- Different Types of SCADA System Architecture
- History of SCADA
- What is Supervisory Control and Data Acquisition (SCADA) System?
- Block Diagram of SCADA system
- Basics concepts of SCADA System
- List out Various types of SCADA systems
- What is the Architecture of SCADA?
- Difference Between PLC and SCADA
- Advantages of SCADA
- Disadvantages of SCADA
- Applications of SCADA
- What are the various types of SCADA systems?
- What are the levels of the SCADA system?
- What are the three main types of SCADA systems?
- What is a SCADA diagram?
- What are the main components of a SCADA system?
- What is SCADA mapping?
- How does a SCADA system work?
- What are the four levels of SCADA architecture?
- Why is SCADA used?
- What is an RTU in SCADA?
Different Types of SCADA System Architecture
- Advanced or recent technology in Intelligent Instrumentation, & Remote Terminal Units (RTUs), or Programmable Logic Controllers (PLCs) has made the operation & management of various industrial process control solutions easier, more reliable, & efficient through the benefits of SCADA systems.
- But in recent days this SCADA system has become more conspicuous in various process industries such as agriculture & irrigation, oil and gas, electric power generation, water and waste control, transportation systems, distribution and utilities, and so on.
- In 1960 the application of the SCADA system became popular to monitor and control plant equipment.
History of SCADA
An important technological leap occurred in the 1950s when computers were first employed for industrial control. Telemetry for data transmission and remote communication was then put into place. By the 1970s, microprocessors and Programmable Logic Controllers (PLCs) had been introduced, and SCADA systems had also been developed. These developments made it possible for industries to operate remotely and automate more tasks.
Distributed SCADA systems were first launched in 2000, enabling centralized control and monitoring of activities that are spread out geographically. Since then, contemporary SCADA systems have developed to provide real-time data monitoring and control from almost any location in the world.
What is Supervisory Control and Data Acquisition (SCADA) System?
- It is a computer-based industrial control system to inspect real-time data.
- It is a software application to monitor & control the whole industrial process through its graphical representation.
- SCADA collects various data in real-time from remote locations to control process & plant equipment.
- The large-scale industry consists of a huge number of processes, but monitoring and controlling each and every process is very complex since each piece of equipment issues or produces different outputs.
- It enables operators to optimize operations, detect abnormalities or faults, and make informed decisions to improve efficiency, productivity, and safety.
Block Diagram of SCADA system
The Block diagram shown below defines different blocks of the SCADA system
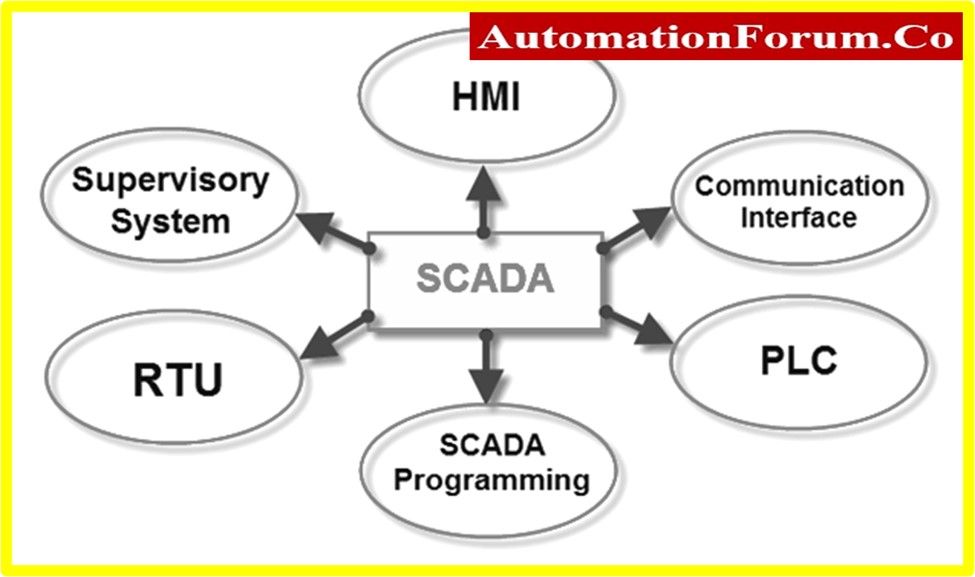
- Human Machine Interface (HMI)
- HMI is a manually controlled I/O device to present the process data by a human operator.
