What is a smart transmitter?
A microprocessor-based smart transmitter has a memory that can perform calculations, produce diagnostics and out-perform older, more conventional transmitters when it comes to accuracy and stability.
A Smart Transmitter will also have a wireless communication protocol which can be used to interpret the measurement values of the transmitter and to customize different transmitter settings
Basic components of Smart transmitter:
- Analog to digital signal processing, when it comes to system overall efficiency, is by far the most critical feature of the architecture. It needs to be done correctly to transform the real world physical value, whether it’s energy, temperature, etc. to a digital value.
- Considerations of the CPU are trivial. Power use is important for field instruments. A variety of low-power machines will fill the bill, since the role does not require a great deal of computing ability.
- I / O (remote communication) allows the instruments to communicate bi-directionally as opposed to the analog transmitting paradigm for analog instrumentation in one way.
- ROM and RAM contain both the operational program of the device (firmware) and the scratch memory needed for any assigned task.
- Digital to analog signal generation provides backwards compatibility with existing systems and faster updates than may be available through digital communications
Why we need smart transmitter?
Main difference between a smart transmitter and a conventional analog transmitter is communication and monitoring, a smart transmitter makes both easier.
Engineers no longer only need to calculate the analog output signal, they need to communicate with the transmitter and read the digital signal.
There are two types of communication protocols used in smart transmitter that makes communication easy:
- HART (Highway Addressable Remote Transmitter)
- SMART (Single Modular Auto-ranging Remote Transducer)
HART:
A HART transmitter comprises both a traditional analog mA signal and a superimposed optical signal over the analog signal. This is compliant with modern systems, since it still has the analog signal. The HART model allows instruments to communicate digitally with each other over the same two wires used to transmit an analog instrument signal from 4-20 mA.
SMART:
SMART transmitters opposed to analog transmitters have microprocessor as their integral component, which allows for self-diagnosis abilities, non-linear compensations, re-ranging without doing calibrations, and ability to communicate digitally over the network.
Parts of smart transmitter:
To fully understand the main components of a smart transmitter, a simplified block diagram of the device is shown below:
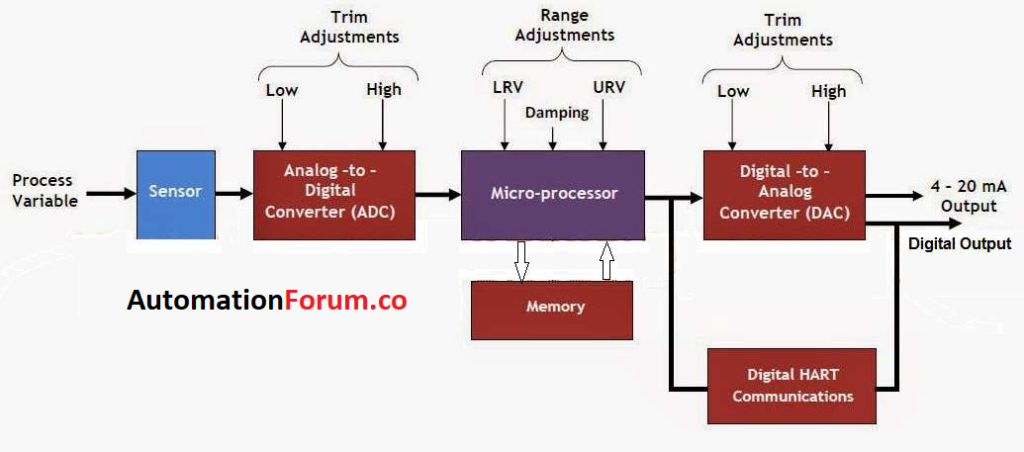
Input section:
The input portion contains the process sensor or transducer as well as the ADC Analog to Digital Converter. The sensor calculates the involved process vector (e.g. friction, temperature, wind, etc.) which is then converted to a relative electrical signal.
Then, the Analog to Digital Converter (ADC) converts the calculated electrical signal into a digital register. This digital count, which is representative of the process variable (PV), is then fed into the microprocessor conversion portion
Conversion Section:
This section includes a microprocessor whose basic function is to transform mathematically from the process vector to the process’s corresponding representation of mA. The memory where the transmitter assembly, initialization and diagnostic data are stored is directly related to the microprocessor.
To measure this mA value, the transmitter’s range values (related to the zero and span values) are used along with a transfer function. Although pressure transmitters can have a square root alternative, a linear transfer feature is the commonest.
Output Section:
The measured mA value reflecting the process vector is fed into a Digital to Analog Converter in this segment, where the mA value is transformed into the real 4-20mA electrical signal. Notice again that the microprocessor has to depend on certain internal tuning factors to bring this performance to the appropriate value.
Adjustment of these calibration criteria is also referred to as a 4-20mA trim or a current loop trim. A smart transmitter using the HART protocol has a microprocessor that manipulates the device data instead of a solely mechanical or electrical direction between the input and the resulting 4-20 mA output signal as received in traditional analog transmitters.
Advantages of smart transmitter:
- High accuracy and reliability
- Single penetration into the measured cycle rather than the multiple penetration needed by discrete devices, enabling and cheaper deployment.
- Allowing remote recalibration or repositioning by giving them a wireless signal.
- Reduction of the amount of spare instruments needed, since one spare transmitter may be programmed to cover any spectrum and thereby replace any faulty transmitter.
- Long-term reliability is increased, and the recalibration frequency required is.
- Data management capability to track plant and instrument performance.