Table of Contents
- Intrinsic Safety Vs. Explosion Proof
- What is Intrinsically Safe?
- Definition and Certification of Intrinsically Safe (IS) Equipment:
- Purpose of IS Protection and Intrinsic Barriers:
- Limiting Energy in Circuits for Explosion Prevention:
- What is Explosion-Proof?
- How to Choose Between Intrinsically Safe vs Explosion-Proof
- Key Differences Between Intrinsically Safe (IS) and Explosion-Proof (Ex)
- Quality System and Certification Standards
- Summary
Intrinsic Safety Vs. Explosion Proof
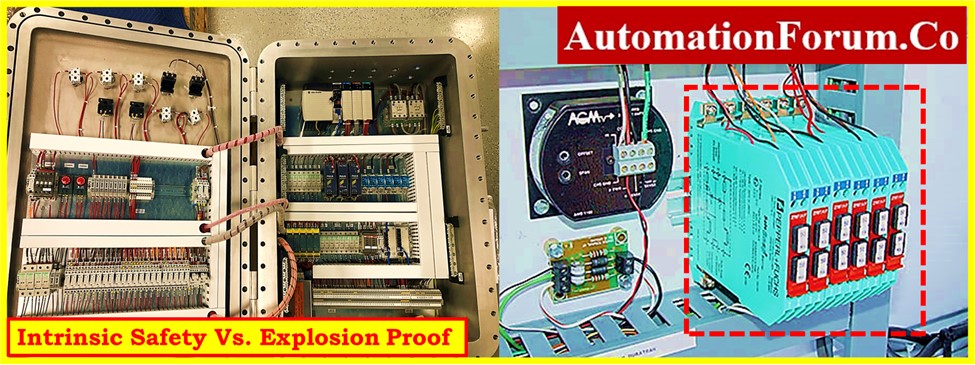
Importance of Safety in Hazardous Environments
- Safety comes priority in hazardous industrial environments where even a slight spark can have catastrophic consequences. Strong safety regulations are necessary to safeguard people and property since explosive gasses have the potential to cause disasters.
- As a first line of defense, safety procedures reduce hazards and protect employees. Modern technology, such as solutions that are Explosion-Proof (Ex) and Intrinsically Safe (IS), are essential in preventing ignition sources.
- Safety precautions ensure continuous operations above and beyond legal requirements, highlighting the teamwork needed for a safer future in hazardous circumstances.
Understanding Explosion-Proof and Intrinsically Safe Technologies
- Understanding Intrinsically Safe (IS) and Explosion-Proof (Ex) technology is critical in hazardous environments.
- A detailed comprehension of these safety precautions is necessary due to the possibility of disasters being started by a single spark.
- Equipment that has been certified as intrinsically safe by regulations such as ATEX and IECEx restricts the flow of energy through intrinsic barriers, consequently preventing sparks in explosive environments.
- In contrast, devices that are explosion-proof are covered in strong materials like stainless steel and work by containing and dissipating energy to prevent explosions.
- The difference is that Ex focuses on robust architecture to contain and withstand possible explosions, whereas IS focuses on minimizing energy to prevent ignition.
What is Intrinsically Safe?
Definition and Certification of Intrinsically Safe (IS) Equipment:
- Equipment certified as intrinsically safe (IS) by organizations like IECEx and ATEX ensures compliance to strict safety regulations.
- These certificates indicate compliance with strict regulations governing machinery intended for use in explosive or hazardous environments.
- Intrinsic barriers are used by IS devices, which are certified components that prevent the generation of sparks and prevent the equipment from igniting explosive environments.
- This certification provides a critical layer of protection against ignition sources and guarantees users that IS equipment can function securely in hazardous circumstances.
Purpose of IS Protection and Intrinsic Barriers:
- Using intrinsic barriers, intrinsic safe protection is designed to limit the amount of energy that can be transferred within circuits.
- Strict standards were followed in the design of these barriers, which ensure that IS equipment won’t be able to ignite potentially dangerous environments with sparks.
- IS protection focuses on minimizing the release of thermal and electrical energy, which prevents explosions from occurring in the first place.
- Intrinsic barriers, which can be classified as Zener barriers and Galvanic isolators, are extremely important in hazardous environments since they are responsible for directing extra electrical energy and providing isolation between the corresponding circuits.
