream and downstream piping.
- Delivers excellent accuracy of ±0.5% of rate for liquids, gasses, and steam.
- Enables volumetric measurement of liquids, gasses, and steam.
- Facilitates mass flow measurement when pressure and temperature sensing are integrated.
- Offers cost-effective installation, thanks to 2-wire technology.
- Incurs lower pressure loss than even vortex technology.
- Available with dual and triple-sensor designs featuring redundant analog loops.
Limitations of Swirl Flowmeters
- Accuracy can be reduced by pulsating flow.
- Unsuitable for highly viscous fluids.
- Less effective at the lower end of the measurement range compared to other technologies.
- Not recommended for applications involving dirty, corrosive, or abrasive fluids.
Ultrasonic Flowmeter Technology
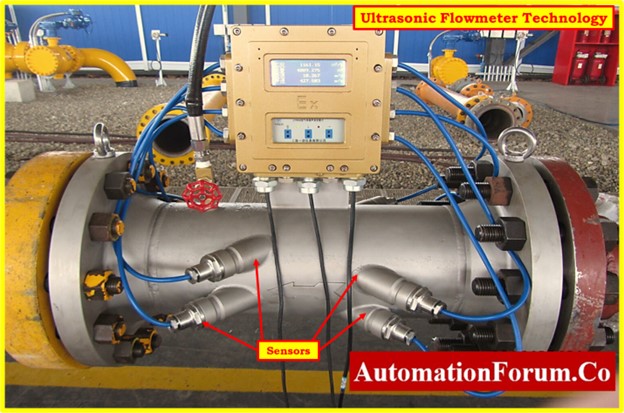
- These flowmeters transmit ultrasonic signals both upstream and downstream within the pipe.
- Sensors are responsible for detecting the differences in transit times between these two signals.
- Combining this data with pipe diameter enables the calculation of the flow rate.
- Ultrasonic technology is best suited for measuring liquids, including water, cryogenic fluids, and chemicals.
- However, it can also measure gasses and vapor. It excels at determining the velocity of liquids through which ultrasonic waves can propagate, such as water, molten sulfur, cryogenic liquids, and chemicals. Slurries, however, can potentially disrupt the ultrasonic signal.
- One of the primary advantages of ultrasonic flowmeters is the absence of pressure loss, making them suitable for use with corrosive fluids.
- However, caution must be exercised to prevent sludge deposits on the pipe walls, which could interfere with ultrasonic signals. The addition of more sensors can mitigate this issue.
Advantages of Ultrasonic Flowmeters
- Applicable across a wide range of pipe sizes.
- Suitable for measuring highly corrosive fluids.
- No pressure loss incurred during measurement.
- Retrofitting is feasible through mounting or welding to a pipe.
- Measurement principle is independent of the physical properties of the fluid.
Limitations of Ultrasonic Flowmeters
- Measurement results can be influenced by flow profiles.
- Medium-to-low accuracy, depending on the acoustic transparency of the fluid.
- Deposits on the pipe or sensor can reduce measurement accuracy.
- The Doppler method is only applicable to specific applications, primarily for flow monitoring.
Variable Area (VA) Flowmeter Technology
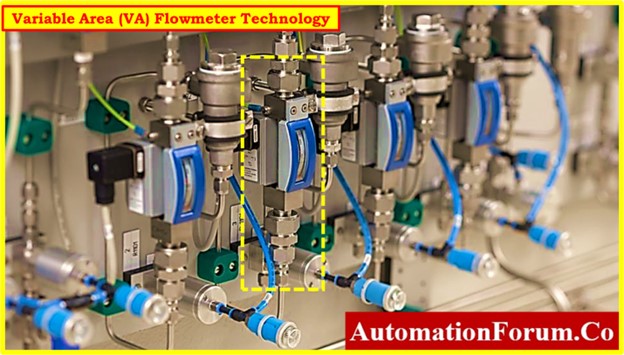
- Variable Area (VA) flowmeters represent a technology that has been in existence for many years.
- It relies on a simple measurement principle that functions effectively with various liquids.
- Commonly employed as a cost-effective means for local indication of small liquid or gas flows, VA flowmeters consist of a vertical, conical column with a narrow base and a wider top.
- Within this column is a specialized float that moves freely in an upward and downward manner.
- The fluid to be measured enters the bottom of the meter and flows upward through a metering tube, encircling the float, and exits at the top.
- Flow rate is determined by observing the position of the float relative to a calibrated scale etched onto a sight glass.
- In some instances, remote measurements can be obtained using sensors that gauge the height of the float.
- This is an inferential type of measurement, primarily suitable for relatively clean liquids and gasses. The medium must possess sufficient clarity for the float level to be visible.
