- Emergency Block Valves
- Requirements & Function of Emergency Block Valve:
- Location of Emergency Block Valve
- Marking of Emergency Block Valve
- Testing of Emergency Block Valve
- Proof Testing of Emergency Block Valve
- Generic Rules for Emergency Block Valve
- What is an Emergency Block Valve?
- What is a block valve also known as?
- What is the purpose of a block valve station?
- Block Valve Station
- What is the difference between BDV and SDV?
- What material is a valve block?
- What is an example of a block valve?
- What are the three most common types of block valves?
- What type of valve is SDV?
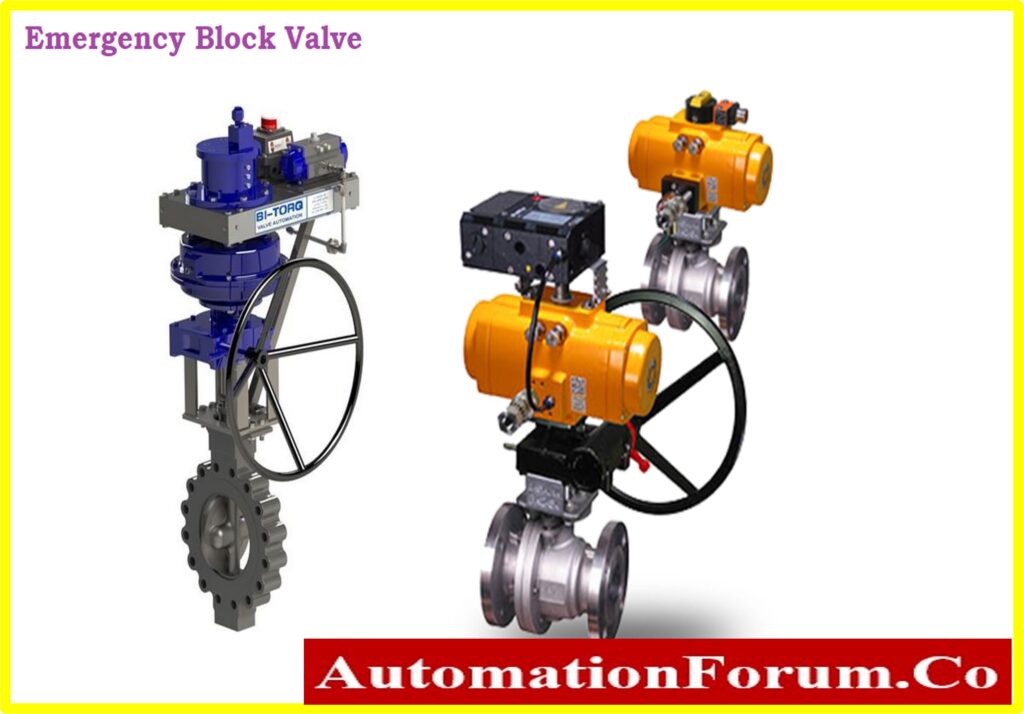
Emergency Block Valves
- Emergency Block Valves are also renowned as Emergency Shut-Down Valves (ESDVs) or Emergency Isolation Valves (EIVs) (EIV).
- “Emergency Block Valves are intended to regulate a dangerous situation,” as per the configuration of Refinery Valves and Accessories for Control and Safety Instrumented Systems API-RP-553.
- These are Emergency Isolation Valves that have been intended to avoid the uncontrolled release of combustible or organic chemicals.
- Any kind of Emergency Block Valves in a fire zone that controls flammable liquid must be fire-safe.
- Emergency Block valves are essential in Safety Instrumented Systems (SIS) to isolate the process completed in the event of a potentially dangerous situation that calls for the process to be shut down for the safety of both workers and machinery.
