- What are impulse lines?
- What is the function of impulse line?
- Purpose of impulse lines
- Impulse line problems
- Solutions for instrument Impulse line problems
- Blockages:
- Freezing or condensing
- Leakage:
- Plugging or Drying:
- Line adherence and reaction time:
- Corrosion and Erosion:
- Mechanical Stress and Vibration:
- Diagnose of Impulse Line Blocking in DP Transmitters
- Diagnostic Method for Impulse-Line Blocking
- Expected Advantages of Diagnose of Impulse Line Blocking
- What material is used for impulse line?
What are impulse lines?
- Impulse lines are used to convey process signals from a measuring point to the instruments or control systems in instrumentation and control engineering.
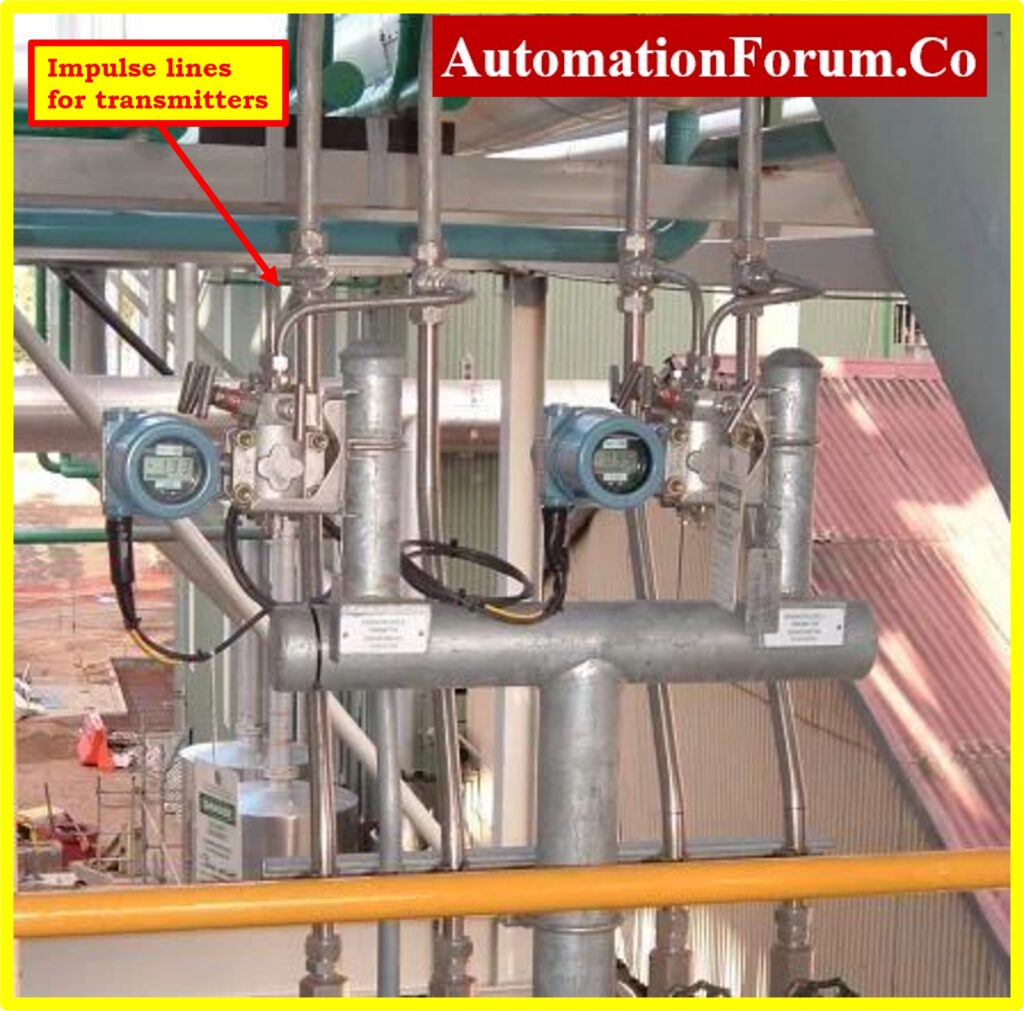
- To connect the process fluid or gas to the sensing element of a pressure or differential pressure transmitter, they are simply small-diameter tubes or pipes.