- It is used by hooking it to the SCADA system’s software programs and databases to issue the management information along with Scheduled Maintenance Procedures, Detailed Schematics, Logistic Information, and Trending Data for a specific sensor or machine.
- HMI systems assist the operator to visualize the process information graphically.
- The HMI allows operators to control the industrial processes by providing controls and commands for initiating or adjusting actions.
- The HMI displays alarms and alerts generated by the SCADA system. These alarms notify operators about abnormal conditions, equipment failures, or other critical events.
- The HMI allows administrators to manage user access and permissions. Different levels of access can be defined for operators, engineers, supervisors, or administrators, ensuring appropriate access to data and control functions within the SCADA system.
- The HMI often includes reporting capabilities that allow operators to generate customized reports based on real-time or historical data. These reports can include parameters such as production metrics, energy consumption, and equipment performance.
- Supervisory System
- The Supervisory system functions as a server unit to communicate sensors to SCADA equipment of the system such as RTU, & PLC.
- Here, HMI software is used only in control room workstations.
- In a smaller SCADA system, only a single computer unit is housed within a master or supervisory system.
- But, for larger SCADA systems, A supervisory system consists of a set of Distributed Software Applications, Catastrophe Recovery software, & Multiple Server units.
- These multiple servers are arranged in a dual-redundant mode, or hot-standby formation for continuous monitor, & control during server failure to maximize the system integrity.
- Triggers alarms and alerts based on predefined conditions.
- Prioritizes alarms based on severity for prompt operator response
- Configures and maintains the SCADA system for optimal performance.
- Defines communication protocols and device configurations.
- Supports system diagnostics and maintenance activities.
- Remote Terminal Unit.
- RTUs act as intermediaries between the field devices and the supervisory system.
- Remote Terminal Units are also known as Remote Telemetry Units; these are a type of device that interfaces Physical objects in the SCADA systems with a microprocessor or electronic device.
- These units convey telemetry information to the supervisory system and receive the information back from the master system to control the connected objects.
- RTUs often have embedded processors and logic capabilities to perform local processing tasks. They can execute simple control strategies and logic based on predefined rules or conditions, reducing the need for continuous communication with the supervisory system for every control action.
- RTUs typically have the ability to store acquired data locally. This feature allows them to continue collecting data even in the event of communication network failures.
- Programming Logic Controllers.
- The PLC unit in a SCADA system is cabled to various sensors to gather process data from these sensors and transforms these sensor output signals into readable digital data.
- Programming Logic Controller provides higher flexibility, configuration, versatility, and affordability in contrast with Remote Terminal Units
- Communication Infrastructure.
In a SCADA system, both radio and direct wired connections are consolidated.
But, SONET/SDH is used in power stations and railways.
The communication infrastructure establishes connectivity between the remote field locations and the central control system. It enables remote monitoring and control of industrial processes, even when the field sites are geographically dispersed.
The communication infrastructure is designed to provide a reliable network connection between the field devices and the supervisory system.
The communication infrastructure incorporates security measures to protect data integrity and confidentiality.
The communication infrastructure supports various communication protocols, such as Modbus, DNP3, OPC, or proprietary protocols, to facilitate interoperability between different devices and systems within the SCADA network.
- SCADA Programming.
SCADA programming is used to create maps and diagrams which is done by using C, or derived programming language.
SCADA programming involves developing control logic algorithms that define the behavior of the system. These algorithms determine how the SCADA system should respond to various conditions, events, and user inputs. They control the sequence of operations, decision-making processes, and automatic control actions.
SCADA programming allows for the configuration of trending and historical data analysis.
Basics concepts of SCADA System
Let us know some basic concepts of SCADA systems
- Various types of SCADA systems
- Architecture of SCADA System.