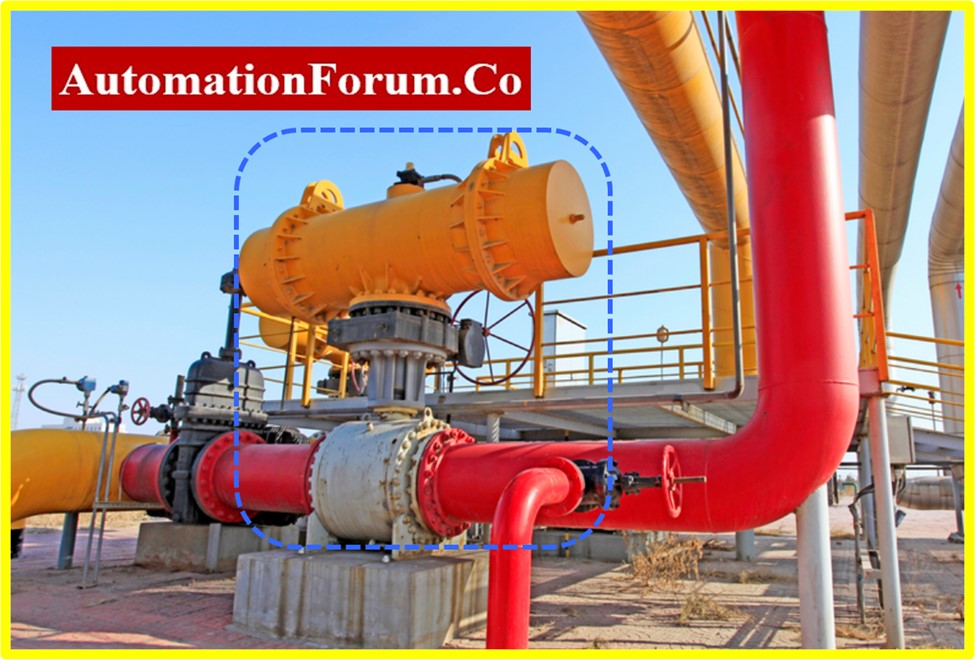
- A metal seated Ball Valve, Gate Valve, or Butterfly Valve can all serve as an Emergency Block Valve to cut off or isolate a flow of hazardous fluid.
- Emergency Block Valves are part of the prevention and control layer and perform after a hazard has transpired.
- This Emergency Block Valve is bolted between the source of inlet pressure and the valve regulator.
- Through manual interference, an Emergency Block Valve (EBV) allows positive equipment isolation, such as Storage Tanks, Vessels, or Piping systems.
Requirements & Function of Emergency Block Valve:
- Emergency Block Valves (EBVs) can be a manual process or remotely powered ON/OFF valves or MOVs (Motor Operated Valves).
- EBVs must have functioned in an extant event of an emergency. They are not, therefore, preventive layers, but prevention and control layers.
- A Safety Instrumented System or basic process control system may also include an Emergency Block Valve.
- In these kinds of instances, these valves must have a manual override to close irrespective of SIS or BPCS action.
- Motorized Operated Valves that are remotely controlled EBVs need to constantly have their selector switch set to Remote.
- If the same valve is requested to be changed to Local Mode, bypass authorizations must be collected.
- When the pressure in the protected system exceeds a certain threshold limit, the valve needs to be immediately shut, cut off, or isolated from it to prevent accidents, leakage, and other disasters.
- It is appropriate for Gas, Natural Gas, & Liquefied Petroleum Gas storage, transportation, and for other combustible gas applications.
- When an EBV is needed, many companies use their own technical and safety standards.
- These may occur in fire protection, pliping, instrumentation, safety, and operations design manuals.
- The need for an EBV may be determined by a hazard review (Hazop, LOPA, SIL), or it may be a requirement of HSE guidelines.
- To describe the whole design, different mixtures of standards may also be needed.
- As an example, a safety standard might say that you need an EBV, a fire protection standard might say that the device needs to be protected from fire, and a monitoring standard might say how the device works and what settings it needs.
- The main point is that you should first look into the standards of the structure’s owner.