- An impulse line reliably transmits the process pressure output to the transmitter from the pipe tapping point.
- The process instrumentation loop contains an impulse line. Measurement accuracy is greatly influenced by the impulse line connections between the process tapping point and the transmitter.
- As a result, the proper operation of each element of the process instrumentation loop determines the accuracy of process measurements.
What is the function of impulse line?
Purpose of impulse lines
- Impulse lines are an extremely important component in the measurement of the process parameters.
- There is frequent misunderstanding regarding whether or not the impulse line accurately reflects the process pressure.
- If one’s concentration is primarily on the transmitter and the impulse line is not functioning properly, it will be nearly hard to obtain precise process variables.
- Impulse lines are mostly used to shield delicate equipment from hard or corrosive process conditions including high pressure, high temperature, corrosive fluids, or the presence of particles.
- Impulse lines help prevent instrument damage or contamination while enabling precise measurement or control by separating the instrument from the process fluid.
- Impulse lines shield instruments and devices from industrial fluids and gases.
- This is crucial when the process fluid is caustic, poisonous, high-temperature, or contains solid particles that could damage or contaminate the instrument.
- Impulse lines send pressure signals to instruments from measuring points.
- The impulse line connects the process fluid to the instrument’s pressure-sensing device.
- It gives the device an accurate pressure reading. Impulse lines reduce process volume and instrument reaction time.
- The instrument responds faster to pressure or differential pressure changes with a smaller volume.
- Impulse lines shield instruments from high pressure, temperature, and toxic substances. Impulse lines protect the instrument from process fluid damage, preserving its accuracy and lifespan.
- Drain valves and purge connectors help impulse lines drain fluids. These characteristics remove trapped air, moisture, and impurities, making instrument calibration and maintenance easier without interruption.
- Impulse lines allow instrument placement. They allow instruments to be placed in control rooms or protective enclosures without compromising process measurement or control.
Impulse line problems
Traditional impulse lines are susceptible to a wide range of challenges, including the following:
- They are a necessary component of the process’s containment. If they have leakage, the product will be lost, which could have safety, economic, and environmental consequences.
- Impulse lines may experience leaks as a result of mechanical stress, ageing, corrosion, or poor installation.
- Leaks may cause process fluid to be lost, measurements to be tampered with, and significant safety risks.
- If process equipment requires exotic materials, the impulse lines also require those materials.
- In the event that the process equipment requires exotic materials, the impulse lines will also require it.
- They are susceptible to filling up with gas or liquid, which compromises their capacity to accurately transmit pressure.
- They are susceptible to freezing during cold temperatures. Condensation or freezing inside the impulse lines is possible in applications where there are temperature differences between the process fluid and the environment. This may result in inaccurate measurements or possibly instrument damage.
- Obstructions found within the impulse tubes. Debris, sludge, or leftover process fluid can clog or impede impulse lines.
- As a result, the sensor may receive a restricted flow of process fluid, giving off erroneous readings or slow response times. Impulse lines must be regularly inspected and cleaned to avoid obstructions.
- Damping of pressure signals can be caused by improperly installed lines.
- Impulse lines are frequently fabricated to order and constructed in the plant’s maintenance facility, demonstrating the capabilities of contractors or pipefitters.
- Process fluids can dry out inside of impulse lines if they are not properly emptied or purged, which can lead to clogging or residue buildup. As a result, the system may get contaminated or the transmission of pressure signals may be hampered.
- Impulse lines that are too long or too thin might induce compliance, delaying the transmission of pressure and slowing down instrument reaction time. Designing and choosing impulse lines that minimize compliance and offer quick and precise pressure transmission is important.