List out Various types of SCADA systems
SCADA systems are classified into four types
- Monolithic SCADA Architecture
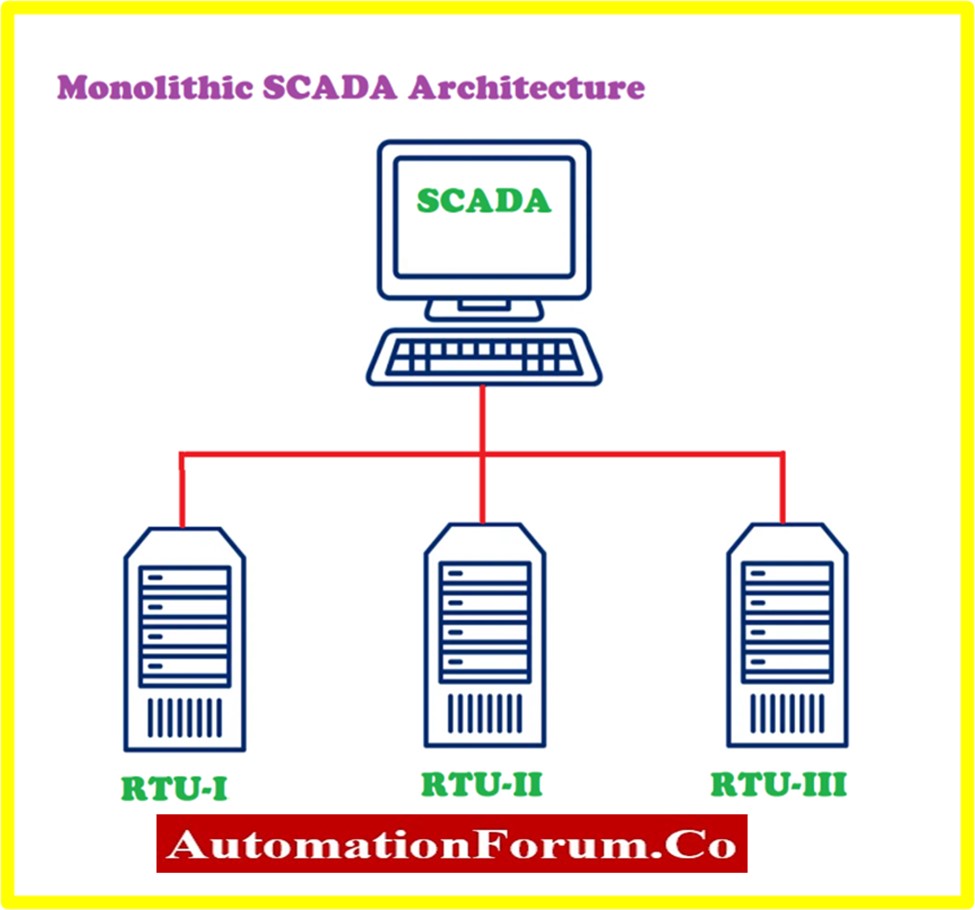
- It is the first & most basic type of architecture of a SCADA system
- This consists of a single SCADA system for communication with Remote Terminal Units.
- These SCADA systems are independent since they don’t have any physical connection with other SCADA systems because they are simple autonomous systems.
- To collect information from Remote Terminal Units these Monolithic systems use a backup mainframe.
- In emergency situations and during sensor monitoring the functions of these are limited to slumping of operations.
- Distributed SCADA Architecture
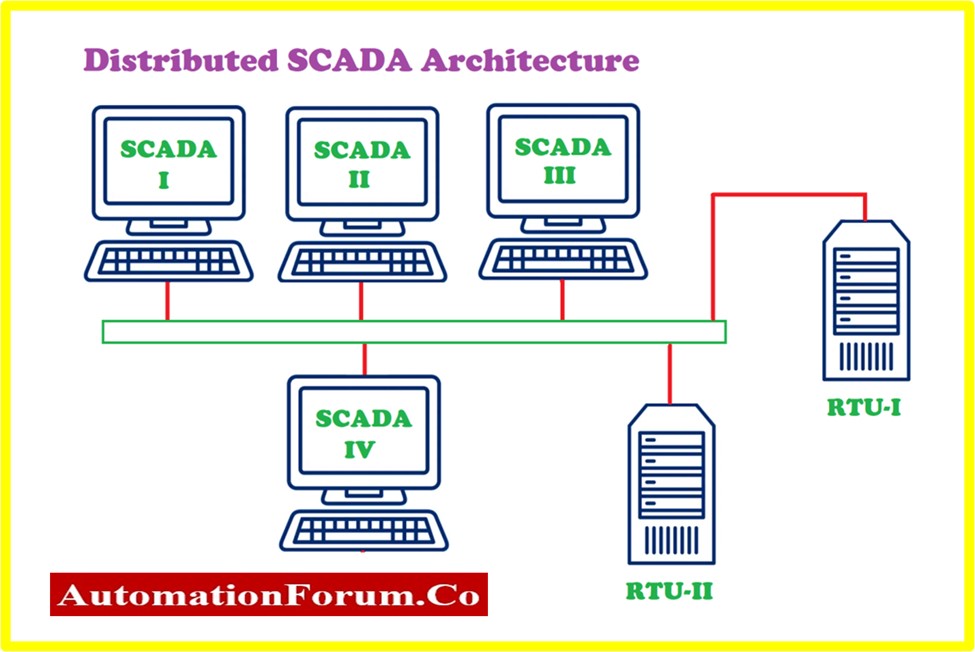
- Distributed SCADA systems architecture is categorized into the Second Generation of SCADA systems architecture.