- Any design reason or selection factors in the owner’s standards are likely to be the owner’s interpretation of the regulations that apply.
- Local site requirements, insurance requirements,or even environmental permit requirements can affect the unique need in a particular unit
Location of Emergency Block Valve
The Emergency Block Valve has been mounted on the liquefied hydrocarbon spherical tank’s inlet and outlet pipelines.
Since Emergency Block Valves are the principal cause of isolation in plants, EBVs are generally situated at
- Battery Limits
- Loading / Unloading Stations
- Compressor Suction / Discharge
- Pumps
- Storage & Process Vessels
- Reactors and Columns
- Tank bunds
Since the main goal of most EBV placements is to stop the spread of things that can catch fire, most EBVs are likely to be exposed to fire.
This would be especially true if EBVs were placed in vessel outlet lines (as close to or on the vessel exit flange as possible) or in individual pump suction lines.
The “Development & Erection” of Liquefied Petroleum Gas (LPG) infrastructure” explicitly states that the block valve on the liquefied hydrocarbon pipeline should be as nearer to the tank body as possible, preferably nearer to the tank wall pipe outlet flange, for the comfort of maintenance as well as operation.
Marking of Emergency Block Valve
Emergency Block Valves should be designated in the Piping & Instrumentation Drawings, labeled as a Block valve in the field (using the standard tag plate standard), and incorporated into the plant emergency management process.
Testing of Emergency Block Valve
- Emergency Block Valve must be tested at a particular frequency (generally = 5Y).
- If the EBV also serves as a Safety Instrumented System or a Basic Process Control System, the SIS/BPCS certification requirements will be imposed .
- EBV must comply with the following SIS certification requirements:
- Visual Inspection
- Proof testing
- Overhauling
Proof Testing of Emergency Block Valve
- Usually, emergency block valve-proof tests are carried out.
- Stroke check every 5 years for automated valves and
- Stroke check every 3 years for manual valves.
- Since Emergency Block Valves should always continue operating after an incident has taken place.
- The Maximum Allowable Leakage Rate (MALR) for these EBVs is regarded as extremely high.
- As a result, the Function test (Stroke test) can be deemed as a Proof test with limited diagnostic coverage (also known as the Imperfect proof test), and the Seat leakage test can be delayed indefinitely only until Overhaul time.
- Seat leakage for EBV is categorized as “Deferred Seat Leakage” because of inadequate proof testing (in which the seat leakage during proof testing is not validated).
- As a result, EBVs must be evaluated for Seat leakage once every 16 years (for clean service). This frequency may be reduced to around 8 years in case of severe application.
Generic Rules for Emergency Block Valve
- When an EBV should indeed keep operating throughout a fire, it needs to have a fire-safe or fire-protected design.
- EBVs must be recognized in the maintenance documentary evidence (for example, in ERP/SAP or a similar maintenance monitoring system).
- It is advisable to test EBVs in-line.
- Partial stroke testing may assist in widening the required full test intervals.
- Manually operated EBVs must always be recognized and positioned by plant and site emergency personnel.
What is an Emergency Block Valve?
In the case of an explosion or fire, an Emergency Block Valve (EBV) is employed to separate flammable or harmful chemicals.
What is a block valve also known as?
In a fluid handling system, a separation valve, also identified as a block valve, stops the flow of process media to a particular location, usually for maintenance or safety reasons.
What is the purpose of a block valve station?
Block Valve Station
- These Block Valve stations are the principal protection lines for pipelines.
- The operator may utilize these valves to separate any portion of the line for maintenance or to disassociate a fracture or leak.
- Depending on the form of the piping system, block valve channels are generally situated every 20 to 30 miles (48 km).
What is the difference between BDV and SDV?
Shutdown Valve (SDV) is a process control emergency shutdown valve that functions as a safety device in the case of an emergency. Blowdown valves (BDVs) are additionally employed as safety integrity functions (SIFs) to enable continuous process streams.
What material is a valve block?
