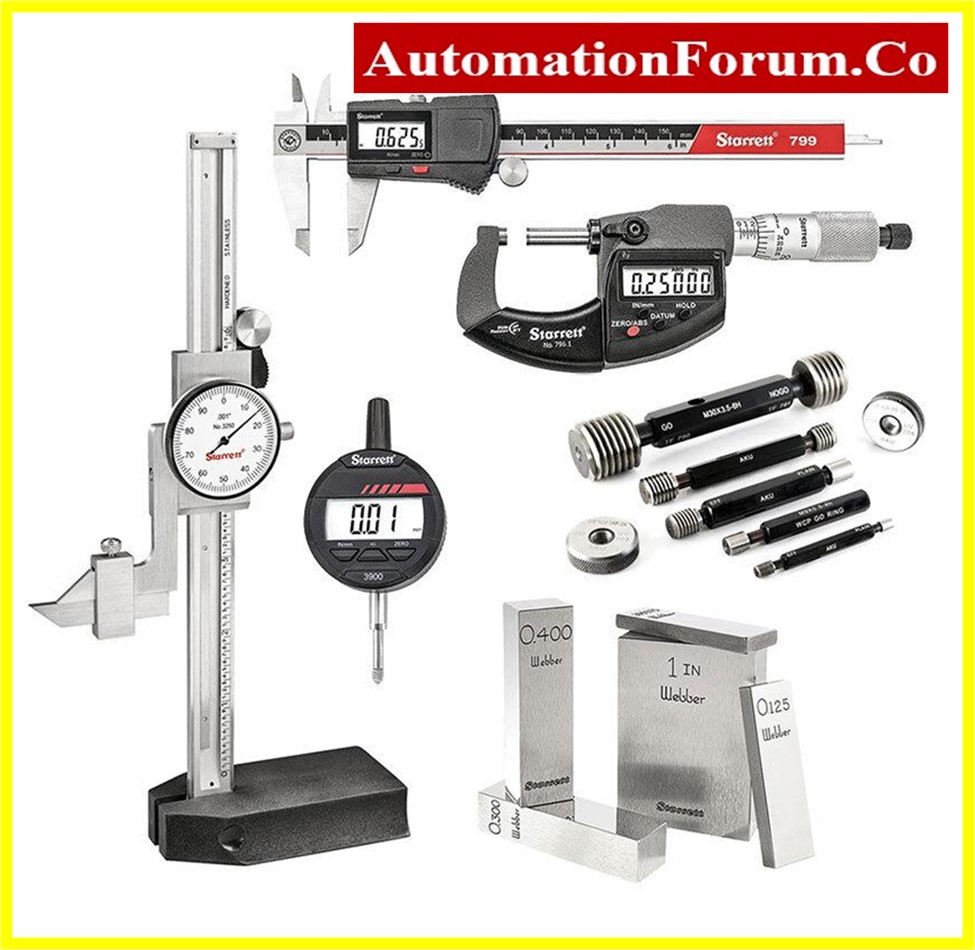
What is Metrology?
- The term metrology is defined as a science or scientific study of measurement. But the definition of metrology is the science of measurement enfolding both theoretical & experimental determinations at any uncertainty levels of various science and technical fields.
- This measurement consists of tools called metrology tools to measure objects.
- This principle of metrology is applied to the CNC machining process for accessories with complicated designs throughout the production.
- Every part of the CNC machine is designed and manufactured with the right specifications such as size and tolerance to be measured by using sophisticated CNC metrology tools.
- The task of measurement is quite simple just using a ruler or measurement tape to spot the points in terms of millimeters or inches.
- When we are dealing with measurements the tolerance of dimensions of CNC machined parts must be lesser than + 0.001 inches. This kind of measurement requires advanced tools with sufficient knowledge.
- Nowadays each and every CNC machine has adopted various sets of metrology tools, based on the type of work, work quality, & quantity.
Describe various metrology tools in modern CNC machine shops.
A list of various metrology tools is shown below.
