Table of Contents
- ASME (American Society of Mechanical Engineers)
- ANSI/FCI (American National Standard Institute/Fluid Control Institute)
- IEC (International Electro-Technical Commission)
- ISA (International Society of Automation)
- American Petroleum Institute (API)
- Key Selection Requirements for Control Valves in Industrial Applications
- In the selection of control valves for industrial applications, adherence to specific codes and standards is important to ensure optimal performance, reliability, and safety.
- These standards provide guidelines and criteria for various aspects of control valve selection, including sizing, capacity testing, noise prediction, and safety considerations.
- Adherence to specific codes and standards is fundamental in this selection process to ensure that the chosen control valves meet industry requirements and comply with safety regulations. Let’s explore each standard and its significance in the process:
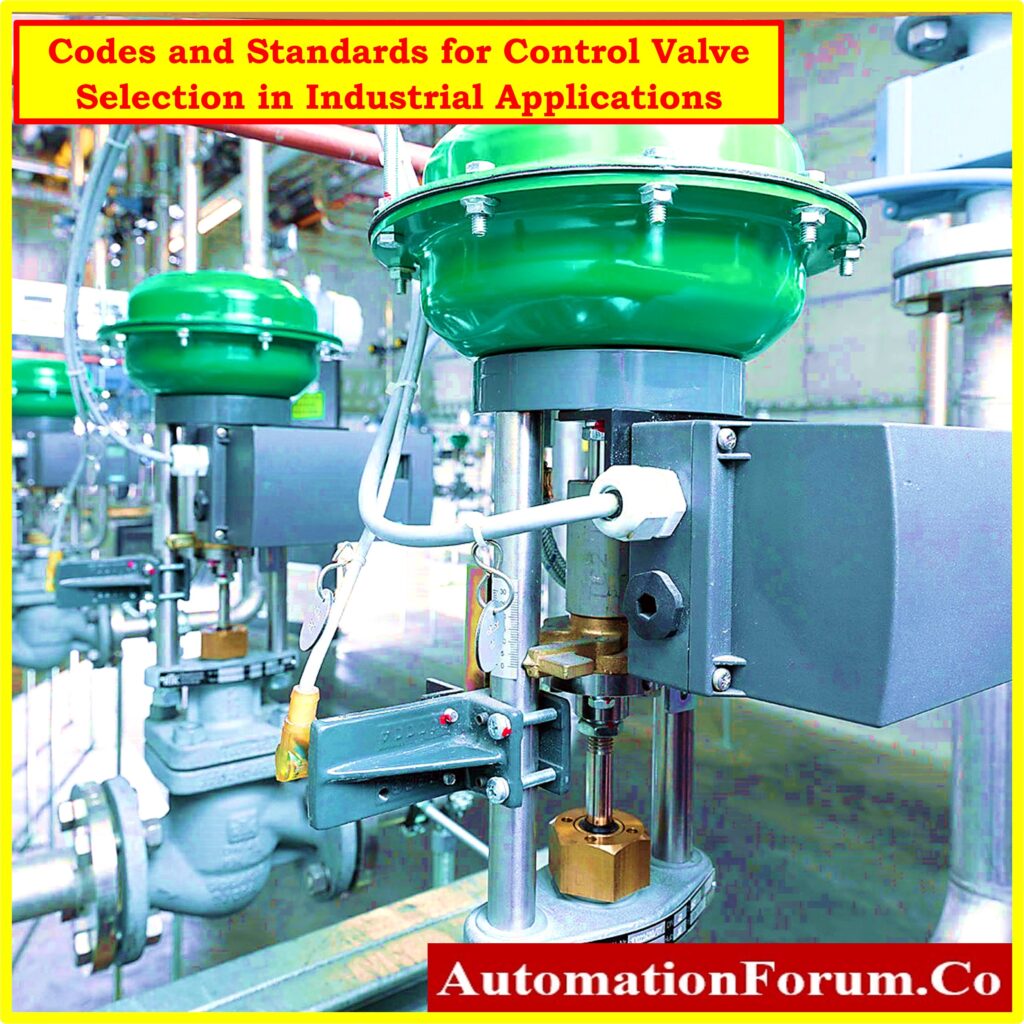
What standards are used in control valves?
