Table of Contents
- 1. What are inspection points for a cable tray installation?
- 2. What are inspection points for field instruments with impulse tubing?
- 3. What are inspection points for cable laying?
- 4. What are inspection points for Junction Box and Marshalling cabinets?
- 5. What are standard methods or ferrules addressing to and from a Junction Box?
- 6. What is final RFI? When should it be raised?
- 7. What is Schedule Q?
- 8. What are the various levels of Inspection? Explain.
- 9. What is ITP? What are Hold and Witness Points?
- 10. What is RFI? When should an RFI be raised?
- 11. What is Cable tray and how is it identified separately for Electrical and Instrumentation?
- 12. What is Calibration and what is process calibration?
- 13. What is the loop and how is the loop folder made?
- 14. What is the specialty rather characteristics of loop check? How do you come to know that loop check is completed?
- 15. What is the standard and what is Standardization?
- 16. What is Inspection?
- 17. What are the responsibilities of QC Inspector?
- 18. What should be the attitude of a QC Inspector while carrying out an Inspection activity?
- 19. What are the requirements for carrying out installation inspection of any instruments and receiving inspection of the said equipment?
- 20. What is the CCTV System?
- 21. What are the differences between QA & QC activities?
- 22. What is Schedule ‘Q’ and how many appendices are there in schedule ‘Q’?
- 23. What are the linked documentations carried out related to QC activity for oil & gas construction project?
- 24. What is process control system?
- 25. What are QCP, QMP, and ITP?
1. What are inspection points for a cable tray installation?
- Material verification involves ensuring that the materials used for the cable tray meet the approved specifications in terms of quality, size, and type. This includes checking for any defects or inconsistencies.
- Sizing refers to confirming that the cable tray dimensions align with the requirements of the installation, ensuring it can accommodate the cables effectively.
- Secure fixation entails properly securing the cable tray to the structure, such as walls or ceilings, to prevent any movement or instability.
- Proper spacing between trays is essential to maintain clearance and prevent interference between different types of cables.
- Grounding should be correctly installed to ensure electrical safety and compliance with regulations.
2. What are inspection points for field instruments with impulse tubing?
- Material verification involves confirming that the materials used for impulse tubing meet the approved specifications, including material type and size, to ensure compatibility and durability.
- Adherence to hook-up specs ensures that the installation of field instruments and impulse tubing follows the designated configurations and connections outlined in the engineering documents.
- Tubing routing inspection involves checking the path of the impulse tubing to avoid any obstructions or interference that could impact the performance or safety of the instrumentation system.
- Pressure testing is conducted to verify the integrity of the impulse tubing system, ensuring it can withstand the required pressure conditions without any leaks or failures.
- Checking for proper insulation of impulse tubing is crucial to prevent electrical hazards and ensure safe operation.
3. What are inspection points for cable laying?
- Material verification ensures that the cables used for laying meet the specified requirements in terms of quality, type, and size, to ensure reliability and longevity.
- Adherence to routing drawings involves following the provided cable routing diagrams accurately to ensure proper installation and avoid any deviations that could lead to issues later on.
- Numbering and bending inspection ensures that cables are appropriately labeled and bent according to the requirements, facilitating identification and preventing damage during installation.
- Tool usage verification involves confirming that the correct tools and equipment are used for cable pulling and laying to ensure efficiency and safety.
- Checking for proper cable cleating during installation is important to ensure secure fastening and prevent cable movement or damage.
4. What are inspection points for Junction Box and Marshalling cabinets?
- Material verification involves confirming that the materials used for Junction Boxes and Marshalling cabinets meet the approved specifications, including type, size, and quality, to ensure durability and functionality.
- Secure installation entails properly mounting the Junction Boxes and Marshalling cabinets, ensuring they are firmly fixed and stable to prevent any movement or instability.
- Labeling involves providing clear and accurate identification on the Junction Boxes and Marshalling cabinets, including tags or nameplates, to facilitate maintenance and troubleshooting.
- Stability inspection ensures that the Junction Boxes and Marshalling cabinets are securely installed and do not shake or vibrate, which could potentially cause damage to the equipment or connections.