The valve block is made up of:
- Steel: 12L14, Iron, Carbon steel, and more.
- Aluminum: 6061T6, 7075T6, and more.
What is an example of a block valve?
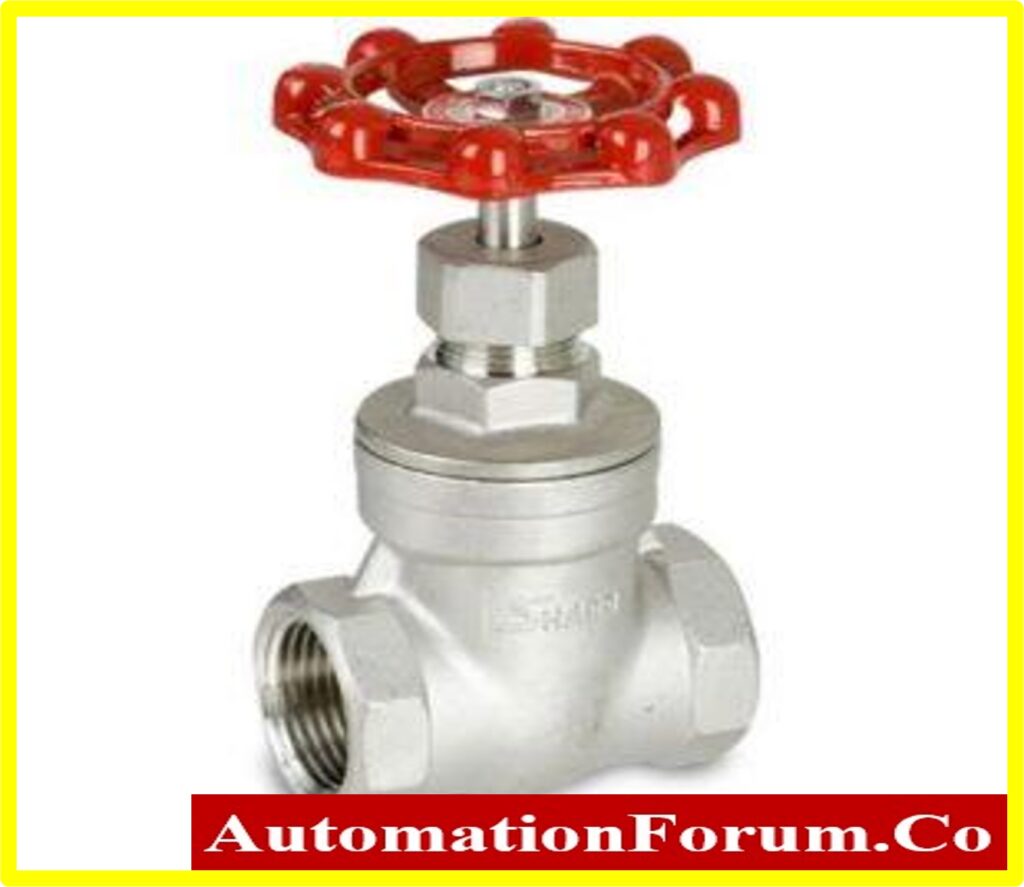
- Full-Bore Ball Valves are excellent examples of block valves since they’re not suitable for decelerating or restricting flow but succeed at actually stopping it and allowing it to pass through uninterrupted.
- Ball check valves really aren’t block valves even though they generally constrain flow even when tried to push open by fluid.
What are the three most common types of block valves?
The three major valve types of control valves:
- Double Block and Bleed,
- Manifolds valve and
- Ball Valves.
What type of valve is SDV?
- When a dangerous situation is identified, a shut-down valve (also known as an SDV or Emergency Shutdown Valve.
- An Emergency Shutdown Valve (ESDV) is provoked to prevent the passage of a potentially dangerous fluid or supplementary hydrocarbons (gases).
- This safeguards against prospective damage to individuals, machinery, or the surroundings.