What is continuous process control and what are its types?
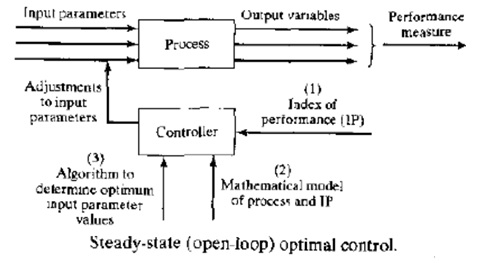
In a continuous type of process control, the physical system will be shown through variables and it will be smooth and uninterrupted in time. Mostly this type of control is used for chemical and oil industries. By using this type of process control very large quantities of products can be produced. In this type of process control, the production will be maintained for a long duration without any interruptions, mostly over weeks or for few months. The major objective of continuous control is to maintain the value of the output variable at the required rate. This type of control is done for a system that has continuous variables and parameters. Most continuous industrial processes have multiple feedback loops.
- What is computer process control?
- What is an adaptive control?
- What are the final control elements in a control system?
- What are the types of instrumentation switches?
- What is industrial automation?
- What is controller tuning
How does a continuous process control, controls a process?
This type of control is used to continuously control the physical output parameter of the material. The parameter will be checked by a sensor and then it will be compared to the required value. The difference between the parameter and the required value is the error and it must be handled properly. This error signal will be used to vary the input parameters so the desired output can be received.
What is the difference between a continuous control and discrete control?
In a continuous control, the parameters and variables are continuous and analog, but in the case of discrete control, the variables and parameters are discrete and analog.
- The continuous process control would measure the weight and also the volume of liquid and solid while the discrete control would measure the number of parts and products
- The continuous control would measure variables and parameters such as temperature, volume flow rate, and pressure. While the discrete control would measure velocity, force, position, and acceleration
- Flow meters and thermocouples are the most used sensors in a continuous control while in case of the discrete photoelectric sensors and strain gauges are used
- Valves, pumps, and heaters are the typical actuators in a continuous control while in the case of the discrete control motors, pistons and switches are used.
What are the types of continuous process control?
- Regulatory control
- Feed forward control
- Steady state optimization
- Adaptive control
Regulatory control
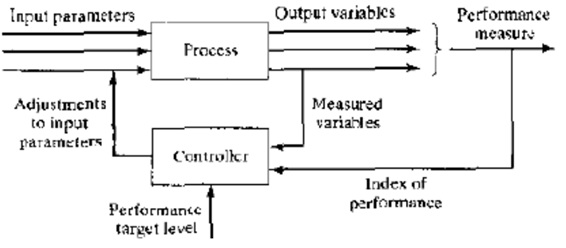
In this type of control, the performance of the process is maintained at a particular value. The performance index is the process performance, the major disadvantage of regulatory control is that it would only take action if there is an error and because of this error the output is not similar to the required value.
Feed-forward control
This type of control would take actions before there is any problem, so it would detect if there is any disturbance which could affect the process and the feedback control would make sure that this disturbance won’t affect the process. The complete compensation can’t be done by the feedback controller because of the limitation of the controller, there could be certain efficiency problems in the operating components. This type of control is mostly used in process industries.
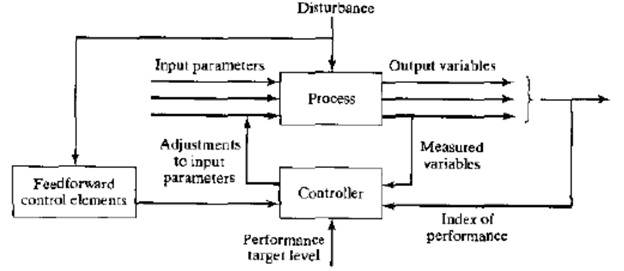
Steady state optimization
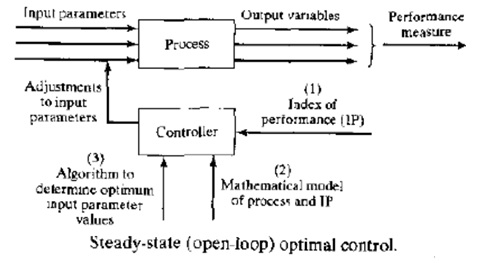
So this type of control is to do the process optimization so that good production rate and also good quality can be achieved. In this type of control, the process variable and the performance index will be determined, and also the system parameter value that can improve the performance index can be known too. So if the above-mentioned characteristics are satisfied then the process can be optimized. Disturbances could affect this type of control.
Adaptive control
This is a self-controlling model of control, it is a combination of feedback and optimal control. During the operation, it would measure certain process variables. There are basically three steps in this type of control and they are identification function, decision function and modification function. In the identification function, the index performance value is known according to the readings from the process. So in the decision function, it would check the readings and make the required changes for the improvement of the process. The modification function is the final step it would do the required work for the improvement of the process variable, mostly the process parameters are modified with the help of actuators.