- Protocol Overview – Modbus TCP/IP
- Protocol Overview – Profinet
- Factor 1. Performance and Timing
- Factor 2. Communication Model
- Factor 3. Diagnostics and Maintenance
- Factor 4. Motion Control and Synchronization
- Factor 5. Data Handling and Representation
- Factor 6. Network Architecture and Scalability
- Factor 7. Configuration and Setup
- Factor 8. Redundancy and Reliability
- Factor 9. Future Readiness and Features
- Factor 10. Standards, Certification, and Support
- Factor 11. Real-World Applications
- Factor 12. Interoperability
- Factor 13. Ethernet Transmission Standards
- Factor 14. Security
- Profinet vs Modbus TCP/IP – Summary Comparison Table
- Which Is Better, PROFINET Or Modbus?
- What is the difference between Modbus and PROFINET?
- What is the difference between PROFINET and TCP/IP?
- Can PROFINET communicate with Modbus?
- Can I use PROFINET and Modbus TCP on the same network?
- Which protocol offers better security PROFINET or Modbus TCP/IP?
- MODBUS Protocol Quiz :Test Your Knowledge
Many industrial automation projects raise a question: Which industrial Ethernet protocol is better, Profinet or Modbus TCP/IP?
It’s not always simple to respond. Both protocols are commonly used, dependable, and fulfill different roles in automation systems. The decision between them, therefore, depends on application complexity, timing needs, diagnostics, scalability, and long-term integration objectives.
This article provides a detailed technical and functional comparison between Profinet and Modbus TCP/IP, supported by practical insights and deployment experience.
Protocol Overview – Modbus TCP/IP
Based on Ethernet, Modbus TCP/IP is a modification of the original Modbus protocol. Often utilized in small-to-medium-scale process automation applications it is well known for its simplicity. Using the TCP/IP stack Layer 4 of the OSI model, it enables consistent point-to-point communication via a client-server design.
It’s ideal for:
- Process control systems
- Applications with low-speed data exchange needs
- Environments with lowl real-time performance requirements
Understanding the Modbus Communication Protocol: Modbus Communication Protocol
Protocol Overview – Profinet
Developed by PROFIBUS & PROFINET International (PI), Profinet (Process Field Net) is a contemporary industrial Ethernet standard built for deterministic and real-time communication. From basic sensor communication to high-speed motion control, it is appropriate for all. It supports isochronous real-time (IRT) and real-time (RT) classes of communication.
Profinet is ideal for:
- Factory automation
- Motion control systems
- Applications demanding precise timing and extensive diagnostics
- Future-ready Industry 4.0 and IIoT environments
Exploring Industrial Communication Protocols: Connecting the Industrial World: An Exploration of Communication Protocols in Automation and Instrumentation
Factor 1. Performance and Timing
Usually, Modbus TCP/IP updates in the tens of milliseconds. Many monitoring applications find this to be acceptable, but for high-speed or synchronized control jobs it is not enough.
Profinet offers microsecond-level determinism, particularly with IRT. It allows exact device synchronisation, which is very necessary for coordinated motion control in robots, packing lines, and CNC machines.
Feature | Profinet | Modbus TCP/IP |
Update Time | As low as <1 ms (IRT) | ~10–100 ms |
Determinism | High (IRT) | Low |
Synchronization Support | Yes (with IRT) | No |
Modbus vs. Modbus Plus Explained: Difference between Modbus & Modbus Plus
Factor 2. Communication Model
Using a client-server or polling technique, Modbus TCP/IP has the client constantly asking the server (device) for data. In high-demand networks, this is inefficient and increases traffic overhead.
Reducing bandwidth use and delay, Profinet uses cyclic and event-driven communication in a provider-consumer architecture. Devices can report only when changes take place, hence enhancing general network efficiency.
Top Industrial Protocol Interview Questions: Industrial Communication Protocol Interview Questions and Answers
Factor 3. Diagnostics and Maintenance
Modbus TCP/IP provides simple diagnostics. Though it lacks thorough error reporting, it can indicate connection problems or timeouts.
Profinet has built-in diagnostics on the process, device, and network levels. It is beneficial:
- Asset management
- Diagnostic alarms
- SNMP (Simple Network Management Protocol)
- HTTP-based diagnostics
- LLDP (Link Layer Discovery Protocol) for topology detection
These characteristics significantly ease troubleshooting and maintenance, hence lowering system downtime.
Factor 4. Motion Control and Synchronization
With exact synchronization of several axes or devices, Profinet IRT appears in time-critical motion control applications. It is applied in: Servo systems
- Servo systems
- Robotics
- Conveyor synchronization
- Machine vision timing
These jobs are not appropriate for Modbus TCP/IP since it lacks synchronization and isochronous capabilities. It might be enough for setting speed references or turning motors on/off, but not for coordinated movement.
