- What is Transducer?
- Parts of Transducer
- What is Transducer Classification?
- How are Transducer Classified?
- How Does a Transducer Work? Working Principle of a Transducer:
- Classification based on the principle of transduction
- Classification as primary and secondary transducers
- Classification as Active and Passive transducer
- Analog and Digital transducer
- Transducers and Inverse transducers
- What are the basic requirement of Transducer?
- Sensors and Actuators
- Difference Between Transducers and Sensors
- Applications of Transducers
- FAQ on Transducer Classification
- What are the Advantages of a Transducer?
- What are the Characteristics of a Transducer?
- How are Transducers Classified?
- What are the Types of Capacitive Transducers?
- What Is the Difference Between a Transducer and an Inverse Transducer?
- What are the Types of Inductive Transducers?
- What are the Types of Pressure Transducers?
- What are the Types of Photoelectric Transducers?
- What are Primary and Secondary Transducers?
What is Transducer?
For most instrumentation systems, the input quantity will be a non-electrical quantity. The non-electrical quantity is converted into an electrical form for using electrical methods and techniques for measurement, manipulation and control. The device which when actuated, transforms energy from one form to another is called a transducer.
Parts of Transducer
- Transduction Element: A transduction element is one which transforms the output of a sensing element to an electrical output.
What is Transducer Classification?
Transducers are classified in a variety of ways based on certain parameters. These include the application region, manner of energy conversion, type of output signal, electrical principles involved, electrical parameters employed, operational principles, and common applications.
How are Transducer Classified?
Transducers are classified into 5 as,
- On the basis of transduction form used
- As primary and secondary transducers
- As passive and active transducers
- As analog and digital transducers
- As transducers and inverse transducers
How Does a Transducer Work? Working Principle of a Transducer:
A transducer is typically made up of two primary components: a sensing element and a transducing element. The sensor element detects an input (such as pressure, temperature, or light) and generates a matching output. This output is then passed via the transducing element, which changes it into an electrical signal proportional to the input.
Classification based on the principle of transduction
This classification is based on the principle of transduction as resistive, inductive, capacitive etc. depending upon their conversion into resistance, inductance or capacitance respectively. They can be classified as thermoelectric, piezoelectric, electrokinetic, optical and magneto-restrictive.
Classification as primary and secondary transducers
Primary transducer senses the input directly and physical phenomenon is converted into the electrical form directly. While in secondary transducer, initially input is being sensed by some detector or sensor and then its output in some form other than input signal is given to transducer to convert into electrical signal.Mechanical device acts as a primary detector transducer and the electrical device acts as the secondary transducer in most of the measurement systems with mechanical displacement serving as the intermediate signal.
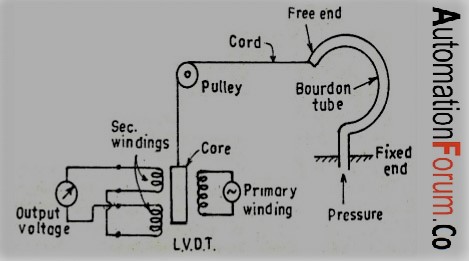
As shown in the figure, the bourdon tube which senses the pressure and converts it into displacement of its free end and hence acts as primary transducer. The core of LVDT (linear variable differential transformer) is moved due to this displacement. Hence the LVDT produces output voltage proportional to that displacement of the free end of bourdon tube. Bourdon tube, which acts as primary transducer and LVDT acts as secondary transducer.
Classification as Active and Passive transducer
Active transducers are one which develop their output in the form of electrical voltage or current without any auxiliary source. They are also called self-generating transducers. Active transducers draw energy from the system under measurement and such transducers normally give very small output. Thermocouples used for the measurement of temperature, tacho-generators used for the measurement of angular velocity comes under this category.