- Impulse lines may corrode or erode when exposed to hostile conditions or corrosive process fluids, which can cause line degradation or failure. These problems can be reduced by using the right materials and applying corrosion-resistant coatings or liners.
- Impulse lines may experience weakness, cracking, or loosening of connections in applications with high levels of vibration or mechanical stress. In order to lessen the effects of mechanical stress on impulse lines, proper support, vibration dampening techniques, and flexible line layouts can be used.
Solutions for instrument Impulse line problems
Here are some answers to some of the typical issues with instrument impulse lines:
Blockages:
- To avoid silt or debris buildup, examine and clean impulse lines on a regular basis.
- To prevent solid particles from entering the instrument, place strainers or filters in the impulse lines.
- To clear any obstructions, think about implementing back flushing mechanisms or automatic purging systems.
Freezing or condensing
- Insulate impulse lines to reduce temperature differences and avoid freezing or condensation.
- To keep impulse lines from overheating, use heat tracing systems or heat exchangers.
- In locations with excessive temperatures, take into account employing heated impulse lines.
- To address these problems, it could be necessary to utilize heat exchangers, proper insulation, or heat tracing.
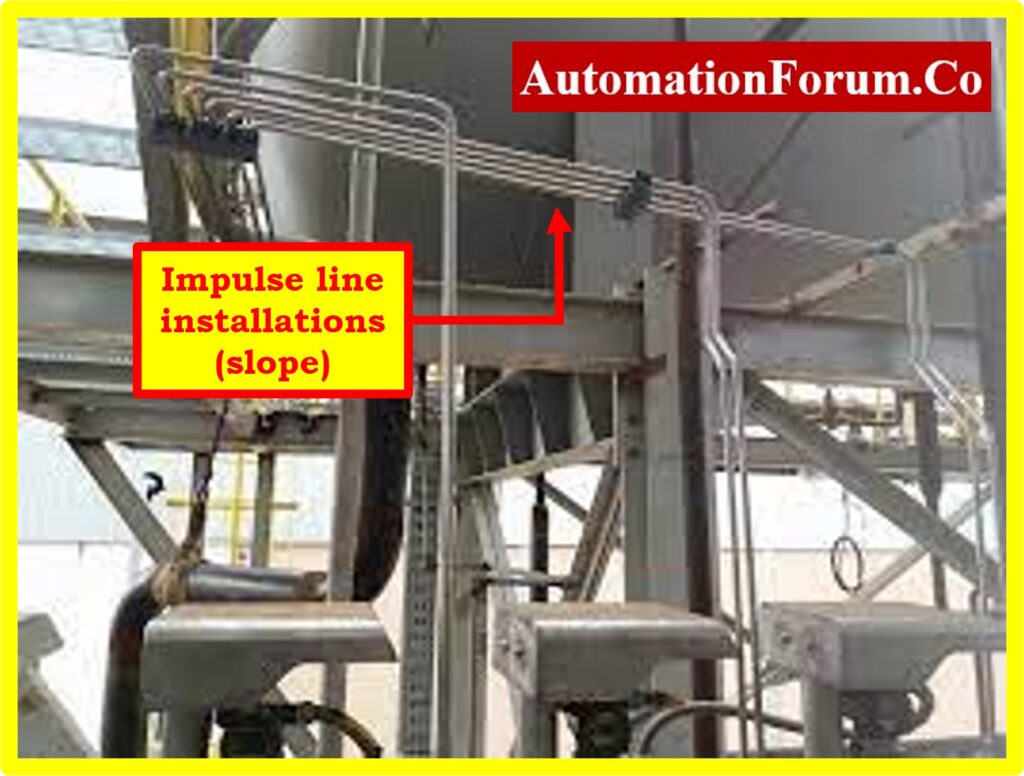
Leakage:
- To find and fix any leaks, perform routine inspection and maintenance on impulse lines.