- Checking for proper cable gland installation is important to ensure ingress protection and prevent moisture or dust from entering the enclosures.
5. What are standard methods or ferrules addressing to and from a Junction Box?
- Terminal addresses should be close and complete for both ends, ensuring clear communication and accurate connection between instruments and the Junction Box.
- It’s important to ensure that the terminal addresses are properly labeled and documented to facilitate maintenance, troubleshooting, and future modifications.
- Checking for proper sealing of terminal connections is essential to prevent moisture ingress and ensure long-term reliability.
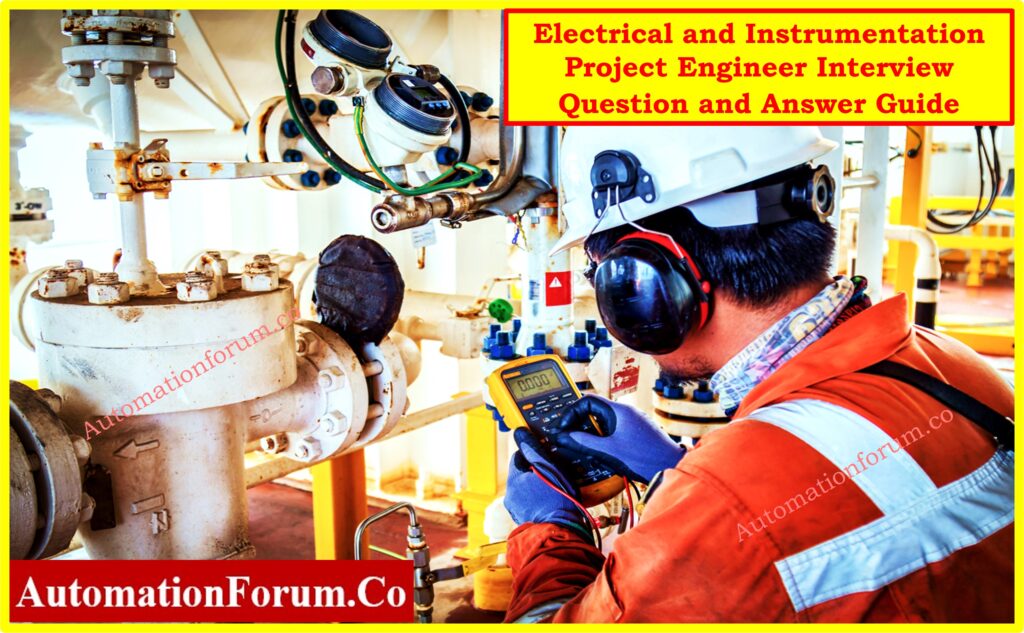
6. What is final RFI? When should it be raised?
- The final Request for Inspection (RFI) is raised when the QA/QC department of the contractor is satisfied that the work detailed in the construction RFI is completed to the required standards and specifications.
- RFIs should be submitted for inspection to the client QA/QC department only when the status of the preliminary inspection is satisfactory, and the works (items) are at Hold or Witness Points as per the project requirements.
- The submission of the final RFI marks a critical milestone in the project, indicating the completion of specific construction activities and readiness for client inspection and approval.
7. What is Schedule Q?
- Schedule Q is an attachment to the contract that outlines the provisions for Quality Assurance and Control, Inspection, and Test Plans (ITPs).
- It provides guidance on the methods and procedures to be followed for ensuring quality throughout the project execution, including the distribution of manpower and the execution of quality control and quality assurance activities.
- Schedule Q serves as a reference document for all parties involved in the project, helping to ensure consistency and adherence to quality standards and requirements.
8. What are the various levels of Inspection? Explain.
- Inspection levels range from Level 0 to Level 4, each with different requirements and intensities of inspection.
- Level 0 involves document requirements only, with no physical inspection conducted.
- Level 1 requires inspection prior to shipping of materials or equipment.
- Level 2 involves minimum requirements with pre-inspection meetings and one or more unspecified “in progress” surveillance visits.
- Level 3 is similar to Level 2 but includes regular “in progress” surveillance inspections.
