- Definition of Valve Flow Coefficient (Cv)
- Significance of Cv in Engineering
- Step-by-Step Guide to Calculating Valve Flow Coefficient (Cv)
- Factors Influencing Cv
- Importance of Cv in Valve Selection
- Cv in System and Pipeline Design
- Free Online Instrumentation Tool for Cv Calculation
- What is Cv and How does it relate to valves?
- Standards and Regulations for Control valve valve flow coefficient (Cv)
- Valve flow coefficient, or Cv, serves as a fundamental parameter in the selection and operation of valves within industrial settings.
- Understanding the importance of Cv is crucial for engineers and operators to ensure optimal performance and efficiency in fluid flow systems.
- Whether it’s controlling the flow of water, chemicals, or gasses, the Cv provides a standardized metric for evaluating valve capacity and effectiveness.
Definition of Valve Flow Coefficient (Cv)
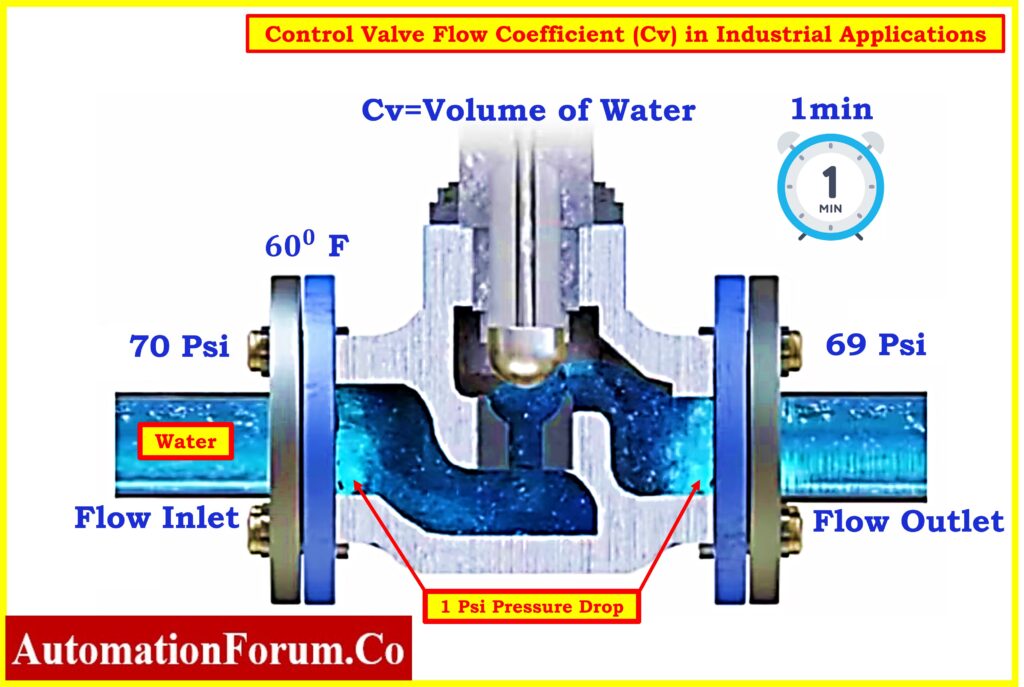
- One of the most significant measurements in fluid mechanics, especially in the engineering and industrial domains, is the valve flow coefficient, or Cv. It focuses on measuring a valve’s flow capacity under particular operating circumstances, giving engineers a common metric to assess and contrast various valves in a range of applications.
- Defined as The amount of US gallons per minute (one US gallon is equal to 3.786 liters) of water that go through a specific area with a pressure drop of one PSI is known as the control valve flow coefficient, or Cv.
- Water is included in the usual definition, however additional fluids and gasses will also fall under this category.
- Cv serves as a universal benchmark, enabling seamless comparison and selection of valves irrespective of the application.
Significance of Cv in Engineering
- Valve Flow Coefficient (Cv) holds paramount significance in ensuring optimal performance and efficiency in fluid flow systems.
- It serves as a Strong foundation for engineers to make informed decisions regarding valve selection and system design.
- By comprehensively understanding the significance of Cv, engineers can navigate the complexities of fluid flow regulation with precision and confidence, ultimately contributing to the seamless operation of industrial processes and systems.
- CV facilitates efficient interaction and collaboration amongst parties engaged in system design, implementation, and operation in addition to streamlining the valve selection process.
Step-by-Step Guide to Calculating Valve Flow Coefficient (Cv)
Engineers may systematically calculate the valve flow coefficient (Cv) for a wide range of conditions by following this step-by-step procedure and applying different parameter values. This will help them make well-informed decisions regarding valve selection and system design.
Step 1 :Understand the Parameters:
- Understanding three important factors is essential before beginning the CV calculation process:
Specific Gravity (SG):
- Specific gravity represents the density ratio of a given fluid compared to water at 4 degrees Celsius.