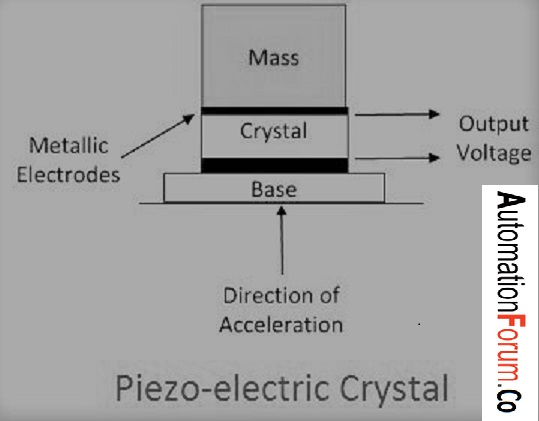
In the example shown above, the crystal is sandwiched between 2 metallic electrodes, and the entire sandwich is fastened to a base which may be the floor of a rocket. On the top of the sandwich a fixed mass is placed which exerts a certain force due to acceleration on the crystal due to which a voltage is generated. The voltage output is proportional force and hence is proportional to acceleration. The property of piezo -electric crystal is that when a force is applied to them, they produce an output voltage.
Passive transducers are one which require external power source for energy conversion. In passive transducers electrical parameters like resistance, inductance, capacitance causes a change in voltage, current or frequency of external source. Resistive, inductive and capacitive transducers fall in this category.

This is an example for passive transducer. A linear potentiometer is a resistive transducer powered by a source voltage ei and is used for the measurement of linear displacement xi.
Analog and Digital transducer
Transducers, on the basis of nature of output can be classified as analog and digital.
- Analog transducers: These type of transducers which convert input signal into output in the form of a continuous function of time such as thermistor, LVDT, thermocouple etc.
- Digital transducers: These type of transducers which convert input signal into output in the form of pulses. The examples of digital transducers are linear displacement transducers using conducting and non-conducting contacts, opaque and translucent segments and shaft encoders. It can be easily represented by opaque and transparent areas on a glass scale or non-conducting and conducting areas as the binary system uses only two symbols 0 and 1.
Transducers and Inverse transducers
The basic requirement for control of physical quantities such as position, speed, temperature pressure and flow rate in an industrial plant is the ability to measure these quantities. The control action is only possible if the physical quantity can be measured. Transducers as early mentioned converts a non-eletrical quantity into electrical whereas inverse transducers converts an electrical quantity into some other forms.
An example is a current carrying coil moving in a magnetic field is an inverse transducer as the current carried by it is converted into a force which causes a rotational or trasnlational displacement. A large number of data indicating and recording devices are inverse transducers. Such devices which include instruments like pen recorders, oscilloscopes that convert electrical into mechanical movement are placed at the output stage are called as output transducers. The below diagram shows a piezo -electric crystal acts as an inverse transducer. When a voltage is applied across its surfaces, a mechanical displacement is caused as it changes its dimensions.
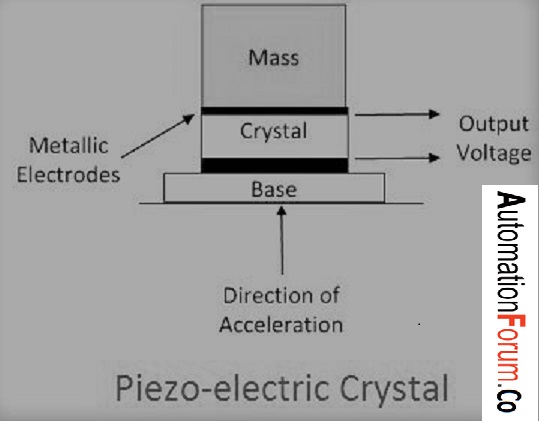
What are the basic requirement of Transducer?
There are 8 basic requirements for the proper functioning of transducers:
- Ruggedness: It should be capable of withstanding over load and some safety should be provided for overload protection.
- Linearity: Its input-output characteristics should be linear and it should produce these characteristics in symmetrical way.
- Repeatability: It should reproduce same output signal when the same input signal is applied under fixed environmental conditions. For example pressure, temperature, humidity etc.
- Residual Deformation: There should be no deformation on removal of input signal after long period of application.
- No Hysteresis: It should not give any hysteresis during measurement while input signal is varied from its low value to high value and vice versa.
- High Output Signal Quality: The quality of the output signal should be good. That is the ratio of signal to the noise is high and the amplitude of the output signal should be enough.
- High Reliability and Stability: It should give minimum error in measurement for temperature variations, vibrations and other various changes in surroundings.