- Distributed SCADA is an improved version of monolithic architecture.
- This architecture offers a redundancy system.
- This system consists of multiple SCADA systems but has the ability to connect to various SCADA systems.
- This system enables a Data sharing facility, where Data between systems is shared either by client systems or server systems.
- Networked SCADA Architecture
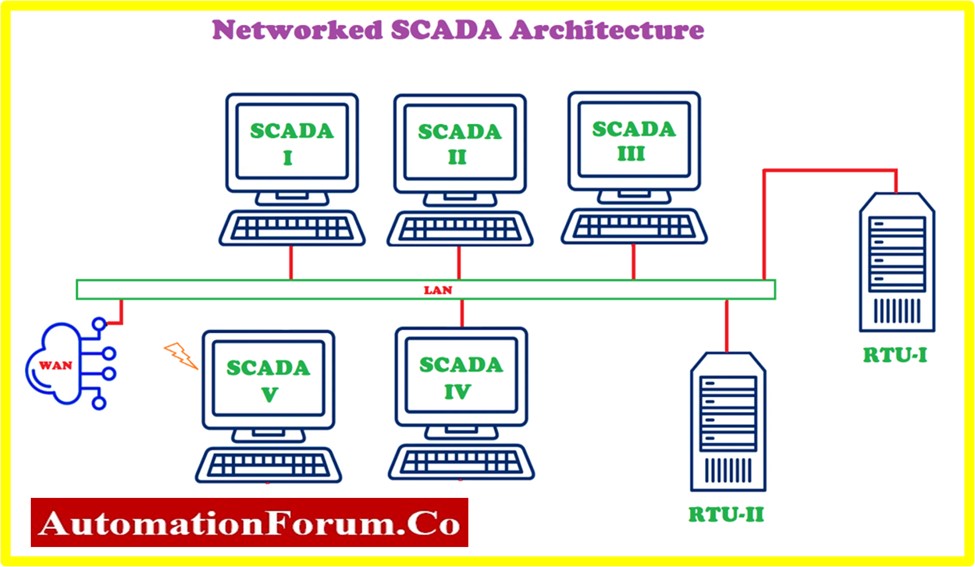
- Networked SCADA systems architecture is categorized into the Third Generation of SCADA systems architecture.
- This Networked SCADA architecture is currently used today in most large industrial sectors.
- Here, Optical Fiber, & Ethernet is used to transmit data between nodes.
- The networked architecture enables accessing and supervising data from other locations other than plant areas.
- Internet of Things technology, SCADA systems
- This IoT SCADA architecture is categorized into the Fourth Generation of SCADA systems architecture
- This architecture comes with cloud computing technology.
- Compared to previous architecture, this IoT comes with reduced infrastructural costs.
- Here Integration and maintenance is very easy.
What is the Architecture of SCADA?
