Sensor
A sensor is a device that reacts electrically to stimulus it receives. A device that yields a useful output in response to a designated input is defined by the American National Standards Institute (ANSI).
Selection of Sensor in instrumentation
List of Factors for Choosing a Sensor
Environmental Factors | Economic Factors | Sensor Characteristics |
1. Temperature range 2. Humidity effects 3. Corrosion 4. Size 5. Over-range 6. Protection 7. Susceptibility to EM Interferences 8. Ruggedness 9. Power Consumption 10. Self-test capability | 1. Cost 2. Availability 3. Lifetime | 1. Range 2. Repeatability 3. Stability 4. Sensitivity 5. Linearity 6. Error 7. Response time 8. Frequency Response |
Explain the Factors considered while selecting sensor
There are several factors to take into account when choosing sensors to measure different characteristics.
1. Measurement Range
Determine the range that is necessary to measure the desired parameter. Make sure the sensor you select can measure within that range precisely and consistently. Think about the minimum and highest values you anticipate seeing.
2. Accuracy
Determine the degree of accuracy needed for your measurement. Accuracy tolerances may vary depending on the application. For your unique demands, pick a sensor that can deliver the appropriate level of accuracy.
3. Sensitivity
Take into account the sensor’s sensitivity, which refers to its capacity to identify minute modifications in the parameter being gauged. Depending on the application, you can want a sensor with high sensitivity to detect minute deviations or one with low sensitivity for readings that are more generic.
4. Response Time
Consider the response time necessary for your application. Real-time or quick responses may be necessary for some measurements, while slower responses may be acceptable for others. Check to see if the sensor can deliver the required reaction time for your application.
5. Environmental Conditions
Consider the surroundings in which the sensor will be placed. Take into account variables like pressure, temperature, humidity, and any potential exposure to severe chemicals or gases. In order to achieve dependable and precise measurements, pick a sensor that is appropriate for the particular environmental circumstances.
6. Calibration and Maintenance
7. Compatibility
Verify that the sensor is appropriate for use with your data collecting or measurement system. In terms of electrical connections, signal output, communication protocols, and integration skills, make sure everything is compatible.
8. Cost
Take into account the sensor’s price, taking into account both the initial purchase price and any further costs like calibration or maintenance. Cost and the performance and reliability that are necessary for your application should be balanced.
9. Reliability and Durability
Evaluate the sensor’s dependability and durability. Look for sensors that have a solid track record, positive reviews, and are appropriate for the operating circumstances of the desired application.
10. Size and Installation
Take into account the sensor’s size, form factor, and ease of installation. Make sure the sensor is easy to install in your application and that it meets any space restrictions.
11. Safety Considerations
Examine any safety issues the sensor may raise. Certain applications could call for sensors that have certain safety certifications or adhere to certain industry requirements.
12. Assistance and Documentation
Verify whether the sensor has access to technical assistance and documentation. To help you with any queries or problems that may occur, look for manufacturers or suppliers who offer thorough product information, datasheets, user manuals, and support channels.
Some of the criteria /types in selecting the right sensor
Temperature Sensor
- Since many physical phenomena are dependent on temperature, we can frequently measure temperature indirectly by measuring pressure, volume, electrical resistance, and strain.
- Temperature sensors are found in buildings, chemical processing facilities, engines, appliances, computers, and many other devices that require temperature monitoring.
- The application requirements, temperature range, precision, response time, cost, and environmental conditions are just a few of the variables that must be taken into consideration when choosing the best type of temperature sensor.
The following are some typical temperature sensor types and selection criteria:
- Thermocouples
- Resistance Temperature Detectors (RTDs)
- Thermistors
- Sensors made of semiconductor materials
- Infrared (IR) sensors
- Bimetallic strips
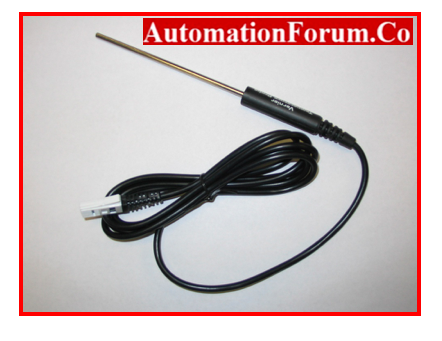
Pipework temperature measurements
- Immersion sensors: The immersion sensor typically provides the best benefits.The sensor must be completely submerged in the pipe for its entire active length.