- Various methods of connecting the float are available to align with specific application requirements.
- Some designs incorporate a spring-opposed vane that responds to variations in flow rate, while others employ a spring-opposed piston, which is less sensitive to viscosity discrepancies.
What are the benefits and limitations of variable area flowmeter technology?
Advantages of Variable Area (VA) Flowmeters
- Capable of measuring liquids, gasses, or steam.
- Economical choice for flow measurement.
- Requires no power supply for operation.
- Sight glass designs offer straightforward, dependable on-site flow monitoring.
- Incurs low pressure loss.
- Suitable for handling high pressures.
Limitations of Variable Area (VA) Flowmeters
- Measurement accuracy is dependent on process conditions and fluid properties.
- Not suitable for media that may coat the measuring tube or float or obstruct sight glass visibility.
- Requires fluid-specific calibration.
- Limited turndown ratio (typically 10:1).
- Susceptible to interference from entrained matter, rendering it unsuitable for liquids containing solids.
- Lacks a totalizing function for cumulative flow measurement.
How do I choose the right flowmeter for liquid, gas, or steam applications?
Choosing your Flowmeter
The six main flowmeter technologies are summarized in these tables based on how effectively they satisfy the most typical application requirements.
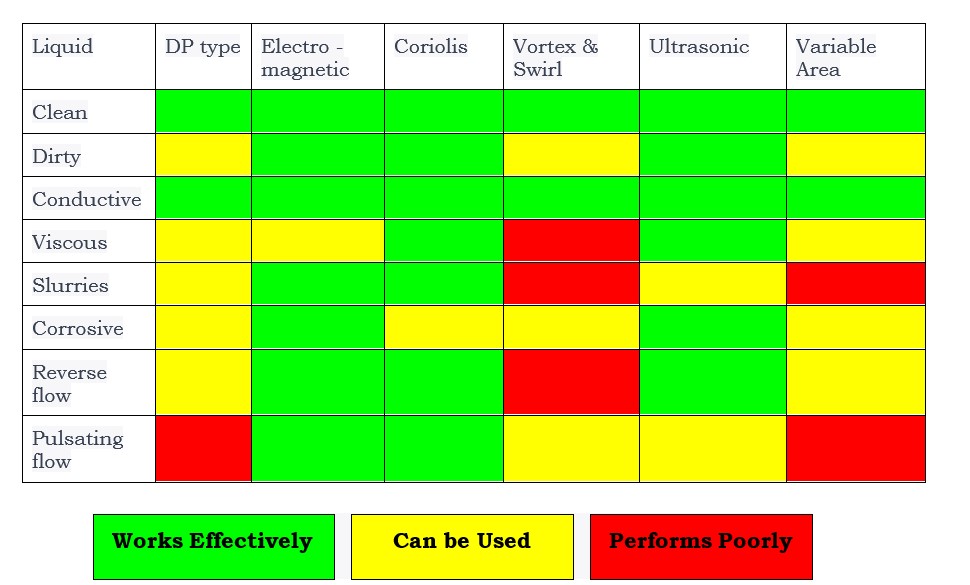
What are the considerations for selecting the right flowmeter for gas applications?
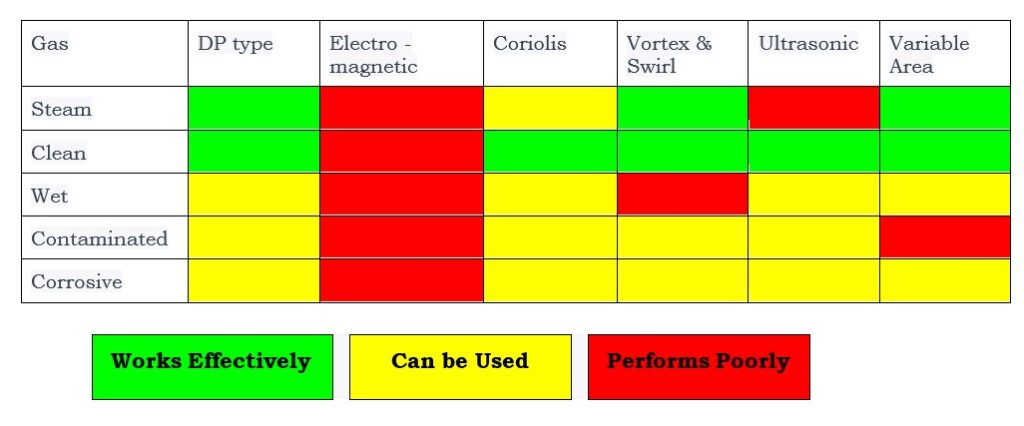