- Coordinate Measuring Machine (CMM)
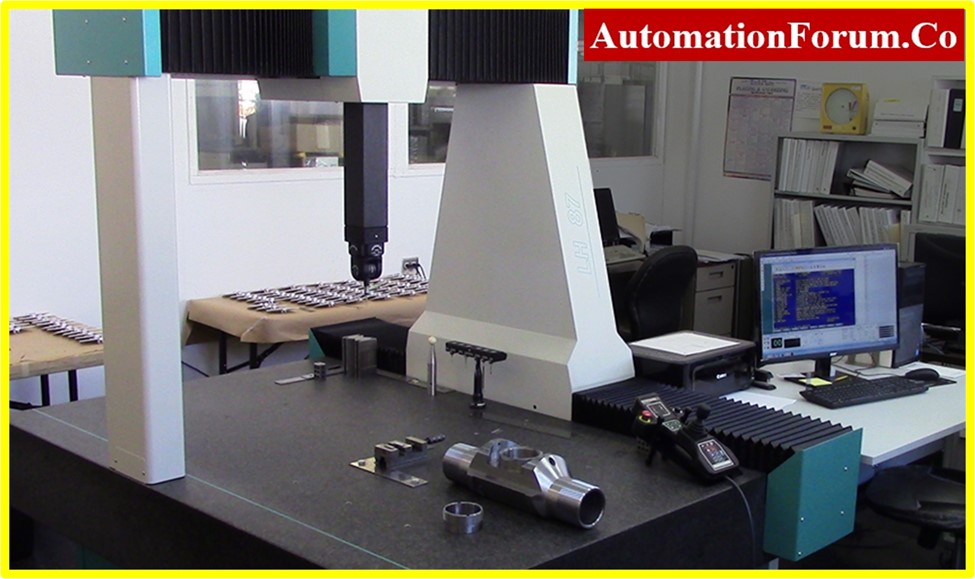
- The Coordinate Measuring Machine initiates a mechanical coordinate system with the objective of measuring the machine as an original plane to assemble coordinate values of measured points on the surface of the object to be measured.
- It is intended to determine different features for small hardware parts of the whole system.
- This Coordinate Measuring Machine in a CNC determines the dimension of a workpiece or a job in all X, Y, & Z axes.
- Some kind of CMM records the measured data that are large enough to measure parts with a size of 10 meters or more than that.
- The measurement of the workpiece or machine’s dimensions in a CMM machine is taken in two different ways
- Touching probe
- Camera or laser beam
- Profile Projectors
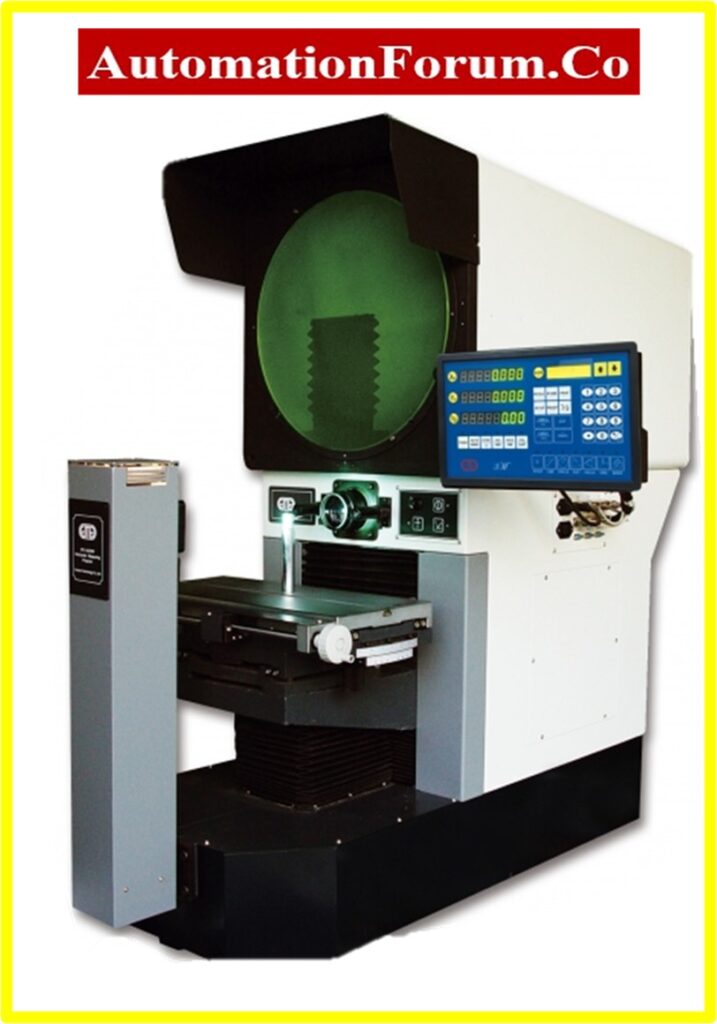
- Profile projectors are a class of optical measuring instruments initially used as an inspection tool for workpiece outlines.
