- Automated Block Valve
- Ball Valve
- Pinch Valves
- Gate Valves
- Butterfly Valve
- Application Characteristics of Automated Block Valve
- Valve Data Required for Actuator Sizing
- Working Principle of an Automated Block Valve
- Applications of Automated Block Valves
- What Characteristics Should a Twin Block and Bleed Valve Have?
- What precisely is the feature of a block valve?
- What else is a block valve called?
- What is the function of a bleed and block valve?
- What precisely is a Manual Block Valve?
- What exactly is a Block & Bleed arrangement?
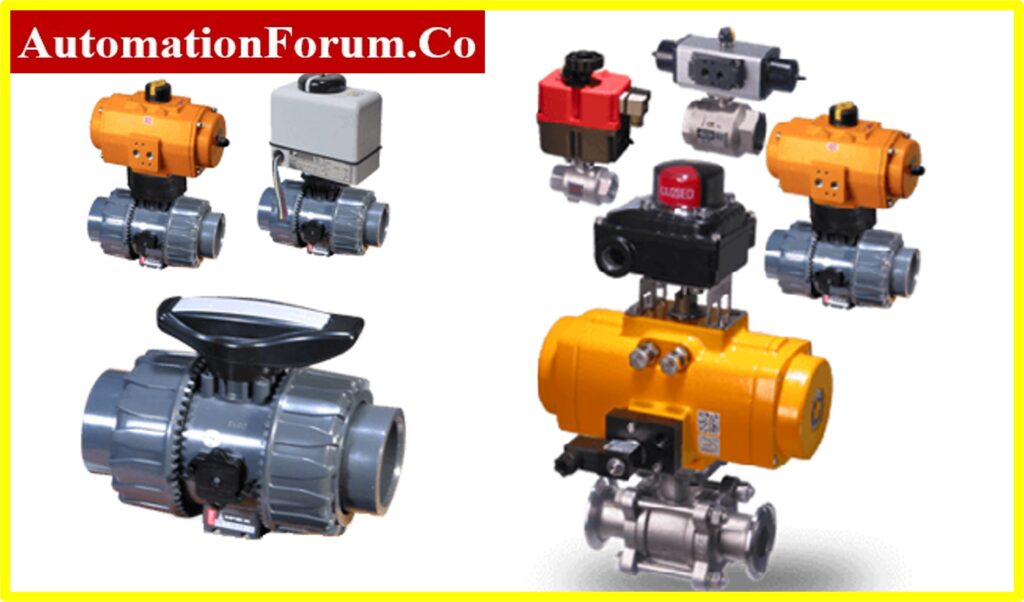
To meet the specific requirements, the final control elements being used in Safety Instrumented System (SIS) applications should be carefully engineered.
These valves are known as Automated Block Valves since they’re controlled in accordance with the LOPA safety requirements (ABV).
Typically, these valves have an essential function in separating the process from any potentially hazardous events; thus, the valves should always fulfill the SIS design criteria as well as the test procedures.
Automated Block Valve
The following are the significant elements of Automated Block Valves (ABV).
- Quarter-turn type on/off valve devices with pneumatic actuation are used in automated block valves.
- In certain situations, valve designs encompass ball valves, butterfly valves, and plug valves.
- Metal seat, soft seat, full bore, reduced bore, and cavity relief quarter-turn valve styles
- Valve Leakage Rate: The valve’s seat leakage is an essential factor that must fulfill API-598 or IEC 60534-4 Class V, VI design specifications for metal-seated ball valves.
- Rack and Pinion or Scotch Yoke actuators were included.