ASME (American Society of Mechanical Engineers)
The American Society of Mechanical Engineers (ASME) and the International Electrotechnical Commission (IEC) have developed several standards crucial for the selection and operation of control valves. Let’s go into further detail about each of these characteristics:
What is the ASME standard for control valves?
IS/IEC 60079 Electrical Apparatus for Explosive Gas Atmosphere
- This standard outlines requirements for electrical apparatus used in potentially explosive gas atmospheres. It ensures that control valves operating in such environments are designed and installed to mitigate the risk of ignition.
IS/IEC 60529 Degree of Protection Provided by Enclosures
- Specifies the degree of protection provided by enclosures against ingress of solid foreign objects and liquids. It ensures that control valve enclosures maintain their integrity and functionality in various environmental conditions.
IEC 60534-3-2 Face to Face Dimension of Rotary Valves (except for butterfly valves)
- Defines the face-to-face dimensions of rotary valves, excluding butterfly valves. It ensures consistency and compatibility in piping systems involving rotary valves.
IEC 60534-4 Seat Leakage
- Addresses seat leakage in control valves, specifying acceptable limits and testing procedures to ensure proper sealing and prevent fluid leakage.
IEC 60534-8.3 and IEC 60534-8.4 Industrial Process Control Valves, Noise Consideration
- These standards focus on noise considerations in industrial process control valves. They provide methods for predicting and mitigating aerodynamic and hydrodynamic noise generated by valves.
IEC-61158 and IEC-61158-2 Fieldbus Standard for Industrial Control Systems
- These standards define communication protocols and physical layer specifications for fieldbus systems used in industrial control applications. They ensure interoperability and reliability in control valve communication networks.
FF 890-894 Function Block Application Process Parts 1-5
- These parts of the Fieldbus standard specify function block application processes, providing guidelines for the implementation of control functions in industrial processes.
IEC 61508 Functional Safety of Electrical/Electronic/ Programmable Electronic Safety-related Systems
- Addresses the functional safety of safety-related systems, including those involving control valves. It ensures that such systems are designed, implemented, and maintained to achieve the necessary level of safety.
IEC-61511 Functional Safety Instrumented System for the Process Industry Sector
- Provides requirements and guidance for the implementation of safety instrumented systems (SIS) in the process industry sector, including the use of control valves in safety-critical applications.
IEC-61804 Function Blocks (FB) for Process Control: Electronic Device Description
- This standard defines function blocks for process control and specifies their electronic device descriptions, facilitating interoperability and integration of control devices, including valves.
ANSI/FCI (American National Standard Institute/Fluid Control Institute)
FCI 70-2 Control Valve Seat Leakage
- Addresses control valve seat leakage, specifying testing procedures and acceptable leakage rates to ensure tight shutoff and prevent fluid loss.
IEC (International Electro-Technical Commission)
75.01.01 Flow Equation for Sizing Control Valves:
- This standard defines equations and methodologies for determining the appropriate size of control valves based on flow requirements in a given application.
75.02 Control Valve Capacity Test Procedure:
- Specifies procedures for testing the capacity and performance of control valves under various operating conditions to ensure they meet specified requirements.
75.04 Control Valve Positioner Stability:
- Addresses the stability of control valve positioners, ensuring they maintain accurate control and response characteristics over time and under varying conditions.
75.05.01 Control Valve Terminology:
- Establishes standardized terminology and definitions related to control valves, facilitating clear communication and understanding across the industry.