Architecture of SCADA System
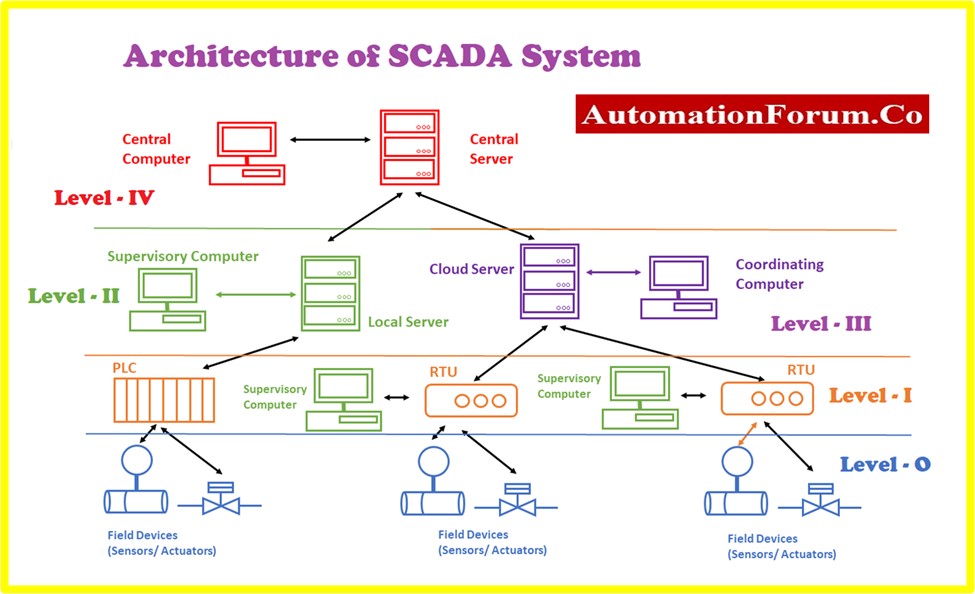
- Generally, the SCADA system is an integrated system for monitoring and controlling the entire process plant.
- SCADA is a pure software application provided on top of the hardware unit. A supervisory system gathers data on the process and sends the command control to the process. The SCADA is a kind of Remote Terminal Unit RTU.
- The SCADA system makes use of Local & Wide Area Networks, both these networks comprise internet protocols to enable data communication between the master station and ground or field devices.
- The sensor is the physical equipment connected to the PLC or RTU. The RTUs convert the sensor signals to digital data and send digital data to the master.
- Level 0 (Sensors & Actuators)
- Level 0 is considered as a ground or field level.
- At this level, these field devices such as Sensors or Actuators usually interact with the physical environment. These devices function as technicians in a supervision system.
- This level consists of various types or classes of sensors and actuators.
- Basically, A sensor is a sensing device to sense the physical changes in process parameters and generates equivalent electronic signals.
- For example, we use RTD, or Thermocouple to measure the temperature of a process. Likewise, the SCADA system uses various sensors like Flow sensors, pressure sensors, LDR, and many more.
- But an actuator is an output device that makes some physical change in a system when an electrical or electronic signal is applied to it.
- For example, we make use of a solenoid valve to regulate fluid flow using an electrical method.
- Level I (Programming Devices)
- Various programming devices such as Programmable Logic Controller, and Remote Terminal Units are the members of this category.
- The main objective of these devices is to monitor and control ground or field-level devices such as sensors and actuators.
- A SCADA system is made up of Local Area Networks (LAN), Wide Area Networks (WAN), or a combination of both networks.
- To build the SCADA system
- Local Area Network is used only for PLC
- Wide Area Networks are used only for RTU
- Level II (Local Control and Human Machine Interface)
- Level II consists of supervisory computers, here various programming devices such as Programmable Logic Controller, and Remote Terminal Unit that controls the ground or field level devices are linked to these supervisory computer systems.
- Supervisory computers are a type of computer system that enables SCADA software for functioning; these may be linked to a specific machine or some machines that are similar to each other within that manufacturing unit.
- These Supervisory computers furnish actual instructions and commands for plant operation.
- These Supervisory computers can be easily operated by respective plant operators, supervisors, & technicians to observe and control production errors.
- Level III (Coordination)
- Coordination is the second top level of the SCADA System.
- In this level-III Coordination is used to coordinate the computers that come under this level.
- Generally, these computers are linked to various control systems of the plant.
- Coordination aims to collect process data from various sections of plants in one place.
- At this level, various activities such as planning, scheduling, and managing event time are done by the plant in charge or section manager.
- Level IV (Central Control)
- Central Control is the topmost level of the SCADA System.
- Here, a central computer is linked to various equipment or machines .
- Generally, this level is governed by the management team of the plant.
- The management team has a right to make decisions by using the data and information that are collected and stored.
- Through this Central Control level, the management team can visualize each and every action and operation of the plant.
