- Understanding Validation and Calibration
- Validation: Definition and Purpose
- Calibration: Definition and Purpose
- Performing Calibration and Validation
- Why Calibration and Validation are Necessary?
- Benefits and Importance of Validation and Calibration
- Comparison Between Validation and Calibration
- Frequency of Calibration and Validation
- Standards and Regulations for Calibration and Validation
- Validation and calibration are two essential procedures that are critical to maintaining reliability, accuracy, and efficiency in the field of instrumentation and management of equipment.
- Although these terms are frequently used together, they have different meanings when it comes to preserving the integrity of systems, processes, and measurement equipment.
- Competence in the differences between validation and calibration is essential for professionals in a variety of industries, including manufacturing, healthcare, and other fields.
Understanding Validation and Calibration
- The methods of validation and calibration are essential in order to ensure the functionality, accuracy, and compliance of the processes and equipment that are being used.
- There is a big difference between them in terms of their approaches, objectives, and applications, despite the fact that they both target the same goal, which is to ensure reliability and quality.
What is Validation?
Validation: Definition and Purpose
- The term “validation” refers to a procedure that is meticulous and documented, with the primary objective of ensuring that equipment, processes, and systems are installed correctly, operating efficiently, and giving accurate outputs without any errors on a constant basis.
- Its major objective is to make sure that the entire system meets the functional purposes for which it was designed and that it functions sufficiently and consistently in accordance with the specifications.
- In its most basic form, validation is the process of ensuring that a system performs as intended and meets the requirements and standards that have been established previously.
What is Calibration?
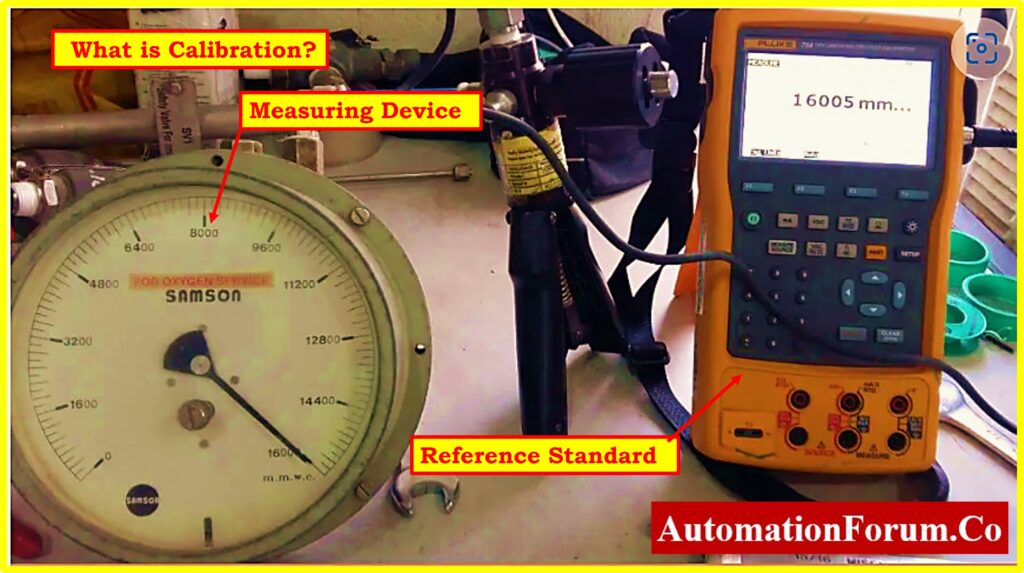
Calibration: Definition and Purpose
- Calibration is a methodical process that involves comparing the measurement readings of a measuring device or equipment to a reference standard.
- Calibration is a practice that is used to ensure that the device or equipment is correct.
- Through the process of modifying the device so that it corresponds with the readings of the standard, its major objective is to validate the accuracy of the measurements.
- Calibration is the process of ensuring that the measurement accuracy of an instrument is in accordance with a defined standard, which in turn improves the device’s reliability and precision.
- The primary objective of calibration is to remove differences and ensure that measurement instruments produce reliable and accurate results within the tolerances that have been specified.
Performing Calibration and Validation
To better understand the practical implementation of calibration and validation, let’s consider an example scenario involving a temperature measurement system in a manufacturing facility.
Calibration Process
Preparation
- Before calibration, gather the necessary equipment, including a reference thermometer with known accuracy and traceability to national standards.
Setup
- Place the reference thermometer and the thermometer to be calibrated side by side in a stable environment with a controlled temperature.
Comparison
- Record the readings from both thermometers simultaneously.
- Any discrepancies between the readings indicate potential inaccuracies in the thermometer to be calibrated.