Ball Valve
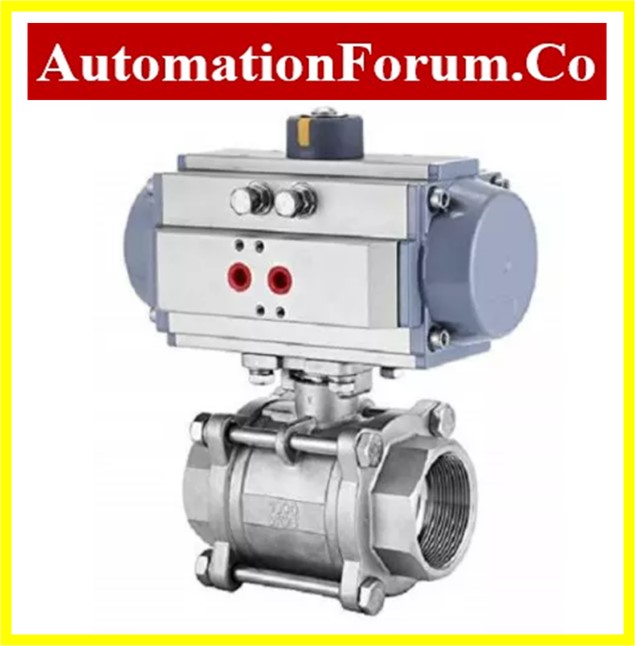
- A ball valve is a quarter-turn valve that governs flow through a hollow and pivoting ball.
- Ball valves are the most common type of valve, especially in PVC applications.
- To completely switch on or switch off the fluid flow within a system, these valves traditionally use spherical seating with a hole in it.
When the valve is turned “on,” liquid can stream through this tunnel.For a valve turn of 90 degrees turn
- When the hollow portion of the ball is parallel to the pipeline with the flow, the valve is said to be opened fully (100% open).
- When the hollow portion of the ball is perpendicular to the pipeline with the flow, the valve is said to be closed fully (0% open).
- Some ball valves are available in “full-bore” designs, which means the diameter of the hole in the ball is the same diameter as the pipeline.
- Full-bore ball valves are popular examples of block valves since they’re not expected to slow or restrict flow but instead to completely stop it and allow it to pass through without obstruction.
- Ball check valves are not block valves since they normally limit flow even when attempted to push open by liquid.
- The valve can be controlled either manually or automatically using just a pneumatic/electric actuator.
Pinch Valves
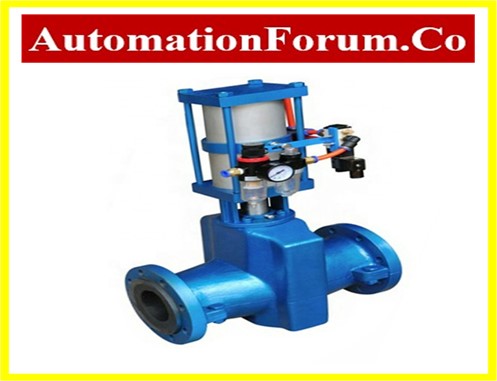
- Pinch valves are distinguishable in comparison to the two types of block valves
- Pinch valves are beneficial in an array of situations due to their ability to perform both as a stop and a limiting valve.
- Pinch Valve consists of an internal tube that can be pinched closed or left open either fully or partially.
- Even though Ball Valves & Gate Valves may not function properly when only they are half-open.
- Pinch valves offer a full port schematic that enables the process fluid to flow through the valve when fully opened.
- They can also close and completely stop liquid flow contingent on the pressure.
- Because of all of these characteristics, this pinch valve is an example of a unique block valve.
Gate Valves
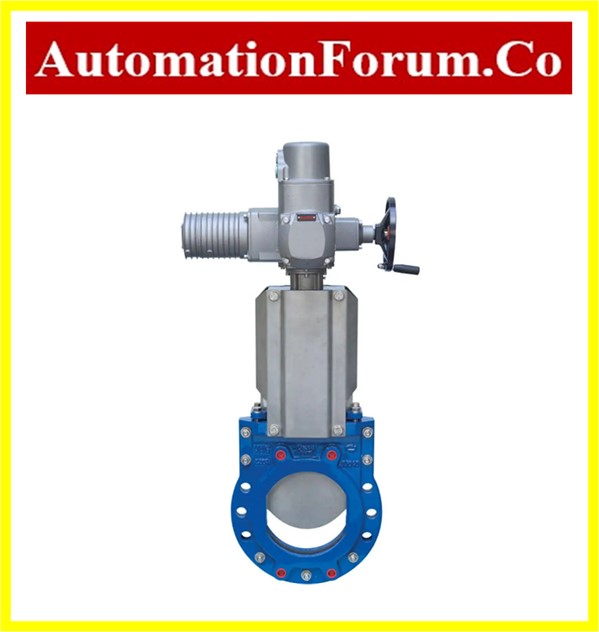
- Gate valves are another excellent example of the various block valve types. They have a vertical gate with a flat surface that prevents liquid from passing through.