- Good Dynamic Response: Its output should be faithful to input when taken as a function of time. The effect is analysed as the frequency response
Sensors and Actuators
Transducers are divided into two major categories based on their applications:
Sensors
Sensors measure physical quantities like temperature, pressure, and flow. They translate physical changes into electrical impulses or usable data. Examples include
- Thermocouples, which measure temperature.
- Strain Gauges – Measure force or strain.
- Flow meters measure the rate of fluid flow.
Actuators
Actuators control physical systems by converting electrical signals into mechanical motion. Examples include:
- Electric Motors – Convert electrical energy into rotational movement.
- Solenoids – Generate linear motion when energized.
- Piezoelectric Actuators – Produce precise movements in response to electrical signals.
Difference Between Transducers and Sensors
Transducers | Sensors |
Convert energy from one form to another. | Convert physical quantities into readable data or electrical signals. |
Examples: Microphones, LVDT, LEDs, Loudspeakers. | Examples: Pressure sensors, motion sensors. |
Applications of Transducers
Transducers are widely used in various applications, including:
- Medical Imaging – Ultrasound machines convert sound energy into electrical signals for display.
- Audio Systems – Microphones transform sound waves into electrical signals.
- Communication Systems – Antennas convert electromagnetic waves into electrical signals.
FAQ on Transducer Classification
What are the Advantages of a Transducer?
- Easy Signal Processing: Transducers’ electrical signals can be easily amplified or processed, making them appropriate for use with output devices such as indicators and recorders.
- Low Power Control: Electrical systems driven by transducers can be controlled with low power, making them more energy efficient.
- Versatility: They can be employed in a variety of applications, including industrial automation and medical equipment.
What are the Characteristics of a Transducer?
Transducers are rated according to their static and dynamic characteristics:
- Static characteristics include sensitivity, linearity, precision, repeatability, and hysteresis. They describe how well the transducer works in steady-state situations.
- Dynamic characteristics define the transducer’s behavior as the input changes over time. Response time, bandwidth, frequency response, and resonance frequency all play important roles.
How are Transducers Classified?
Transducers are classified based on their operating principles, applications, and signal types. Common types include:
- Piezoelectric transducers: convert mechanical stress into electrical impulses.
- Electromagnetic transducers: use magnetic fields to generate electrical signals.
- Resistive Transducers: Use resistance changes to measure physical quantities.
- Capacitive transducers: measure capacitance changes.
- Optical transducers: use light to detect and measure changes.
What are the Types of Capacitive Transducers?
Capacitive transducers are classified into:
- Parallel Plate Capacitive Transducers
- Cylindrical Capacitive Transducers
- Differential Capacitive Transducers
- Capacitive Pressure Transducers
What Is the Difference Between a Transducer and an Inverse Transducer?
- A transducer converts a non-electrical quantity (such as temperature or pressure) into an electrical signal.
- Inverse transducers do the inverse, converting an electrical signal into a non-electrical output (such as motion or light).
What are the Types of Inductive Transducers?
Inductive transducers are divided into two main types:
- Self-Generating Transducer: Produce a voltage signal from relative motion in a magnetic field without using an external power source.
- Non-Self-Generating Transducers: Need an external power source to energize coils whose inductance varies with motion.
What are the Types of Pressure Transducers?
Pressure transducers come in various types, including:
- Resistive (Strain Gauge) Pressure Transducers
- Capacitive Pressure Transducers
- Inductive Pressure Transducers
- Potentiometric Pressure Transducers
- Resonant Wire Pressure Transducers
- Piezoelectric Pressure Transducers
- Piezoresistive Pressure Transducers
What are the Types of Photoelectric Transducers?
Photoelectric transducers are classified based on their working principles:
- Photoemissive: Radiation causes electrons to be emitted from a cathode.
- Photovoltaic: Converts light directly into electrical energy.
- Photoconductive: Changes electrical resistance when exposed to light.
What are Primary and Secondary Transducers?
- Primary transducers convert physical inputs (such as pressure or temperature) into intermediate forms (such as displacement or strain). Its output serves as the input for the following stage.
- The secondary transducer converts the intermediate output from the primary transducer into an electrical signal.