Profibus is a vital fieldbus communication standard in automation, ensuring seamless interaction among devices. Here, we address essential questions for a concise understanding of this key industrial communication protocol.
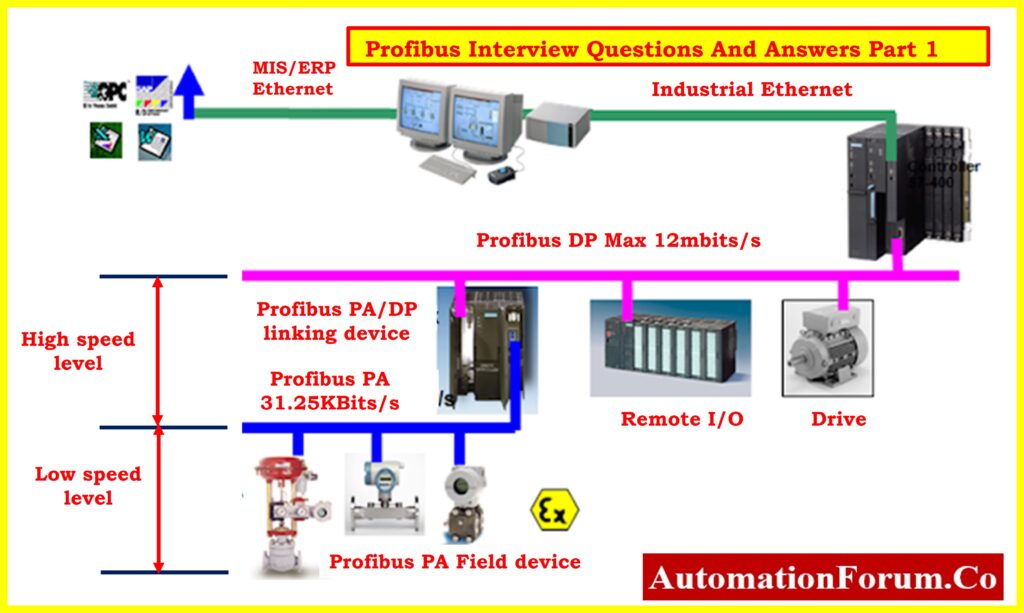
1. Could you define Profibus?
In the field of automation, Profibus is a standard for fieldbus communication that enables communication between systems and devices on the same network.
2. Which are the two Profibus versions?
Profibus-PA (Process Automation), which is used in hazardous situations and for process automation, and Profibus-DP (Decentralized Periphery), which is utilized for high-speed communications, are the two variants.
3. How is Profibus different from other networks used in industry?
The objective of Profibus’s design was to give industrial control systems a reliable and effective communication method. It is unique in that it is deterministic and supports both high-speed and process automation applications.
4. What is Profibus-DP’s maximum data rate?
Profibus-DP has a maximum data rate of 12 Mbit/s.
5. How many devices are able to join a network that uses Profibus?
A single master and up to 126 devices can be supported on a single Profibus network.
6. How does a Profibus master function?
On the bus, the master regulates communication. Slaves reply to its requests by sending them messages.
7. Is it possible for a Profibus network to have more than one master?
It is possible for multiple masters to coexist and monitor their individual slaves in multi-master systems supported by Profibus.
8. What does Profibus Slave mean?
On the Profibus network, a device that complies with requests from the master is called a slave. Communication cannot be initiated by slaves.
9. What is a GSD file for Profibus?
A GSD (General Station Description) file contains information on the characteristics and functionalities of a device. It is necessary in order to configure a network using Profibus.
10. Could you clarify the distinction between Profinet and Profibus?
PROFIBUS is a serial communication protocol, and PROFINET is an Industrial Ethernet protocol: Both are industrial communication standards
11. How does ProfiTrace function in Profibus networks?
For maintenance and troubleshooting in Profibus networks, ProfiTrace is an effective tool. It makes network testing, monitoring, and analysis possible.
12. How is error detection handled by Profibus?
Cyclic Redundancy Check (CRC) is a technique used by Profibus to identify errors in data that is transmitted.
13. What makes Profibus deemed to be deterministic?
Profibus is deterministic since data is transmitted at predetermined times, ensuring reliable and consistent communication.
14. What is the Profisafe system?
Profisafe is a Profibus and Profinet profile that specifies safety-related communication.
15. What is the power source for Profibus-PA?
Profibus-PA supplies power and communication over the same pair of wires using a method known as Fieldbus Intrinsically Safe Concept (FISCO).
16. How may a Profibus network be terminated?
In order to eliminate signal reflections, resistors should be used to terminate a Profibus network at both ends.
17. What is the longest possible Profibus segment?
The baud rate determines the maximum length. A segment up to 1200 meters can be had at the slowest speed (9.6 Kbps). A maximum of 100 meters can be covered at the fastest speed (12 Mbps).
18. How would you describe Profibus addressing?
On a Profibus network, every device is assigned a unique address that falls between 0 and 125. The master has reserved address 126.