- The conventional gate valve is aimed to be a shut-off valve rather than a control valve.
- When the gate valves in a full-bore design are open, the gate is entirely out of the way. When the valve is open, it means that the flow is uncontrolled.
- A gate valve, comparable to a ball valve, is an example of a “Block Valve.”
Butterfly Valve
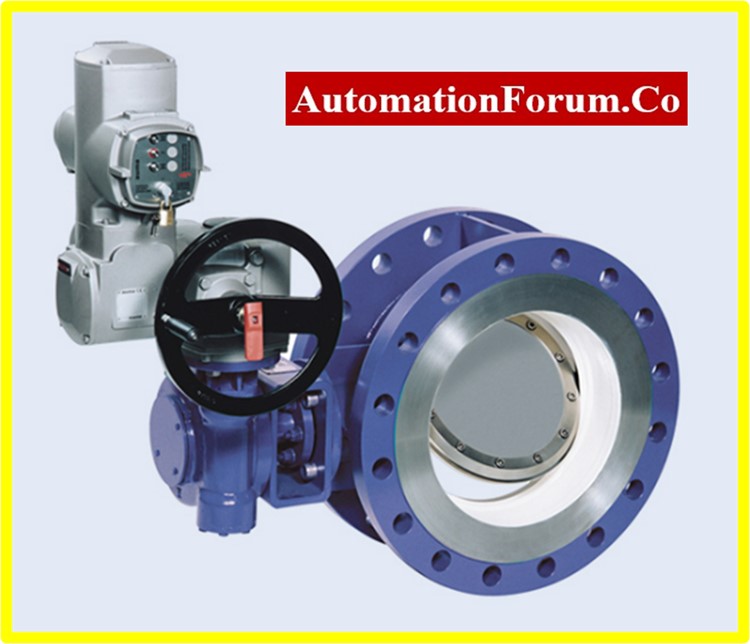
- The butterfly valve is composed of a disc and a shaft, with the rotation of the valve disc controlling the fluid flow.
- When the valve is closed position, the disc seats along the pipe bore, restricting flow through the valve.
- When the valve is in the open position, the disc is perpendicular to the flow direction, permitting flow through the valve.
There are 3 types viz.
- Zero offsets,
- Double offset &
- Triple offset butterfly valve.
Application Characteristics of Automated Block Valve
The selection of Automated Block Valves for the respective applications is based on the Application characteristic & specific requirements.
Automated Block Valve performance is based on the following factors
- Fluid Medium
- Process Data parameters
- Design Conditions
- Fluid Properties
- Flow Direction
- Pressure / Temperature rating
- Pipe Specification – pressure class, rating
- Application Specific Requirements
Some parameters shown below define the type of valve to be selected in SIS applications.
- Cycle Frequency
- Open/Closing Time (travel time)
- Water hammering
- SIL classification (SIL 1/2/3)
- Fail Action
- Fire Safe/Fire Retardant
- Fugitive Emission Requirements
- Tightness Class requirement
Valve Data Required for Actuator Sizing
To design an appropriate actuator for a particular valve, here are some basic parameters required to be provided by the Valve manufacturer to the Actuator manufacturer
- Valve torque
- Determine the total torque for the supplied shut-off pressure.
- Considerations of torque: Breakaway from open torque; running torque: Torque permitted for remounting
- Application features including particles and application process temperature seem to be torque adjustment considerations.
- Frequency of operations
- Maximum Allowable Stem Torque
- Travel time requirements
Working Principle of an Automated Block Valve
- Both bleed and double block Valves are utilized to isolate themselves from both convergent, & Divergent process flow or process pressures.
- To achieve this, two balls, a gate, a globe, a needle, and other products are often used. Back-to-back valves, with a third “isolatable” valve in the middle hollow.
- The chamber formed by the primary process isolation when isolation has been created in one or more of the valves, they can be unloaded.
