- The Bump Test is also known as the functional test.
- Bump testing is defined as qualitative testing of detectors or sensors that are bared to challenge gas for a particular time and at a concentration to energize all alarm units to lower alarm settings.
- Bump testing is an action of precise exposure of installed sensors to the predicted concentration of calibration gas higher than the low alarm set point.
- Bump testing consists of a quick test of our portable gas detectors to confirm the function as required.
- Bump testing is advised by all manufacturers and also includes Safety of Life at Sea (SOLAS) regulations.
- Usually, this bump testing is made more convenient & efficient by using these to hand when needed.
Main Objective of the Bump Test
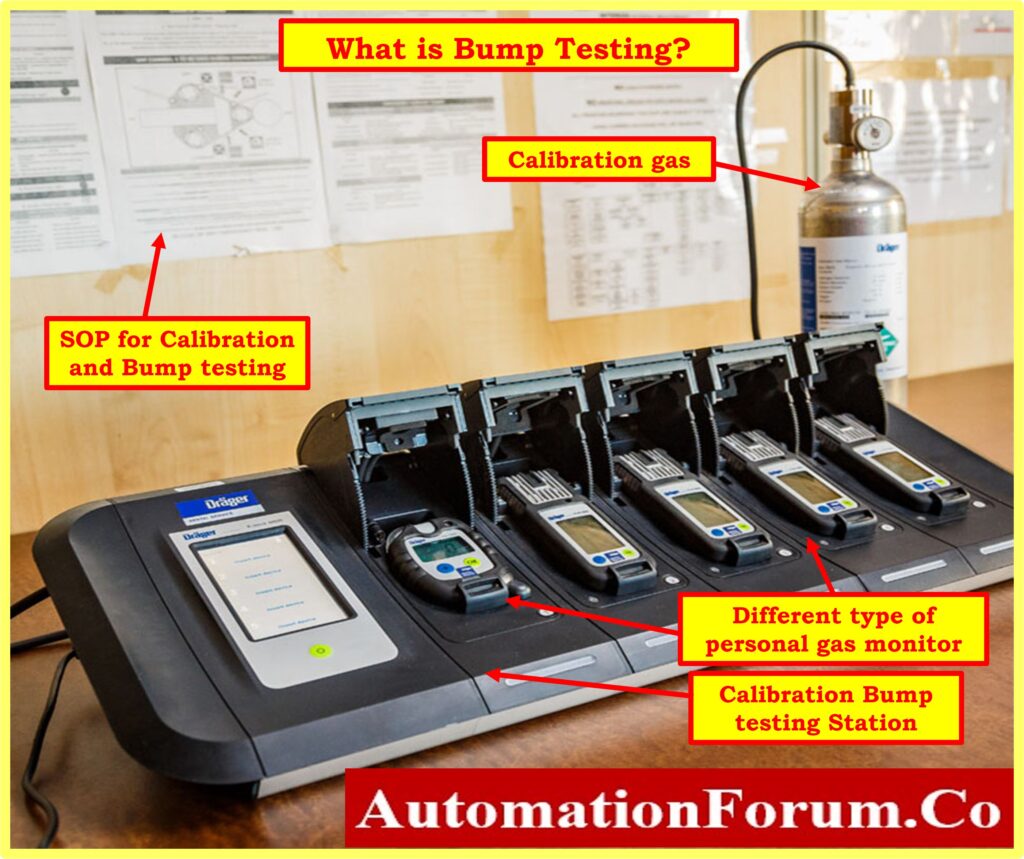
- The main objective of the Bump test is to ensure that the test gas has the ability to reach the sensors.
- The bump test inspects and certifies that all sensors and alarm units are functioning properly by exposing the detector precisely to a known gas concentration.
- Bump testing helps the sensor to alert you to hazardous gas in the atmosphere during our regular scheduled daily duties on board.
- The choice of forte gases from Air Products issues stable and traceable mixtures in a wide range of portable barrels made for convenient calibration and testing.
Importance of Bump Testing:
- During accurate functionality within the specified range of an instrument, Gas detectors are definitely sensational pieces of protective technology. But these are not error-free.
- Since they are kept in regions having a safe atmosphere. Without conducting a bump test, it is unable to decide whether they are operating properly.
- Several investigations have been conducted to verify the durability of portable gas detectors and analyze the significance of frequent bump testing as a consequence of troubling rates of passivity and several companies disputing the requirement of bump testing on regular schedules.
- The study of the collected information according to ISC research delivered surprising results.
- The failure rate for bump tests on equipment that were tested every day was 0.3%, or 3 per 1000, which is not negligible at any given moment.
- Only one detector per 100 gas detectors that had not undergone bump testing & failed to alert potential dangerous gas leaks.
- Making use of a gas detector without conducting a bump test is the same as a pilot in an airplane without routine checks before starting.
- The primary purpose of gas detectors is to protect workers from exposure to hazardous gases. Bump testing ensures that these devices are capable of providing early warnings, allowing workers to take appropriate safety measures when gas concentrations reach dangerous levels.
- Bump testing provides peace of mind to both workers and employers. Knowing that gas detectors are in proper working condition increases confidence in the safety of the workplace.
- Many industries are subject to regulations and standards that require the use of gas detectors and regular bump testing. Compliance with these regulations is essential to avoid fines, legal consequences, and reputational damage.
Important Definitions:
Bump Test:
- It is the only method to ensure the accurate function of the sensor and alarm.
- The bump test doesn’t determine the accuracy of the sensor, & adjustments are not done for an instrument at the time of the bump test.
- Probably these Gas Detection instruments are life-securing devices.
