- What is a level sensor ?
- Classification of a level sensor according to the sensing point
- What are the different types of level measurement?
- Direct level sensor
- Indirect level sensors
- Direct level sensing methods
- Indirect level sensing methods
- How to select a level sensor?
- Level Sensor Classification
- Point Level Measurement Sensors
- Continuous Level Measurement Sensors
- Differences in Level Sensing Methods
- Advancements in Level Sensing Technology
- Comparison of Level Sensor Types: Contact vs. Non-Contact Methods
- What are the classifications of level sensors?
- What types of sensors are used for point level measurement?
- What types of sensors are used for continuous level measurement?
- What is the most common type of level sensor?
- What are the 4 main types of level sensors?
- What is the theory behind level sensors?
- What are liquid level sensors?
- How do liquid level sensors work?
What is a level sensor ?
Level sensors are devices that are used to measure the substances, such as water, oil, slurries, dust particles, solids, etc. The medium which is to be measured could be stored in a vessel, bins, silos, etc. The liquid level is the position of a liquid surface above or below a reference point. These sensors are also capable to detect the powder levels and also the interface between the liquids. Level sensors are required for many industrial applications and they are inevitable in fluid systems. The liquid which is to be measured could be in a tank or it would be in natural forms like a lake or river. The variation in the fluid level could be sensed by the level sensor and it would transmit this info to the operator.
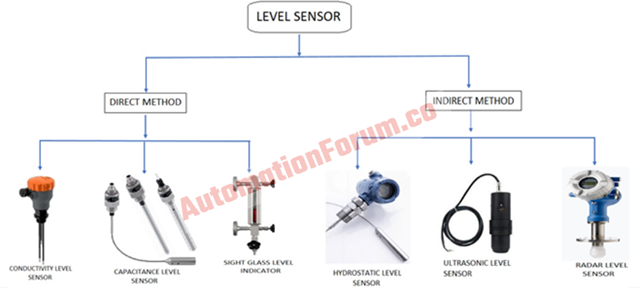
Classification of a level sensor according to the sensing point
Level sensors are classified according to the number of locations where the fluid measurement is to be done.
Single point level sensor
This type of sensor is used for single location measurement of the fluid.
Multi-point level sensor
This type of sensor is used in multiple locations to do the level measurement of the fluid.
Continuous level sensor
This type of level sensor is used where the level measurement at all locations must be done.
What are the different types of level measurement?
Direct level sensor
This type of level sensor would detect the surface or interface of the liquids and the variation in the density of the measured substance won’t affect the measurement.
Types of the direct level sensor
- Floats
- Displacer switch
- Sight glass
- Capacitive level sensor
- Conductivity level sensor
- Vibration level sensor
- Potentiometric level sensor
Indirect level sensors
In this type of level measurement, the measurement of the liquid level is done by measuring certain parameters such as pressure, temperature, weight, etc. This parameter would be calculated to determine the fluid level.
Types of indirect level sensors
- Ultrasonic level sensor
- Hydrostatic level sensor
- Magnetic level sensor
- Radar level sensor
- Radiometric level sensor
- Thermal dispersion level sensor
Direct level sensing methods
1. Float type
In this type of level measurement, a buoyant object will be placed between the fluid which is to be measured and also the headspace vapor in the tank. The float would sink to the bottom of the fluid and then it would float on the top of the fluid which is to be measured. The float level sensor is composed of a magnet and also a magnetic reed switch, the float would vary its position according to the change in the liquid. The reed switch would open or close and it is dependent if it is in the air or in liquid.