- Level 4, known as Resident Inspection, involves continuous monitoring of the work by inspectors stationed at the site.
- The level of inspection may vary depending on factors such as project complexity, risk assessment, and client requirements.
9. What is ITP? What are Hold and Witness Points?
- An Inspection and Test Plan (ITP) outlines the scope of work and the types of inspections and tests required for a specific project.
- Hold Points are stages in the project where inspection by the client is mandatory before proceeding further. Work cannot proceed until inspection is completed and approval is obtained.
- Witness Points are stages where inspection can proceed without the immediate presence of the client, but the client may choose to witness the inspection if available.
- Hold and Witness Points are critical checkpoints in the project’s timeline, ensuring that quality is verified at key stages of construction and installation.
10. What is RFI? When should an RFI be raised?
- A Request for Inspection (RFI) is a formal request submitted by the contractor when certain construction activities are ready for client inspection.
- RFIs should be raised only when the status of the preliminary inspection is satisfactory, and the works (items) are at Hold or Witness Points as specified in the project requirements.
- RFIs serve as a communication tool between the contractor and the client, indicating readiness for inspection and ensuring compliance with project standards and specifications.
11. What is Cable tray and how is it identified separately for Electrical and Instrumentation?
- A cable tray is a structural system used to support and protect cables in various settings, such as buildings or pipe racks.
- Cable trays are identified separately for Electrical and Instrumentation purposes based on their specific usage and requirements. For example, Electrical cable trays may carry power cables, while Instrumentation cable trays may carry signal cables or instrument wiring.
- Proper identification and segregation of cable trays help in organizing and managing the cable infrastructure effectively, reducing the risk of interference and simplifying maintenance.
12. What is Calibration and what is process calibration?
- Calibration involves testing and adjusting equipment to ensure its accuracy and reliability.
- Process calibration specifically refers to the calibration activities carried out in relation to industrial processes, where instruments and equipment are calibrated to maintain process efficiency and product quality.
- Calibration is essential for ensuring the accuracy and reliability of measurement instruments, which is critical for maintaining quality and compliance in industrial operations.
13. What is the loop and how is the loop folder made?
- A loop refers to the electro-mechanical circuitry that includes components such as sensors, controllers, and actuators, used for monitoring and controlling a specific process or system.
- A loop folder is a collection of documents and records related to loop checks, including drawings, checklists, punch lists, and other relevant documentation, organized in a systematic manner for easy access and reference during loop testing and commissioning.
- The loop folder serves as a comprehensive resource for conducting loop checks and ensuring the successful operation and handover of a project.
14. What is the specialty rather characteristics of loop check? How do you come to know that loop check is completed?
- Loop check is a critical phase in commissioning where the functionality and performance of control loops are verified.
- Characteristics of loop check include serving as a blueprint for system functionality, verifying instrument serviceability, identifying system limitations, and providing documentation for project handover.
- Completion of a loop check is indicated by the successful verification of each loop’s functionality, documented punch list items addressed, and marking with a Red Colored Label bearing the date of completion and witnessing parties’ initials.
- Loop checks involve coordination between field and control room teams, requiring systematic testing and documentation to ensure the integrity and reliability of the control system.
15. What is the standard and what is Standardization?
- A standard is an authenticated documented instruction that provides guidelines or specifications for the execution of specific projects or activities.
- Standardization refers to the process of implementing and adhering to established standards in project execution, ensuring consistency, quality, and efficiency.
- Standards play a crucial role in ensuring uniformity and reliability in various industries, facilitating interoperability, and promoting best practices.
16. What is Inspection?
- Inspection is a process of verifying the application of methods or procedures according to documented and authenticated instructions, such as standards or specifications.
- It involves assessing the quality, compliance, and performance of materials, equipment, or processes through physical examination, testing, or observation.
- Inspection helps identify deviations, defects, or non-conformities early in the project lifecycle, enabling timely corrective actions to maintain quality and prevent costly rework.
17. What are the responsibilities of QC Inspector?
The following is a list of the extraordinary obligations that are expected to be carried out by any Quality Control Inspector during the course of any inspection.