75.07 Laboratory Measurement of Aerodynamic Noise Generated by Control Valves:
- Specifies methods and procedures for measuring aerodynamic noise generated by control valves in laboratory settings to assess their noise characteristics.
75.08.01 – 75.08.06 Face-to-Face Dimensions for Different Control Valve Body Types:
- Provides standardized dimensions for various types of control valve bodies, including integral flanged, flangeless, and butt-weld end globe-style valves, ensuring interchangeability and compatibility.
75.11.01 Inherent Flow Characteristic and Rangeability of Control Valves:
- Defines inherent flow characteristics and rangeability requirements for control valves, crucial factors in determining their suitability for specific applications.
75.19.01 Hydrostatic Testing of Control Valves:
- Specifies procedures for conducting hydrostatic testing on control valves to verify their integrity and pressure rating compliance.
75.22 Face-to-Center-Line Dimensions for Globe-Style Angle Control Valve Bodies:
- Establishes standardized dimensions for the face-to-center-line of flanged globe-style angle control valve bodies, ensuring proper installation and alignment.
75.25.01 and TR 75.25.02 Test Procedure for Control Valve Response Measurement for Step Inputs:
- Outlines procedures for measuring and evaluating the response of control valves to step inputs, assessing their dynamic performance.
75.13 Method of Evaluating the Performance of Positioners with Analog Input Signals and Pneumatic Output:
- Defines methods for assessing the performance of control valve positioners when subjected to analog input signals and pneumatic output.
75.17 Control Valve Aerodynamic Noise Prediction:
- Provides guidelines for predicting and mitigating aerodynamic noise generated by control valves to ensure compliance with noise requirements.
RP75.23 Considerations for Evaluating Control Valve Cavitation:
- Offers considerations and recommendations for evaluating and mitigating cavitation phenomena in control valves to prevent damage and performance degradation.
ISA (International Society of Automation)
The International Society of Automation (ISA) has established various standards essential for the proper selection, testing, and operation of control valves in industrial applications. Here’s an overview of each standard:
75.01.01 Flow Equation for Sizing Control Valves
- Defines equations and methodologies for determining the appropriate size of control valves based on flow requirements in a given application.
75.02 Control Valve Capacity Test Procedure:
- Specifies procedures for testing the capacity and performance of control valves under various operating conditions to ensure they meet specified requirements.
75.04 Control Valve Positioner Stability:
- Addresses the stability of control valve positioners, ensuring they maintain accurate control and response characteristics over time and under varying conditions.
75.05.01 Control Valve Terminology:
- Establishes standardized terminology and definitions related to control valves, facilitating clear communication and understanding across the industry.
75.07 Laboratory Measurement of Aerodynamic Noise Generated by Control Valves:
- Specifies methods and procedures for measuring aerodynamic noise generated by control valves in laboratory settings to assess their noise characteristics.
75.08.01 – 75.08.06 Face-to-Face Dimensions for Different Control Valve Body Types:
- Provides standardized dimensions for various types of control valve bodies, ensuring interchangeability and compatibility.
75.11.01 Inherent Flow Characteristic and Rangeability of Control Valves:
- Defines inherent flow characteristics and rangeability requirements for control valves, crucial factors in determining their suitability for specific applications.
75.19.01 Hydrostatic Testing of Control Valves:
- Specifies procedures for conducting hydrostatic testing on control valves to verify their integrity and pressure rating compliance.
75.22 Face-to-Center-Line Dimensions for Flanged Globe-style Angle Control Valve Bodies:
- Establishes standardized dimensions for the face-to-center-line of flanged globe-style angle control valve bodies, ensuring proper installation and alignment.
75.25.01 and TR 75.25.02 Test Procedure for Control Valve Response Measurement for Step Inputs:
- Outlines procedures for measuring and evaluating the response of control valves to step inputs, assessing their dynamic performance.
75.13 Method of Evaluating the Performance of Positioners with Analog Input Signals and Pneumatic Output:
- Defines methods for assessing the performance of control valve positioners when subjected to analog input signals and pneumatic output.