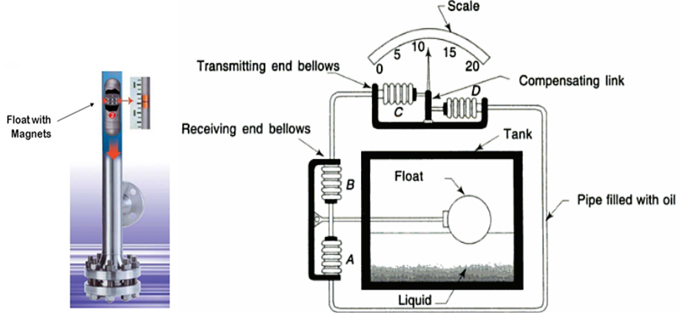
Advantages of float level sensor
- It is accurate
- It can be used with different fluid densities
Disadvantages of float level sensor
- It can’t be used with dirty fluids
- The measurement is possible if there is a large amount of liquid
- Big size
Applications of float level sensor
- Tank level measurement
- It can be used to measure the level of water, oil, hydraulic fluids, and chemicals
2. Displacer switch
In this type of level sensor, a displacer is used and spring would be connected to the displacer. So the displacer would be immersed in the fluid which is to be measured and this would change the buoyancy force. Due to this the force that acts on the spring would vary and thus the spring would compress. This is similar to the float switch and it has a magnetic sleeve and this would be attached to the spring so when the spring moves the magnet would move along it and thus switching would be done.
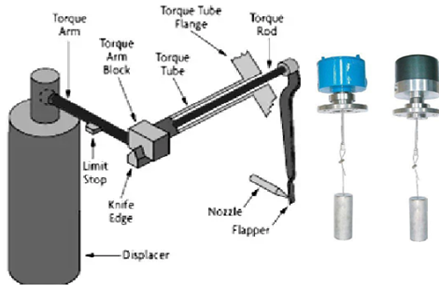
Advantages of displacer switch
- It can be used for high temperature and pressure
- Less movement of the displacer
Disadvantages of displacer switch
- Fluid density change would affect the measurement
- It is mostly used with small tanks
Applications of displacer switch
- Heavy oils
- Liquids with solids
- Paints
- Dirty liquids
3. Sight glass
In this type of level measurement, a glass gauge is used and it will be placed close to the pressurized tank. This glass tube will be connected to the tank at the bottom with proper fittings so that the pressure could be retained. The liquid in the vessel could be bypassed through a transparent tube. We can directly observe the liquid level through the sight glass, the liquid level in the glass gauge would be the same as the tank.
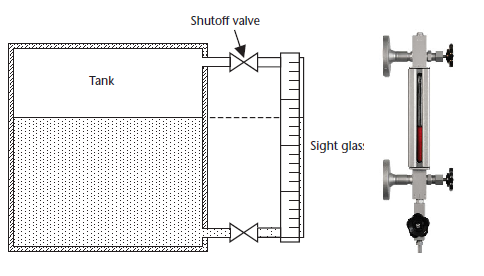
Advantages of sight glass level measurement
- Cheaper
- Direct reading
Disadvantages of sight glass
- It can only be used with clean liquids
- Only non-corrosive liquids can be measured
- It can’t be used with dangerous process fluids
Applications of sight glass
- Food and beverage
- Lubricating oil
4. Capacitive level sensor
This type of level measurement is a continuous level measurement and a capacitance probe is used for this measurement. The probe will be placed inside the tank, the metal wall of the tank, and the probe would act as two capacitor plates. The media which is to be measured is dielectric, so the capacitance value would change by varying the dielectric. So when the fluid level in the tank changes then the dielectric constant would change and thus the capacitance would vary.
