The chance of a load cell failure is a lot and it could be because of various reasons, the load cell failure could be because of mechanical, electrical, or environmental problems. In case if the load cell is not working properly then we should do the visual inspection. The problems could happen because of the damage to the cable. So in order to determine this, we can visually inspect it, we should keep the plug clean and we shouldn’t carry a load cell by the cable.
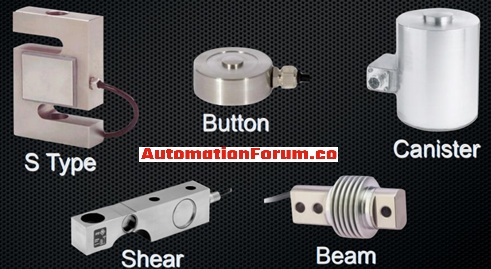
How to do the visual inspection of the load cell?
We should check if the load cell is covered in rust, or corroded if there is rust then it could reach strain gauge areas too. If the physical condition, of the load cell, is good then we need to check the sealing areas and cables. So check the strain gauge seals for any damage and we should also check the load cell cable entrance. We should also check for cracks, metal distortion, and rippling. The visual inspection will only be completed after checking the cables so check if the cables have any cuts, crimps, and abrasions. If the cable is cut, and if the load cell is in the wet area then the chances of water entering the load cell are huge and it could damage the load cell.
What are the failures that could happen in a load cell and how to solve them?
Mechanical failure of load cell
The load cell can mechanically fail, if we select a load cell that is too small for the purpose it is used for then it could be damaged. So if the weight can’t be handled by the load cell then the cell would be damaged and it won’t be able to return to its no-load shape. So while selecting a load cell for an application we should consider the total weight of the structure and also the weight of the material that is being weighed. The structural support point in the load cell would help to distribute the load in the load cell. So the total weight of the material will be divided equally in the load cell.
Another chance for mechanical failure in load cells is due to shock loading. Shock loading means the weight will be dropped suddenly to the load cell, so while loading proper care must be taken to avoid the shock loading. If the load cell capacity is high then it could affect the sensitivity. Failure could also happen due to the non-axial side loading and it would also pay the way for measurement inaccuracies. So the weight must be loaded to the load cell by using proper mounting devices.
Environmental effects in load cell
Most load cells are designed to operate in a specified temperature range. The load cell could operate without any problems beyond these limits, but the calibration data which is in the load cell would only be valid if the load cell operates in its temperature range. The load cell must be kept away from moisture because moisture could cause a lot of problems like no output overload indications, or continuous drift can also happen. Moisture can get inside the load cell through cut cables or through pressure, so while using a load cell we should check if it is damaged in any way. If the load cells are exposed to chemicals then the chances of corrosion will be high and this corrosion could reach the strain gauge. So in order to prevent this, a stainless steel load cell can be used to prevent corroding.
Other similar problems that could happen in a load cell
Readings of the load cell are unstable
In case of this check if the readout box is properly positioned, also check if the data logger’s swept-frequency excitation settings are correct or not. Also, we need to check if the readout or the data-logger works with another load cell or not and if it is not connected then there could be some problem with the readout like low battery or something similar to that. This problem could also happen in case if there is any electrical noise close to it. We should check if the shield drain wire is connected to the ground or not.
High thermistor resistance
In case of this problem check if all the connections and terminals are proper, also check for any cut in the cable.
Resistance of the thermistor is very low
In case of this problem, we should check for any short circuits and also check the connections, plugs, and terminals. It could also happen in case if the water has entered the load cell.
Failure of the load cell gauge to read
This problem could happen if the cable is cut or crushed and in order to determine this, we can use an ohmmeter to check the resistance between the two gauge leads and the resistance will be very high in case of any cut wire.