Step-by-Step Modbus Troubleshooting Guide: Step by Step Procedure for :Troubleshooting
Factor 5. Data Handling and Representation
Modbus TCP/IP is easy to use and limited in data form.
It manages:
- Coils (single bits)
- Registers (16-bit integers)
- Discrete inputs
- Holding registers
Profinet enables rich and flexible data structures including:
- Bits, bytes, words, doublewords
- Real numbers (floating-point)
- Strings
- Complex structured data types
Profinet’s GSD (General Station Description) file standardizes and simplifies configuration by defining a device’s data format and communication capabilities.
Essential Modbus Interview Q&A: Modbus Interview Questions and Answers: Essential Knowledge
Factor 6. Network Architecture and Scalability
Modbus TCP/IP, while functional, has limitations when dealing with big networks. It’s most appropriate for tiny, point-to-point or small star topologies.
Profinet is scalable to hundreds of devices and supports a variety of topologies, including ring, line, and star. It handles complex automation hierarchies with ease and supports:
- Media redundancy
- Controller redundancy
- Line topology with daisy-chained devices
- Integration with higher-level MES/ERP systems
Guide to OT Cybersecurity Protocols: Protocols and Standards in Industrial Automation: A Guide to OT Cybersecurity
Factor 7. Configuration and Setup
Modbus TCP/IP: Programmed Communication
Usually, Modbus TCP/IP communication calls for PLC code writing using communication blocks or instructions (e.g., MSG instructions in Allen-Bradley PLCs). This calls for more testing and development.
Profinet: Configured Communication
The majority of Profinet’s communication is configured rather than programmed. Reading the device’s GSDML file, the engineering tool (e.g., TIA Portal, Studio 5000) allows for simple device addition and mapping with little scripting.
Manual programming is only necessary in exceptional circumstances, such as sophisticated motion applications.
Factor 8. Redundancy and Reliability
Profinet supports:
- Redundancy in media (MRP rings)
- Redundancy of controllers/devices
- Devices that can be hot-swapped
Modbus TCP/IP provides not much redundancy. Failover usually calls for human scripting or third-party tools.
Comparing Modbus Serial and TCP/IP: MODBUS SERIAL VS MODBUS TCP/IP
Factor 9. Future Readiness and Features
Profinet supports advanced features:
- PROFIsafe (functional safety)
- Fast start-up
- Time-Sensitive Networking (TSN)
- Advanced Physical Layer (APL)
- OPC UA integration
- Seamless IIoT and Industry 4.0 compatibility
Modbus TCP/IP purposefully keeps its simplicity. To ensure backward compatibility, the protocol has stayed mostly unchanged.
Factor 10. Standards, Certification, and Support
Profinet
- Extensive global support
- 160Over 1600 member firms (Siemens, Emerson, Phoenix Contact)
- 30M+ Profinet nodes installed (as of 2019)
Modbus TCP/IP
- Optional certification
- Supported primarily by Schneider Electric
- About 90 members
- One acknowledged test laboratory
Factor 11. Real-World Applications
Use Case | Profinet | Modbus TCP/IP |
Motion Control | ✔️ | ❌ |
Small Process Applications | ✔️ | ✔️ |
Robotics | ✔️ | ❌ |
Pump & Valve Control | ✔️ | ✔️ |
Safety-Critical Systems | ✔️ (with PROFIsafe) | ❌ |
Large Factory Automation | ✔️ | ❌ |
Factor 12. Interoperability
Gateways are there to connect Profinet and Modbus TCP/IP networks. These are beneficial in brownfield deployments or for combining existing Modbus devices with new Profinet infrastructure.
HMS, Prosoft, and Moxa are among vendors providing dependable protocol converters for smooth integration.
Factor 13. Ethernet Transmission Standards
- IP Layer: Uses IP/subnet/gateway systems to manage device addressing
- TCP Layer: Guarantees data reliability, prevents conflicts
Profinet, on the other hand, can optimize performance and lower latency by using Layer 2 Ethernet (IEEE 802.3), hence avoiding TCP/IP for real-time communication.
Factor 14. Security
Modbus TCP/IP:
Modbus TCP lacks built-in security structures. Without encryption or authentication, it sends data in plain text, therefore exposing itself to attacks like spoofing, illegal access, and data manipulation. Firewalls, network segmentation, or VPNs must be used to externally manage security, hence adding implementation effort and complexity.
PROFINET:
PROFINET provides improved security features in line with industrial cybersecurity guidelines. It provides integration with security protocols including SNMPv3, user authentication, access control, VLAN segmentation, PROFINET Security Class 1 and 2 (as specified by PI) aims to stop undesired device access and control supporting safe automation network deployment.
While Modbus TCP calls for more infrastructure to satisfy current security criteria, PROFINET offers a better basis for safe communication in industrial networks.