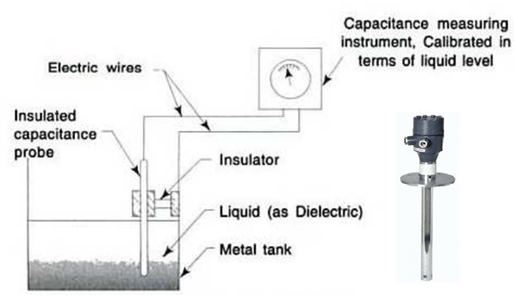
Advantages of capacitance level sensor
- It can be operated in high temperature and pressure
- Can be used with solids and slurries
- It can be used with mixed materials
- It would give continuous indication
Disadvantages of capacitance level sensor
- It can’t be used with varying dielectric materials
- It can’t be used with media that coats the sensing element
- Measurement is affected by the variations in temperature
Applications of capacitance level sensor
- Chemical
- Food and brewery industries
- Slurries
- Liquids with solid particles
5. Conductivity level sensor
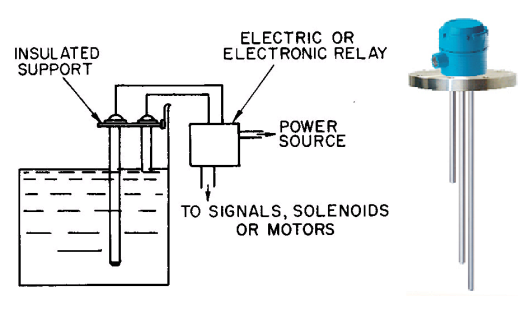
In this type of level measurement, the fluid conductivity is utilized to do the measurement. Two conductive probes are used in this one of them is a short probe so when the fluid is not in contact with the probe then the electrical resistance between the probe and the and vessel would be really high. But when the fluid level increases and covers the probe then the circuit will be completed between the vessel and the probe, thus the circuit resistance would be lowered.
Advantages of the conductive level sensor
- No moving parts
- Easy to use
- Low cost
Disadvantages of the conductive level sensor
- Invasive (contact level measurement)
- It can only be used with conductive liquids
- The probe could erode during time
Applications of the conductive level sensor
- Level measurement of boiler water
- It can be used with highly corrosive liquids
- Reagent monitoring
6. Vibration
This type of level sensor uses a tuning fork to do the level measurement, so when the media comes in contact with the blade or fork then a relay contact switch would be tripped. The relay would be switched according to a high, or low level. This device also consists of a piezoelectric element to pick up the frequency of the vibrating fork. So the level measurement is done according to the change in frequency.
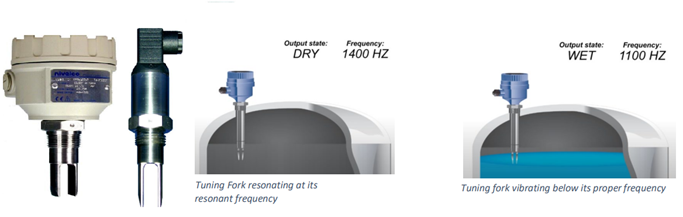
Advantages of vibration level sensor
- It can be used for solid and liquid level control
- It can be used with media that exhibit sticky properties or foam
- Compact
- It is independent of the media characteristics
Disadvantages of vibration level sensor
- It can’t be used for continuous level measurement
Applications of vibration level switch
- It is used to control the maximum amount of solids and liquids in many applications such as grains, cement, granules, powder
- Food and beverage
7. Potentiometric level sensor
This type of level measurement is done by measuring the voltage ratio change between the measurement rod and tank wall which contains the process fluid. The measurement rod or the probe would be immersed in the process media and this measurement tube has low resistance. AC power will be transmitted to the probe from a power source. The voltage ratio between the tank wall and the probe will be taken to determine the level.
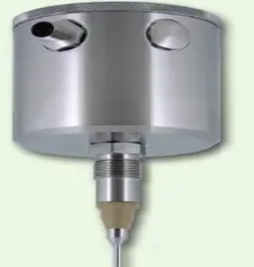
Advantages of the potentiometric level sensor
- Level monitoring in metallic pipes
- It can be used to do the level control of paste or adhesive media
- It can be used to do the level measurement of small tanks
Disadvantages of the potentiometric level sensor
- A specified amount of conductivity is required for the media
- It can’t be used in explosive areas
Applications of the potentiometric level sensor
- It can be used with sticky or foaming media
- Level monitoring in the process tank
- Level detection in cream production
Indirect level sensing methods
1. Ultrasonic level sensor
This type of level sensor can be used to do the noncontact level measurement. This sensor would transmit high-frequency ultrasonic signal waves and it would be reflected back from the media which is to be measured. So the time taken by the waves to reflect back from the media is calculated and thus the level can be determined.