The movement of the load cell is restricted
This problem could happen because of the friction or it could also happen due to any obstacle and this would affect the load cell measurement, the output of the load cell won’t be accurate. So we must make sure that there is no obstruction for the load cell and also the mounting of the load cell is proper.
Electrical damage to the load cell
This type of damage can occur because of lightning strikes and it could also happen if welding is done to the structure in which the load cell is attached. So in order to prevent this, we can use surge suppression devices
Reading is not stable in the load cell
This problem could arise if the power supply is not good if the voltage level is lower than eleven volt DC then fluctuations could occur in the readings.
The capacity of the supply system should be checked too, the scale indicators would draw a good amount of power at twelve volt DC according to the applications.
The unstable reading of the load cell can also happen because of the poor load cell connections. So make sure the physical conditions of the connectors, sockets, and pins are in good condition. Make sure the cable doesn’t have any cut. In order to determine the internal breaking in the cable flex the cable thoroughly and while doing this watch the display for any sudden reactions.
Indicator faults
- This problem could arise if there is any damage to its circuit
- The digital indicator would be out of calibration
- The digital indicator and the load cell would require the coarse zero adjustment
How to do the load cell testing?
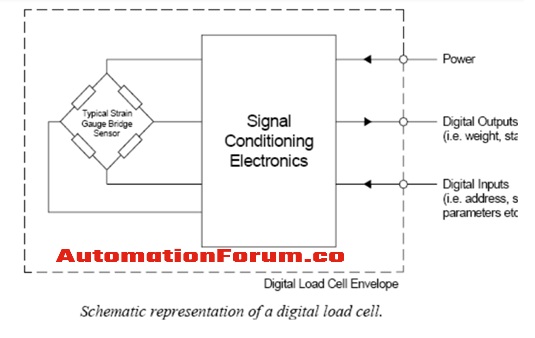
We need certain test equipment to check or evaluate the load cell and they are
Ohmmeter
We should use high-quality calibrated digital volt and ohmmeter and it should have good measuring accuracy. So it can be used to measure the zero resistance and also the integrity of the bridge circuit.
Megohmmeter
A megohmmeter is really capable to do the measurement of five thousand megaohms with good accuracy and this is required to do the testing of the insulation. We should be careful while selecting a megohmmeter, we should not use a megohmmeter that supplies more than fifty volts to the load cell.
Dead load lifter
We should also use some equipment that should be able to lift the dead load such as a tank, conveyer, etc. This equipment must be capable to lift the dead load off the load cell so that the load cell can be removed and also zero balance can be checked too.
Zero balance test
This is the output of the load cell in case of a no-load situation, there will be variations in the zero balance if the load cell has been mechanically overloaded. The zero balance test can be done to determine if the load cell has been physically varied due to the mechanical overload. Physical distortion can also happen because of shock load or also because of metal fatigue. So before the beginning of the test, the load cell must not have any load, which means that the cell must be removed from the scale and the dead load must be counterbalanced. So the load cell is not connected to the cell, now we can check the signal leads so we need to disconnect the signal leads and also should measure the voltage across the negative and positive signal leads. In order to determine the positive and negative signal leads, we can check the calibration certificate to get the color code. So while doing the measurement the output must be similar to or close to the manufacturer’s specification. While testing we should make sure that the leads must be connected with the digital weight indicator which would provide the excitation voltage to the leads.
Bridge resistance testing
By using an ohmmeter we can do this test, so before starting this test the load cell must be disconnected from the digital weight indicator. The ohmmeter can be placed between the positive and negative excitation leads for the measurement of the input resistance. The measurement which is done should have a similar value to the value which is stated in the load cell calibration datasheet.
Insulation resistance test
This test is done to check the insulation resistance between the load cell and also the element or the cable shield. So in order to do this test, the load cell should be disconnected from the junction box, and connect the input, output, and sense lead together. Then we can use a megohmmeter to measure the insulation resistance between these connected leads and the load cell body. After that do the measurement between the load cell body and also the cable shield.