- The function of Profile projectors is similar to optical microscopes.
- Generally, this Profile projector is also known as shadowgraph.
- Profile Projector consists of placing the target on the stage, & flashing a light beam on it from the bottom to safeguard the shadow. Finally this telecentric optical arrangement makes the measurement more precise.
- Height Gage
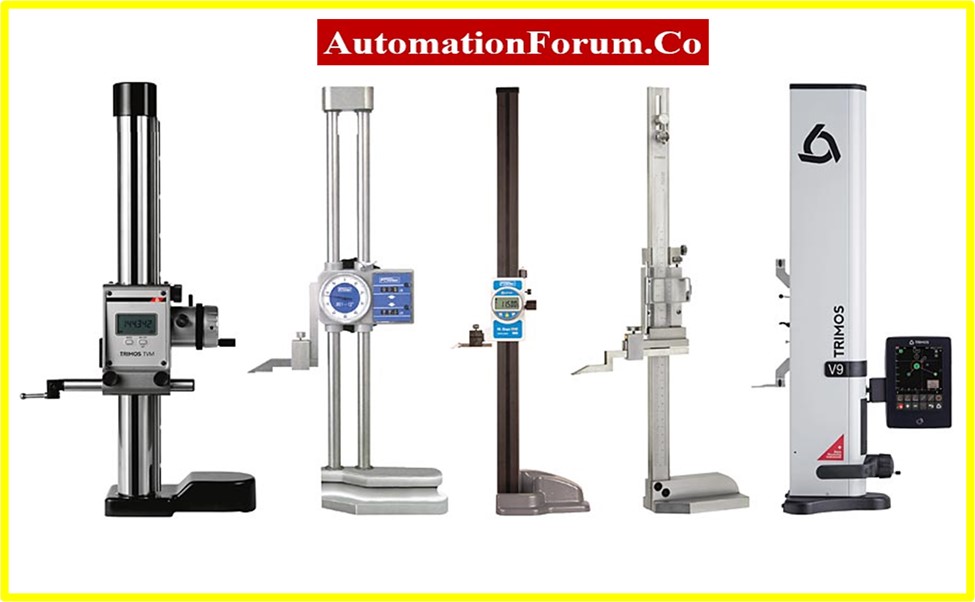
A height gauge is another metrology tool in CNC machining to determine object height of large objects more precisely.
- Surface Plate
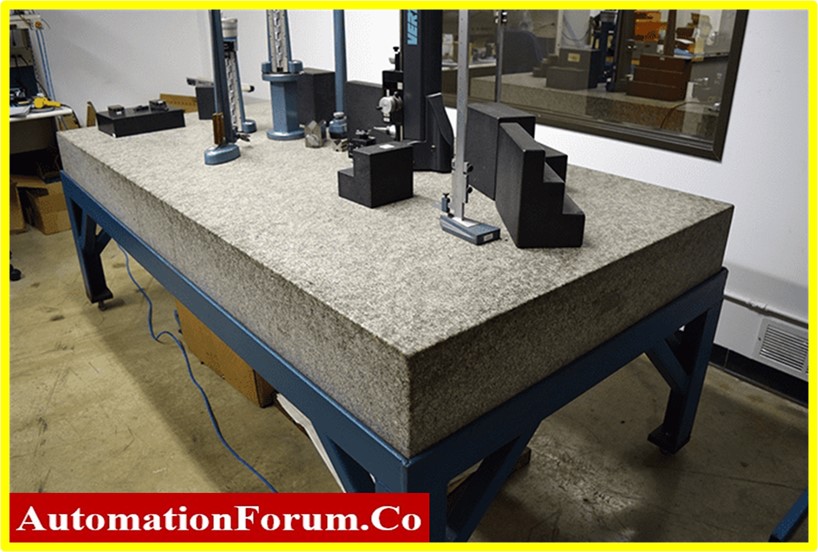
- The surface place is a flat solid plane intended for exact inspection, marking, & tooling arrangement.
