- What is Ratio Control?
- Applying Ratio Control
- Explanation of Ratio Control in Combustion Systems
- Understanding the Diagram of Ratio Control in Combustion Systems
- Key Features of Ratio Control in Combustion
- Benefits of Ratio Control in Combustion
- Ratio Control Loop for Three Streams (A:B:C = 1:2:10) – Example Scenario
- Practical Applications of Combustion System Ratio Control
- Advantages of Ratio Control
- Disadvantages of Ratio Control
- Frequently Asked Questions (FAQ) on Ratio Control
- What is ratio control?
- What does “ratio of control” mean?
- What is a ratio control valve?
- What is the difference between cascade control and ratio control?
What is Ratio Control?
A ratio controller is a special type of feed forward controller where disturbances are measured and their ratio is held at a desired set point by controlling one of the streams.
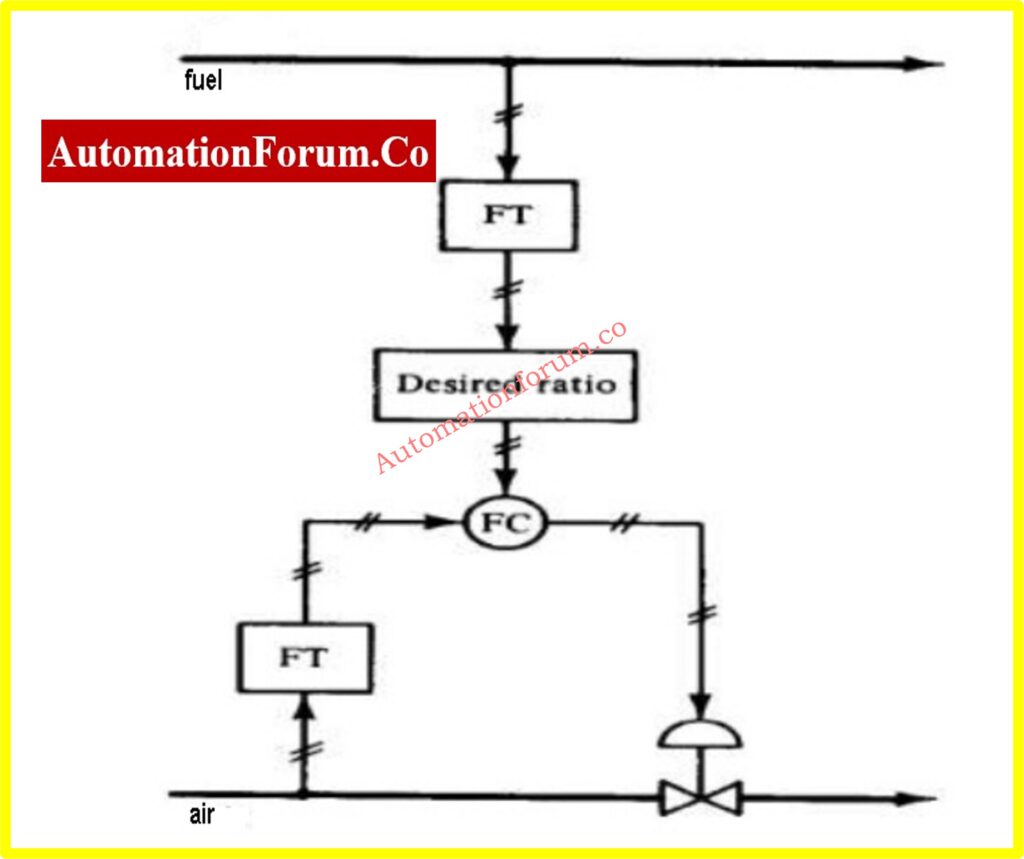
Ratio control is used when two fluids must be mixed together in a specific ratio. A practical way to do this is to use a standard control system to control the flow on one line. The same transmitter signal is used as a set point for a second controller which controls the flow in a second line. The ratio of one flow rate to the other can be changed by adjusting the gain (or proportional band) of the secondary controller. Figure shows a typical ratio control system. The air to fuel ratio of the fluid going to the combustion chamber is set at 2:1.