Difference Between PLC and SCADA
Essential parts of industrial automation, PLC (programmable logic controller) and SCADA (supervisor control and data acquisition) have various uses even if they are While SCADA is a software-based system for supervisor level process monitoring and control, PLCs are mostly utilized for hardware-level control of machines. The following table shows their variations:
Aspect | PLC | SCADA |
Full Form | Programmable Logic Controller | Supervisory Control and Data Acquisition |
Nature | Hardware-based | Software-based |
Primary Function | Controls processes in industries like motors, machines, etc. | Supervises, monitors, and controls plant operations |
Components | Processor, I/O Modules, Programming Device, and Power Supply | MTU (Master Terminal Unit), RTU (Remote Terminal Unit), HMI (Human Machine Interface) |
Types | Fixed (Compact) and Modular | Monolithic, Distributed, Networked, and IoT |
Input/Output Representation | Represented as NO (Normally Open), NC (Normally Closed), and coil contacts | Represented as images |
Component Identification | Components are identified by addresses | Components are identified by names |
Control Scope | Operates at a machine or equipment level | Supervises at the plant or process-wide level |
Complexity | Handles real-time, low-level process control | Manages high-level process visualization and data analysis |
Data Logging | Limited or none | Extensive, includes trends and historical data |
Communication | Communicates with field devices directly | Interfaces with multiple PLCs and other systems |
Cost | Relatively lower | Higher due to software and integration capabilities |
Advantages of SCADA
The SCADA system offers numerous advantages, including:
- Enhances operational efficiency and output quality.
- Reduces system failures and enhances uptime.
- Minimizes the need for frequent maintenance.
- Simplifies complex processes, requiring less manual intervention.
- Enables the monitoring of large-scale system parameters.
- Automates processes, decreasing the need for human labor.
- Facilitates quicker identification and resolution of faults.
- Provides accurate fault identification and location.
- Records vast amounts of operational data for analysis.
- Presents data in various formats as per user needs.
- Supports thousands of sensors for effective monitoring and control.
- Offers operators real-time data simulations for better decision-making.
- Ensures quick reactions to changing conditions.
- Easily adapts to additional resources or expanded systems.
- Provides detailed on-screen displays of operational status.
- Allows integration of new control units and sensors as required.
- Operates effectively under critical conditions.
Disadvantages of SCADA
Despite its benefits, SCADA systems have some limitations:
- The system relies on interdependent modules and hardware units.
- Needs skilled operators, analysts, and programmers for maintenance.
- Involves significant initial investment.
- Reduces the need for manual labor, potentially increasing unemployment rates.
- Limited to specific hardware devices and compatible software.
Applications of SCADA
SCADA systems are widely used in various industries and applications, including:
Turbines and Generators: Monitoring and controlling equipment performance.
Power Generation and Distribution: Monitoring and controlling power plants, transmission, and distribution systems.
Public Transport: Managing train systems, traffic lights, and other transportation infrastructure.
Water and Sewage Systems: Controlling water treatment, distribution, and reservoir management.
Manufacturing: Supervising and automating factory processes.
Industrial and Building Systems: Managing heating, cooling, and other building operations.
Communication Networks: Overseeing data and signal transmission systems.
Oil and Gas Industries: Monitoring pipelines, refineries, and storage facilities.
Traffic Control Systems: Managing urban and intercity traffic signals.
What are the various types of SCADA systems?
SCADA systems are classified into four types
- Monolithic or Early SCADA systems (Gen I),
- Distributed SCADA systems (Gen II),
- Networked SCADA systems( Gen III)
- Internet of Things technology SCADA systems (Gen IV)
What are the levels of the SCADA system?
SCADA system consists of four levels
- Field Instrumentation Level.
- Programmable Logic Controllers (PLC) level
- Remote Telemetry Units (RTU) level
- SCADA Host Platform.
What are the three main types of SCADA systems?
Usually, SCADA systems are categorized into three kinds depending on their architecture:
- Monolithic SCADA System: Operating from a single, centralized mainframe or computer, the earliest version
- Distributed SCADA Systems: These use several network-spread controllers, each in charge of particular tasks, therefore allowing improved scalability and redundancy.
- Networked SCADA Systems: The most current type of networked SCADA systems uses sophisticated networks and internet protocols for remote monitoring, real-time control, and data exchange across several sites.
What is a SCADA diagram?
Graphically representing the SCADA system architecture, a SCADA diagram Usually, it shows the interaction between software components (like HMIs and central servers) and hardware (like sensors, RTUs, and PLCs) used for real-time monitoring and control of industrial processes..
What are the main components of a SCADA system?
A SCADA system is made up of hardware and software components working in concert to collect, process, and show data. The primary components are:
- Field Devices: Process control and data acquisition sensors, relays, and actuators.
- Control Units: Control units include PLCs (Programmable Logic Controllers) and RTUs (Remote Terminal Units) that process and forward data.
