Table of Contents
What is meant by Error?
- Error is defined as a discrepancy between the performance or behavior of a system or object as desired and as it really occurs. Therefore, error in instrumentation is the difference between the true value and the desired value.
Define Measurement Error
- Comparing an unknown quantity to a recognized standard quantity is the process of measurement. It entails interfacing a measurement instrument with the system in question and monitoring the instrument’s response to the response. Since it is extremely difficult to quantify the genuine value, the term “expected value” is employed. The measurement so produced is a quantitative measure of the so-called “true value.” Numerous factors can alter any measurement, so the results rarely match the value that was anticipated. For instance, adding a measuring device to the circuit in question always changes value.
Types of Error
- Static error and dynamic error are the two main categories of measurement error.
- The numerical difference between a quality’s true value and its quantity value as determined by measurement, or the fact that successive measurements of the same amount produce different results, is known as a measuring instrument’s static error.
- Dynamic error is the discrepancy between an instrument’s indicated value and the true value of a quantity that changes over time. Gross errors, also known as human errors, systematic errors, and random errors are the three types of static errors.
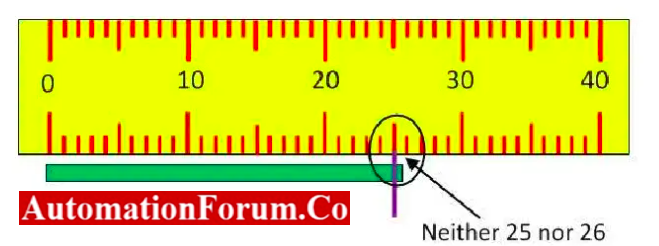
Source of Measurement Errors & Minimizing method
Instrumentation measurement errors can have many different causes. The following are some of the most typical causes of measurement errors and methods to reduce them:
1. Sensor Calibration
- Measurement mistakes can be caused by inaccurate or poor sensor calibration.
- Consistently calibrate sensors in accordance with the manufacturer’s instructions.
- To achieve accurate measurements, adhere to rigorous calibration processes and use traceable standards.
2. Environmental Factors
- Errors in measurement can be caused by environmental factors such temperature, humidity, electromagnetic interference, and vibration.
- Reduce these errors by providing the proper environmental controls, such as maintaining stable temperatures and humidity levels, providing electromagnetic interference protection, and isolating instruments from vibration sources.
3. Interference and Noise
- Errors in measurements might result from interference from neighboring electrical or electronic equipment.
- Use appropriately shielded wires and grounding methods to reduce interference.
- Use signal isolation and filtering techniques to cut down on noise and undesired signals.
4. Signal Drift
- Instruments may experience signal drift over time, which might result in inaccurate measurements.
- To identify and correct signal drift, instruments should be routinely calibrated and verified.
- For sensors that are impacted by temperature changes, use temperature compensation strategies.
5. Signal Loss or Attenuation
- Signal loss or attenuation might result in measurement mistakes due to long transmission lengths or subpar wires.
- To reduce signal losses, make sure you choose the right cable and route it properly. If necessary, use signal amplification or signal conditioning techniques.
6. Nonlinearity and Hysteresis
- When measuring across a large range, nonlinear response and hysteresis in sensors or equipment can cause inaccuracies.
- Select sensors with low hysteresis and linear response characteristics. To account for nonlinear behaviour, perform calibration and corrective processes.
7. Sampling Rate and Aliasing
- Low sampling rates might cause aliasing and incorrect signal representation.
- To prevent aliasing mistakes, choose an appropriate sample rate based on the Nyquist criterion. Take into account the signal’s bandwidth and frequency range when analyzing it.
8. Human Error
- Errors may result from mistakes made by operators during measurement setup, data entry, or data interpretation.
- Give operators the appropriate instruction in how to use instruments, conduct measurements, and handle data.
- When it’s feasible, automate data collection and processing processes and use double-checking procedures.
9. Instrument Resolution
- When monitoring minute adjustments or minute details, low instrument resolution might result in quantization errors.
- Select measuring devices with the right resolution for the precise measurements needed.
10. Measurement Technique
- Errors can be introduced by using inaccurate or incorrect measurement procedures.
- Make sure that measurements are taken consistently and correctly by adhering to defined measurement processes and methodologies.
11. Instrument Drift
- As a result of ageing or environmental variables, instruments may drift over time.
- To adjust for drift and keep accuracy, calibrate instruments on a regular basis.
12. Instrument Limitations
- Every instrument has specific restrictions, including those related to measurement range, linearity, accuracy, and sensitivity.
- Recognize the limitations of your instruments and choose the best one for the particular measuring assignment.
It is essential to adhere to excellent measurement practices, such as accurate calibration, environmental controls, suitable signal conditioning, and adherence to established measuring methodologies, in order to reduce measurement errors.
To provide precise and trustworthy measurements, instruments must undergo routine maintenance, calibration, and verification.
Redundancy or cross-checking techniques can also be used to find and reduce errors.