Applying Ratio Control
You can get a much better grasp of ratio control by considering some specific examples. Assume we want a “blender,” that is, to blend two streams, A and B, in a proportion or ratio R:
R=B/A
An example for ratio control is given in figure below, the wild flow A is measured, and then it is multiplied by R to get the required value of B. Thus, as the flow A varies, the set point to the flow
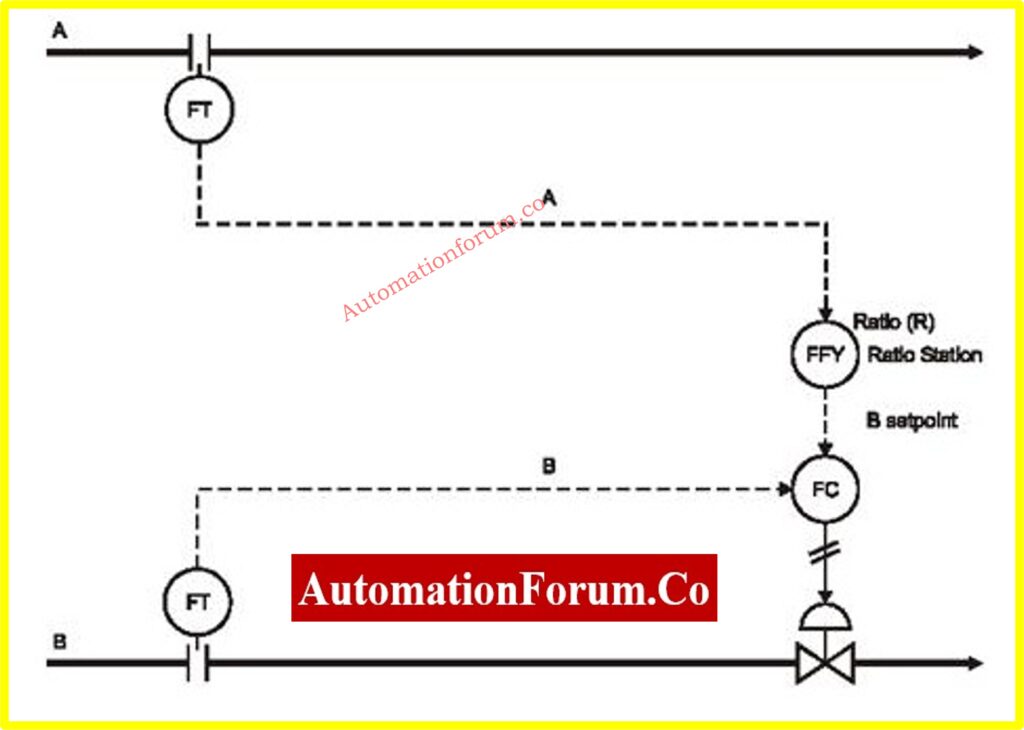
Controller of stream B will vary to maintain R. If a new value of R is desired, it must be set into the ratio station. Differential-pressure sensors are shown measuring flow; their output indicates the square of flow and, therefore, square root extractors are shown to obtain flow. By using flow, and not its square, the loops will behave more linearly and thus will be more stable and easier to tune.
Explanation of Ratio Control in Combustion Systems
Definition of Ratio Control
Ratio control is a type of control strategy used to maintain a fixed relationship between two process variables. In combustion systems, it ensures the correct proportion of air and fuel is supplied to the combustion chamber to optimize efficiency, minimize emissions, and maintain safe operation.
Purpose in Combustion Systems
In a combustion process, maintaining the proper air-to-fuel ratio is critical:
- Excess Air: Too much air leads to heat loss and reduces system efficiency.
- Insufficient Air: Too little air results in incomplete combustion, causing higher emissions and unsafe operation.
The ratio control system adjusts the fuel flow to match changes in air flow (or vice versa) to maintain the desired ratio.
Understanding the Diagram of Ratio Control in Combustion Systems
Air Flow Measurement and Control
- The flow transmitter (FT) measures the air flow entering the system.
- The signal from the FT goes to the air flow controller (FIC).
- The air controller is configured with proportional band (PB) = 50% and gain (G) = 2, ensuring fast response and precise control.
- The air controller sends its output signal to the final control element (FY), which drives the air control valve.
Fuel Flow Measurement and Control
- The fuel flow is controlled using a separate FIC.
- The setpoint of the fuel FIC is derived from the output of the air FIC. This ensures the fuel flow follows the air flow to maintain the desired ratio.