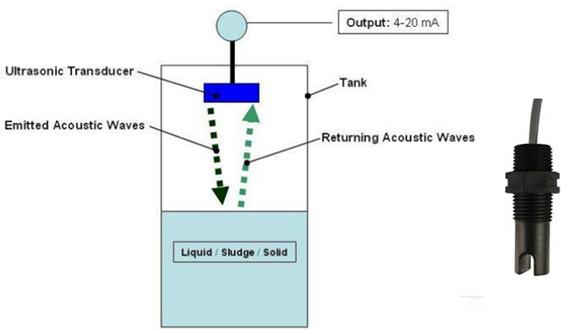
Advantages of the ultrasonic level sensor
- Non-contact level measurement
- Compact
- Measurement is not affected by the type of media which is to be measured
Disadvantages of the ultrasonic level sensor
- Costly
- High pressure and temperature could affect the measurement
- Reflections could happen due to agitation
- Foam, steam, change in concentration would affect the measurement
Applications of the ultrasonic level sensor
- Measurement of high viscous fluids
- Measurement of bulk solids
- Water treatment applications
2. Hydrostatic level sensor
This type of level sensor is the submersible type and the level measurement is done by measuring the hydrostatic head which is created by the liquid column. In this measurement, a pressure sensing element is utilized and this sensor would be placed under the bottom of the tank. This sensor would determine the tank pressure and this pressure will be proportional to the liquid level.
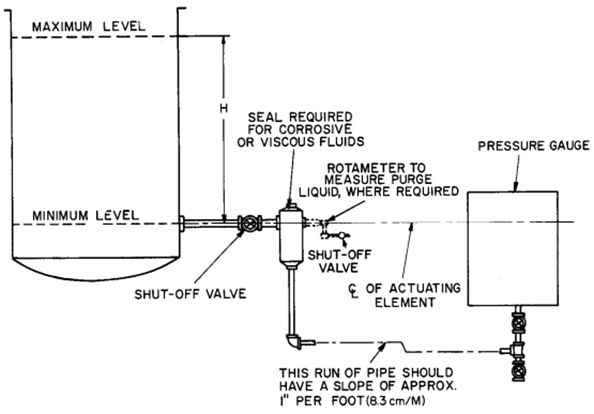
Advantages of the hydrostatic level sensor
- Reliability
- Measurement is not affected by the media properties such as foam, vapor, density, etc.
- Easy calibration
Disadvantages of the hydrostatic level sensor
- It can’t be used with bulk materials
- The tank must be emptied to do the sensor maintenance
Applications of the hydrostatic level sensor
- It is used in storage tanks
- Processing vessels
- Measurement of corrosive liquids
3. Magnetic
In this type of level sensor, the sensor would be placed parallel to the tank and this device consist of a column with visual indicators and it would show the level. The device consists of magnetic floats and it would move up and down according to the water level in the tank. This device would indicate the level by using a float that is magnetically coupled to an index or a column of rotating flaps. This magnetic float would also move the visual indicators in the column.
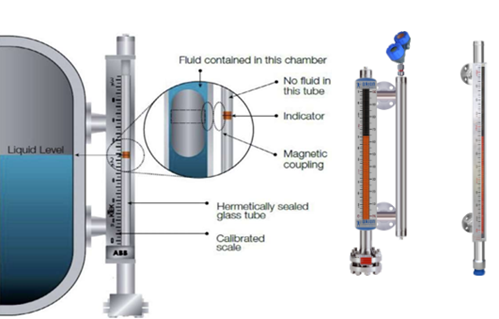
Advantages of the magnetic level sensor
- Visual indication of the level
- The visual indicators are not composed of process fluid that is being measured so there is no risk if the glass breaks
- We can measure the level of colorless fluids
- We can also measure the level of fluids that may foul the sight glass
Disadvantages of the magnetic level sensor
- The float in the magnetic indicator could get stick
- The magnetic float is dependent upon the pressure in the vessel and also the specific gravity of the process fluid
Applications of the magnetic level sensor
- High pressure and high-temperature applications
- It can be used with corrosive liquids
- Mining
4. Guided wave radar
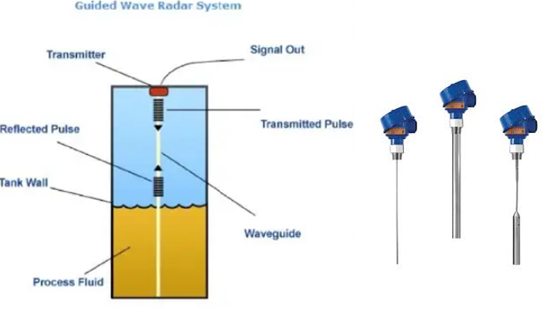
In this type of level measurement, a microwave is transmitted to the process fluid. In the above image, we can see a transmitter that is mounted to the tank, and the transmitter probe would transmit the microwave to the process fluid, a significant proportion of this microwave would be reflected back. The time taken by the wave to reflect back from the fluid is calculated to determine the level.