Adjustment
- If discrepancies exist, adjust the thermometer’s settings or calibration parameters to align its readings with those of the reference thermometer.
- This adjustment process may involve calibration software or manual adjustments, depending on the device’s capabilities.
Verification
- After adjustment, repeat the comparison process to ensure that the calibrated thermometer now provides accurate readings consistent with the reference thermometer.
Documentation
- Document all calibration procedures, including initial readings, adjustments made, and final verification results.
- This documentation serves as evidence of compliance with calibration standards and regulatory requirements.
Click here for Basic Safety and General Consideration While Executing Calibration Process in process industries
Calibration Process – Example
Consider a similar example with a pressure transmitter. We’ll input pressure values and observe the corresponding output generated by the pressure transmitter. The acceptable error limit as per the process requirement is within +/- 0.5%.
Case 1: Calibration and Validation Table
Input Pressure (psi) | Desired Output (mA) | Actual Output (mA) | Error (%) | Validation Status | Calibration Needed |
0 | 4 | 3.98 | 0.5 | Pass | No |
50 | 12 | 12.05 | 0.42 | Pass | No |
100 | 20 | 19.98 | 0.1 | Pass | No |
50 | 12 | 12.02 | 0.17 | Pass | No |
0 | 4 | 3.99 | 0.25 | Pass | No |
In Case 1, the pressure transmitter has produced output within the acceptable error limits as per the process requirement. Hence, no calibration is needed.
Case 2: Calibration and Validation Table
Input Pressure (psi) | Desired Output (mA) | Actual Output (mA) | Error (%) | Validation Status | Calibration Needed |
0 | 4 | 3.5 | 1.25 | Fail | Yes |
50 | 12 | 11.5 | 1.25 | Fail | Yes |
100 | 20 | 19.2 | 0.4 | Pass | No |
50 | 12 | 11.8 | 1.67 | Fail | Yes |
0 | 4 | 3.6 | 0.5 | Pass | No |
In Case 2, the pressure transmitter has produced output with errors exceeding the acceptable limits for several input values. Hence, calibration is required.
After calibration, adjustments such as zero trim and span trim may be performed to ensure the pressure transmitter meets the required accuracy standards.
The same pressure transmitter will be validated once more after calibration, and the response will be observed.
Validation Process
Preparation
- Define the validation protocol outlining the scope, objectives, acceptance criteria, and testing procedures for the temperature measurement system.
Installation Qualification (IQ)
- Verify that the temperature measurement system is installed correctly according to manufacturer specifications and regulatory guidelines.
- This may involve checking sensor placement, wiring connections, and calibration status.
Operational Qualification (OQ)
- Assess the performance of the temperature measurement system under normal operating conditions.
- This includes testing the system’s accuracy, precision, and response time across a range of temperatures.
Performance Qualification (PQ)
- Evaluate the system’s ability to consistently deliver accurate temperature measurements over an extended period of operation.
- This may involve conducting repeated measurements under varying conditions to demonstrate reliability and consistency.
Data Analysis
- Analyze the validation data to ensure that the temperature measurement system meets predefined acceptance criteria and regulatory requirements.
- Any deviations or discrepancies must be thoroughly investigated and addressed.
Documentation
- All validation work should be documented, including with the procedures, test findings, deviations, and corrective actions done.
- This documentation serves as a comprehensive record of the validation process and provides evidence of compliance with regulatory requirements.
Why Calibration and Validation are Necessary?
- Calibration ensures measurement instruments provide accurate readings by aligning them with reference standards.
- Validation verifies equipment, processes, and systems operate effectively and consistently, minimizing variability and errors.
- Calibration and validation are required by regulatory bodies to meet industry-specific regulations and quality standards.
- They help identify and mitigate risks associated with inaccurate measurements, equipment malfunctions, and non-compliance.
- Calibration and validation are integral to quality management systems, ensuring product quality and customer satisfaction.
- They ensure measurement data integrity and reliability for informed decision-making and continuous improvement.
- Well-calibrated equipment and validated processes enhance operational efficiency by minimizing downtime and optimizing resource utilization.
Benefits and Importance of Validation and Calibration
In addition to their many advantages, validation and calibration are essential for improving quality, productivity, and compliance. To ensure operational excellence and establish into effect strong quality management systems, it is essential to understand their importance.
Benefits of Validation:
- Minimizes the amount of product that is rejected by ensuring that the product quality and process performance are consistent.
- Reduces utility costs by optimizing energy consumption and resource utilization.
- Provides assistance in the timely implementation of corrective actions by identifying deviations and inefficiencies in the processes.
- This ensures that production performance is consistent, which ultimately leads to increased customer satisfaction and a better reputation for the business.