- Familiarize yourself with the specific gravity values of common substances, such as water, ethanol, iron, and gold.
Flow Rate (Q):
- Flow rate, which is commonly expressed in gallons per minute (GPM), shows how much fluid passes through the valve in a given amount of time.
- Ensure the flow rate is converted to gallons per minute if provided in different units.
Pressure Drop (P):
- Pressure drop signifies the decrease in pressure across the valve necessary for regulating flow. It’s a critical parameter influenced by factors such as pipe material, temperature, and fluid density.
- Pressure drop is usually expressed in pounds per square inch (psi).
Step 2:Gather Parameter Values:
- Collect the specific gravity, flow rate, and pressure drop values relevant to your application.
- Ensure consistency in units, converting values if necessary to match the standard units discussed earlier.
Step 3: Apply the Cv Formula
- Utilize the Cv formula,
Cv = Q * (? (SG/P)), to calculate the valve flow coefficient.
- This formula expresses the relationship between specific gravity, flow rate, and pressure drop, providing a systematic approach to determine Cv.
Step 4:Calculation for Cv
- Let’s consider an example using different parameter values:
Given parameters:
Specific Gravity (SG) = 0.85
Flow Rate (Q) = 15 gallons per minute
Pressure Drop (P) = 0.2 psi
- Plug these values into the Cv formula:
Cv = 15 * (? (0.85/0.2))
Cv = 15 * (? (4.25))
Cv = 15 * 2.0615528128088303 ? 30.923
- The calculated Cv value of approximately 30.923 indicates the required valve flow coefficient to achieve a flow rate of 15 gallons per minute at a pressure drop of 0.2 psi for the specified fluid.
- Now, let’s calculate Cv for two additional sets of parameter values:
For example Q = 2.5, SG = 0.6, P = 0.5:
Cv = 2.5 * (? (0.6/0.5)) ? 2.5 * (?1.2) ? 2.5 * 1.095 ? 2.74
For example Q = 18, SG = 1.2, P = 0.15:
Cv = 18 * (? (1.2/0.15)) ? 18 * (?8) ? 18 * 2.828 ? 50.91
Factors Influencing Cv
- Cv values are influenced by a wide range of variables, including operating circumstances, material composition, and valve size and shape.
- It is critical for engineers to understand these components in order to choose the right valves and create systems with informed decisions.
Valve Size and Shape
- The physical dimensions and configuration of a valve significantly impact its Cv value.
- Larger valves with more open pathways tend to reflect higher Cv values, enabling greater flow rates and enhanced system performance.
Valve Type
- Various valve types, including butterfly, ball, and globe valves, have different CV characteristics because of their different flow profiles and designs.
- Engineers must consider these inherent differences when selecting valves to ensure compatibility with system requirements.
Material and Trim
- The choice of materials used in valve construction, along with the design of internal trim components, can influence Cv values.
- Smoother surfaces and optimized trim designs contribute to improved flow efficiency and performance, thereby affecting Cv calculations.
Pressure Rating
- The pressure rating of a valve dictates its ability to withstand pressure differentials, thereby impacting Cv values.
- Engineers must consider the operating pressure range of the system when selecting valves to ensure reliable performance and safety.
Temperature
- Fluid temperature plays a critical role in Cv calculations, as it affects the viscosity and density of the fluid, thereby influencing flow characteristics.
- Temperature variations have the potential to alter Cv values, hence system design and valve selection must be done with extreme caution.
Flow Profile
- The flow profile of the fluid passing through the valve, whether laminar or turbulent, also influences Cv values.
- In order to precisely determine the CV requirements and ensure optimal performance, engineers need to take into consideration the fluid dynamics and flow conditions within the system.
Fluid Properties
- Beyond specific gravity, other fluid properties such as viscosity and compressibility affect Cv. Viscous fluids like oils or highly compressible gases require different Cv considerations than less viscous fluids like water.
Installation Orientation
- The orientation of the valve installation, whether horizontal, vertical, or at an angle, can impact the Cv value due to changes in fluid dynamics and flow patterns.
Control System Dynamics
- The dynamics of the control system in which the valve operates, including response time and stability, can influence the effective Cv required for optimal control performance.
System Turbulence
- Turbulence within the piping system, caused by factors such as bends, elbows, or sudden expansions or contractions, can affect Cv by altering flow profiles and pressure distributions.
Environmental Conditions
- Environmental factors such as ambient temperature and humidity may indirectly influence Cv by affecting fluid properties or valve performance characteristics over time.