- This slide plate is required to form shape adjustment, & calibration correction of errors for useful results.
- Granite is the best example of a surface plate
- Laser Scanning Arms
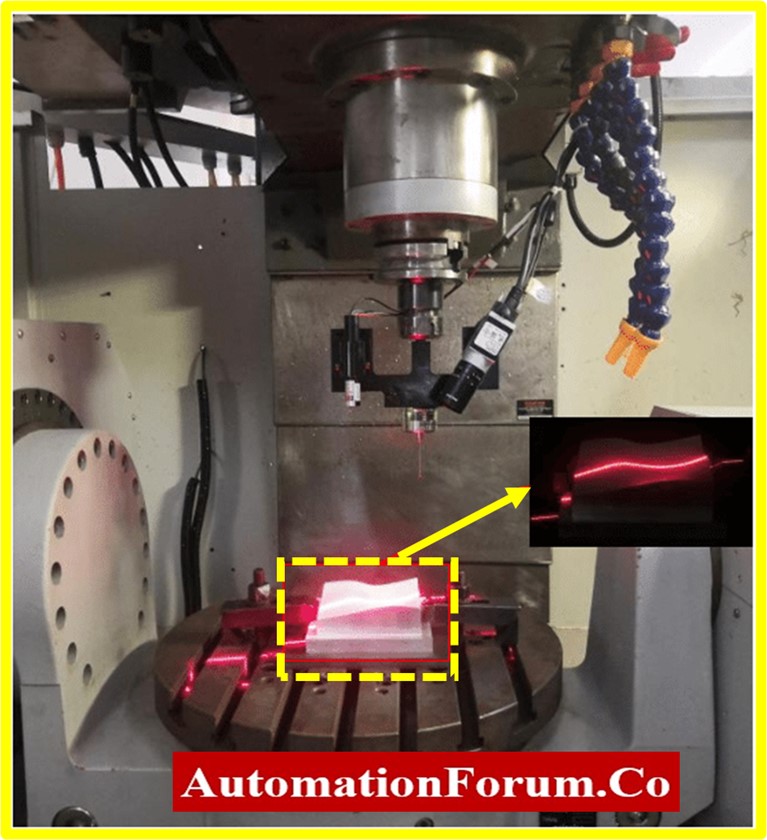
- Laser scanning arms determines the dimensions of a wider range simultaneously,
- This arm enables the determination of thousands of data points automatically.
- Go/No-Go Gauge
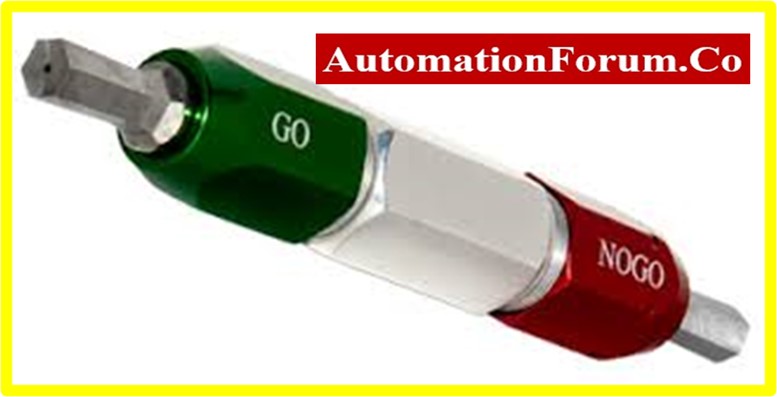
- The go/No-Go gauge is an observation device to inspect the workpiece for a specific range of tolerance for the go/no-go test.
- Usually, this workpiece consists of two tests, one is a Go test called pass one test, & the other is a No-Go test called fail the other test.