- Strap on Sensor: When installation conditions render animmersion sensor inappropriate, strap-on sensors are used for installation of retrofit (renovation projects) for residential building heating systems.
- Cable sensors: The cable sensor has numerous benefits in refrigerant pipelines, such as sealing.
Tank temperature monitoring
- Important: Avoid taking measurements at the tank’s 20 cm outermost points.
- Capillary sensors with probes or cable sensors:
- They are best used when a distance between the sensor and the device head is necessary owing to vibration, space constraints, or climatic conditions.
Temperature measurement in ducts
- Probe sensors: In general, probe sensors are appropriate for this purpose measuring the temperature in ducts
- Test sensors: These produce spot measurements and should only be applied to ducts without stratification.
- Averaging sensors:For all applications, recommended. The rod’s or capillary tube’s length must be appropriate for the duct cross-section (about 4 m per m2). Never place a sensor downstream of an electric heating coil that has plastic-coated sensor elements. If this cannot be avoided, install a radiant-heat shield.
Room temperature measurement
- Room sensors: It is desirable to utilize multiple sensors in vast areas (for an average value).Sensors must not be placed in the exhaust air flow when there are large internal loads or when extractors are utilized above lamps.
- Important: Don’t forget to allow for reheating in the duct.Install far from heat sources.
Humidity measurement
Depending on the type of sensor, the humidity sensor’s time constant (also known as lag coefficient or response time) can range from 10 seconds to 5 minutes.For measurements in the supply air, sensors with a quick response time (less than 1 minute) should often be employed.
Lag coefficients for several sensor elements, in a table:
- Sensor component Lag coefficients
- Man-made fiber – About 1…3 minutes
- Lithium chloride -110s
- Cotton – 3 minutes
- Capacitance – 10…20s
Supply air, steam humidifiers, and spray humidifiers are quick humidification devices.
- Important: The lifespan and functionality of humidity sensors will be hampered by substances used in laboratories, swimming pools, hospitals, and other settings such as chlorine and disinfectants. Air speed: At the sensing site of a humidity sensor, the maximum permissible air velocity must not be exceeded.
Air quality sensors
- Detectors of air quality measuring the temperature outside Suitable for heating systems are outside sensors.
- Temperature readings for ventilation systems must be taken immediately following the weather shield in the outside air intake.
Measuring the pressure and differential pressure of liquids and gases, such as air
- The safety pressure of the system must match the nominal pressure of the pressure sensor.
- One side’s maximum allowable load cannot be exceeded.
- The use of the pressure sensor with the measurement medium (such as water, vapor, refrigerant, food, gases, etc.) must be allowed.
- It is necessary to choose the measuring range so that the set value is not at the scale’s beginning or finish.
Volumetric flow rate and velocity measurements
For measuring velocity or volumetric flow rate, a variety of measurement systems are available. What matters most in this situation is whether a spot measurement or an average is needed.
Measuring systems
Spot measurements
- Pressure tube – Gases, liquids
- Hot wire anemometer – Gases
- Vane anemometer – Gases, liquids
Averaged measurements
- Orifice plates – Gases, liquids
- Flow nozzles (cross)- Gases
- Flow nozzles (ring) – Gases
- Ultrasound – Liquids
- Magnetic flux – Liquids
- Helical flow – Liquids
- Ring piston – Liquids
With spot measurements, the flow profile has a significant impact on the measured outcome. Because of this, it is strongly advised to utilise “averaging” type measuring equipment when determining velocity and volumetric flow rates.
Flow & Level Sensor
The application requirements, fluid characteristics, flow rate or level range, accuracy, response time, installation requirements, environmental conditions, and cost all play a role in choosing the best type of flow and level sensor. The following are some typical flow and level sensor types.
List of Level Sensors
- Float Switches
- Capacitance Level Sensors
- Ultrasonic Level Sensors
- Pressure-based Level Sensors
- Radar Level Sensors
List of Flow Sensors
- Differential Pressure Flowmeters
- Magnetic Flowmeters
- Ultrasonic Flowmeters
- Coriolis Flowmeters
When choosing flow and level sensors, carefully consider the requirements of your individual applications and compare the sensor’s specifications, such as compatibility with the fluid, range of flow rate or level, accuracy, response time, installation needs, and compatibility with your measurement system or controller.
