What is a controller?
The controllers are the major controlling element in a process in a control system. So in a control system, the controller would compare the controlled value to the required value and if there is an error or deviation from the required value the controller would correct it. The controller would receive the error in some form and it would do the proper control function. The controller would maintain the process variable such as temperature, pressure, flow rate, etc to a required level. The controller would transfer the output after the correction to the final control element and thus the required set point can be achieved. The controller is the major part of the control system. The controllers are used in the process plant to modify the system parameters and also to make the system stable.
- What is cascade control?
- What is a feedback control system and what are its types?
- What is an automatic control system?
- What is industrial control system (ICS)
- What is mimic panel?
- What is Protective system Override ? & What is Protective Override switch (POS)?
- How a Valve is controlled using a 4-20mA loop
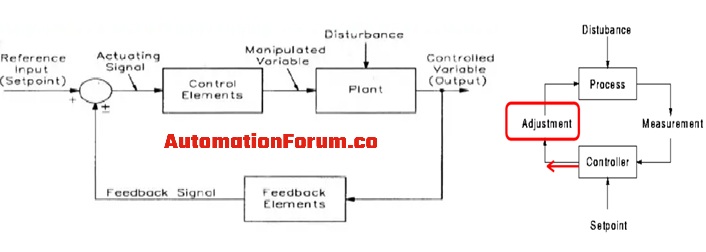
What are the major parts of a controller?
- The controller has a measuring unit with certain instruments and with the help of these instruments the controller can measure the process state like the temperature, pressure, etc
- There will be an input set-point device to set the required value
- A comparator which would compare the measured value to the required value
- There is a control unit to calculate the output magnitude and direction so that it can compensate for the deviation from the required value
- There are certain output units in the controller such as the control valve, motor to convert the output to physical action.
What are the functions of a controller?
The controller plays an important role in a control system, the control system would do the comparison, measurement, computation, and correction of the process variable. The correction and comparison are completely done by the controller. After clearing the error the output will be sent to the final control element and this will be done with the help of a controller. The control mechanism of the controller consists of two sections the comparator and the controller.
How does a controller work?
The controller would receive the output from the feedback system, so it would compare the output to the required value and if it deviates from the required value then the controller would do certain actions to get the required value. The output is sensed by the sensors in the feedback system and it would be converted to a proper feedback signal. The reference input is the setpoint value, the error detector would compare the feedback value to the reference value.
What is a variable range and controller output range?
The controlled variable has a range of values in a control system, these values would maintain the control. The control variable can be specified as some nominal values and plus-minus tolerance and this range is required for the design of the controller. The range is associated with the controller output variable and they have maximum and minimum values. The output of the controller is in percentage the minimum output is zero percent and the maximum output of the controller is a hundred percent. The zero-percent output of the controller is not a zero output.
What is the control lag and dead-zone in a controller?
The control lag is the time required for a controller to make the required changes in order to receive the output at its setpoint. The dead zone is the time that has gone between the instant where the error occurs and the instant when the first corrective action takes place.
What are the types of controller?
There are continuous and discontinuous controllers, the discontinuous controller is further classified as an on-off controller and a multi-position controller. The continuous mode controllers are proportional control, integral control, and derivative control.
ON-OFF CONTROLLER
We can control the process variable with this type of controller. This is the old method of controlling the process, a switch will be used to do the on, off control. This is a discontinuous form of control action and this is also called a two-position control. The On-off controller will be on if the measurement is below the setpoint and the manipulative variable is at its maximum value. So if the manipulative variable is above the setpoint then the controller is off, and the manipulative variable will be minimum. This type of controller is used in industrial and domestic applications. The controller gain of this controller is really good.
The On-off control would only respond if there is an error and this type of controller is not suitable for continuous automatic feedback control. We can use the on-off controllers for the system that doesn’t need accurate control, it can also be used in systems that can handle the on and off frequently, and it can also be used where the mass of the system is great.
Advantages
- These controllers are simple and inexpensive
Disadvantages
- They are not versatile and also ineffective
- Flow rate control is not possible
- This type of controllers has very limited applications
Proportional controller
This is a continuous type of controller, this type of control system is more complex than the discontinuous control system. In this type of control, the controller would create an output signal and it will be proportional to the error. So if the error magnitude is high then the corrective action which is applied will be large too. The proportional control can remove the cycling which can be seen in the on-off control. If the output reaches the setpoint then the proportional controller would decrease the average power supplied to the system. So due to this the system will slow down and it won’t overshoot the setpoint but it will reach the setpoint and can maintain a stable output. The on-off controller can only be used in a system that has a long response time, but it can’t be used in systems which has rapid response time. So in this place, we can use a proportional controller, the output will be made as a continuously variable value.
The gain in the proportional controller can also be referred to as sensitivity, it compares the ratio of the amount of change in the final control element to the amount of change in the controlled variable. In the proportional control, the gain of the controller gain can be varied in order to change the controller output
Advantages of proportional controller
- It can reduce the steady-state error and thus it can make the system stable
- The over-damped system would have a slow response and by using this controller we can make it fast.
- In this type of controller, the steady-state error is inversely proportional to the proportional gain so if the gain is made larger then the error will become low.
Disadvantages of the proportional controller
- These controllers would increase the maximum overshoot of the system
- It can only be used in case if the deviation is not large and because of this it can only be used in a system that has less deviation between the input and output
- It can’t be used where the deviation is sudden
- There will be some offsets in the system because of the proportional controller
Integral controller
In this type of controller, the output will be directly proportional to the integral of the error signal. The major disadvantage of the proportional controller is that it cannot cancel the error it would finally have an offset error. If the load changes then the output will vary from the setpoint and this type of error is called an offset error. So this controller would respond to error which would build up over time, so because of this feature, these controllers are able to remove the error quickly. The integral control can be used to cancel the offset of a system, this control is always used in conjunction with the proportional control.
Advantages of integral control
This type of controller can return the controlled variable to the setpoint, following a disturbance and because of this, it is called a reset controller.
Disadvantages of integral control
It could make the system unstable because it would act slowly to an error
Derivative control
The derivative control can determine the error signals’ future behavior and it is done by considering the rate of change. The controller could act according to the error if the error is small and if it is not increasing quickly this information will be used by the controller to decrease the control signal and thus the control actions can be limited. In this type of control, the output of the controller is dependent on the time rate of change of the actual error. The major feature of this type of control is that according to the rate of change in error signal there will be a unique value of controller input.