Profinet vs Modbus TCP/IP – Summary Comparison Table
Category | Profinet | Modbus TCP/IP |
Ethernet IO | Yes | Yes |
Motion Control | Yes | No |
Peer-to-Peer | Yes | No |
Functional Safety | Yes (PROFIsafe) | No |
Integrated Buses | PROFIBUS, AS-i, DeviceNet, etc. | Modbus only |
Communication Model | Provider-Consumer (full duplex) | Client-Server (half duplex) |
Real-Time Options | RT, IRT (IEEE 802.3) | TCP/IP only |
Typical Jitter | Low (<1ms) | High (~100ms) |
Transmission Type | Unicast & Multicast | Unicast only |
Network Management | DCP, SNMP, LLDP, DHCP, Topology tools | Vendor-specific/manual |
Device Diagnostics | Built-in, detailed, SNMP, LLDP | Minimal, protocol timeout only |
Redundancy | Controller & Media redundancy | Limited / None |
Scalability | High (hundreds of nodes) | Moderate (limited by polling model) |
Future Readiness | IIoT, OPC UA, TSN, APL, Industry 4.0 | Limited advancement |
Certification | Mandatory by PI labs | Optional/self-certified |
Global Support | 1600+ companies, certified centers | Limited, Schneider-backed |
Typical Applications | Factory, process, motion, robotics | Process, small-scale control |
Which Is Better, PROFINET Or Modbus?
Profinet is especially the clear victor for high-performance, real-time applications in modern factories and integrated systems requiring advanced diagnostics, motion control, and future-proof scalability. Designed for the future of automation, it is feature-rich and sturdy.
Modbus TCP/IP is still a consistent, simple, and strong protocol for many process control systems especially those without fastness and determinism.
Bottom line: Use Profinet if you need performance, precision, and long-term scalability. Use Modbus TCP/IP when simplicity, reliability, and straightforward integration are most crucial.
What is the difference between Modbus and PROFINET?
While Modbus is easier, more frequently used, and perfect for basic data transfer in less time-sensitive situations, PROFINET offers sophisticated diagnostics and standardized GSD files for simple device integration.
What is the difference between PROFINET and TCP/IP?
TCP/IP is meant for generic data transfer. Built on Ethernet, PROFINET provides deterministic, real-time communication, therefore perfect for industrial automation with tight timing and dependability criteria.
Can PROFINET communicate with Modbus?
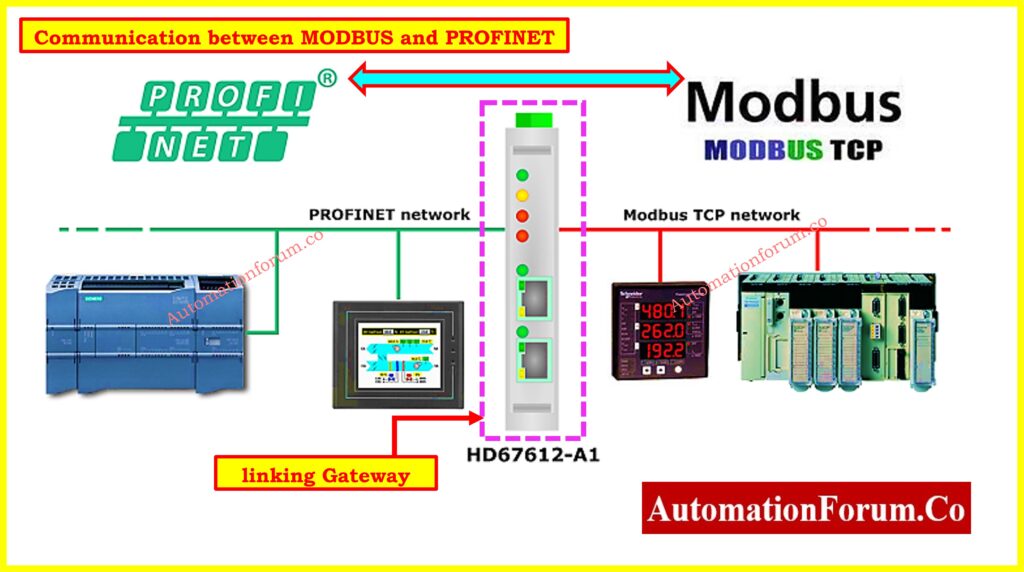
Yes, Protocol gateways allow PROFINET and Modbus devices to communicate, hence facilitating smooth data transfer between the two separate network standards.
Can I use PROFINET and Modbus TCP on the same network?
Which protocol offers better security PROFINET or Modbus TCP/IP?
While Modbus TCP has no built-in security, making it more susceptible until additional defenses like firewalls or VPNs are used, PROFINET has improved security features including user authentication, VLAN support, and access control.
MODBUS Protocol Quiz :Test Your Knowledge
Refer the below link to test your knowledge in MODBUS communication Protocol