19. How may issues with a Profibus network be diagnosed?
Tools such as ProfiTrace are useful for problem diagnosis. Moreover, many Profibus devices contain diagnostic registers providing information on errors and conditions.
20. What does a Profibus repeater do?
In order to build a branch inside a Profibus network or to increase the length of an existing network, a repeater is utilized.
21. What are some common uses for Profibus?
In a wide variety of industries, including manufacturing, process control, and automation, Profibus is utilized for a variety of activities, including monitoring temperature, pressure, flow rate, and other related parameters.
22. What is the purpose of a Profibus connector?
To link a device to the Profibus network, utilize a Profibus connection. To enable or disable the bus termination, it usually has a termination switch.
23. What do a Profibus connector’s LEDs indicate?
The network status is shown visually by the LEDs. They can display information on the network’s activity, the transfer and reception of data, and error rates.
24. What are Profibus’s main advantages?
Profibus provides predictable, reliable, and efficient communication. Additionally, it supports a large range of devices and is highly scalable.
25. How is collision detection handled by Profibus?
Because Profibus employs a token-passing protocol, communication can only begin by the master device that has the token, preventing collisions.
26. Could you describe a Profibus telegram’s structure?
Fields for synchronization, recipient address, control information, data, and error checking are all included in a Profibus telegraph.
27. Describe a Profibus proxy.
Communication between a Profinet network and a Profibus network is made possible by a Profibus proxy.
28. What benefits does Profibus-PA provide?
Process automation is the focus of Profibus-PA, which also provides integration with Profibus-DP, power and communication over the same wire, and intrinsic safety for hazardous areas.
29. In a Profibus network, how is device replacement managed?
When a device is swapped out, the master will automatically detect the new one, avoiding the need for reconfiguration.
30. What data types are Profibus compatible with?
Many data types, including Boolean, Byte, Word, Double Word, and Real, are supported by Profibus.
31. What is the definition of a Profibus DP slave?
A device that executes the commands of the DP master in a Profibus DP network is known as a slave. It is unable to initiate communication.
32. What kinds of wires are utilized in a network that uses Profibus?
Depending on the Profibus version being used, shielded twisted pair cables are usually utilized for Profibus networks.
33. What is Profibus International?
The group that supports and advances the Profibus and Profinet technologies is called Profibus International. It is in charge of training, certification, and standardization.
34. Can Profibus and Profinet networks communicate with one another?
Yes, Profinet and Profibus networks may communicate to one another through the use of a proxy.
35. What does a Profibus DP master do?
Data requests and commands are sent by a Profibus DP master, which also manages communication with the DP slaves.
36. How do you establish synchronization in a Profibus network?
In Profibus, synchronization is achieved by precisely timing the transfer of data and utilizing a master clock.
37. What security features is Profibus equipped with?
The Profisafe profile for safety-related communication is supported by Profibus. In order to ensure data integrity, it also has error detection systems.
38. What is a network profile for Profibus?
A Profibus network profile is a specification that details the characteristics and actions of a specific class of application or device within the network.
39. Could you clarify the distinction between Profibus DP and Profibus FMS?
An advanced communication protocol called Profibus FMS (Fieldbus Message Specification) is utilized for communication between equal partners. Profibus DP is designed to exchange I/O data at high speeds in a cyclic fashion.
40. How is network failure handled by Profibus?
Diagnostic registers on Profibus devices are able to detect problems with the network. Redundancy is also used by some networks for important purposes.
41. What kinds of hardware are compatible with Profibus networks?
Several devices, including as PLCs, sensors, actuators, drives, and more, can be connected.
42. How do devices in a Profibus network become configured?
Software tools are used to set up devices, and the manufacturer’s GSD file is used to establish the device parameters.
43. How does Profibus manage data that is time-sensitive?
Profibus ensures timely transmission of data by utilizing a token-passing system.
44. Could you describe the OSI model for Profibus?
With only three layers—the Physical Layer (1), Data Link Layer (2), and Application Layer (7)—Profibus employs a condensed version of the OSI paradigm.
45. How is device failure handled by Profibus?
Diagnostic features on Profibus devices allow them to report malfunctions. Redundancy may be utilized in specific circumstances to guarantee ongoing operations.
46. What function does a Profibus coupler serve?
A Profibus coupler is used to join two Profibus network segments together. This is frequently done to increase the network’s coverage area or to join Profibus-PA and Profibus-DP segments.
47. How is real-time data handled by Profibus?
In order to ensure that data is sent and received at exact, consistent intervals, Profibus uses its deterministic nature to manage real-time data.
48. What Is ProfiDrive?
A common interface for a range of drives is provided by ProfiDrive, a Profibus profile specifically created for drive technology.
49. What is a segment of a Profibus network?
A Profibus network segment is an area of the network that is connected continuously—that is, without interruptions from repeaters or other devices—by cables.
50. What is redundancy in Profibus?
The method of having backup devices or networks in place to ensure continuing functioning in the event of a failure is known as profibus redundancy.