Importance of Cv in Valve Selection
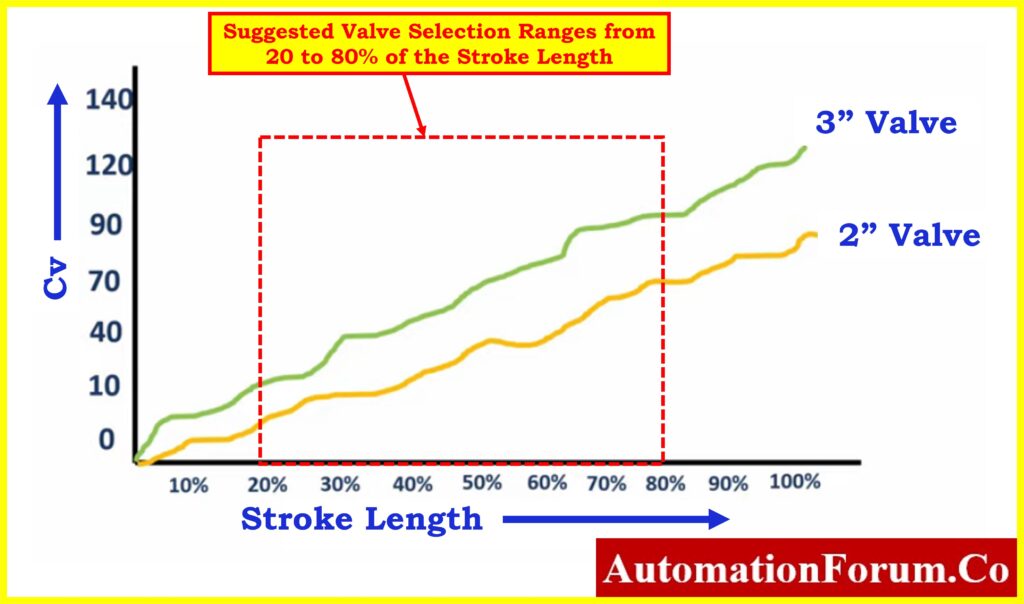
- It is impossible overestimate the importance of CV in valve selection since it is essential to obtaining reliable and efficient fluid flow control in industrial applications.
- It is crucial to choose a valve with the right Cv to prevent flow restrictions, pressure drops, and inefficiencies in the system.
- On the other hand, selecting a valve with an excessive Cv can result in irregular flow situations, damage to the valve, and higher energy usage.
- Valve selection ranges, typically recommended between 20 to 80% of the stroke length, correspond to Cv values, ensuring optimal performance within this range. This aligns with efficient flow control while considering the valve’s flow capacity characteristics.
Cv in System and Pipeline Design
- Cv values are essential for optimizing system performance and efficiency in pipeline and system design.
- Engineers use Cv data to estimate flow rates, compute pressure drops across valves, and make sure the right valves are sized and chosen for a given application.
- Engineers can efficiently eliminate potential difficulties and optimize system performance to fulfill operational needs by incorporating CV concerns into the design process.
Free Online Instrumentation Tool for Cv Calculation
- To facilitate Cv calculations and streamline valve selection processes, Kimrey offers a free online tool for control valve Cv calculation and flow rate estimation.
- This user-friendly tool empowers engineers with the resources needed to make informed decisions and optimize system performance, thereby enhancing operational efficiency and reliability.
Click here for Free Tool for Calculating Valve Cv
What is Cv and How does it relate to valves?
- In many different applications, including plumbing systems and industrial installations, valves are essential parts of the fluid flow management system.
- Choosing the right valve characteristics is essential to their effective functioning.
- A key factor in determining how well a valve performs is the valve flow coefficient, or Cv for short (or Kv in metric units).
- In systems, valves are used as control mechanisms to regulate fluid flow.
- In order to maintain appropriate flow rates and process conditions, valves are essential whether managing chemicals, gasses, or water.
- Because Cv can describe a valve’s flow capacity, there is a correlation between Cv and valves.
- To evaluate a valve’s fitness for a given application and ensure efficient fluid flow regulation within specified limits, engineers use Cv values.
- Selected a valve with the right Cv is practically necessary to get optimal performance.
- Greater flow rates can be accommodated by higher CV valves, making them perfect for applications requiring high-volume fluid transmission.
- On the other hand, for accurate flow control at lower rates, lower CV valves are preferred.
- Essentially, Cv is an important valve selection parameter that allows engineers to match valve features to system requirements for maximum effectiveness and performance.
- Engineers ensure proper valve integration by taking CV into account in addition to elements like material compatibility and pressure ratings, which improves overall system performance and dependability.
Standards and Regulations for Control valve valve flow coefficient (Cv)
- ISA develops standards for automation, including control valve sizing with guidance on Cv calculation.
- ANSI/ISA-75.01.01 (IEC 60534-2-1) provides sizing equations for control valves, aiding proper selection.
- ASME B16.34 covers valve design and performance, indirectly influencing Cv considerations.
- API standards like API 600, API 602, and API 609 offer specifications for valve design and testing.
- ISO standards such as ISO 5211 and ISO 5752 provide guidance on valve specifications affecting Cv.
Click here for to know more about Flow Measurement.
Click here for to know more about Control Valve