- The fuel controller has PB = 100% and G = 1, indicating slower response compared to the air control loop.
- The fuel controller’s output adjusts the fuel valve via its final control element (FY).
Ratio Adjustment
- The relationship between the air and fuel flows is pre-set in the air-to-fuel ratio controller.
- If the air flow changes (e.g., due to varying combustion demand), the air FIC immediately adjusts its valve, and the fuel FIC follows suit to maintain the specified ratio.
Key Features of Ratio Control in Combustion
Master-Slave Control:
The air controller acts as the master loop, while the fuel controller serves as the slave loop.
Tuning:
The air control loop is tuned to respond more quickly than the fuel loop to ensure stability and avoid overcorrection.
Proportional Band (PB):
A smaller PB for air flow (50%) results in tighter control, while a larger PB for fuel (100%) ensures smoother adjustments.
Gain (G):
Higher gain for the air loop ensures sensitivity to changes, while lower gain for the fuel loop avoids oscillations.
Benefits of Ratio Control in Combustion
- Efficient Fuel Usage: Ensures the optimal amount of fuel is used for the given air flow.
- Reduced Emissions: Prevents incomplete combustion and minimizes pollutant generation.
- Stable Operation: Prevents process disturbances from causing unstable combustion.
- Safety: Maintains a safe and controlled combustion environment by avoiding excessive air or fuel supply.
Ratio Control Loop for Three Streams (A:B:C = 1:2:10) – Example Scenario
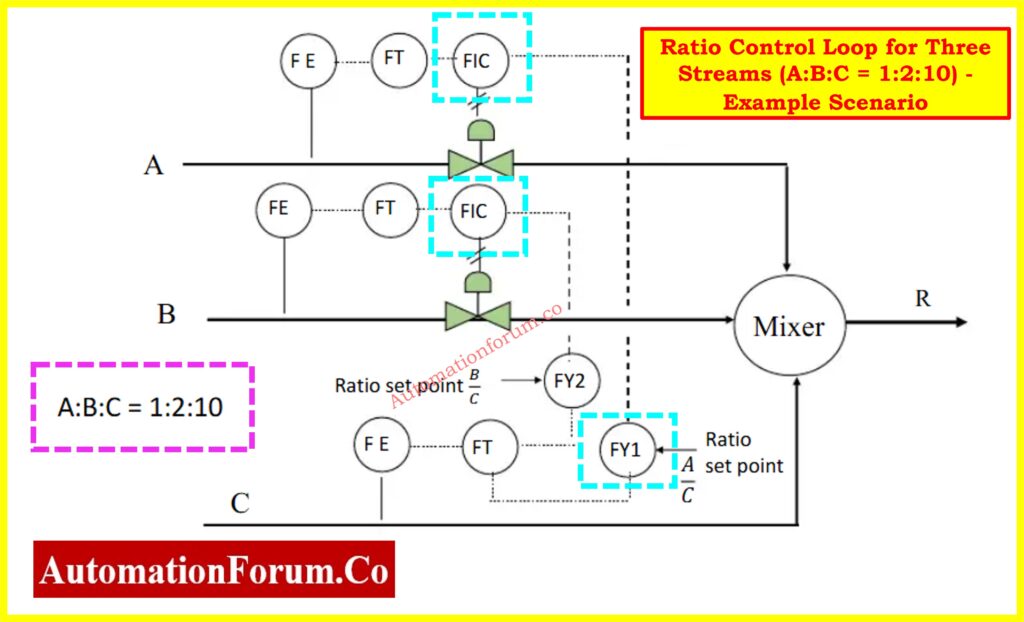
This above diagram illustrates a ratio control loop for three input streams (A, B, and C) going into a mixer. The control objective is to maintain the flow ratio of A:B:C = 1:2:10. Here’s a breakdown of how the control loop works:
Process Description:
We have three process streams, A, B, and C, entering a mixer. The goal is to maintain the mixing ratio such that:
- A : B : C = 1 : 2 : 10
This means that for every 10 units of stream C, there should be 2 units of stream B and 1 unit of stream A.
Control Strategy:
1. Master Stream:
- Stream C is chosen as the master stream. Its flow is measured using a flow transmitter (FT).
- The flow rate of stream C acts as the basis for calculating the required flow rates of streams A and B.
2. Ratio Computation:
- The flow rate of stream C is multiplied by the appropriate ratio values to generate setpoints for streams A and B.