Zero:
- The setting of Zero in every installed sensor acknowledges the ambient air as fresh air.
- Usually, this natural air is not clean air any gasses present and relevant to the installed sensor type will be measured and indicated as zero.
- If the unit is not zeroed correctly in a fresh ambient air, or zero air cylinder then the unit readings might be inaccurate.
Calibration:
- Generally, each and every instrument gets degraded over time.
- The sensor displays inaccurate results of actual gas concentration if not calibrated regularly.
- While calibrating an Instrument, the instrument has the ability to self-adjust so that the sensors maintain their capacity for accurate measurement and indication of actual gas concentration value.
- If the sensor doesn’t function properly after calibration it means the sensors can’t pass a calibration.
- If a sensor deteriorates below its acceptance level, this sensor is said to have reached its lifespan .
Peak Readings:
- The peak reading of an instrument is defined as the instrument deposits maximum value of actual gas concentration value.
- Bump testing and calibration of a sensor periodically record new peak readings.
- The clearing of the peak reading of an instrument must obey each calibration.
- An operator has a right to clear the peak reading after bump testing and calibration of that instrument prior to the change in location, or after addressing an alarm.
Types of Bump Testing:
Functional Test and Full Calibration are two methods of bump testing to verify the accuracy of an instrument.
Functional Test
- A bump test certifies the calibration of an instrument by disclosing it to a noted test gas concentration.
- The indicated value of an instrument is now compared to the actual quantity of gas present or indicated on the cylinder.
- The calibration of an instrument is said to be verified if the feedback of the instrument is within the allowable permissive range.
- However, the users are recommended to check the equipment for allowable permissive range from the vendor or manufacturer.
- To obtain more accuracy of the bump test the instrument must be zeroed prior to the bump test.
- The concentration of the test gas must be much higher to activate the alarm during the bump test.
Full Calibration
- Full calibration of the instrument is done only when the results of the bump test don’t lie within the acceptable range or after service of the instrument.
- A full calibration is the modification of the instrument’s reading to equate with a certified standard or known concentration of test gas.
- To verify the accuracy, calibration gas must be detectable, & must be certified by the National Institute of Standards and Technology (NIST).
- This full calibration must only be organized and supervised in a clean fresh air environment.
Why does a Bump Test fail?
Generally, environmental factors are wrongdoers instead of an issue with the gas detector or sensors themselves.
The failure in the Bump Test is due to a defective or broken unit.
There are several reasons for a failed bump test such as
- Extreme shock
- Extreme Temperature Variation & Climatic Changes.
- Excessive exposure to dust, dirt, & grime.
- Immersing the device in water
Extreme Shock:
- Generally, Portable gas detector environments are subjected to frequent wear and tear.
- Descending the instrument from maximum height to hard surface area may cause the sensor for improper functionality.
Extreme Temperature Variation & Climatic Changes:
The elevation of sensors to extreme hot or cold temperatures may impact the sensitivity of the sensor.
Excessive exposure to dust, dirt, and grime:
- Physical clogging might lead the sensor to be less sensitive to gas in the ambient or surrounding atmosphere.
- A portable gas detector must always be bump tested before using a single time or multiple times on the same day if entering a new environment.
If an instrument gets damaged or dropped from a particular height
In case of any accident, the device must be bump tested once again even if checked earlier in the day.
The device has been immersed in water:
- Since most of the portable gas detectors are not waterproof.
- The device may not respond correctly, hence these devices require complete protection against mist, humidity, or water splashes.
- Triple-C is a type of device developed for marine applications since this device is fully operable submerged up to a depth of 1.5m about 25 minutes to 35 minutes.
- Bump Testing is still recommended for Triple-C before immersion.
- Bump Testing of an instrument is the only way to certify for secure protection.
- This test in the gas detection system ensures the gas sensor and related components are accurate, & in proper function to detect the target gases.
- Generally, a Bump test of an instrument is conducted on a routine or daily basis.
How to conduct the bump test of an Instrument?
Calibration Adjustments:
- If the gas detector stops to react correctly, or if the response of the gas detector is beyond range.
- It may require regular maintenance & calibration.
- Calibration involves sensor adjustment & setting to obtain accurate readings.
Calibration Gas Selection:
A known concentration of gas provided in a calibration gas cylinder is selected.
The concentration of the gas must lie within the desired range.
Preparation:
Check and confirm that the power supply, connection, & calibration of the gas are as per instructions provided by the manufacturer.
Exposure:
Expose the gas detector to the calibration gas by locating it in a controlled environment or using a calibration cup that permits the gas to flow to the sensor.
Confirmation:
The gas detector must respond immediately & display the concentration of the test gas accurately.
This confirmation certifies that the sensor is working as desired.
Documentation:
Note down the results of the bump test along with the concentration of the gas used, the date and time of the test, & any alteration in the desired response to ensure that this meets the calibration criteria.
Proper documentation is essential for adherence to safety regulations and standards.
Frequently Asked Questions:
What is a bump test in calibration?
As per ISEA bump test is a qualitative function check in which test gas is allowed to pass through the sensor to energize all indicators, & alarm to present at least their lower alarm setting
What is the frequency of the bump test?
Depending on the model, a gas detector must be bump tested on a regular basis, usually once daily or once each shift. Consult your instruction manual before bump testing any models, as some might need to be done more frequently.
Please consult with the manufacturer or your supervisor if you’re unsure how frequently to bump test your gas detector.
Regarding individual gas detectors Before starting to use, bump testing is always safe and advised, and it should be performed by the user or in front of the user for eyewitness verification.