- Make sure to use the necessary fittings, seals, and fasteners during installation.
- To lessen the possibility of leaks, think about installing secondary containment systems or double containment.
Plugging or Drying:
- To avoid process fluid drying out inside impulse lines, follow correct purging and draining methods.
- To prevent residue building in impulse lines and to maintain cleanliness, use automatic purging or flushing devices.
Line adherence and reaction time:
- Based on the particular needs of the application, optimize the impulse line’s length and diameter.
- Utilize rigid materials or add more support to reduce line compliance.
- To reduce the pressure variations and enhance instrument reaction time, use pulse dampeners or snubbers.
Corrosion and Erosion:
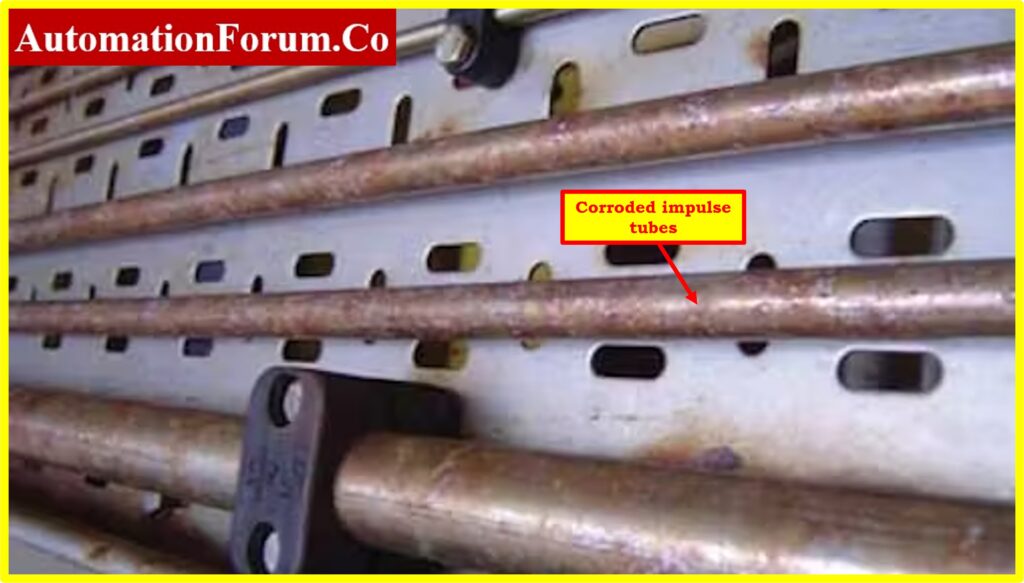
- Depending on the process circumstances, choose materials for impulse lines that are corrosion- and erosion-resistant.
- To increase impulse lines’ resistance to corrosive environments, cover or line them with protective materials.(Resistant coating)
- Impulse lines should be routinely inspected and monitored for corrosion or erosion, and replaced as necessary.
Mechanical Stress and Vibration:
- Support and secure impulse lines properly to lessen the effects of mechanical stress and vibration.
- Utilize techniques or materials that reduce vibration, including rubber isolators or flexible connections.
- In applications with substantial mechanical stress, use flexible or coiled impulse lines to absorb movement.