Pressure Sensor
Application requirements, pressure range, accuracy, sensitivity, reaction time, medium compatibility, ambient conditions, and cost are just a few of the variables that influence pressure sensors.
List of Pressure Sensors
- Strain Gauge Pressure Sensors
- Capacitive Pressure Sensors
- Piezo resistive Pressure Sensors
- Vibrating Element Pressure Sensors
- Absolute, Gauge, and Differential Pressure Sensors
- Silicon-based Pressure Sensors
Accelerometer
The optimum sort of vibration measurement sensor is dependent on the application needs, vibration properties, frequency range, sensitivity, mounting options, and environmental factors.
List of vibrational Sensors
- Accelerometers: Accelerometers are frequently used to measure vibration. They gauge an object’s acceleration in one or more directions. When choosing accelerometers, take into account the frequency range, sensitivity, dynamic range, and mounting possibilities. The three primary categories of accelerometers are:
- Piezoelectric accelerometers
- Microelectromechanical Systems (MEMS) accelerometers
- Capacitive accelerometers
- Velocity sensors: Geo-phones and velocity transducers are two examples.
- Proximity probes
- Laser vibro-meters
- Strain gauges
Applications include heart monitors, automobile alarms, washing machines, and air bags. shock waves, bursts, impacts, and vibrations.
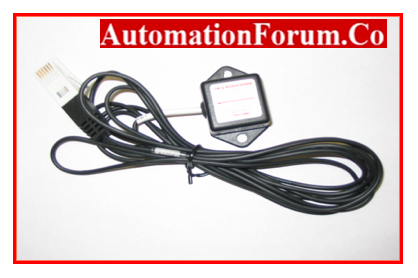
Light Sensor
Applications for ambient lighting, infrared detectors, and cameras all use light sensors. Some of the light sensors are.
List of Light Sensors
- Photodiodes
- Phototransistors
- Light-dependent resistors (LDRs
- Photodiode arrays:
- CMOS/CCD image sensors:
- Color sensors
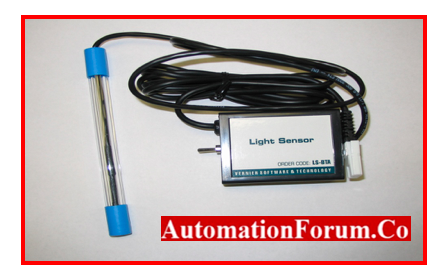
Gas Sensor
The target gas to be detected, application requirements, gas concentration range, response time, sensitivity, selectivity, operating conditions, and cost are only a few of the variables that affect the type of gas sensor.
List of Gas Sensors
- Electrochemical sensors
- Semiconductor gas senosrs.
- Catalytic bead sensors.
- Infrared gas sensors: There are two types of infrared sensors: nondispersive infrared (NDIR) and dispersive infrared (DIR) sensors.
- Photoionization detectors (PID)
- Metal oxide gas sensors
Example Gas Sensor in measuring CO2
CO2 sensor measures gaseous CO2 levels in an environment which measures CO2 levels in the range of 0-5000 ppm and monitors level of infrared radiation is absorbed by CO2 molecules
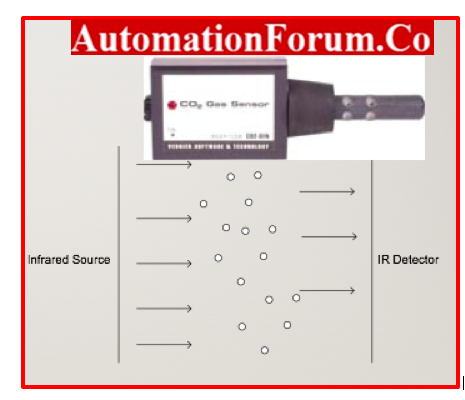
Installation of Sensor
Before mounting sensor, one should always confirm the following:
- Minimum and maximum ambient temperatures
- Vibration exposure
- Explosion protection
- Ambient humidity and water spray exposure
- External affects
- Consider both the active and inactive portions of a sensor probe.