Advantages of radar level sensor
- High accuracy
- Noncontact measurement
- It can measure level through plastic tanks
- It can be used with all types of liquids
Disadvantages of radar level sensor
- This device is sensitive to the build-up in the sensor face
- Highly expensive
- Limited detection range
Applications of radar level sensor
- It can be used for applications where the temperature and pressure would be a problem
- It can be used in moist, vapor, and dusty environment
5. Radiometric
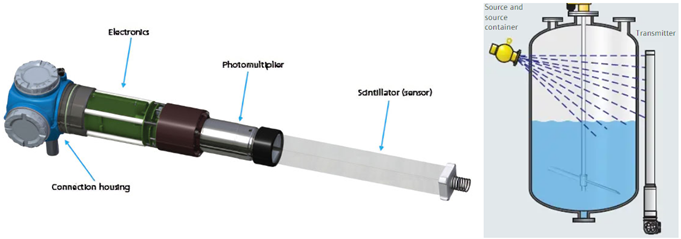
This type of level measurement is done by transmitting gamma source and in order to do that cesium or cobalt isotope is used as the source. So from the source, electromagnetic radiation is transmitted and this radiation is emitted in a way that it would pass through the material to reach the transmitter which is placed on the opposite side of the tank. So the intensity of the received signal is used to determine the level of the process fluid.
Advantages of the radiometric level sensor
- Noncontact measurement
- Safety and reliability
- It can be used in extreme conditions
- Maintenance is not required
Disadvantages of the radiometric level sensor
- Accuracy could be affected by external radiation
- Expensive
- There could be many safety problems due to the radiation
Applications of the radiometric level sensor
- It can be used for high temperature and pressure applications
- It can measure toxic media
- It can be used with high viscous fluids
- It can be used for applications where installation is difficult
6. Thermal dispersion level sensor
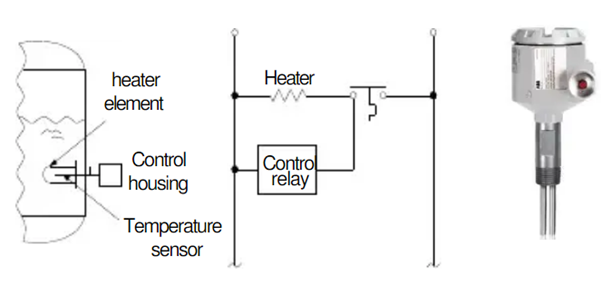
Advantages of thermal dispersion level sensor
- Low maintenance because there are no moving parts
- Good accuracy
- High sensitivity
- It can be used with corrosive and hazardous fluids
Applications of thermal dispersion level sensor
- Hydroelectric plants
- Petrochemical
- HVAC
- Food and beverage
How to select a level sensor?
- It should be selected according to the media which is to be measured like clean fluid, slurries, liquids with solid particles, etc.
- It should be selected according to the temperature and pressure range of applications
- Point or continuous level measurement
- Measurement range
- We must consider if the measured material is electrically conductive
- Does the liquid surface contain turbulence, foam, or vapor
- Contact or non-contact level measurement
Level Sensor Classification
Level sensors are broadly categorized into two types:
- Point Level Measurement
- Continuous Level Measurement
Point level measurement sensors indicate the presence of a product at a specific point, whereas continuous level measurement sensors monitor the level of a product as it rises and falls.