- Human-Machine Interface (HMI): Shows information and lets users interact with the Human-Machine Interface (HMI).
- Communication Infrastructure: Enables data movement from field devices to central systems via communication infrastructure.
- SCADA Software: manages graphical visualisation, data logging, trending, and alarm management.
What is SCADA mapping?
SCADA mapping is a configuration and depiction of field equipment, processes, and paths of communication inside a SCADA system. By connecting physical assets with their virtual representations in the HMI, it allows precise real-time monitoring and control.
How does a SCADA system work?
Using RTUs or PLCs, SCADA systems run by gathering data from field devices via sensors and actuators. A central server processes this data and shows it on HMIs. Operators may send control commands back to the field, track system status, and examine the data.
What are the four levels of SCADA architecture?
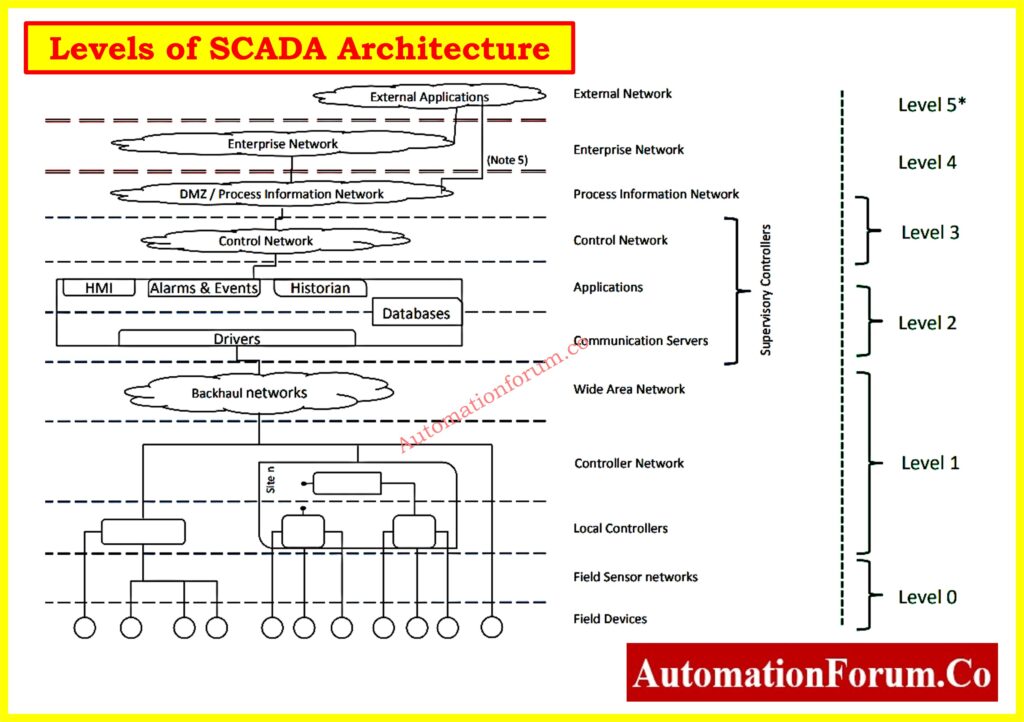
Modern SCADA systems are structured into hierarchical levels:
- Level 0: Field Instruments like sensors and actuators that interact directly with the physical process.
- Level 1: Local Control like RTUs or PLCs that collect data and execute control logic.
- Level 2: Supervisory Control like SCADA software and HMIs for centralized monitoring and control.
- Level 3: Manufacturing Execution Systems (MES) Software that bridges the gap between production and business systems.
- Level 4: ERP (Enterprise Resource Planning) systems used for business and financial decision-making.
Why is SCADA used?
Industries needing real-time process monitoring and control depend on SCADA systems. Their main advantages are:
- Automation and remote supervision
- Improved operational efficiency
- Data collecting and processing in real time
- Early warning creation and fault identification
- Lowered maintenance expenses and downtime
SCADA systems are often used in industries including energy, water treatment, oil and gas, manufacturing, and transportation.
What is an RTU in SCADA?
A field device in a SCADA system, an RTU (Remote Terminal Unit) gathers data from sensors and equipment at remote places. It sends this information to the central SCADA system and also gets control signals to run devices like valves, motors, or switches. In remote or distributed settings, RTUs are essential for facilitating communication between field instruments and central controllers.