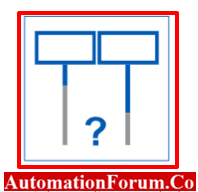
- Each sensor must have a tight-sealing test hole next to it.
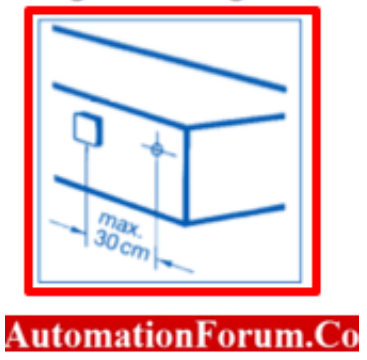
- To keep water from getting inside the sensor housing, the wire needs to be attached with a “drip loop”.
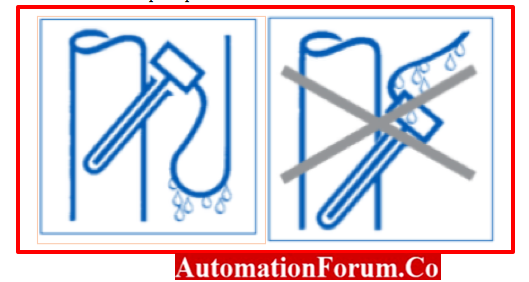
Always provide enough extra cable so that the sensor can be removed whenever necessary without disconnecting the cabling.
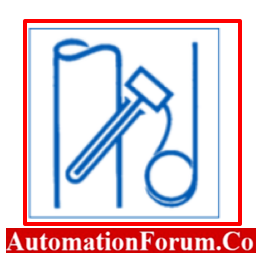
A sensor should not have the lagging compressed during installation.
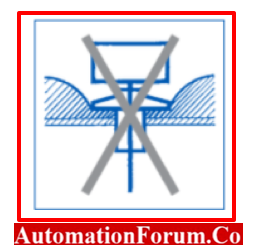
To prevent squeezing the lagging, use a mounting flange with graduated diameters.
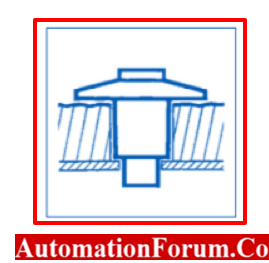
If the supplied mounting flange lacks the necessary graduations, add spacing bushes to prevent the lagging from being compressed.
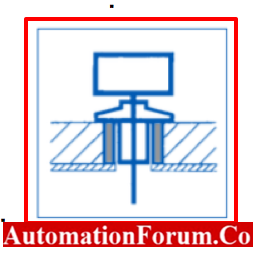
- Mark the locations of the sensors visibly and include them in the site documentation if they need to be hidden (for example, under false ceilings, shafts, etc.)
- Place an identifying plate right next to the sensor. The reference number from the plant schematic must also be included, along with a plain text explanation. Do not affix the label to the actual gadget.
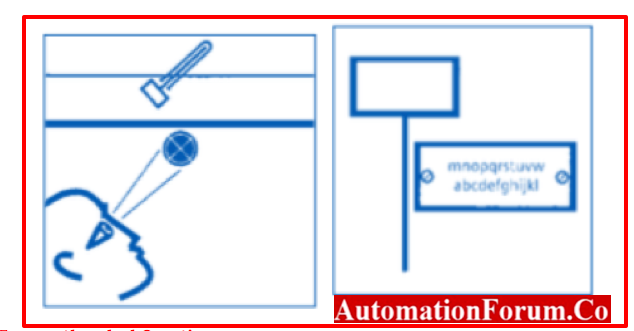
Frequently asked Questions
What is the importance of sensor placement?
Location of sensor is essential for any sensor-based data gathering system to guarantee that the system can see the correct data for analysis.
How does sensor selection work?
Matching a sensor’s operating characteristics to an application’s needs is the basis for choosing an appropriate sensor. Additional factors, including as cost and impedance matching, help with the choice.
Mention some operational conditions needed to choose a sensor
The essential operating requirements of the application when choosing the sensors to check the sample.
- Range of temperatures
- Size
- Protection level
- Range of Voltage
- Analogue or discrete output