Limiting Energy in Circuits for Explosion Prevention:
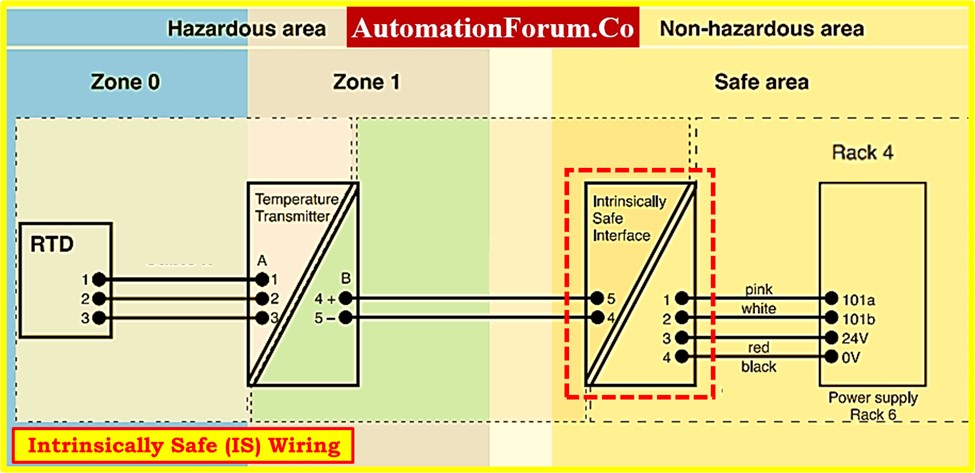
- The fundamental concept behind intrinsically safe (IS) protection is to maintain circuit energy levels below whatever is needed to ignite specific dangerous air mixtures.
- This restriction applies in both typical circumstances and in the event of a system failure. Intrinsic safety (IS) protection is achieved by use of intrinsic barriers, of which there are two primary types: galvanic isolators and Zener barriers.
- This keeps the electrical and thermal energy below the ignition threshold. In potentially explosive situations, the risk of sparking and ignition is significantly decreased by this careful regulation of energy levels.
What is Explosion-Proof?
Definition and Certification of Explosion-Proof (Ex) Equipment:
- Equipment marked as Explosion-Proof (Ex) is approved for operation in dangerous environments and complies with strict guidelines, like those set established by the National Electrical Code.
- Certification signifies the apparatus’s capability to withstand a gas or vapor explosion, containing it within the enclosure.
- This certification ensures that the structure of the equipment is made to avoid the discharge of energy outside the enclosure in the case of an explosion.
- In order to make sure a strong and established level of protection against potential explosions in potentially explosive environments, the National Electrical Code specifies precise requirements for obtaining Explosion-Proof certification.
Materials Used in Explosion-Proof Equipment:
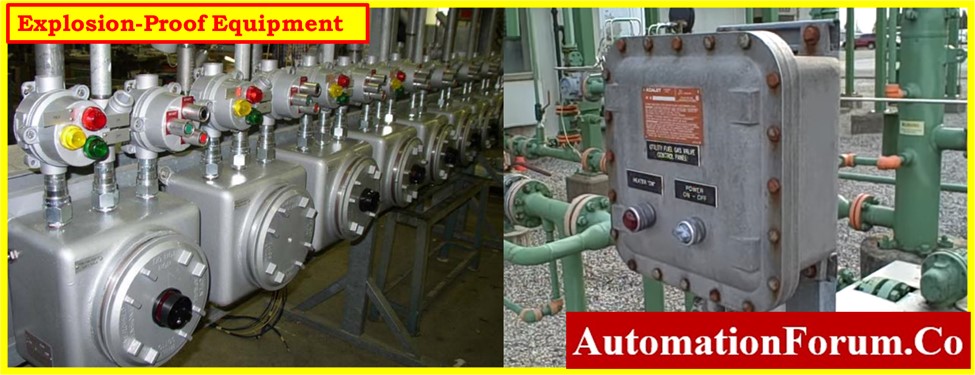
- Explosion-Proof (Ex) equipment is built strong using materials like cast aluminum or stainless steel. These materials have been selected because they are durable and powerful, which are necessary for preventing explosives and surviving possible blasts.
- To ensure that the apparatus can sustain the forces produced during an explosion without losing its integrity, a robust structure is essential.
- Explosion-Proof equipment uses materials that are highly resistant to explosive forces to create a dependable barrier that prevents explosions from spreading in dangerous areas.
Containment and Dissipation of Energy in Case of Explosion:
- Explosion-Proof (Ex) equipment performs extremely well at both containing and dissipating released energy in the event of an explosion.
- The enclosure’s design is very important, and it has been carefully constructed to withstand the forces produced by an explosion.
- Energy may be dissipated and kept from escalating because to the enclosure’s extensive surface area of flanges or threads.
- By reducing the possibility of further explosions and improving overall safety in hazardous conditions, this dual system of containment and dissipation ensures that even in the extremely unlikely case of an explosion, the equipment remains undamaged.
How to Choose Between Intrinsically Safe vs Explosion-Proof
Cost Comparison: IS vs. Explosion-Proof
- Generally speaking, Intrinsically Safe (IS) systems are less expensive than their Explosion-Proof counterpart. Because intrinsic barriers are the foundation of IS technology, heavy explosion-proof enclosures are not necessary. Because it is affordable for both installation and maintenance, IS is an excellent choice for industries with limited financial resources and provides strong safety in hazardous environments.