Point Level Measurement Sensors
Capacitance Level Sensor
Capacitance level sensors detect levels by the effect of the material on their electrical field.
Advantages:
- Compact size
- Cost-effective compared to other sensors
- No moving parts
- High accuracy
Disadvantages:
- Require calibration
- Only suitable for certain liquids
- Invasive to the product
Applications:
- Ideal for liquid storage tanks in facilities like water treatment plants.
Optical Level Sensor
Optical sensors measure the level by converting light rays into electrical signals.
Advantages:
- No moving parts
- Unaffected by high pressure or temperature
- Small size
- Suitable for liquid applications
Disadvantages:
- Require cleaning if the lens gets coated or dirty
Applications:
- Used as low-level indicators to prevent dry-run conditions in oil, coolant, or hydraulic systems.
Conductivity (Resistance) Level Sensor
These sensors use a probe with electrodes to detect liquid levels based on conductivity.
Advantages:
- No moving parts
- Low cost
- Easy to use
Disadvantages:
- Invasive (probe touches the product)
- Suitable only for conductive liquids
- Probe erosion over time
Applications:
- Commonly used for signaling high or low levels in various systems.
Vibrating (Tuning Fork) Level Sensor
These sensors use fork-shaped elements that vibrate at a natural frequency, which changes upon contact with the material.
Advantages:
- Cost-effective
- Compact design
- Easy installation
- Maintenance-free
Disadvantages:
- Invasive (must touch the material)
Applications:
- Widely used in mining, food and beverage, and chemical processing industries.
Float Switch
Float switches operate by raising or lowering a float to open or close a circuit.
Advantages:
- No power required
- Provides direct level indication
- Low cost
Disadvantages:
- Invasive to the product
- Moving parts prone to wear
- Larger in size
Applications:
- Ideal for high or low-level indication in liquid storage tanks.
Continuous Level Measurement Sensors
Ultrasonic Level Sensor
Ultrasonic sensors emit and receive ultrasonic waves to measure distance based on the time it takes for waves to reflect back.
Advantages:
- Non-invasive (non-contact)
- No moving parts
- Compact and reliable
- Unaffected by material properties
- Self-cleaning
Disadvantages:
- Relatively expensive
- Environmental factors may impact performance
Applications:
- Suitable for hot asphalt tanks in shingle manufacturing plants.
Radar Level Sensor
Radar sensors use microwaves emitted by an antenna to detect levels. The time taken for the microwaves to reflect back determines the level.
Advantages:
- Not affected by temperature, pressure, or dust
- Suitable for liquids, pastes, powders, and solids
- Highly accurate with no need for calibration
- Non-invasive
Disadvantages:
- Expensive
- Limited detection range
Applications:
Ideal for hot liquid storage tanks, such as those in shingle manufacturing plants.
Differences in Level Sensing Methods
The primary distinction among level sensing methods lies in how they detect the level of a liquid:
- Non-Contact Sensors: Sensors like ultrasonic and radar operate without physically touching the liquid.
- Contact Sensors: Sensors such as optical, float level switches, and conductivity sensors interact directly with the liquid being measured.
Each method has unique advantages and disadvantages, making the choice of sensor dependent on the application’s requirements and the material’s properties.
Advancements in Level Sensing Technology
The evolution of level sensing technology has transformed processes that once required costly equipment. Today’s innovative and intelligent solutions are:
- Cost-effective
- Reliable and robust
- Highly accurate
- Easy to install
Modern level sensing technologies have made it possible to detect challenging fluids such as:
- Bubbly or foamy substances (e.g., soaps)
- Sticky materials (e.g., glue, ink)
- Delicate liquids (e.g., milk)
These advancements have expanded the range of applications for level sensing, offering more effective and efficient solutions for even the most demanding industrial needs.
Comparison of Level Sensor Types: Contact vs. Non-Contact Methods
This below table provides a concise comparison of different level sensors based on their contact type, detection method, advantages, disadvantages, and typical applications.