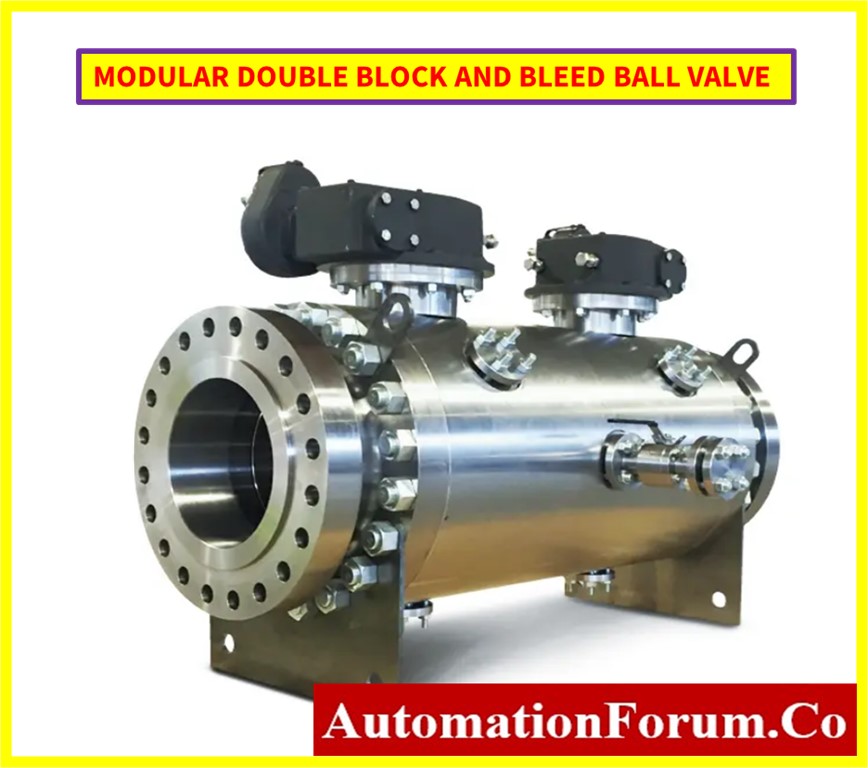
- This is beneficial for flow diverting, sampling, or injection, as well as servicing and/or error checking, where seat leakage can be monitored using the third “Bleed Valve”.
Applications of Automated Block Valves
Generally, both these Double Block Valves and Bleed Valves are available nowadays in the oil and gas industries, but they are used in various process applications.
It is frequently used when the valve chamber must be bled, piping must be disconnected for repair or any of the following circumstances:
- Prevent product residues.
- Detach the equipment from operation to permit for cleanup or restoration.
- Meter calibration
- Service for liquids near a river or communities
- Transmission and indexing
- Chemical accumulation and sampling
- Keep pressure gauges and lever gauges distinct from the rest of the equipment.
- Steam used in the primary process
What Characteristics Should a Twin Block and Bleed Valve Have?
Take into account the fluid characteristics, pressure, and temperature when deciding on a valve, just as you would any other. The most essential factor, regrettably, is how the valve has been used. Should choose the version that perfectly suited your process and requires the possible choices.
What precisely is the feature of a block valve?
Block valves allow liquids to go through with negligible flow restriction and pressure loss when fully opened, and provide a tight seal when fully closed. The most common way to turn things on and off is with gate valves.
What else is a block valve called?
According to the classical definition of “block valve,” it is “any valve that has the possibility to obstruct movement in one or more directions” (or shutdown valve). Regrettably, most individuals utilize the expression to refer to a valve that may stop completely or enable movement.
What is the function of a bleed and block valve?
The block and bleed valve system segregates or prevents the passage of fluid in the system, guaranteeing that fluid from upstream components does not reach downstream elements.
What precisely is a Manual Block Valve?
By definition, manual valves are valves that make use of a manual operator (such as a hand wheel or hand lever) to interrupt and resume flow (block or on-off valves), while some patterns are used for normal throttling.
What exactly is a Block & Bleed arrangement?
A block and bleed manifold is a hydraulic element that merges one or more block valve or isolation valves such as ball valves and one or more bleed or vent valves such as ball valves or needle valves into a single element for participation with some other elements like pressure measurement transmitters, gauges, switches, and so on.