- These calculations are handled by ratio computing elements (also called ratio stations or function blocks).
- For stream A:
- Setpoint = (1/10) × Flow of C
- For stream B:
- Setpoint = (2/10) × Flow of C
- For stream A:
3. Slave Streams:
- Streams A and B are considered slave streams.
- Each has its own flow control loop, which includes:
- A flow transmitter (FT) to measure the actual flow.
- A flow controller (FIC) to compare actual flow to the setpoint.
- A control valve to adjust the flow based on the controller output.
- The setpoints for the FICs of streams A and B come from the ratio calculation units.
4. Mixing:
- After passing through the control valves, all three streams enter a common mixer.
- The output from the mixer is the final mixed stream, R, which has the ratio A:B:C maintained at 1:2:10.
Summary of Control Loop Components
Stream | Function | Control Logic |
C | Master stream | Flow measured and used for ratio basis |
A | Slave stream | Setpoint = (1/10) × Flow of C |
B | Slave stream | Setpoint = (2/10) × Flow of C |
Mixer | Final mixing point | Combines A, B, and C into ratio-controlled R |
Advantages of Ratio Control:
Minimizes waste and reduces the need for manual adjustments.
Ensures consistent product quality by maintaining correct proportions of input materials.
Automatically compensates for fluctuations in the master stream’s flow.
Practical Applications of Combustion System Ratio Control
- Industrial boilers.
- Gas turbines.
- Furnace systems.
- Power plants requiring precise air-fuel control to meet environmental and operational standards.
Advantages of Ratio Control
- Enables users to link two streams effectively and maintain a specified ratio between them, ensuring consistent output quality or system performance.
- The control system is straightforward to implement and operate, making it suitable for various industrial applications without requiring extensive technical expertise.
- Does not require complex mathematical models or algorithms, simplifying system design and maintenance.
- Due to its simplicity, ratio control often involves lower implementation and maintenance costs compared to advanced control strategies.
- Ensures consistent process behavior by maintaining the desired relationship between two variables, which is critical in blending, mixing, and proportional control applications.
- Responds rapidly to changes in flow rates or other inputs, allowing for real-time adjustments to maintain the desired ratio.
Disadvantages of Ratio Control
- Ratio control is most effective when applied to flow rates. For other process variables, its usefulness may diminish, especially if the relationship between variables is nonlinear or unstable.
- The effectiveness depends on a clearly defined and stable ratio relationship between the controlled variables, which may not always hold true in complex or dynamic systems.
- Changes in the ratio may lead to unintended consequences in one of the streams, as individual control of the streams is often not possible.
- Accurate measurements of the controlled variables are crucial. Errors in flow meters or sensors can lead to incorrect ratio control, affecting process performance.
- Processes with frequent changes in dynamics or interactions between variables may require more advanced control strategies.
- Ratio control focuses only on maintaining the specified ratio. It does not account for external disturbances or deviations in process conditions, which may affect the system’s overall stability.
Frequently Asked Questions (FAQ) on Ratio Control
What is ratio control?
Ratio control is a type of feed-forward control strategy designed to maintain a constant ratio between two process variables, typically flow rates. This ensures that disturbances in one variable are compensated by proportional changes in the other. Common applications include:
- Maintaining reactant ratios in chemical reactors.
- Controlling the reflux ratio in distillation columns.
- Adjusting the fuel/air ratio in burners for optimal combustion.
What does “ratio of control” mean?
The “ratio of control” refers to the specific proportional relationship that is maintained between two process variables. For example, in blending operations, it could be the ratio of one fluid’s flow rate to another.
What is a ratio control valve?
A ratio control valve is a specialized device used to maintain a fixed ratio between two fluids without requiring an external power source. It operates by balancing fluid pressures:
- The pressure from the reference side acts on a bellows mechanism.
- The valve adjusts so that the pressure on the other side is consistently higher by a specific amount, determined by a setting spring.
What is the difference between cascade control and ratio control?
Ratio Control: This method focuses solely on maintaining a predefined ratio between two process variables (e.g., flow rates). Unlike cascade control, it doesn’t rely on nested loops but directly adjusts one variable to match the desired ratio relative to the other.
Cascade Control: This approach uses multiple nested control loops. The inner loop addresses rapid disturbances affecting one variable, while the outer loop manages another variable to achieve overall stability.