Power Limitations and Applications:
- Although inexpensive, intrinsically safe (IS) systems have power limitations. They work well in low-power circumstances in which power control and limitation are required for the entire system.
- Explosion-Proof systems, on the other hand, are a better option in situations when a significant amount of energy must be provided for operations since they are capable of handling high-power applications.
Maintenance Considerations:
- Maintenance Considerations: Intrinsically Safe (IS) systems allow for flexible maintenance on live equipment under specific circumstances.
- However, maintenance on Explosion-Proof systems necessitates turning off the electricity, which presents logistical challenges.
- The operational flexibility provided by IS technology should be compared to the increased maintenance requirements of Explosion-Proof equipment.
Wiring Differences and Legal Compliance:
- The simpler intrinsically safe (IS) wiring just needs an IS barrier and does not require conduits or seals.
- Explosion-proof wiring, on the other hand, necessitates extra precautions like conduit and seals to keep hazardous gasses from entering circuits.
- The protection strategy used depends on legal compliance because hazardous locations are zoned.
- While Explosion-Proof protection is restricted to Zones 1 and 2, not Zone 0, IS equipment is appropriate for Zones 0, 1, and 2.
- Compliance to industry standards and safe operations are ensured by compliance with these requirements.
Key Differences Between Intrinsically Safe (IS) and Explosion-Proof (Ex)
Below is a table summarizing the key differences between Intrinsically Safe (IS) and Explosion-Proof (Ex) technologies:
Criteria | Intrinsically Safe (IS) | Explosion-Proof (Ex) |
Definition and Certification | Certified by directives like ATEX, IECEx | Certified for use in hazardous areas |
Protection Approach | Limits energy to prevent ignition | Robust construction to contain and survive explosions |
Certification Standards | ATEX, IECEx, CAN/CSA, FM, UL, etc. | National Electrical Code, UL, regional authorities |
Materials Used | Lightweight materials; intrinsic barriers | Stainless steel, cast aluminum for robustness |
Power Limitations | Suitable for low-power applications | Suitable for high-power applications |
Maintenance | Permits maintenance on live equipment under conditions | Requires shutdown for maintenance |
Wiring Requirements | Simpler wiring with IS barriers; no conduit and seals | Requires conduit and seals for wiring |
Zones of Use (Hazardous Areas) | Suitable for Zone 0, Zone 1, and Zone 2 | Suitable for Zone 1 and Zone 2, not Zone 0 |
Weight and Flexibility | Lighter weight, offering more flexibility in usage | Heavier, may have more constraints in usage |
Cost Comparison | Generally cost-effective | Often involves higher costs for construction |
The most important distinctions between intrinsically safe and explosion-proof technology can be easily understood in this table.
Quality System and Certification Standards
Importance of Quality System in Hazardous Environments:
- A high quality system is essential for manufacturing products that comply to strict safety regulations in hazardous environments.
- After the initial certification achieved, continuous compliance with an established Quality System is crucial.
- Frequent audits of the factory ensure consistent compliance, proving that the items are created frequently with exacting attention to safety and regulatory regulations, in addition to meeting approval standards.
Regulatory Standards for IS and Explosion-Proof Equipment:
- In order to be certified, products made for dangerous situations have to adhere to strict regulations. Intrinsically Safe (IS) equipment complies with internationally recognized rules by adhering to standards including ATEX, IECEx, CAN/CSA, and FM.
- Similar to this, equipment marked as Explosion-Proof complies to guidelines provided by agencies such as the National Electrical Code, UL, and other local government agencies.
- The criteria for safe design, construction, and operation in hazardous areas are established by these standards.
Certification and Product Labeling:
- Products go through certification after meeting strict requirements, which enables them to be labeled with important information.
- Once an intrinsic product has complied with standards like as UL, FM, and CAN/CSA, it is labeled as suitable for use in hazardous environments.
- Products that meet standards such as UL are labeled as “explosion-proof” to indicate that they are capable of withstanding explosive environments.
- A product’s certification and labeling act as visible indicators of its conformity with safety regulations and acceptability for use in potentially hazardous environments.
Summary
Summarizing the Key Differences and Considerations:
- The key difference between Explosion-Proof (Ex) and Intrinsically Safe (IS) technologies is that both of them depend on strong construction, while the second type of technology limit energy to prevent ignition.
- Cost, power limitations, and maintenance are different, but IS is adaptable and inexpensive. The decision is influenced by zoning regulations, design choices, and legal compliance.
Making Informed Choices for Hazardous Environment Safety:
- Adherence to safety regulations, design limitations, and power requirements must all be carefully considered when making assessments regarding the safety of a hazardous environment.
- The subjective selection between Explosion-Proof and IS technologies requires considering weight, adaptability, cost, and regulatory compliance into account. Customizing decisions ensures the best safety precautions for certain operational requirements.