- Well-versed in the technology that is being assessed in order to carry out the inspection.
- Should be able to analyze the procedure using whatever logic that is available to them.
- Should have a comprehensive understanding of the technique that will be used for inspection, also known as the standards that will be implemented.
- The individual should be able to communicate the irregularities that were discovered to the relevant authorities.
- Should be completely honest regarding the way the job is being carried out.
- Should maintain a state of constant vigilance.
18. What should be the attitude of a QC Inspector while carrying out an Inspection activity?
A perfect inspector possesses the following qualities, which are listed below:
- It is imperative that the quality of the inspection be maintained at all times and should never be compromised.
- Should have a genuine attitude toward carrying out the tasks.
- Be sure to arrive on time.
- Should demonstrate exemplary behavior in the manner in which they approach inspections.
- Should possess the capabilities to persuade the authorities about the anomalies via the use of educated advocacy.
19. What are the requirements for carrying out installation inspection of any instruments and receiving inspection of the said equipment?
- Requirements include having access to instrument data sheets, test instrument certificates, vendor instruction manuals, and test instrument instruction manuals.
- These documents provide essential information for conducting thorough inspections and ensuring compliance with specifications and standards.
- Proper documentation and preparation are essential for effective inspection activities, facilitating accurate assessment and verification of equipment and installations.
20. What is the CCTV System?
- The Closed-Circuit Television (CCTV) system is a digitally controlled surveillance system used for monitoring and recording activities in and around a plant or premises.
- It enables automatic alarm notification in case of unforeseen hazards or security breaches, providing real-time surveillance and enhancing safety and security.
- CCTV systems play a vital role in risk management, incident response, and maintaining a secure environment for personnel and assets.
21. What are the differences between QA & QC activities?
- Quality Assurance (QA) activities focus on ensuring that quality requirements are met throughout the project lifecycle by establishing processes, standards, and procedures.
- Quality Control (QC) activities involve verifying and monitoring the execution of these processes and procedures to ensure compliance with quality standards and specifications.
- QA is proactive and preventive, focusing on process improvement and risk mitigation, while QC is reactive and corrective, focusing on identifying and correcting defects or deviations.
22. What is Schedule ‘Q’ and how many appendices are there in schedule ‘Q’?
- Schedule ‘Q’ is an attachment to the contract that provides guidelines for Quality Assurance and Control, Inspection, and Test Plans (ITPs).
- It includes provisions for manpower distribution, quality process execution, and documentation requirements.
- Schedule ‘Q’ typically consists of six appendices covering various aspects of quality management and control.
- Appendices in Schedule ‘Q’ may address specific topics such as inspection procedures, testing protocols, quality documentation formats, and audit requirements.
23. What are the linked documentations carried out related to QC activity for oil & gas construction project?
Linked documentations for QC activities in oil & gas construction projects include:
- Application for inspection from the construction department after completing each activity.
- Production of drawings based on project planning and specifications.
- Method application priority-wise to ensure adherence to standards.
- Procurement records for items and equipment required for project execution.
- Comprehensive documentation is essential for traceability, accountability, and ensuring that quality standards and requirements are met throughout the project lifecycle.
24. What is process control system?
- A process control system is a system implemented to monitor and control industrial processes, ensuring they operate within specified parameters and meet desired performance criteria.
- It involves the use of sensors, controllers, actuators, and feedback mechanisms to regulate process variables such as temperature, pressure, flow, and level.
- Process control systems play a critical role in optimizing process efficiency, ensuring product quality, and enhancing safety in various industries such as oil & gas, chemical, and manufacturing.
25. What are QCP, QMP, and ITP?
- QCP (Quality Control Procedure) outlines the procedures and methods for ensuring quality standards are met during project execution.
- QMP (Quality Management Procedure) defines the overarching quality management framework and principles for the project.
- ITP (Inspection and Test Plan) details the scope of work, required inspections, and tests to be performed at various stages of the project.
- QCP, QMP, and ITP are essential documents that help ensure quality requirements are understood, implemented, and verified throughout the project lifecycle.
Click here for more Instrumentation Interview Question and Answers