Diagnose of Impulse Line Blocking in DP Transmitters
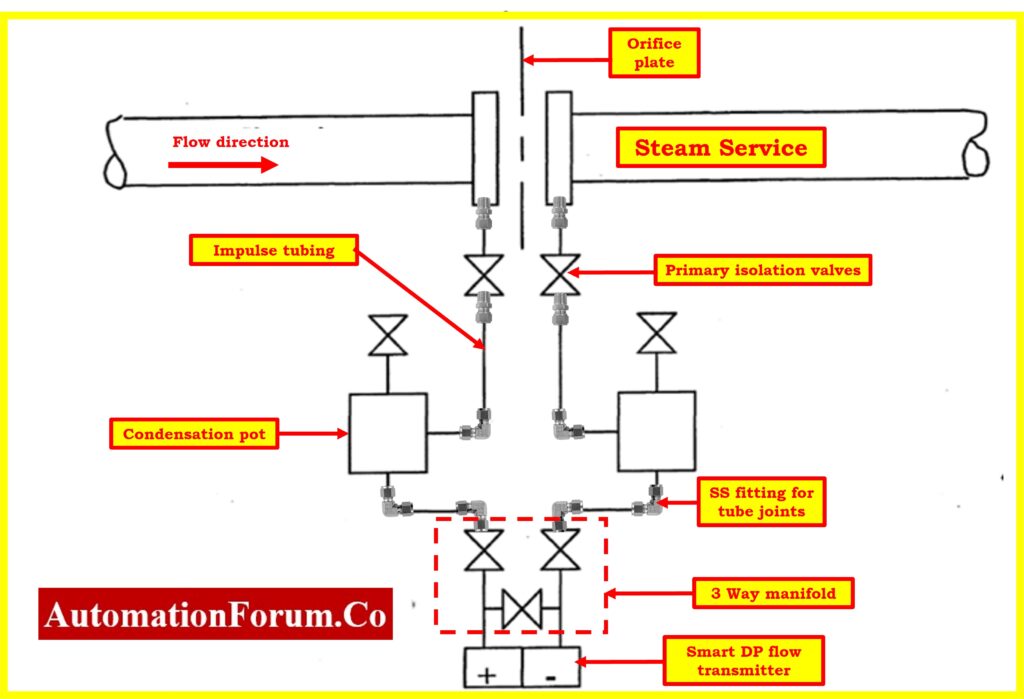
Orifice plates and current DP transmitters are particularly dependable due to their straightforward construction. However, corrosion, fluid condensation, and freezing can all lead to blockages in the impulse lines that send process pressure to the DP transmitter. To ensure effective operation and maintenance, the issue of impulse line blocking must be solved.
A silicon resonant sensor that is built into the DP transmitter (smart multivariable transmitter) allows it to quickly detect both static and differential pressure. These characteristics allow for the creation of a diagnostic method that can identify changes in static and differential pressures. Operators can verify whether an impulse line at a certain installation location has been blocked by using a digital communications network like Fieldbus. The workload and expense of maintenance can be greatly reduced with the use of this information.
Diagnostic Method for Impulse-Line Blocking
- Static pressures that fluctuate as differential pressure components typically fall when an impulse line is blocked.
- The difference between differential and static pressures that are collected at incredibly little time intervals is used to calculate fluctuating components, which are calculated as the square sum of this difference.
- The square root of the summation is used to calculate the amplitudes of fluctuating components. These components are offered as fluctuation components through flowrate adjustment since flowrate changes can affect them.

- Table displays the fluctuating component values for blocking on the Hi-side, Lo-side, or both sides.
- The values for when there is no blocking are also displayed. All fluctuating components become less when both sides of impulse lines are blocked.
- When one side of an impulse line is obstructed, the fluctuating component corresponding to that side decreases.
- The fluctuating component of the differential pressure in this situation is greater than it is in situations where there is no obstruction.
Expected Advantages of Diagnose of Impulse Line Blocking
- Alerts operators and maintenance engineers before an impulse line blockage causes a process interruption.
- Based on blockage thresholds, forecasts when the impulse line will be clogged and provides a solution.
- Blocking substance, flowrate change, and the amount of time needed for corrective action are taken into account while determining blockage thresholds.
What material is used for impulse line?
- Due to its resistance to corrosion, stainless steel (SS 304, SS 316, or a higher metal alloy) is the choice for the majority of applications.
- Nevertheless, a lot of industrial operations still use manifolds, pipes, and process interface valves made of carbon steel.
- The choice of alloys is typically influenced by the process fluid, the surrounding environment, and the system pressure/temperature.