- Streamlines quality assurance processes and minimizes the need for extensive finished product testing.
Benefits of Calibration:
- Ensures specificity, linearity, accuracy, and sensitivity of measurement instruments, enhancing reliability and precision.
- This certification ensures that crucial measurements are accurate, which in turn makes standardized release of products easier.
- Enables easier maintenance of equipment by identifying and rectifying deviations in measurement accuracy.
- Supports automation and process optimization by providing accurate data for control and decision-making.
- Reduces the risk of production liabilities and ensures compliance with regulatory standards and industry requirements.
Comparison Between Validation and Calibration
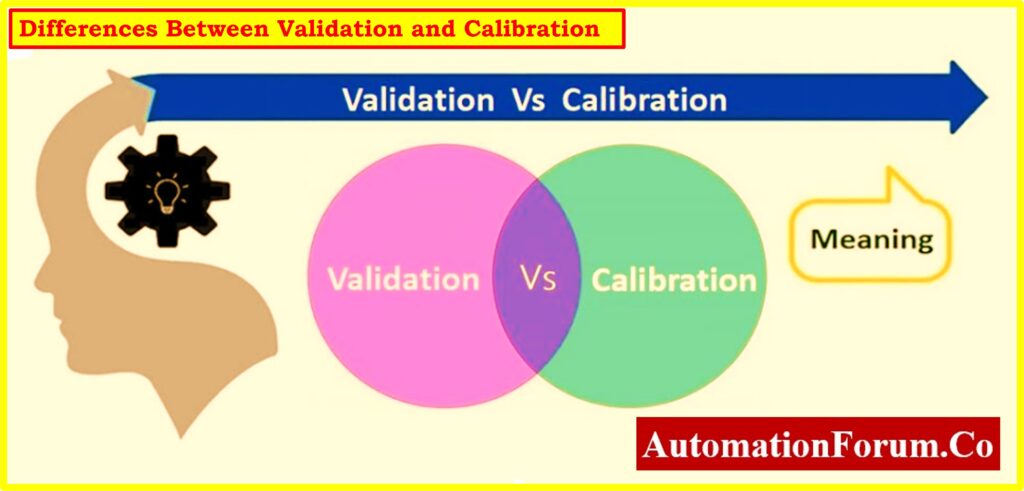
This below table provides a clear, concise overview of the key differences between validation and calibration, highlighting their respective definitions, purposes, methodologies, applications, and regulatory aspects.
Aspect | Validation | Calibration |
Definition | Confirms equipment, processes, and systems are installed correctly and operate effectively, delivering accurate results consistently.It is a methodology for analyzing performance. | Ensures measurement instruments provide accurate readings by aligning them with reference standards. It is a performance evaluating of the system. |
Purpose | Verifies that the entire system meets its intended functional intent and performs adequately according to specifications. | Certifies the accuracy of measurements, enhancing reliability and precision in measurement outcomes. |
Objective | Ensures functionality, accuracy, and compliance of equipment and processes. | Ensures measurement accuracy and reliability, minimizing errors and deviations. |
Methodology | Meticulous, documented process involving testing and analysis of equipment and processes. | Systematic procedure comparing measurement values against a reference standard. |
Application | Commonly applied in industries where process integrity and product quality are crucial (e.g., pharmaceuticals, manufacturing). | Found across various sectors requiring accurate measurement instruments (e.g.,Process industries]. |
Regulatory | Compliance with regulatory standards and guidelines (e.g., FDA, ISO) is essential. | Adhering to regulatory requirements is necessary for quality control and safety. |
Risk Mitigation | Helps identify and mitigate risks associated with process deviations and non-compliance. | Minimizes risks related to inaccurate measurements and equipment malfunctions. |
Documentation | Detailed documentation of validation protocols, testing results, and compliance records. | Comprehensive documentation of calibration procedures, adjustments made, and verification results. |
Frequency of Calibration and Validation
- Calibration: Typically performed periodically according to manufacturer recommendations or industry standards. The frequency can vary depending on the instrument type, criticality, and expected stability.
- Validation: Usually performed once at initial implementation or after significant changes to a process or system. However, re-validation might be required at specific intervals depending on regulatory requirements or risk assessments.
Standards and Regulations for Calibration and Validation
- Both calibration and validation can be subject to specific industry standards and regulatory requirements. These standards outline acceptable practices and acceptance criteria for conducting these procedures. Common standards include:
- ISO 17025: Specifies the General requirements for the competence of testing and calibration laboratories.
- Good Manufacturing Practices (GMP): Regulations for the pharmaceutical industry, which include specific requirements for validation of equipment and processes.