- Micrometer
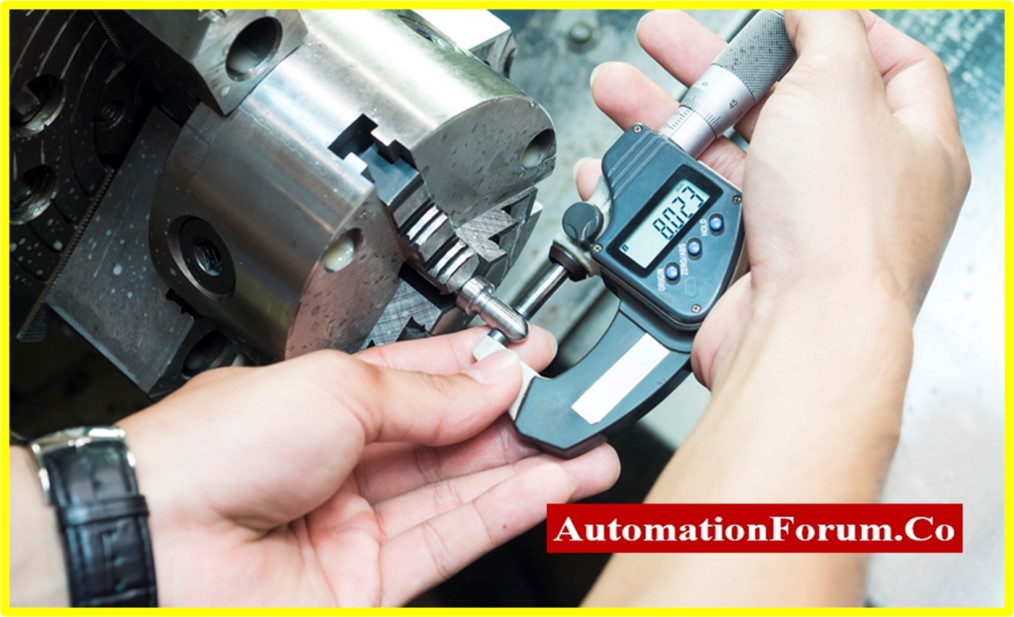
- Micrometer or Micrometer Screw Gauge is used as a CNC measuring tool to determine precise measurements of machined components.
- Generally, working with digital calipers, vernier calipers, & many more metrological equipment.
- Calipers
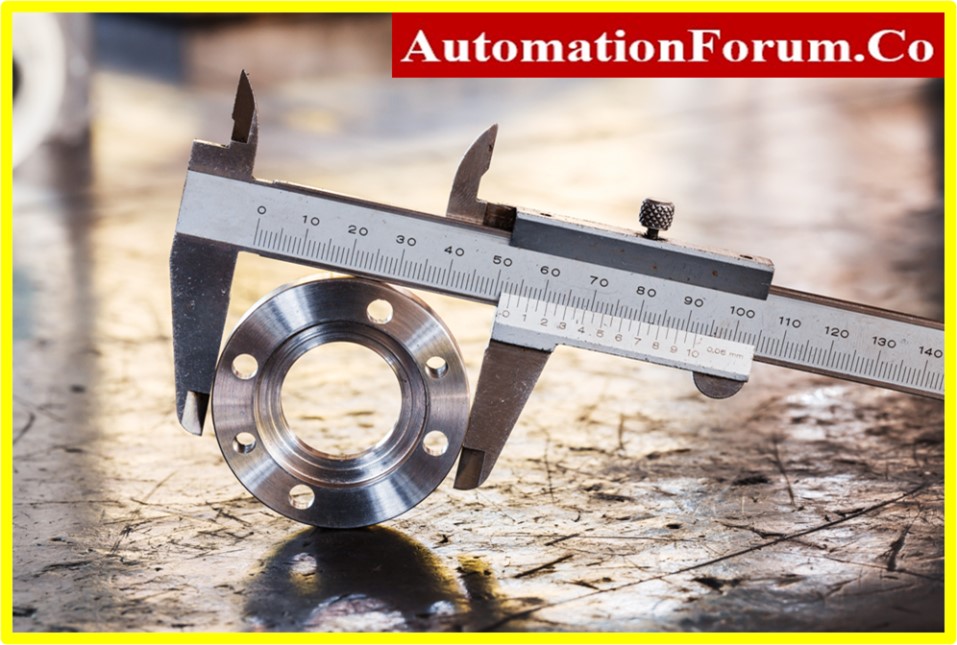
- A caliper in CNC machining is a metrological device used as a measuring tool to determine the exact separation between two opposite faces of the job or workpiece.