Sensor Type | Contact/Non-Contact | Detection Method | Advantages | Disadvantages | Applications |
Float Switch | Contact | Buoyancy (Float) | Simple, cost-effective, reliable | Limited to clean liquids, large size | Water tanks, oil levels, hydraulic fluids |
Capacitive Sensor | Contact | Capacitance change | Works with solids and slurries, high temperature | Affected by varying dielectric materials | Chemical processes, food and brewery industries |
Ultrasonic Sensor | Non-Contact | Sound wave reflection | Non-contact, suitable for varying media | Affected by foam, steam, agitation | Water treatment, bulk solids, high viscous fluids |
Radar (Microwave) Sensor | Non-Contact | Electromagnetic wave reflection | High accuracy, works through various media | Expensive, sensitive to build-up on sensor face | High-pressure/temperature applications, corrosive liquids |
Optical Sensor | Contact | Light reflection | Accurate, good for clear liquids | Limited to clean, non-coating liquids | Food and beverage, clear liquid measurement |
Conductivity Sensor | Contact | Electrical conductivity | Simple, low cost | Only works with conductive liquids, erosion risk | Boiler water, reagent monitoring |
Vibrating (Tuning Fork) Sensor | Contact | Frequency change due to vibration | Compact, works with sticky or foamy media | Not suitable for continuous level measurement | Solids, grains, powder |
Hydrostatic Sensor | Contact | Pressure measurement | Reliable, not affected by media properties | Requires tank to be emptied for maintenance | Storage tanks, corrosive liquids |
Magnetic Sensor | Non-Contact | Magnetic float movement | Visual indication, good for colorless fluids | Magnetic float can stick, pressure dependent | High pressure/temperature applications, corrosive liquids |
Radiometric Sensor | Non-Contact | Gamma radiation transmission | Suitable for extreme conditions, non-contact | Expensive, safety concerns due to radiation | High temperature/pressure, toxic media |
Thermal Dispersion Sensor | Contact | Heat dispersion measurement | High sensitivity, good accuracy | Not suitable for varying temperatures | HVAC systems, petrochemical, food and beverage |
What are the classifications of level sensors?
Level sensors are classified into two main categories:
- Point Level Measurement
This type of measurement indicates when a substance reaches a specific point. - Continuous Level Measurement
This type of measurement provides a continuous reading of a substance’s level as it changes.
What types of sensors are used for point level measurement?
Point level measurement sensors include:
- Capacitance sensors
- Optical sensors
- Conductivity sensors
- Vibrating (Tuning fork) sensors
- Float switches
What types of sensors are used for continuous level measurement?
Continuous level measurement sensors include:
- Ultrasonic sensors
- Radar (Microwave) sensors
What is the most common type of level sensor?
The most common type of level sensor is the float switch. It is widely used due to its simplicity, reliability, and cost-effectiveness in various applications for detecting the level of liquids.
What are the 4 main types of level sensors?
The four main types of level sensors are:
- Capacitive Sensors – Measure level changes by detecting variations in capacitance.
- Ultrasonic Sensors – Use sound waves to determine the level of a substance.
- Radar (Microwave) Sensors – Utilize electromagnetic waves to measure the level of liquids or solids.
- Conductivity Sensors – Detect liquid levels based on the electrical conductivity of the substance.
What is the theory behind level sensors?
The theory of level sensors involves detecting the presence or level of a substance liquid, solid, or slurry within a container or environment. This is achieved through various principles, such as buoyancy (float switches), capacitance changes (capacitive sensors), sound wave reflection (ultrasonic sensors), electromagnetic wave reflection (radar sensors), and electrical conductivity (conductivity sensors). The selected method depends on the type of substance, required accuracy, and environmental conditions
What are liquid level sensors?
Liquid level sensors are devices designed to measure the height or level of a liquid within a container. They are used in various applications, including:
- Monitoring water levels in tanks
- Measuring oil or fuel levels in storage containers
- Gauging liquid levels in chemical process vessels
How do liquid level sensors work?
Liquid level sensors detect the presence or level of a liquid using different principles, depending on the type of sensor. They can monitor and control the liquid level, and may also trigger alarms or shut-off valves if the level reaches predefined high or low points.