75.17 Control Valve Aerodynamic Noise Prediction:
- Provides guidelines for predicting and mitigating aerodynamic noise generated by control valves to ensure compliance with noise requirements.
RP75.23 Considerations for Evaluating Control Valve Cavitation:
- Offers considerations and recommendations for evaluating and mitigating cavitation phenomena in control valves to prevent damage and performance degradation.
American Petroleum Institute (API)
6D Pipeline Valves (Gate Valve, Plug, Ball, and Check Valves)
- Specifies the requirements for design, manufacturing, testing, and inspection of pipeline valves, including gate valves, plug valves, ball valves, and check valves, used in petroleum and natural gas industries.
598 Inspection Requirements
- Outlines the inspection and testing requirements for various types of industrial valves, including gate valves, plug valves, ball valves, and check valves, to ensure they meet specified performance and safety standards.
609 Lug and Wafer Type, Butterfly Valves
- Defines the design, materials, testing, and inspection requirements for lug and wafer type butterfly valves used in petroleum and natural gas industries, ensuring their reliability and performance in pipeline applications.
What are the selection criteria for control valves?
Key Selection Requirements for Control Valves in Industrial Applications
When selecting control valves for industrial applications, various requirements must be considered to ensure optimal performance and safety. Here are the key selection requirements:
Suitable Capacity of Flow Coefficient Cv calculated as per ISA 75.01
- The flow coefficient (Cv) must be calculated according to ISA 75.01 standards to ensure that the control valve can handle the required flow rates effectively.
Suitable Rangeability
- The control valve should have adequate rangeability to adjust the flow smoothly and precisely across the desired operating range.
Proper Shutoff Pressure to Actuator
- The actuator should be capable of providing sufficient shutoff pressure to ensure tight closure of the valve when necessary.
Materials for Body, Trim, Packing Box, and Other Parts as per Process Conditions
- Select materials for the valve components that are compatible with the process fluid and operating conditions to prevent corrosion, erosion, or other forms of degradation.
Consideration of Cavitation, Flashing, and Noise in Limiting the Range
- Evaluate the potential for cavitation, flashing, and noise generation under different operating conditions and ensure that the selected valve design can mitigate these effects within the desired range.
Type of Positioner
- Choose an appropriate type of positioner based on the control requirements, such as pneumatic, electro-pneumatic, or digital positioners, to achieve accurate control and response.
Control Valve Noise Calculation as per ISA 75.17
- Perform noise calculations according to ISA 75.17 standards to assess and mitigate potential noise issues associated with control valve operation.
Consideration of Failure Actions
- Evaluate potential failure modes and specify appropriate actions to maintain or restore process safety and operability in case of valve failure.
Opening Type of Control Valve
- Select the appropriate opening type (e.g., linear, rotary) based on the process requirements and control strategy.
Shut-off Leakage of Valves in Accordance with FCI 70.2
- Ensure that shut-off leakage meets the requirements specified in FCI 70.2 standards to prevent fluid leakage during valve closure.
Type of Actuator Use
- Choose the type of actuator (e.g., force-balance, smart digital, field bus) based on control system compatibility, response time, and reliability requirements.
Control Valve Leakage
- Minimize control valve leakage to maintain process efficiency and prevent environmental hazards or product losses.
Selection of Actuators to Achieve Specified Valve Failure Positions
- Select actuators capable of positioning the valve to specified fail-safe positions in case of actuator or control system failure.
Testing in Accordance with API 589, Hydro-tested to ASME B 16.34 Clause 7.1, Leak Tested to ASME/FCI 70.2
- Ensure that control valves are subjected to appropriate testing procedures as per API 589, hydro-testing standards (ASME B 16.34), and leak testing standards (ASME/FCI 70.2) to verify their performance and integrity before installation and operation.
Click here for more about Control Valves