- Usually, there are wide ranges of calipers available in the market, and each range of calipers varies in shape and size.
- Air Gage
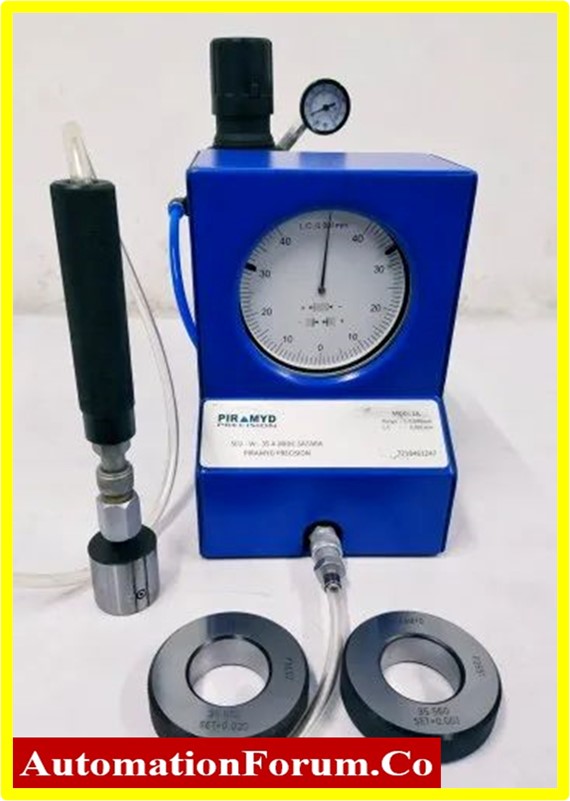
- The main objective of an Air Gauge in CNC machining is used to eliminate air present in a calibrated nozzle,
- This Air Gauge records or stores the rate at which the air returns to the nozzle of multiple sensors.
- Object size is determined by reading the rate of airflow between the measuring tool, & the measured object.
Applications of Metrology Tools for CNC Machining
- Quality Control in Manufacturing
- Inspection of Prototype Parts
- Tooling Verification and Calibration
- Calibration of CNC Machines
- Alignment and Positioning
- Geometric Tolerance Verification
- Surface Roughness Measurement
Advantages of Metrology Tools for CNC Machining
- Improved Accuracy
- Increased Efficiency
- Time and Cost Reduction
- Better Quality Control
- Standard Compliance
- Calibration and Maintenance
- Verification of Complex Geometries
Limitations of Metrology Tools for CNC Machining
- High Initial Cost
- Technical Expertise Required
- Time-Consuming
- Environmental Factors
- Accessibility and Size Constraints
What is the extension form of CNC, & CMM?
The extension form of
- CNC is Computerized Numerical Control.
- CMM is a Coordinate Measuring Machine
Define CNC metrology
CNC Metrology is defined as the science of measurement. Here principles of metrology are used to ensure that each part is machined to the right size and shape with specific tolerances.
Define the principle of CMM
The CMM makes use of a probe to determine the physical characteristics of a dimensional surface.
This probe is moved along all three axes X, Y & Z to determine the spatial displacement of the workpiece.
What are the parts of a CMM?
The major components of CMM are
- The machine body.
- The measuring probe
- Control or computing system
- Measurement software
How accuracy of CMM is determined?
- The accuracy of CMM is regulated by ISO 10360-II, using notation such as “2.3 + L/600.
- The accuracy of CMM is determined by using the relation
E = A + L (1 ÷ K)
What is CNC code?
The most popular programming language for CNC is G-code or RS-274
What are CNC parameters?
Speed is the Feed rate CNC parameter. The speed is determined in distance units per minute like mm/m, or in/m